Les gaz de protection dopés pour le soudage MIG de l'aluminium
On utilise principalement de l'argon pour le soudage MIG de l'aluminium et des alliages d'aluminium. Pour les plaques plus épaisses, qui nécessitent un apport de chaleur suffisant en raison de leur vitesse de refroidissement plus élevée, on recommande un mélange argon-hélium. Les gaz de protection doivent être chimiquement inertes en raison de la forte affinité de l'aluminium et de ses alliages avec l'oxygène.
Soudage MIG à l'argon
Le soudage MIG avec de l'argon comme gaz de protection présente une pénétration caractéristique en forme de 'doigt' étroit au milieu de la soudure. Il s'agit d'une conséquence du transfert de matière du fil de soudure qui est concentré au centre de l'arc et du gradient de température élevé à l'extérieur de l'arc.
Dans des conditions défavorables, cette pénétration en forme de doigt peut entraîner des porosités et/ou des manques de liaison, ainsi que des fissures à chaud. Les porosités (inclusions de gaz) peuvent se produire dans le bas du doigt, car le métal de soudage liquide se solidifie rapidement à cet endroit, rendant le dégazage difficile. Les manques de liaison peuvent résulter d'un chevauchement incorrect des 'doigts' lors d'un soudage en angle et donc d'un mauvais positionnement de la torche de soudage. La chute rapide de la température sur le côté de la colonne d'arc, qui est caractéristique de l'argon, fait en sorte que la pénétration sur les côtés est faible.
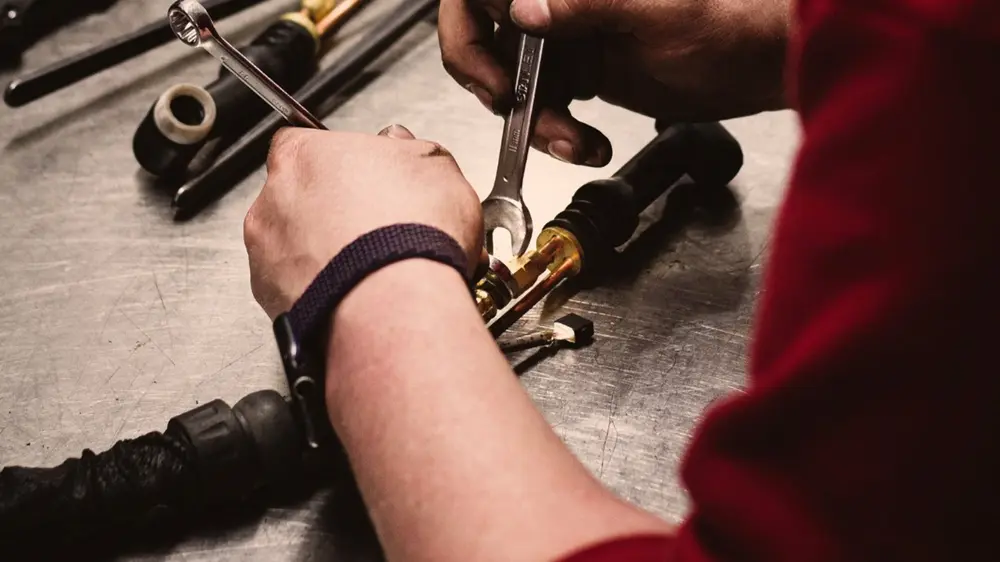
Ajout d'hélium
Pour un même courant de soudage et une même longueur d'arc, la tension d'arc avec l'hélium est plus élevée qu'avec l'argon, si bien que l'apport de chaleur est plus important. La conductivité thermique plus élevée de l'hélium provoque une constriction de la colonne d'arc, de sorte que la tension d'arc est considérablement plus élevée que celle de l'argon. Dans les mélanges argon-hélium, l'augmentation de la tension d'arc permet d'obtenir un bain de soudure plus fluide et plus plat, avec moins de risques de porosités grâce à un meilleur dégazage. Le profil de pénétration est également plus large et moins en forme de doigt qu'avec l'argon. La pénétration augmente également vers les côtés en raison d'une zone plus large où le gaz de protection est à haute température.
