ELKE AANDRIJVING HAAR EIGEN PLC?
Alternatieven voor centrale aansturing
Een belangrijke trend in onze productiebedrijven is om in meer situaties met modulaire machines te werken. Een flexibele productie vraagt om makkelijk uitbreidbare en aanpasbare installaties. Een centrale besturing is voor modulaire installaties minder interessant. Steeds vaker zien we een verschuiving naar een aansturing vanuit 'het veld', via slimme I/O's en frequentieregelaars. Maar is dat wel een goed idee? En wat zijn hier de alternatieven?
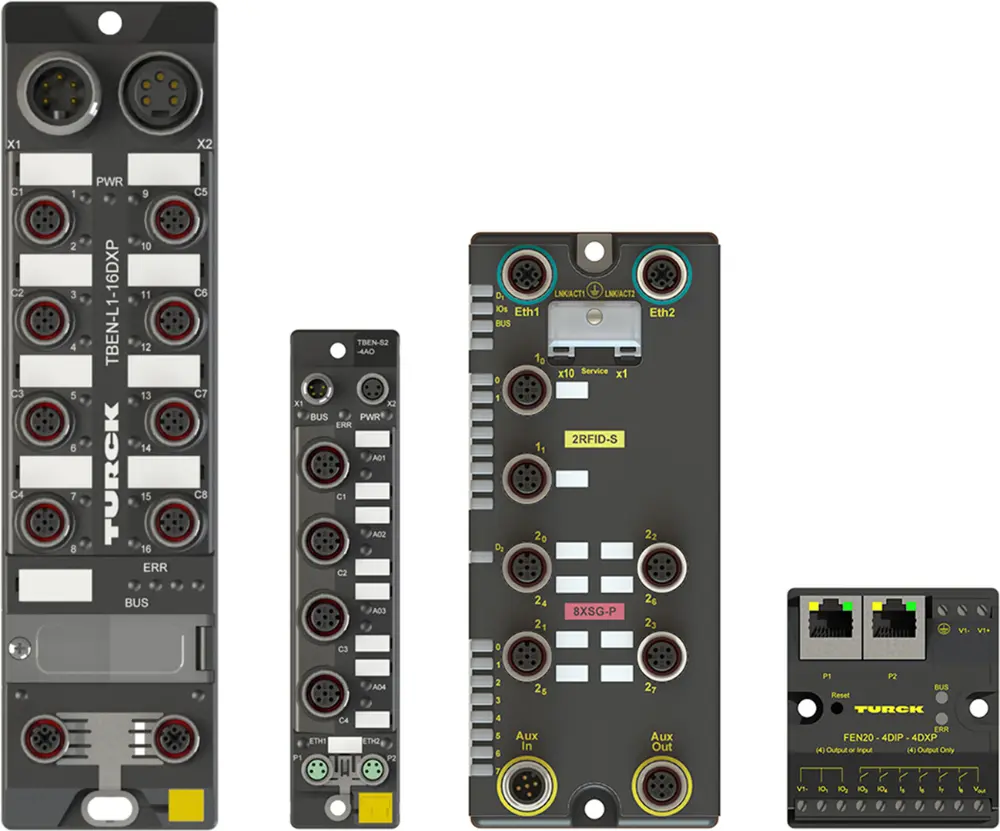
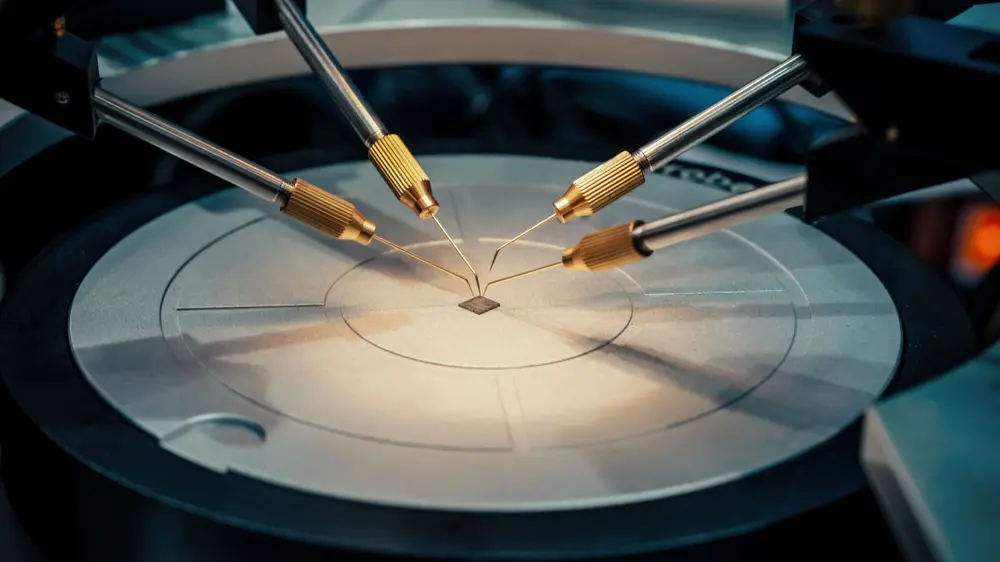
WAAROM DECENTRALISEREN?
