PLAATBEWERKERS STAP DICHTER BIJ ‘FABRIEK VAN DE TOEKOMST’
Terwijl heel wat bedrijven volop hun productieproces automatiseren, denken fabrikanten van plaatbewerkingsmachines en automatisatieoplossingen al enkele stappen verder vooruit. Gaandeweg zien ze de sector evolueren naar een slimme fabriek van de toekomst, waarin manarm wordt geproduceerd en alle onderdelen op elk moment in het productieproces kunnen worden getraceerd. Het automatisch uitnemen en sorteren van bewerkte onderdelen blijft een heikel punt; zelfrijdende voertuigen die gebruikmaken van artificiële intelligentie, bieden een antwoord op het manuele transport tussen de verschillende productieprocessen op de werkvloer.
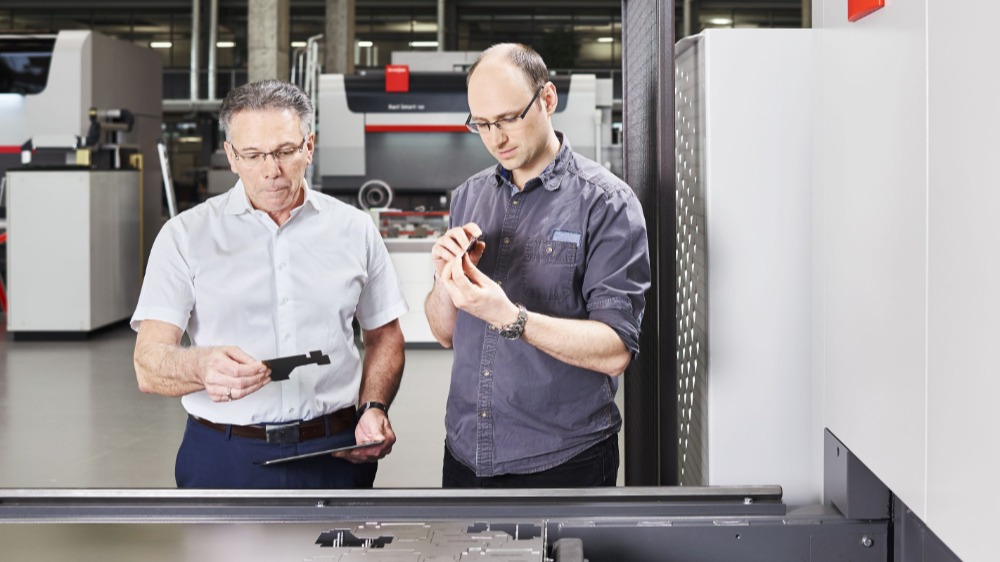
Foto: Bystronic
AUTONOOM PRODUCTIEPROCES
Toen we enkele maanden geleden een bezoek brachten aan de 25e editie van de vakbeurs EuroBLECH in Hannover, Duitsland, konden we er maar moeilijk omheen. ‘Autonoom’ was er het modewoord bij zowat alle (grote én kleinere) fabrikanten van plaatbewerkingsmachines. Of het nu ging om autonoom snijden, plooien of nog iets anders. Steeds opnieuw werden we ermee om de oren geslagen. Zo blijkt er een wezenlijk verschil te zijn tussen geautomatiseerde en autonome productieprocessen. Waar automatisatie traditioneel valt over het knelpunt dat machines enkel en alleen de taken zullen uitvoeren die hun opgelegd zijn, zijn autonome processen nog nét iets anders. De machines leren bij, passen zich aan en worden dankzij artificiële intelligentie (AI) na verloop van tijd beter. Een autonoom productieproces zorgt er met andere woorden voor dat de verschillende geautomatiseerde oplossingen geoptimaliseerd worden.
Torenopslag en aanvoerunits
Het automatiseren van de plaatbewerking heeft de afgelopen decennia al een lange weg afgelegd. (Toren)opslagsystemen sturen de platen via een aanvoerunit naar de wisseltafel van de (laser)snijmachine of ponsmachine. Terwijl de machine snijdt of ponst, haalt de aanvoerunit bijvoorbeeld met vacuümtechnologie een nieuwe plaat uit de aangesloten (toren)opslag. Zodra de afvoerunit de gesneden plaat terug op de wisseltafel plaatst of naast de machine legt, laadt de aanvoerunit de lasersnijmachine met de nieuwe plaat. Machinestilstand wordt zo tot een minimum beperkt. Afhankelijk van de toepassing en de fabrikant zijn er systemen op de markt voor verschillende (grotere) afmetingen plaat en met meerdere cassettes. De verbinding met de opslagtechnologie kan flexibel gebeuren met een direct gekoppeld enkel of dubbel torenopslagsysteem.