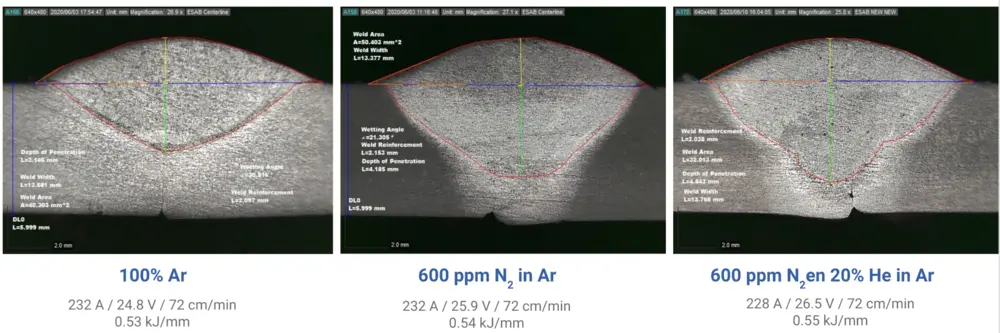
Le pourcentage d'hélium utilisé pour le soudage MIG de l'aluminium est généralement compris entre 20 et 75%. Le comportement de l'arc et du bain à des pourcentages plus faibles d'hélium est presque identique à celui avec l'argon. A partir de 20% d'hélium, on observe un changement significatif de la conductivité thermique. Avec un pourcentage d'hélium de plus de 75%, le comportement est similaire à celui avec de l'hélium pur.
Lors du soudage MIG de l'aluminium avec un mélange d'argon et d'hélium, l'énergie plus élevée de l'arc permet d'obtenir une vitesse de soudage plus élevée à la même profondeur de pénétration et parfois de rendre le préchauffage superflu. Un mélange argon-hélium présente une grande tolérance d'ajustement des pièces à souder. C'est souvent un avantage pour les pièces composites complexes, qui ne peuvent pas toujours être alignées parfaitement.
La densité de l'hélium est inférieure à celle de l'argon. Par conséquent, le débit de gaz d'un mélange argon-hélium doit être plus élevé afin d'obtenir une bonne protection par gaz.
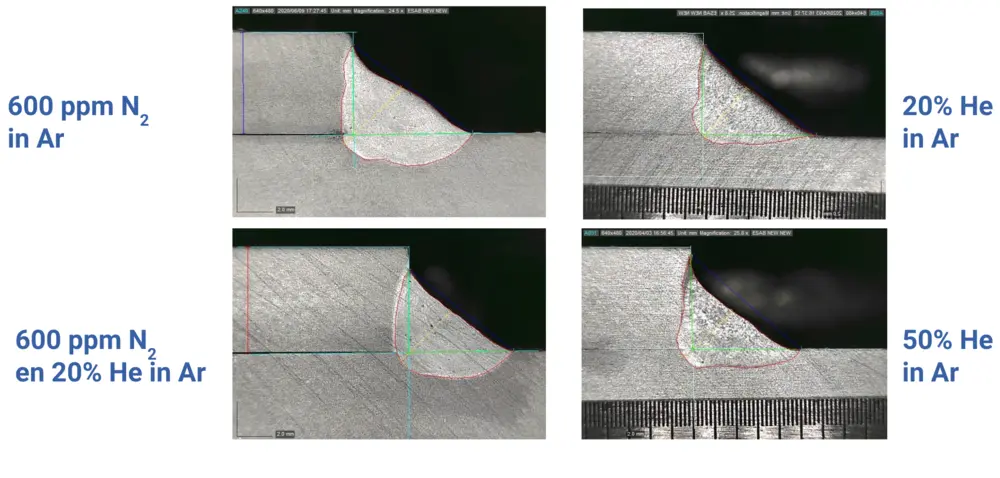
pénurie d'hélium
L'hélium est à peu près le seul élément sur Terre qui n'est pas du tout renouvelable. L'hélium dont nous disposons aujourd'hui a été formé il y a des millions d'années dans les profondeurs de la roche par la désintégration radioactive naturelle de l'uranium et du thorium. Une fois formé, l'hélium s'élève à travers la croûte terrestre. Ensuite, soit il est piégé dans des cavités avec du gaz naturel, soit il atteint la surface terrestre.
