Laserlassen steeds toegankelijker
Ondanks de vele voordelen van laserlassen zie je dat bij veel kmo's nog steeds de klassieke MIG/MAG- en TIG-lastechnieken dominant aanwezig zijn. Zal dit veranderen doordat de eisen aan lassamenstellingen wijzigen en laserlassen beter bereikbaar wordt voor kleinere bedrijven?
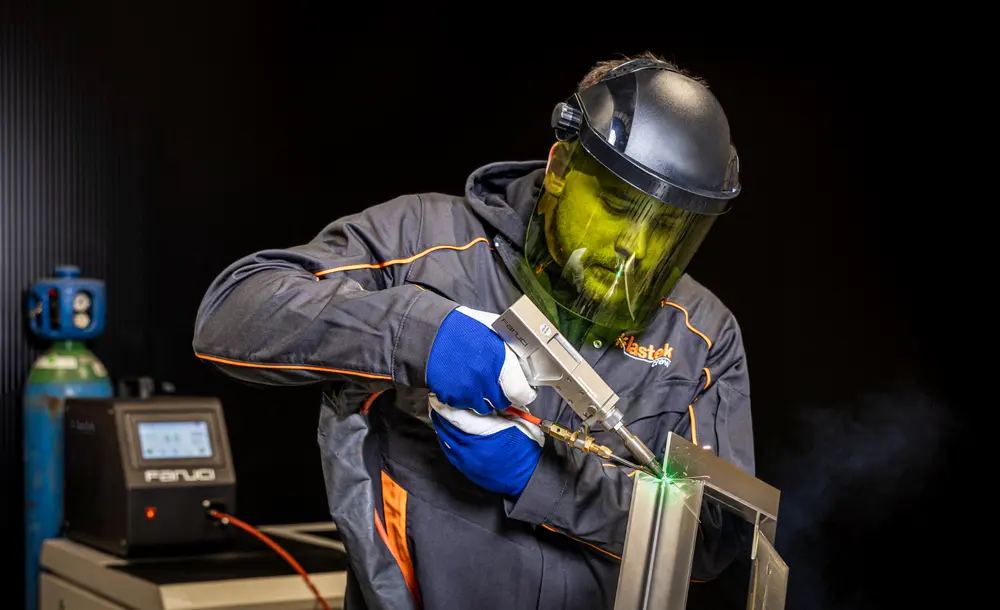
In serieproductie in onder andere de automobielindustrie is laserlassen al lang en breed geaccepteerd. Naast de hogere productie die men met laserlassen kan realiseren (tot 10 keer sneller dan MIG-lassen), waarderen autofabrikanten vooral de betere kwaliteit. De geringe warmte-inbreng en de hoogwaardige lasnaad leiden ertoe dat producten minder hoeven te worden nabewerkt. Zeker bij dunne plaat weegt dit voordeel zwaar mee. Doordat er weinig warmte in het materiaal komt, blijft de vervorming beperkt of zelfs helemaal achterwege.
Lagere en hogere vermogensdichtheden
Men kan bij laserlassen twee principes onderscheiden: bij een relatief lage vermogensdichtheid (minder dan 105 W/cm2) is de lassnelheid laag en de lasdiepte gering. Bij hogere vermogensdichtheden spreekt men over keyhole lassen: er ontstaat een diepe las en de snelheid ligt hoger. De vermogensdichtheid is een belangrijk gegeven om een stabiel lasproces te creëren. Daaruit volgt dat de spotgrootte een van de belangrijke parameters is. Hiermee wordt de hoeveelheid energie geregeld die per cm2 wordt ingebracht.
