Vitens optimizes energy consumption of critical pumps
Sensors and AI algorithms show where and how to save energy
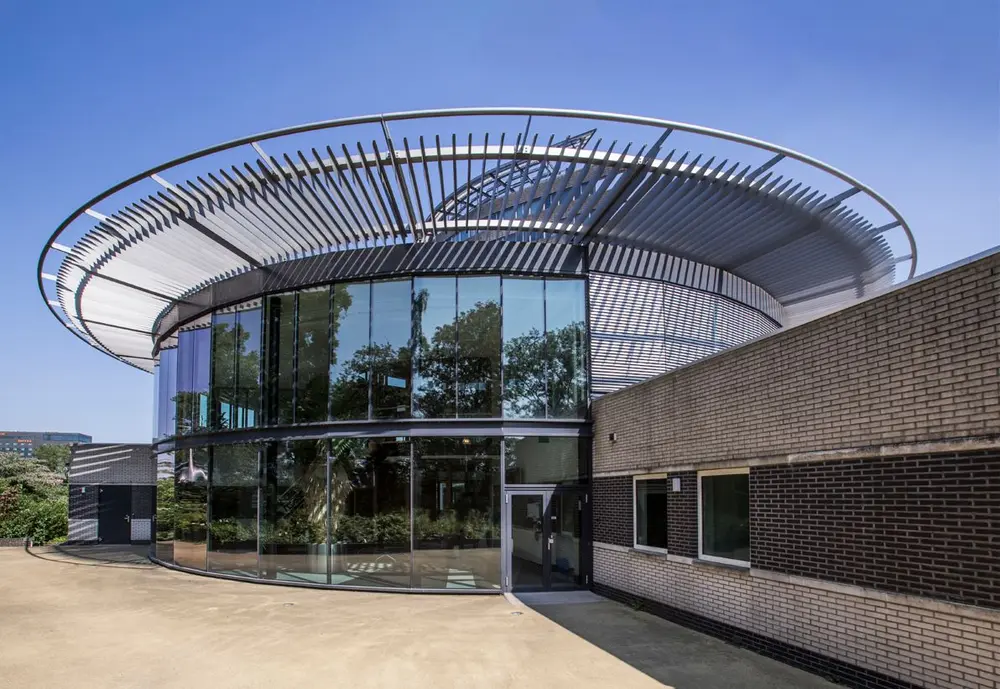
"Every Drop Sustainable," that's the vision at the heart of Vitens, the largest drinking water company in The Netherlands. The utility delivers high-quality drinking water to 5.6 million people and companies in 7 of the 12 Dutch provinces. Vitens understands that reliable drinking water is a necessity for our health and well-being, and securing the supply of this essential resource has to be sustainable and cost effective. As a company that places global responsibility at the heart of its long-term vision, Vitens is committed to creating a sustainable water ecosystem by 2030.
Up to 40% of energy used by industrial equipment is wasted due to operational inefficiencies, process-machine mismatches and developing damage
proof-of-value pilot
To this end, Vitens is investing in innovative solutions, using data smartly to improve its operational performance. Through continuous (real-time) measurement and the use of algorithms, model calculations and scenario analysis, a more constant and reliable drinking water quality and quantity can be produced and delivered. This sets Vitens at the forefront of water industry innovation to improve efficiency and sustainability. Reducing energy consumption and emissions plays a key role in this journey for Vitens, especially in light of climate change issues, a volatile energy market and rising energy prices. Pumps are the lifeblood of Vitens' daily operations with the majority of electricity consumption used in groundwater extraction and clean water distribution. Improving pump performance and efficiency will therefore have a positive impact on Vitens' operations in reducing energy consumption, costs and environmental impact.
Vitens implemented an electrical signature analysis-based system to undertake a proof-of-value pilot at one of the production facilities. The aim of this pilot was to demonstrate the ability of a continuous asset monitoring system to improve the performance and energy efficiency of critical pumps.