L'hélium ne peut être extrait que d'un nombre limité de puits de gaz naturel sur Terre. L'hélium étant chimiquement inerte, il ne réagit avec aucun autre élément et ne peut donc être 'piégé' dans aucun autre composé. Lorsque l'hélium atteint effectivement la surface de la Terre, il échappe à la gravité en raison de son faible poids et se perd dans l'espace. C'est le seul élément du tableau périodique qui s'échappe physiquement de la Terre et se perd. L'hydrogène, qui se situe un cran en dessous de l'hélium dans le tableau périodique, est encore plus léger. Mais l'hydrogène réagit avec d'autres éléments et reste donc piégé sur Terre.
En raison de toutes sortes de développements de haute technologie, notamment dans le domaine des voyages spatiaux et des supraconducteurs, la demande d'hélium augmente. Et c'est extraordinaire pour un élément qui a été découvert il y a seulement 150 ans. La production mondiale d'hélium est localisée dans quelques pays seulement. Et lorsque l'un de ces pays est confronté à un problème de production, le prix de l'hélium atteint des sommets sans précédent. En raison de l'instabilité du prix de l'hélium sur le marché, les scientifiques sont mis au défi d'examiner dans quelles applications l'hélium apporte réellement une valeur ajoutée et s'il existe des alternatives.
Alternatives à l'utilisation de l'hélium comme gaz de protection
Les scientifiques de la technologie de soudage à l'arc ont également été confrontés à la recherche d'autres mélanges gazeux pour remplacer partiellement ou totalement l'hélium. En 1999 déjà, le CTAS (centre de recherche d'Air Liquide) en France a étudié la possibilité d'utiliser de l'oxygène dans l'argon pour le soudage MIG de l'aluminium. Bien que la vitesse de soudage ait pu être augmentée de 10 à 20% et qu'il n'y ait eu aucune perte de propriétés mécaniques, l'oxygène s'est avéré très nuisible à l'aspect de la soudure. Les possibilités du CO2 ont également été étudiées. Encore une fois, sans grand succès. D'autres fabricants de gaz ont également expérimenté l'oxygène, mais aussi le NO (monoxyde d'azote) et le N2O (oxyde d'azote).
Un autre axe de recherche a conduit à l'utilisation de l'azote dans l'argon et les mélanges argon-hélium. On a notamment examiné l'ajout de zéro à mille ppm (0,1%) d'azote et son effet sur la vitesse de soudage, la pénétration et les propriétés mécaniques. Au-delà de la limite de mille ppm d'azote, le risque de porosité augmente fortement. Il s'agit donc d'une limite absolue.
dopage à l'azote
En 2007, J.M. Fortain (ETG) a démontré que des micro-additions d'azote à l'argon et aux mélanges de gaz argon-hélium dans la plage de 300 à 900 ppm donnaient des résultats similaires à ceux des mélanges d'argon à forte teneur en hélium. L'ajout de 150 ppm d'azote a un effet similaire à celui de 5% d'hélium dans l'argon sur la profondeur de pénétration. Les propriétés mécaniques sont comparables dans les deux cas.