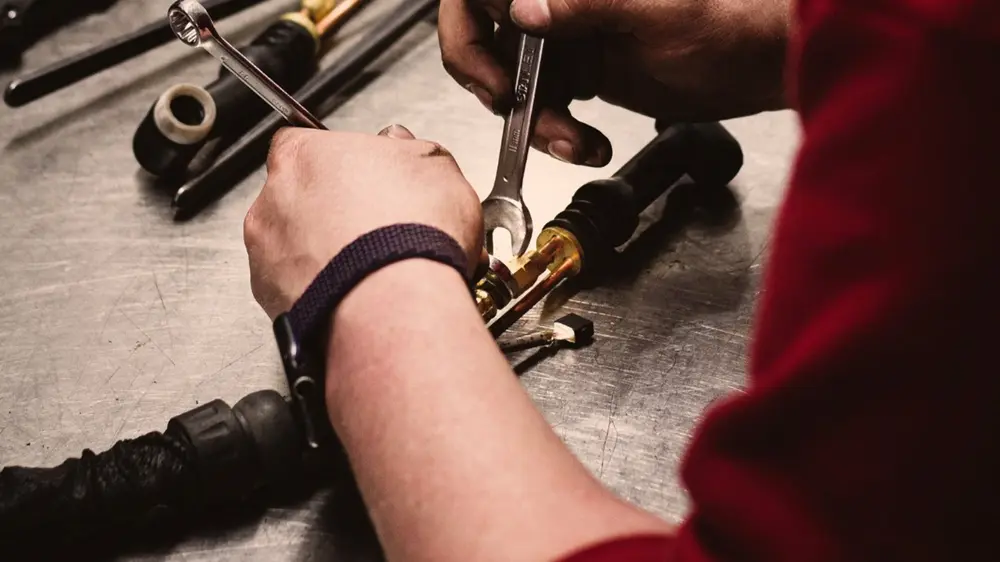
In serieproductie is laserlassen al langer geaccepteerd. Naast de hogere productie die men met laserlassen kan realiseren (tot 10 keer sneller dan MIG-lassen), waarderen ze vooral de betere kwaliteit
Een andere parameter is het materiaal: hoeveel of hoe weinig energie absorbeert het materiaal dat men wil lassen? Door de sterk geconcentreerde energie-inbreng en de korte duur hiervan, blijft de door de warmte beïnvloede zone in het werkstuk beperkt. Vandaar dat vervormingen niet of amper optreden. Laserlassen leent zich goed voor nieuwe materiaalsoorten, zoals hoogsterktematerialen of slijtvaste materialen. De overvloedige warmte-inbreng van klassieke lasprocessen leidt bij deze materialen tot veranderingen in de eigenschappen, doordat de korrelstructuur door de warmte verandert. Oververhitting zorgt eveneens voor interne spanningen. Met laserlassen vermijdt men dit.
Waarom niet geaccepteerd in kmo's?
Toch is laserlassen in de toeleveringsindustrie, bij de kmo's, nog niet echt een standaardlastechnologie geworden. Dit komt onder andere door de hogere investeringen die men moet doen. Niet alleen is de laserbron veel duurder dan een klassieke lasbron, men moet ook automatiseren. Er komt dus nog een robot bij en men heeft lasmallen nodig. Als daar geen redelijke serie tegenover staat, zullen veel bedrijven naar een andere oplossing zoeken. Anderzijds biedt het tekort aan ervaren lassers tegenwicht: dit kan een argument zijn om juist wel te automatiseren.
Een tweede reden waarom bedrijven vaak vasthouden aan de klassieke lastechnieken – al dan niet gerobotiseerd – is dat laserlassen hogere eisen stelt aan de nauwkeurigheid van de componenten die men gaat verbinden. Zeker bij een stompe lasnaad heeft er lange tijd gegolden dat de breedte van de spleet beperkt is: minder dan 0,15 mm. Dit argument weegt tegenwoordig echter minder zwaar, omdat de technologie meer vergevingsgezind is geworden en doordat bedrijven door het automatiseren van klassieke lasprocessen toch al hoogwaardigere componenten vragen.
Duitse onderzoekers hebben een oplossing ontwikkeld om ook in de staalconstructie laserlassen toe te passen
Zeker met hybride laserlassen – de combinatie van laserlassen met MIG-MAG-booglassen – kan men een bredere spleet overbruggen met het booglassen en de typische diepe las (keyhole) realiseren met de laser. Wil men met MIG-lassen bepaalde dieptes bereiken, dan moet er meer ampère stroom worden gebruikt, met alle nadelen van dien.
Een tweede oplossing om een bredere vooropening (tot 0,5 mm) te overbruggen, is de zogenaamde Wobble-technologie, ofwel oscillerend laserlassen (soms ook wel roerlassen genoemd). Met behulp van spiegels of lenzen maakt de laserstraal een roterende beweging, waardoor het smeltbad verbreedt en men dus een grotere vooropening kan lassen. Dit kan doordat de CO2- of Nd:YAG-laserbron de jongste jaren vaak vervangen wordt door een fiberlaser. Daarnaast blijkt deze techniek de kwaliteit van de lasnaad te verhogen, vergeleken met laserlassen met andere bronnen. Ook is het makkelijker om vulmateriaal toe te voegen.
