gedopeerde beschermgassen voor MIG-lassen van aluminium
Voor het MIG-lassen van aluminium en aluminiumlegeringen wordt overwegend argon als beschermgas gebruikt. Voor grotere plaatdiktes, die door hun grotere afkoelsnelheid om voldoende ingebrachte warmte vragen, is een argon-heliummengsel aan te bevelen. De beschermgassen moeten chemisch inert zijn o.w.v. de grote affiniteit tot zuurstof van aluminium en zijn legeringen.
MIG-lassen met Argon
Het MIG-lassen met argon als beschermgas heeft een kenmerkende inbranding in de vorm van een smalle ‘vinger’ in het midden van de las. Dit is een gevolg van de materiaaloverdracht van de lasdraad die in het midden van de lasboog is geconcentreerd en de steile temperatuurgradiënt aan de buitenzijde van de boogzuil.
Deze vingervormige inbranding kan onder ongunstige omstandigheden leiden tot porositeiten en/of bindingsfouten en tevens tot warmscheuren. De porositeiten (gasinsluitingen) kunnen onderaan in de punt van de vinger ontstaan, doordat het vloeibare lasmetaal hier snel stolt, waardoor de ontgassing moeilijk is. Bindingsfouten kunnen het gevolg zijn van een niet goed overlappen van de ‘vingers’ bij het verkant lassen en dus van het onjuist positioneren van de lastoorts. De snelle temperatuurdaling aan de zijkant van de boogzuil, die kenmerkend is voor argon, zorgt ervoor dat de inbranding naar de zijkanten gering is.
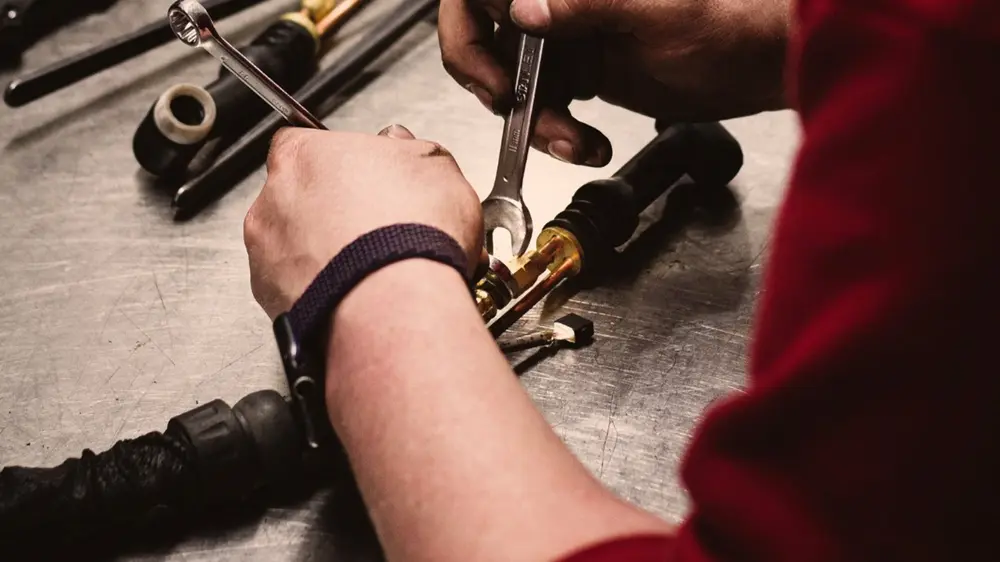
Toevoeging van helium
Bij gelijke lasstroom en booglengte is de boogspanning bij helium hoger dan bij argon, zodat de warmte-inbreng hoger is. Het hogere warmtegeleidingsvermogen van helium zorgt immers voor de insnoering van de boogzuil, waardoor de boogspanning aanzienlijk hoger is dan argon. Bij argon-helium mengsels resulteert de toename van de boogspanning in een beter aangevloeid en vlakker lasbad, met een geringere kans op porositeiten door een betere ontgassing. Het inbrandingsprofiel is ook breder en minder vingervormig dan bij argon. De inbranding neemt ook toe naar de zijkanten dankzij een bredere zone waarin het beschermgas op hoge temperatuur staat.