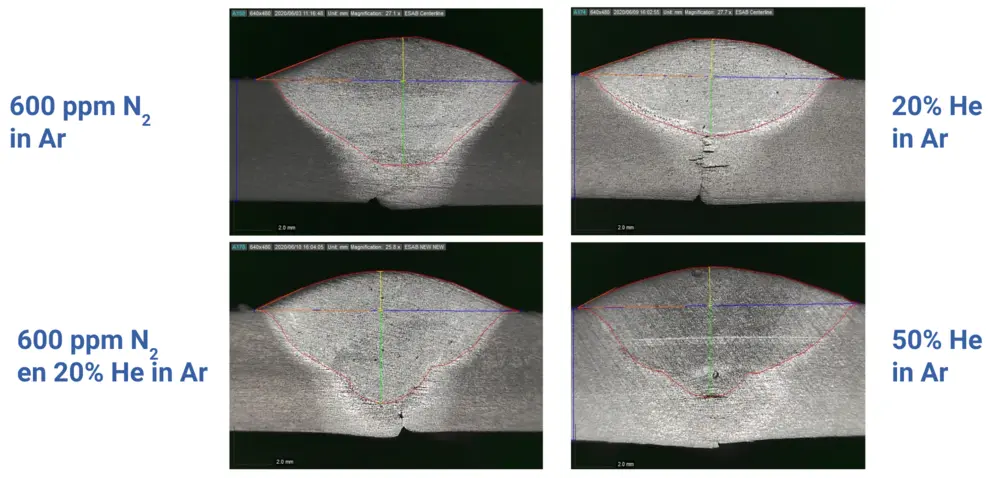
Ce phénomène peut être expliqué par la formation de nitrure d'aluminium sur le bain pendant le soudage. D'une part, cela limite le mouvement de la tache cathodique et, d'autre part, cela améliore la stabilité de l'arc grâce au taux d'émission élevé du nitrure d'aluminium (jusqu'à 2x plus élevé que celui de l'aluminium). Lors du soudage MIG, la pièce bascule en négatif et fait office de cathode: elle doit émettre des électrons dans l'arc de soudage. Plus le degré d'émission est élevé, plus les électrons sont émis facilement et plus l'arc est stable. En raison de l'émissivité améliorée, l'arc est resserré, ce qui entraîne une augmentation de la densité d'énergie et de la conductivité thermique, et donc une pénétration profonde.
productivité et qualité
En 2020, Air Liquide (Advanced Fabrication Center, Delaware, États-Unis) et ESAB ont lancé une étude pratique conjointe sur l'application de l'argon dopé à l'azote et des mélanges argon-hélium. L'accent a été mis sur la productivité et la qualité. La productivité comprend des aspects tels que la pénétration, l'allumage de l'arc et la vitesse de soudage. La qualité se concentre sur la sensibilité aux imperfections de soudure, à la porosité et à l'aspect de la soudure.
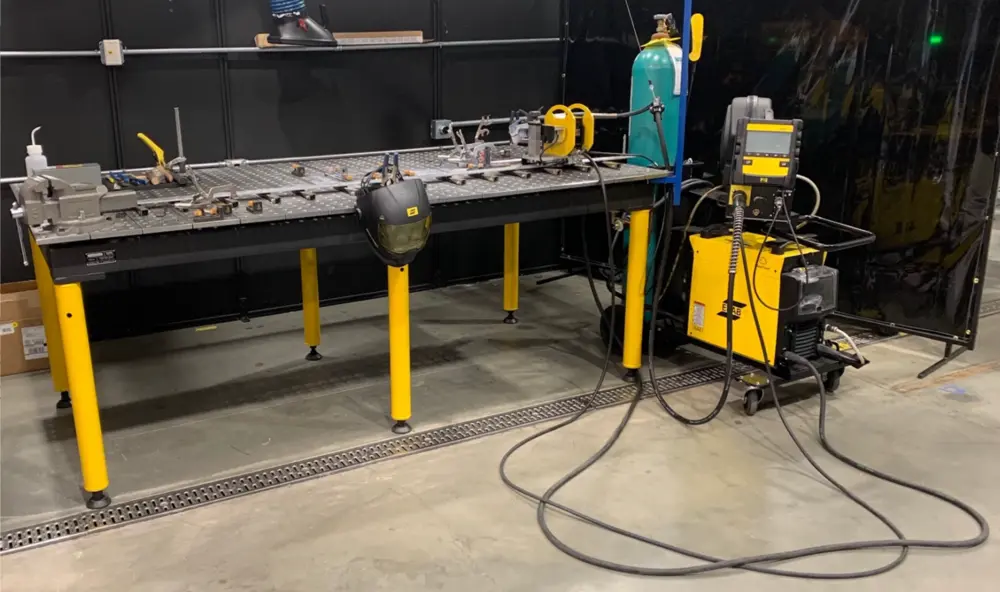
Les compositions gazeuses les plus courantes sur le marché pour le soudage MIG de l'aluminium sont l'argon pur, l'argon avec 20% de He, l'argon avec 50% de He et l'argon avec 70% de He. Compte tenu de la relation entre 150 ppm d'azote et 5% d'hélium, les mélanges gazeux innovants suivants ont été inclus dans la recherche commune: d'une part, de l'argon avec 600 ppm d'azote pour remplacer un mélange argon-hélium avec 20% d'He et, d'autre part, un mélange argon-hélium avec 20% d'He et 600 ppm d'azote comme alternative à 50% d'hélium dans l'argon. Ces gaz ont été comparés à pas moins de neuf autres compositions gazeuses qui conviennent au soudage MIG de l'aluminium.