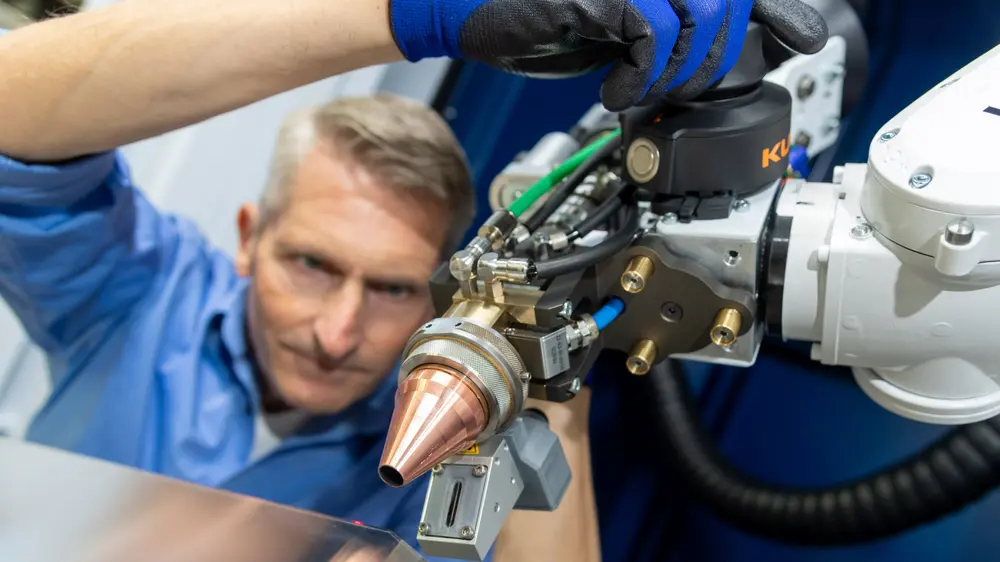
Geringe warmte-inbreng
Naast de esthetische kwaliteiten van een laserlasnaad is de geringere warmte die in het werkstuk komt het belangrijkste argument om naar laserlassen te kijken. Dit geldt voor heel veel toepassingen. Lichtbooglassen springt niet efficiënt om met de energie, die vooral als warmte in het werkstuk terechtkomt en slechts voor een deel in de lasverbinding zelf. Laserlassen heeft daar geen last van, omdat de energie sterk gebundeld wordt en telkens slechts heel korte tijd in het werkstuk komt. Hierdoor zullen er bij laserlassen amper spanningen in de constructie ontstaan. Daarnaast kunnen bij het MIG-lassen van bepaalde legeringen de eigenschappen veranderen door de warmte, of kunnen er zelfs legeringselementen loskomen. Na het lassen en weer afkoelen, is de microstructuur van het materiaal gewijzigd. Als dat ongewenst is, dan is laserlassen zeker een oplossing.
Opdelen van laserstraal
Een vrij nieuwe ontwikkeling bij laserlassen is het opdelen van de laserstraal, bijvoorbeeld in een kern en een ring daaromheen. Dit heeft als voordeel dat er ook bij hoge lassnelheden amper lasspatten ontstaan. Dat bespaart nabewerking.
In een project samen met de Duitse automobieltoeleverancier Benteler gaat Trumpf nog een stap verder door met BrightLine Weld de laserstraal eerst te verdelen in een kern en een ring. Met een nieuwe multifocusoptiek wordt deze ring-kernstraal nog eens verdeeld in vier stuks, die gelijktijdig in één smeltbad actief zijn. Hierdoor blijft het keyhole tijdens het lassen open en kunnen verontreinigingen ontsnappen, bijvoorbeeld als men aluminium last. Tot nog toe is dat namelijk een van de problemen bij het laserlassen van aluminium: als het keyhole niet lang genoeg open blijft, kunnen verontreinigingen niet meer ontsnappen en ontstaan er oncontroleerbare poriën in de lasnaad. Met de nieuwe technologie van Trumpf voorkomt men dit dus, waardoor men ook aluminium met een hoge snelheid kan laserlassen.
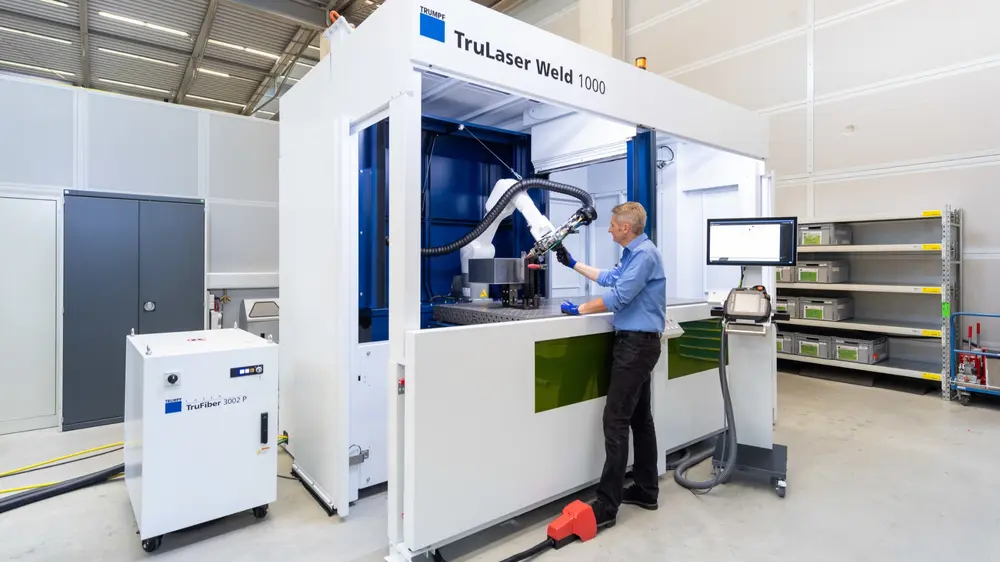
Ook staalconstructies laserlassen
Een sector waar laserlassen tot nog toe niet wordt toegepast, is de staalconstructie. Het lassen van grote constructies, uiteenlopend van een zeecontainer, het chassis van een vrachtwagen tot een brug of nog groter, is nog altijd het domein van onder poeder of met beschermgas lichtbooglassen. Een team wetenschappers van het Fraunhofer IWS (straaltechnologie) in Dresden heeft recent samen met partners uit de industrie een oplossing ontwikkeld om ook in deze sector laserlassen toe te passen. Een van de drijfveren achter deze ontwikkeling is de reductie van het energieverbruik.