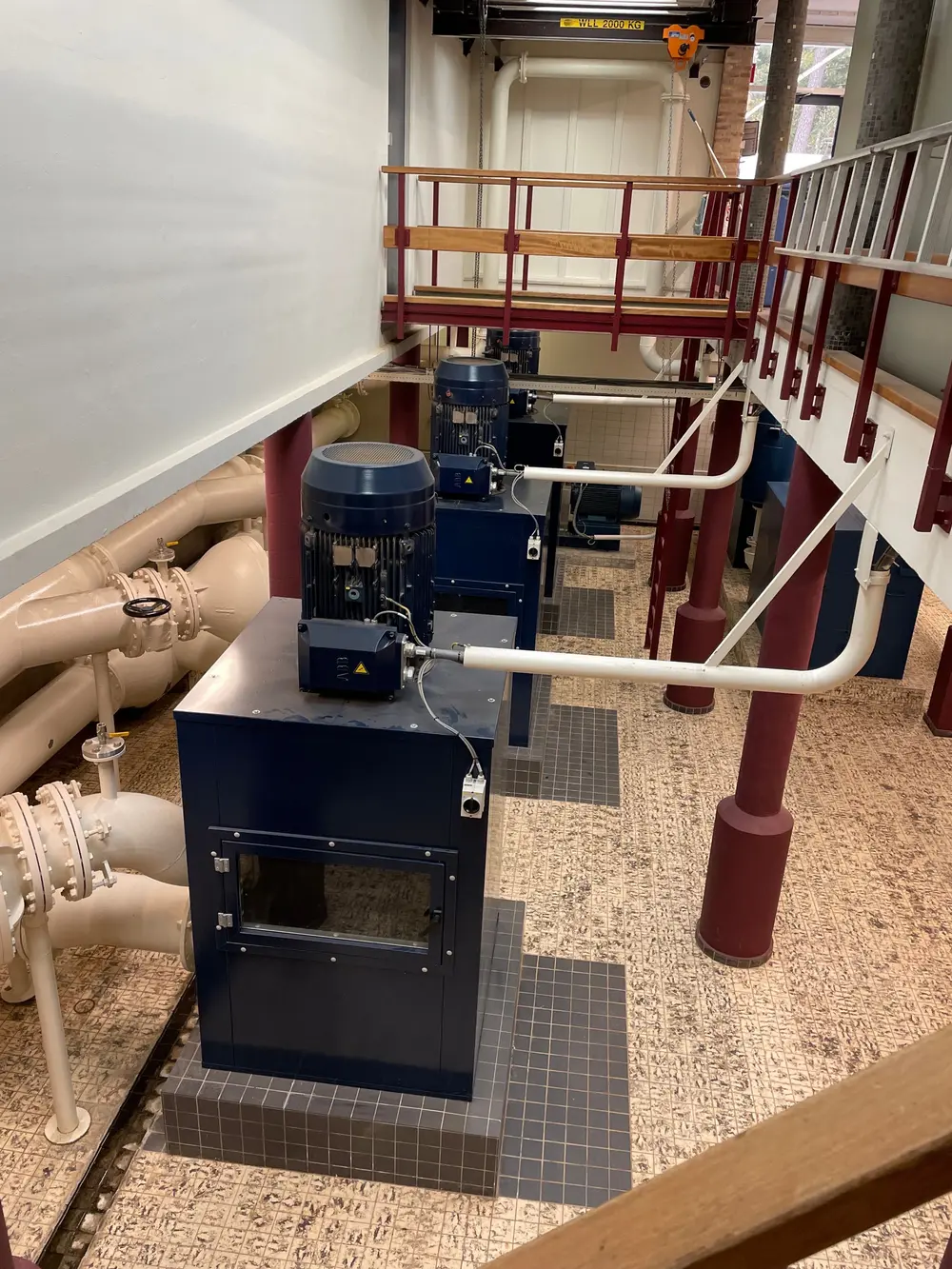
Analyzing a vast water network
To be able to continuously supply reliable and affordable drinking water, Vitens requires a vast drinking water infrastructure. 117 extraction fields with 1,250 extraction wells for groundwater extraction, 100 water treatment works, 49,000 kilometres of water mains and 1,400 employees are needed to deliver 350 million m3 of water annually across a large area of The Netherlands. At the heart of this are thousands of pumps including borehole pumps and clean water distribution pumps.