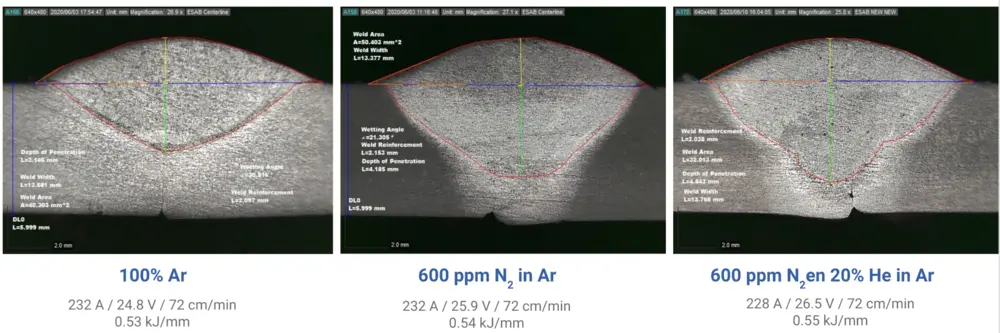
Het percentage helium voor het MIG-lassen van aluminium ligt typisch tussen de 20 en de 75%. Het gedrag van zowel de lasboog als het smeltbad bij een lager percentage helium is nagenoeg gelijk aan dat van argon. Vanaf 20% helium is er pas sprake van een significante verandering van de thermische geleidbaarheid. Bij een hoger percentage dan 75% helium is het gedrag gelijk aan dat van zuiver helium.
Bij het MIG-lassen van aluminium met een argon-heliummengsel zorgt de grotere boogenergie er voor dat er met een hogere lassnelheid kan worden gewerkt bij gelijkblijvende inbrandingsdiepte en dat voorverwarmen soms overbodig wordt. Een argon-helium mengsel heeft een grote fit-up tolerantie voor de te lassen stukken. Dat is vaak een voordeel bij complex samengestelde stukken, die niet altijd perfect kunnen worden uitgelijnd.
De dichtheid van helium is lager dan die van argon. Bijgevolg moet het gasdebiet van een argon-helium mengsel hoger ingesteld worden om een goede gasbescherming te verkrijgen.
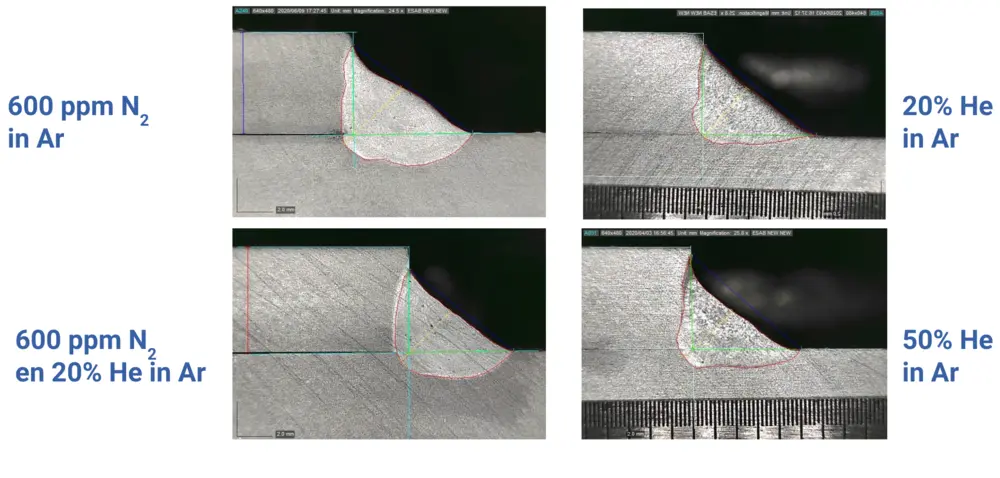
De schaarste van helium
Helium is zowat het enige element op aarde dat helemaal niet hernieuwbaar is. Het helium waarover we vandaag beschikken, werd miljoenen jaren geleden diep onder de grond gevormd in het gesteente, door het natuurlijk radioactief verval van uranium en thorium. Het gevormde helium stijgt op door de aardkorst en raakt ofwel opgesloten in holtes met aardgas of het bereikt het aardoppervlak.