Uitnemen en sorteren van de stukken
Het automatisch uitnemen en sorteren van de stukken is nog een andere zaak. Fabrikanten zijn volop bezig met het ontwikkelen van systemen die de onderdelen uit de plaat nemen en vervolgens sorteren en stapelen. Bij veel bedrijven gebeurt dat nog handmatig, ook al kwamen er de voorbije maanden meerdere gestroomlijnde oplossingen op de markt. Deze stap in het manarme productieproces is nog steeds een bottleneck. Dergelijke ontwikkelingen kunnen zinvol zijn, maar veel hangt af van de nesting, het productieschema en het aantal beschikbare operatoren. Naar alle waarschijnlijkheid zullen er in de nabije toekomst nog heel wat verdere ontwikkelingen gebeuren wat betreft de automatisatie van deze stap in het productieproces. Op sommige ponsmachines kunnen de werkstukken via een trechter afgevoerd worden, om ze daar op te halen.
Intern transport
Net daarin ligt een deel van de uitdaging. Ondanks nieuwe innovaties op het vlak van automatisch snijden, plooien en lassen en ontwikkelingen op het vlak van automatisch sorteren en uitnemen van de stukken brengen operatoren nog steeds manueel onderdelen van het ene proces naar het andere met vorkheftrucks, karren en andere arbeidsintensieve oplossingen. Hier en daar duiken transportbanden op die creatief ingezet worden, maar voor het grootste deel blijft het verplaatsen van taken tussen de verschillende operaties bijna volledig handmatig verlopen.
(lees verder onder de foto)
Automated Guided Vehicles (AGV’s) en Self Driving Vehicles (SDV’s) kunnen dat veranderen. Een ver-van-mijn-bedshow? Niet echt. Dat bleek ook tijdens de meest recente editie van EuroBLECH, waar verschillende fabrikanten hun autonome productieproces presenteerden. SDV’s zorgden voor het transport tussen de verschillende operaties of processen. Een mobiele robot, als het ware. Als het voertuig in beweging is, beweegt de robot niet. Wanneer het voertuig stilstaat, kan de robot bewegen. Sensoren die op het systeem zijn gemonteerd, zorgen ervoor dat als iemand binnen een afstand van drie meter van de robotarm komt, de robot wordt uitgeschakeld. De AGV’s worden, zoals hun naam al doet vermoeden, op een of andere manier fysiek geleid, zoals met een magneetstrook, bakens, barcodes of een ander mechanisme. Ze reizen op vaste paden in een gecontroleerde ruimte. Ze voelen de wereld om zich heen met behulp van een lasergebaseerde of soortgelijke technologie en gebruiken algoritmes om hun eigen weg door de fabriek te navigeren, of in dit geval de beursstand. De robot maakt op zijn beurt gebruik van machinevisie om de elementen in zijn omgeving te lokaliseren. Na verloop van tijd passen deze zelfrijdende voertuigen zich aan, leren ze bij en worden ze idealiter efficiënter en nauwkeuriger. Tegenwoordig kunnen SDV’s ook uitgerust worden met camerasystemen of perceptie- en kaartsoftware, waardoor ze geen tapes, bakens of andere fysieke infrastructuur nodig hebben. Het systeembeheer vindt plaats via een softwareplatform dat met de SDV communiceert via wifi. Elk zelfrijdend voertuig werkt als zelfstandige eenheid en zal indien nodig zelf naar het accudock rijden om op te laden.
Afhankelijk van de keuze van de gebruiker kunnen de zelfrijdende wagens aangestuurd worden vanuit het ERP-systeem of handmatig. In dit laatste geval voert de machineoperator op de bedieningsterminal van de SDV in dat een order klaar is en waar deze naartoe gebracht moet worden. De fleetmanager regelt dan automatisch dat een van de wagens de producten ophaalt en transporteert.
De technologie deed al enkele jaren geleden haar intrede, maar kwam pas nu nadrukkelijk naar voren op de beursvloer. Waar AGV’s vroeger enkel bruikbaar waren voor repetitieve en herhaalbare taken, helpen ze nu om meer onderdelen in het productieproces in beweging te krijgen. Vandaag telt immers niet langer hoe productief een bepaalde machine is, belangrijker is hoe snel en consistent de onderdelen ‘in beweging’ blijven (parts flow). Nadat de onderdelen sneller dan ooit worden gesneden (sommige machinefabrikanten pakten op EuroBLECH uit met een fiberbron van maar liefst 15 kW), zouden ze idealiter niet genest moeten wachten tot iemand hen naar het volgende proces brengt.