In 2021, energy consumption across the Vitens network amounted to 171 GWh. Vitens has ambitious plans to reduce this level of energy consumption as part of their 2030 sustainability goals. It has been estimated that across industry globally up to 40% of energy used by industrial equipment driven by electric motors is wasted due to operational inefficiencies, process-machine mismatches and developing damage. This therefore provides quite a large scope for efficiency improvements across all industries.
The Vitens production facility in Hoenderloo, in the Dutch province of Gelderland, was chosen as the optimal location to perform this proof-of-value pilot with Samotics. At this facility, Vitens pumps water to the surface using a group of borehole pumps. After being treated, the clean water is distributed further to three locations via dedicated pump stations on site.
The total pump station efficiency improved by 7.1%. This translates to yearly electricity savings of €2,500
Rein Wuestman, Process Engineer of the Water Expertise Center at Vitens about the project: "With water production coming under increasing pressure, we are committed to creating a sustainable future. Digitizing and automating water network management processes is critical to this approach. Our partnership with Samotics has clearly demonstrated how optimizing pump operations through continuous insights and smart data can immediately reduce energy consumption, costs and emissions – with minimal investment and implementation costs."
Implementing an advanced analytics solution
Since 2010, Vitens has been working on the innovation program SLIMM, which stands for 'Self Learning Integrated Model based Management'. The aim of this project is to digitize and automate water network management processes, so that the quality of the drinking water produced and distributed can be continuously controlled, and as efficiently and effectively as possible. One key element of the Hoenderloo pilot was to determine if Samotics' advanced analytics solution could be integrated with Vitens' SLIMM system. This was successful.
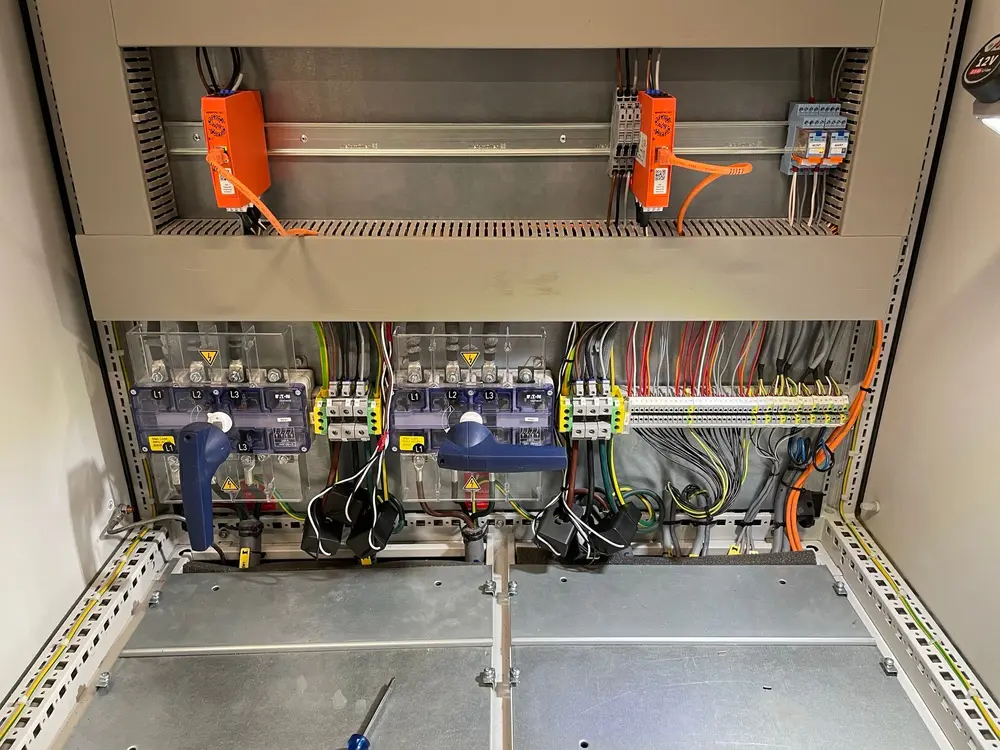
Samotics' SAM4, and ESA-based analytics solution, was implemented to continually monitor all of the 17 pumps at the Hoenderloo production facility and to determine its ability to locate and diagnose energy waste for the pumps and generate solutions to these issues to help Vitens lower energy consumption, costs and associated emissions for these pumps. SAM4 Energy focuses on monitoring the full efficiency of the pump motor set-up in the field, distinguishing motor and pump efficiency per asset (component efficiency), looking at asset efficiency (full pump set-up) and higher level efficiency (like pumping stations with co-located pumps).