Slechts vanuit een beperkt aantal aardgasbronnen op aarde kan helium worden gewonnen. Aangezien helium chemisch inert is, reageert het met geen enkel ander element en kan het dus niet ‘gevangen’ worden in een andere verbinding. Zodra helium effectief het aardoppervlak bereikt, ontsnapt het zelfs aan de zwaartekracht door zijn lage gewicht en verliezen we het aan de ruimte. Het is het enige element uit het periodiek systeem dat fysisch ontsnapt van de aarde en verloren raakt. Waterstof, dat een trapje lager staat dan helium in het periodiek systeem, is nog lichter. Maar waterstof reageert wel met andere elementen en blijft zo gevangen op aarde.
Door allerlei hoogtechnologische ontwikkelingen, met name in ruimtevaart en supergeleiders, stijgt de vraag naar helium. En dat is bijzonder voor een element dat nog maar 150 jaar geleden ontdekt werd. De wereldwijde heliumproductie is gesitueerd in amper een paar landen. En als een van die landen wordt geconfronteerd met een productieprobleem, piekt de prijs van helium naar ongekende hoogtes. Door de instabiele prijsvorming van helium op de markt, worden wetenschappers uitgedaagd om na te denken in welke toepassingen helium effectief een meerwaarde biedt en of er alternatieven bestaan.
Alternatieven voor Helium in het beschermgas
Ook wetenschappers in booglastechnologie werden geconfronteerd met de zoektocht naar andere gasmengsels om het helium deels of volledig te vervangen. Reeds in 1999 onderzocht het CTAS (onderzoekscentrum van Air Liquide) in Frankrijk de mogelijkheid om zuurstof te gebruiken in argon voor het MIG-lassen van aluminium. Hoewel de lassnelheid kon worden opgedreven met 10 tot 20% en er geen verlies was aan mechanische eigenschappen, bleek zuurstof zeer nadelig te zijn voor het lasuiterlijk. Ook de mogelijkheden van CO2 werden onderzocht. Opnieuw zonder veel succes. Andere gasfabrikanten experimenteerden eveneens met zuurstof maar ook met NO (stikstofmonoxide) en N2O (stikstofoxide).
Een andere onderzoekpiste leidde tot het gebruik van stikstof in argon en argon-helium mengsels. In het bijzonder werd gekeken naar de toevoeging van nul tot duizend ppm (0,1%) stikstof en het effect op de lassnelheid, de inbranding en de mechanische eigenschappen. Boven de grens van duizend ppm stikstof neemt het risico op porositeiten sterk toe. Het is daarom een absolute grens.
doperen met stikstof
In 2007 toonde J.M. Fortain (CTAS) aan dat micro toevoegingen van stikstof aan argon en argon-helium gasmengsels in het bereik van 300-900 ppm vergelijkbare resultaten opleverden als hoog helium houdende mengsels van argon. Toevoeging van 150 ppm stikstof heeft een vergelijkbaar effect als 5% helium in argon op de inbrandingsdiepte. De mechanische eigenschappen zijn in beide gevallen vergelijkbaar.