VANDAAG TELT NIET LANGER HOE PRODUCTIEF EEN BEPAALDE MACHINE IS, BELANGRIJKER IS DE PARTS FLOW: HOE SNEL EN CONSISTENT DE ONDERDELEN ‘IN BEWEGING’ BLIJVEN
Levering en facturatie
Een volgende stap is dat onderdelen automatisch gescand worden en in de vrachtwagen kunnen worden geladen richting klant. Papierloze opdrachten gebeuren hierbij automatisch en onmiddellijk. Het is goed mogelijk dat een klant amper 48 uur eerder zijn tekening van onderdelen had geüpload naar de offertesoftware, die binnen enkele minuten een offerte maakt. Vervolgens wordt deze offerte automatisch verwerkt, de bestelling geplaatst, de planning gemaakt en de nesting uitgevoerd, vooraleer de eigenlijke productie plaatsvindt.
De uitdagingen die transport met zich meebrengt, vormen een van die zaken die bij heel wat bedrijven in de sector nog marge hebben voor verbetering. Het traceren van het onderdeel in het productieproces, het onderdeel beschermen tegen transportschade, verloren ladingen, het gewicht van de lading beperken, de uitstoot verminderen ... kortom: een verbeterde en consistente 'parts flow'.
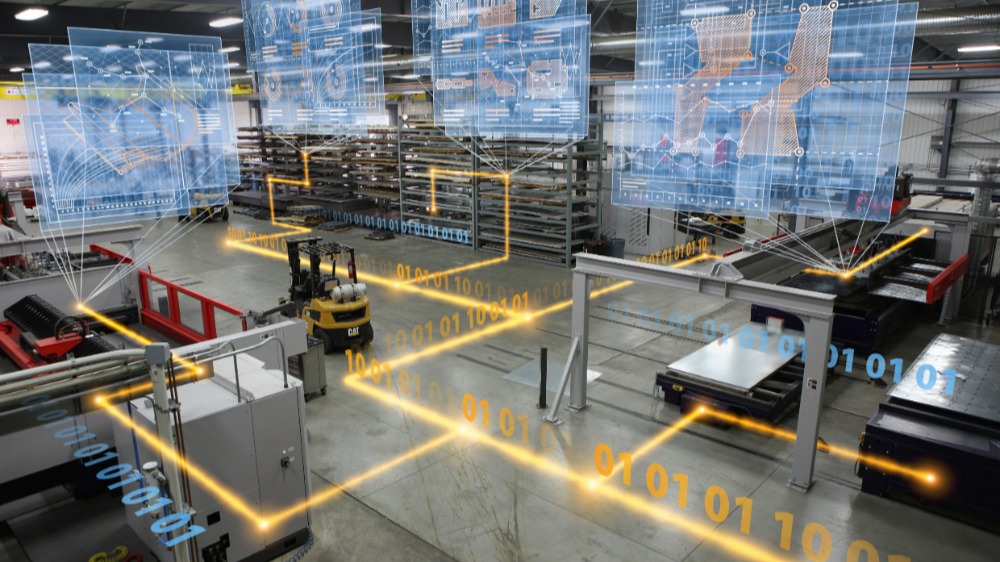
Dit alles begint bij het identificeren en het markeren van het onderdeel. Niet alleen om de oorzaak van eventuele defecten op te sporen, eveneens om in real time het productieproces op te volgen. Laser- of inktmarkeren is niet nieuw, maar is wél aan een opmars bezig, ook bij kleinere kmo's. Nieuwe ontwikkelingen op dat vlak maken immers de brede inzetbaarheid van een lasermarkeertool mogelijk. Die bieden bovendien als voordeel dat ze, in tegenstelling tot inkt, op bijna elk type materiaal kunnen worden aangebracht. Denk aan QR-codes, die heel wat bijkomende informatie over een onderdeel bevatten. Ook de prijsdaling van de lasermarkeertool speelt ongetwijfeld een rol in de revival van het gereedschap. Vanaf daar is het maar een kleine stap om alle onderdelen te koppelen met het ERP-systeem van het bedrijf ... wat opnieuw een stap dichter bij de autonome fabriek van de toekomst is.