Een groot deel van de energie die nodig is voor onder poeder lassen van een staalconstructie gaat de stalen balken en platen in en wordt niet gebruikt voor de eigenlijke lasverbinding. Dit komt doordat de lichtboog een geringe energiedichtheid heeft. Na het lassen moeten deze constructies vaak gericht worden om de vervorming door de warmte-inbreng teniet te doen. Dat kost opnieuw energie. Door over te stappen naar laserlassen zeggen de onderzoekers tot wel 80% minder energie nodig te hebben in vergelijking met het onder poeder lichtboogproces. Ze hebben hiervoor een hoogvermogenlaserbron gebruikt in combinatie met een multi-pass-narrow-gap-lastechniek. Met deze MPNG-techniek kan men, gebruikmakend van vulmaterialen, spleten tot 2 mm gemakkelijk overbruggen.
De voordelen van laserlassen beperken zich niet tot de geringere energiebehoefte. Tijdens het lassen van de demo-opstelling – een 4 m lange giek van een kraan – van 30 mm dikke staalplaten werden de totale kosten gehalveerd. Vergeleken met lassen met beschermgas (bij platen tot 20 mm dik) is de kostenreductie zelfs tot 80%. Dit komt zowel door de geringere hoeveelheid energie die nodig is, tot 85% minder vulmateriaal dat nodig is, en de meer dan halvering van de lastijd, alsook doordat men de constructie daarna niet meer opnieuw hoeft uit te richten. De warmte-inbreng is zo gering dat de constructie tijdens het lassen niet vervormt. Vanuit het oogpunt van kwaliteit komt daar nog bij dat de lasnaad 100% correct is, wat bij onder poeder lassen lang niet altijd het geval is.
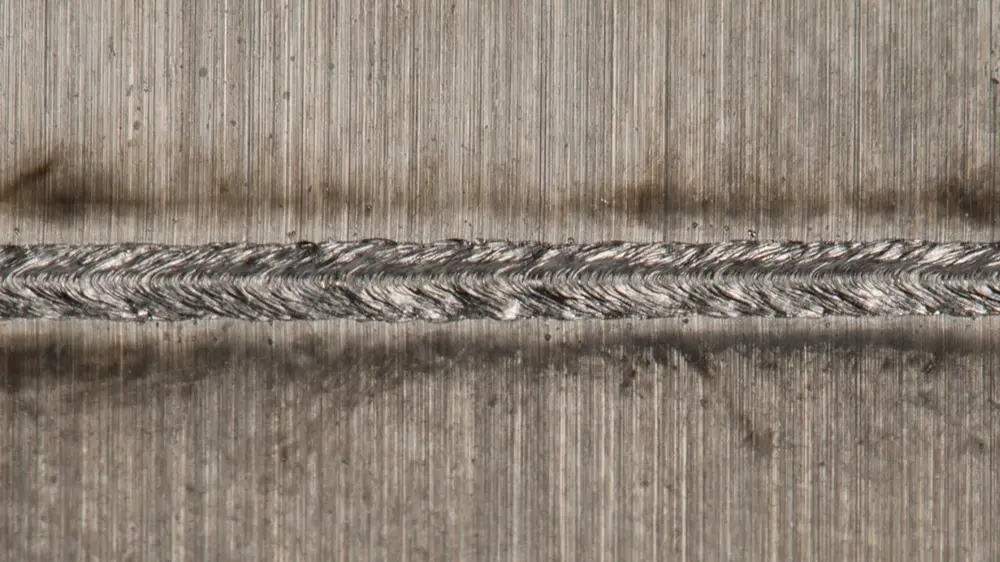