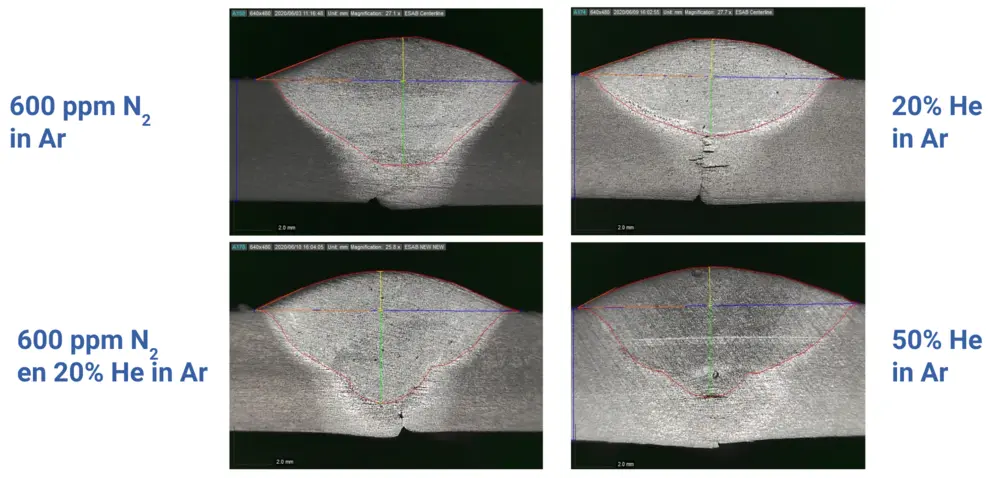
I-naad, dikte 6 mm
Dit fenomeen kan worden verklaard door de vorming van aluminiumnitride op het smeltbad tijdens het lassen. Dit zorgt enerzijds voor de beperking van de bewegingsvrijheid van de kathodevlek en anderzijds voor de verbetering van de boogstabiliteit dankzij de hoge emissiegraad van aluminiumnitride (tot 2x sterker dan die van aluminium). Tijdens het MIG-lassen is het werkstuk negatief geschakeld en doet het dienst als kathode: het werkstuk moet elektronen uitzenden in de lasboog. Hoe hoger de emissiegraad, hoe gemakkelijker de elektronen worden uitgezonden en hoe stabieler de boog is. Als gevolg van de verbeterde emissiegraad wordt de boog ingesnoerd, wat leidt tot een toename van de energiedichtheid en de thermische geleidbaarheid en dus een diepe inbranding.
productiviteit en kwaliteit
In 2020 startten Air Liquide (Advanced Fabrication Center, Delaware, USA) en ESAB een gezamenlijk praktisch onderzoek naar de toepassing van stikstof gedopeerde argon en argon-heliummengsels. Daarbij lag de focus op productiviteit en kwaliteit. Productiviteit omvat aspecten zoals inbrandingsdiepte, ontsteking van de boog en lassnelheid. Kwaliteit legt de focus op de gevoeligheid voor las-imperfecties, porositeiten en het lasuiterlijk.
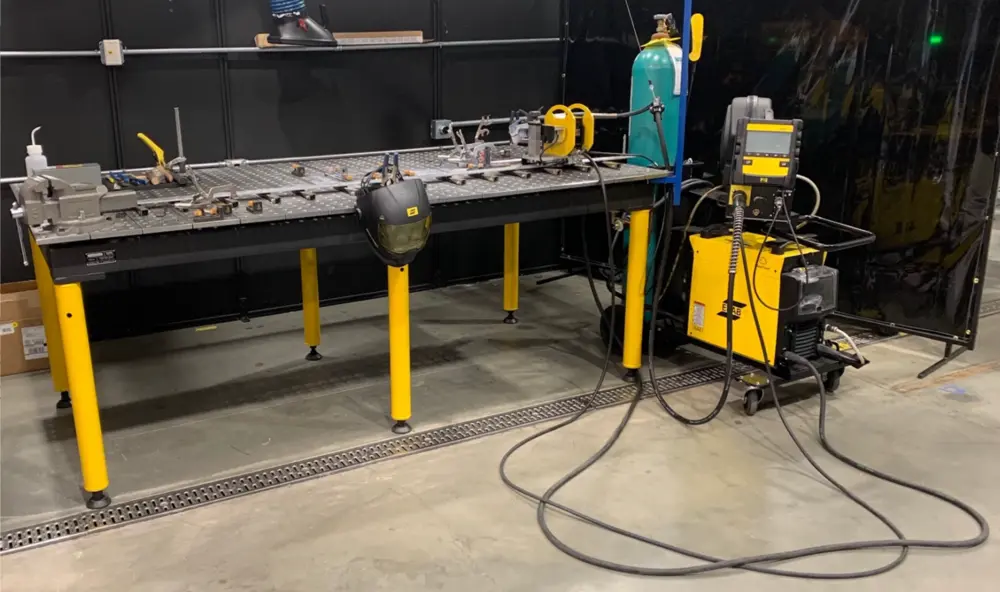
De meest voorkomende gassamenstellingen op de markt voor het MIG-lassen van aluminium zijn zuiver argon, argon met 20% He, argon met 50% He en argon met 70% He. Rekening houdend met het verband tussen 150 ppm stikstof en 5% helium, werden volgende innovatieve gasmengsels opgenomen in het gezamenlijk onderzoek: enerzijds argon met 600 ppm stikstof ter vervanging van een argon-heliummengsel met 20% He en anderzijds een argon-heliummengsel met 20% He én 600 ppm stikstof als alternatief voor 50% helium in argon. Deze gassen werden vergeleken met maar liefst negen andere gassamenstellingen die geschikt zijn voor het MIG-lassen van aluminium.