Toute une série de soudures a été réalisée en utilisant le matériau de base AL5086. Il s'agit d'un alliage d'aluminium du groupe 5XXX qui, en plus de ses bonnes propriétés mécaniques, présente une bonne résistance à la corrosion. L'AL5086 doit sa résistance mécanique principalement au magnésium (3,5 - 4,5%) en tant qu'élément d'alliage et a un large éventail d'applications dans le secteur des transports, la construction navale et la fabrication de passerelles. Du manganèse et du silicium sont également ajoutés à l'alliage pour réduire sa sensibilité à la fissuration thermique. Pour l'étude pratique, on a choisi un fil de soudure en aluminium de type 5356 (AlMg5Cr) de ESAB Alcotec. Ce type d'alliage convient parfaitement au soudage des joints bout à bout et des joints à chevauchement.
conclusion
L'étude d'Air Liquide et les essais pratiques conjoints avec ESAB montrent que la micro-addition d'azote à l'argon est très efficace pour remplacer l'hélium. Une pénétration profonde, un bon écoulement et une bonne stabilité de l'arc sont constatés. Les mélanges gazeux conviennent aux plaques minces et épaisses, aux joints bout à bout, aux joints à chevauchement et aux joints d'angle. Ces gaz conviennent au soudage à l'arc de pulvérisation et au soudage pulsé. Dans la combinaison AL5086 soudée avec un métal d'apport AlMg5Cr et la combinaison AL6005 soudée avec AlMg4.5Mn, les essais non destructifs et destructifs conduisent à de bons résultats. Ainsi, les gaz dopés à l'azote offrent une alternative au remplacement total ou partiel de l'hélium dans le soudage MIG.

Le concept de micro-addition ou de dopage de gaz de protection est également appliqué avec succès à d'autres matériaux. Par exemple, les alliages à haute teneur en nickel peuvent être soudés avec des mélanges argon-hélium ou argon-hydrogène dopés au CO2.
Les gaz dopés sont une exception parmi les gaz de protection et sont souvent inconnus ou méconnus de nombreux experts en soudage. Pour le dire avec les termes de la norme EN ISO14175: ne pensez pas que la classification Z (qui comprend les gaz dopés) inclut juste des mélanges de gaz dont la seule caractéristique est de se situer en dehors de la plage standard d'un tableau standardisé. Il y a toute une science et une technologie derrière cela. Mais on n'aime que ce qu'on connaît...
Sources:
- J.M. Fortain, T. Opderbecke & S. Gadrey: "Selecting suitable gases to increase the performances in MIG & TIG welding of the Alloys", Air Liquide CTAS, Cergy-Pontoise, France, 2007; Conférence EUROJOIN 7.
- H.L. Saunders, T. Anderson, F. Armao, B. Christy, J.A. Clarke, P. Pollak, D. Rager, D.J. Spinella & K. Williams: "Welding Aluminum: Theory and Practice", The Aluminum Association, Arlington, VA, 2002.