The system consists of energy sensors, which were installed inside the motor control cabinet for the pumps to gather electrical data; a gateway for edge processing and data distribution; and access to Samotics' benchmark analytics platform to transform this electrical data into asset performance/efficiency recommendations. With no sensors needing to be installed on any of the pumps themselves, the installation could be performed quickly and data analytics could commence.
By incorporating advanced analytics into their water management strategy and systems, Vitens was aiming to determine where these pumps were not running under the most efficient modes of operation (as close to best efficiency point as possible) or could potentially be outsized for purpose.
Locating pump energy inefficiencies and generating solutions
During the pilot, a focus was placed on three clean water distribution pumps that form the core of a pumping station that distributes clean water to Otterlo/Ede, located not far from the Hoenderloo production facility. These pumps are critical to the supply of water to customers during both peak and non-peak times. It is quite common to have multiple pumps of different sizes to work together in specific locations to meet demand variations. The three clean water distribution pumps include two larger 55 kW distribution pumps (RNP8 and RNP9) and a smaller 11 kW distribution pump (RNP7). See Figure 1 for an overview of the set-up.
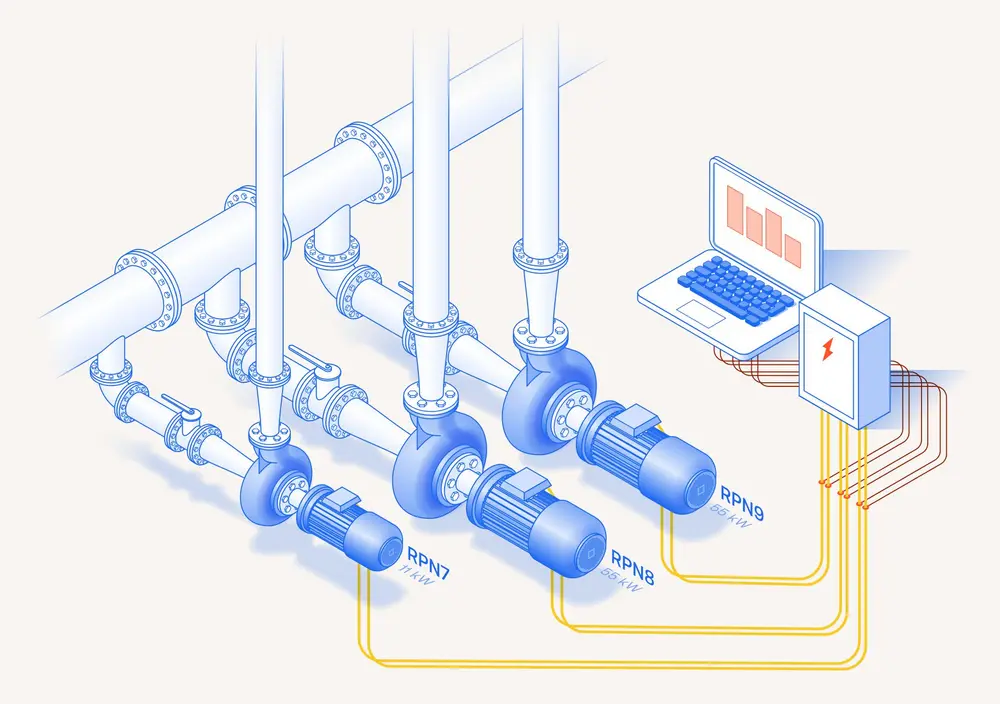
Following sensor installation, the SAM4 Energy platform informed Vitens that the two larger pumps (RNP8 and RNP9) were often used inefficiently to supply flow rates that could be independently covered far more efficiently by the smaller pump. SAM4 Energy further determined that a significant part of the energy losses were due to the mode of operation introducing operational efficiency losses in the pump and associated electric motor accounting for about 10% of total efficiency losses.