Een hele reeks lasverbindingen werd uitgevoerd met AL5086 basismateriaal. Dat is een aluminium legering uit de groep 5XXX, die naast goede mechanische eigenschappen eveneens over een goede corrosiebestendigheid beschikt. AL5086 heeft zijn mechanische sterkte voornamelijk te danken aan magnesium (3,5 - 4,5%) als legeringselement en heeft een breed toepassingsgebied in de transportsector, scheepsbouw en bij de fabricage van loopbruggen. Aan de legering is ook mangaan en silicium toegevoegd om de gevoeligheid voor warmscheuren te beperken. Voor de praktische studie werd gekozen voor een aluminium lasdraad type 5356 (AlMg5Cr) van ESAB Alcotec. Dit type legering is uitermate geschikt voor het lassen van stompe naden en overlap naden.
conclusie
De studie van Air Liquide en de gezamenlijke praktische testen met ESAB tonen aan dat de micro toevoeging van stikstof aan argon heel effectief is ter vervanging van helium. Een diepe inbranding, mooie aanvloeiing en goede boogstabiliteit worden ervaren. De gasmengsels zijn geschikt voor dunne en dikke platen, stompe naden, overlap naden en hoeknaden. De gassen zijn geschikt voor het sproeiboog lassen en het pulserend lassen. Bij zowel de combinatie AL5086 gelast met AlMg5Cr toevoegmateriaal als de combinatie AL6005 gelast met AlMg4.5Mn leiden de niet-destructieve en destructieve beproevingen tot goede resultaten. Daarmee bieden de stikstof gedopeerde gassen een alternatief voor de volledige of gedeeltelijke vervanging van helium bij het MIG lassen.

Het concept van micro toevoegingen of het doperen van beschermgassen wordt ondertussen ook succesvol toegepast voor andere materialen. Hoog nikkel legeringen kunnen vb. worden gelast met CO2-gedopeerde argon-helium of argon-waterstofmengsels.
Gedopeerde gassen zijn een buitenbeentje in de beschermgassen en zijn bij vele lasdeskundigen vaak niet of onvoldoende bekend. Om het in de termen van de EN ISO14175 te zeggen: denk niet dat de Z-classificatie (waaronder de gedopeerde gassen vallen) zomaar gasmengsels bevat die als enige kenmerk hebben dat ze buiten de standaard range vallen van een gestandaardiseerde tabel. Er zit een ganse wetenschap en technologie achter, waar voor geldt ‘onbekend is onbemind’.
Bronvermelding:
- J.M. Fortain, T. Opderbecke & S. Gadrey: “Selecting suitable gases to increase the performances in MIG & TIG welding of the Aluminum Alloys”, Air Liquide CTAS, Cergy-Pontoise, France, 2007; EUROJOIN 7 Conference.
- H.L. Saunders, T. Anderson, F. Armao, B. Christy, J.A. Clarke, P. Pollak, D. Rager, D.J. Spinella & K. Williams: “Welding Aluminum: Theory and Practice”, The Aluminum Association, Arlington, VA, 2002.