Implementing simple process changes
Vitens implemented two simple setting changes to achieve more efficient pumping during low-flow periods. In phase one of these activities, the changeover flow threshold was adjusted: the flow threshold at which the 11 kW pump delivered flow was increased, as the 11 kW pump could deliver the low flow independently and more efficiently than two 55 kW pumps. The resulting flow, energy consumption and efficiency were thereafter tracked using the SAM4 Energy platform.
The second phase of this operational change increased the speed of the 11 kW pump in order to further widen the useful operating range of the smaller pump to deliver increased flow at the required pressure. This was performed by increasing the supply frequency of the VFD, without exceeding the motor's nominal power and the pump's capabilities. This resulted in a larger feasible flow range for the 11 kW pump, only switching on the larger pumps when this was truly necessary.
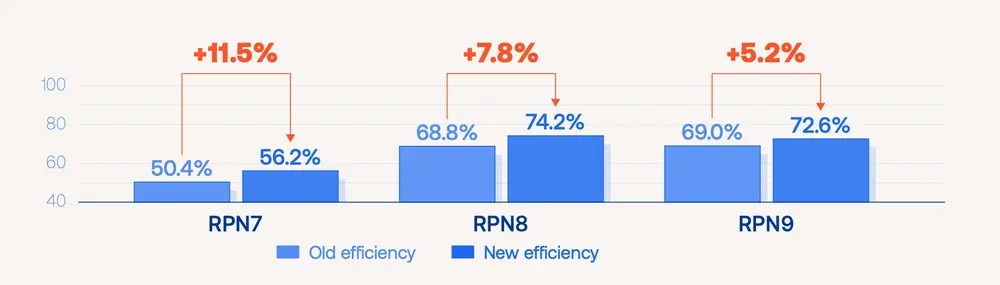
Validating results
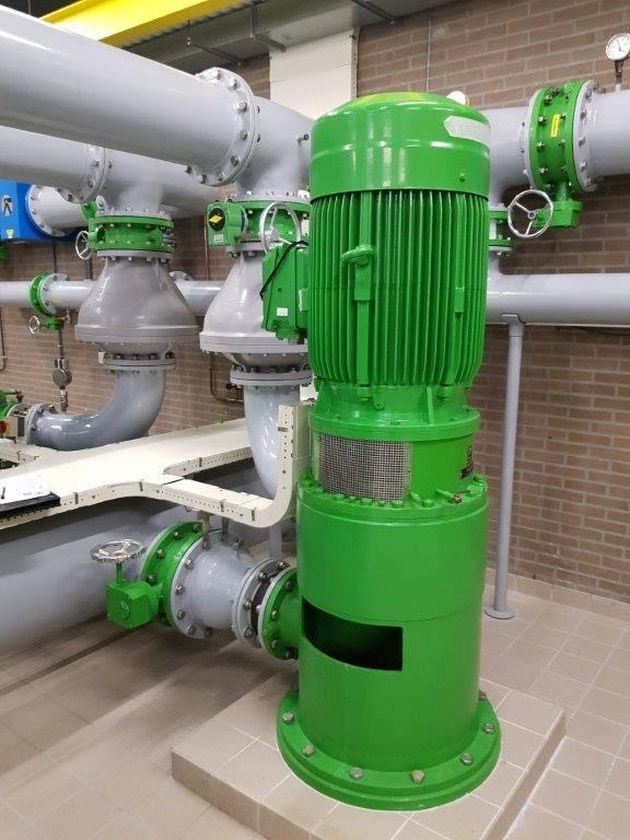
Once these simple process changes were implemented, the improvement in the situation could be seen immediately in the energy monitor and the generated pump curve. The relatively simple operational changes could be made without additional investment and resulted in all three pumps operating closer to their best efficiency points. This increased pump efficiency and reliability. The total pump station efficiency improved by 7.1%, taking into account the distribution of running time, pressure and flow in the old and new situations. This translates to yearly electricity savings of €2,500 across the three pumps and an associated reduction of 9.2 tonnes of CO2 based on energy reduction alone.
An additional point of significance is the fact that inefficient operation can double the chance of failure and shorten lifespan of industrial equipment. This implies that further savings can be accrued from improved operational health.