De tijd dat een productieomgeving er dertig jaar lang hetzelfde uitzag, is stilaan voorbij. Er wordt vanuit de vraagzijde meer flexibiliteit gevraagd en een modulaire opbouw van het machinepark maakt het makkelijker om zich aan te passen aan nieuwe situaties en productievragen. Ook de integratie van meer componenten in een groter netwerk zorgt ervoor dat er meer informatie aanwezig is in onze machines, die via I/O's gecommuniceerd kan worden met de andere componenten van de installatie. Het zou zonde zijn, mocht die informatie ongebruikt blijven.
Traditioneel worden motoren aangestuurd door een centrale PLC, die vanuit de verdeelkast als master zijn slaves in de installatie aanstuurt. Als die slaves zich in het veld bevinden, spreken we over remote aandrijving. Maar een modulaire opbouw betekent an sich dat slaves op elk moment ook master moeten kunnen worden, wat impliceert dat ze zelfstandig beslissingen moeten kunnen uitvoeren en die ook communiceren met de anderen componenten. Dat heeft repercussies voor de opbouw van de sturing van de installatie, want er moet ook intelligentie voorzien worden in de I/O's die deze taak op zich moeten kunnen nemen.
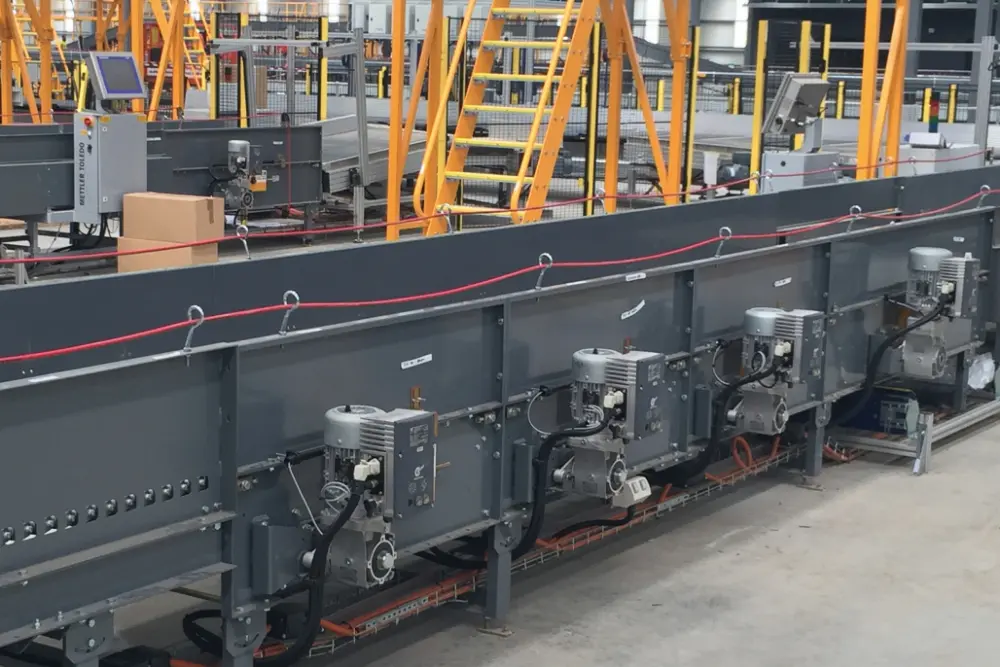
OPLOSSING: DECENTRALE AANSTURING
Technisch is het perfect mogelijk om dezelfde functionaliteiten te creëren met een modulaire opbouw. Het zou bijvoorbeeld opgelost kunnen worden door bij elke module telkens een aparte PLC te voorzien die de plaatselijke I/O's verwerkt. Dat leidt evenwel tot een duurdere installatie en het is ook niet evident om een component vol gevoelige elektronica zomaar in een productieomgeving te plaatsen. Temperatuurschommelingen, contact met schadelijke stoffen en EMC-problemen zijn maar enkele van de mogelijk negatieve invloeden. Een oplossing kan zijn om de PLC ook hier in een aparte verdeelkast te plaatsen, maar de extra kosten voor behuizing en bekabeling rijzen dan nog verder de pan uit.
ALTERNATIEVEN
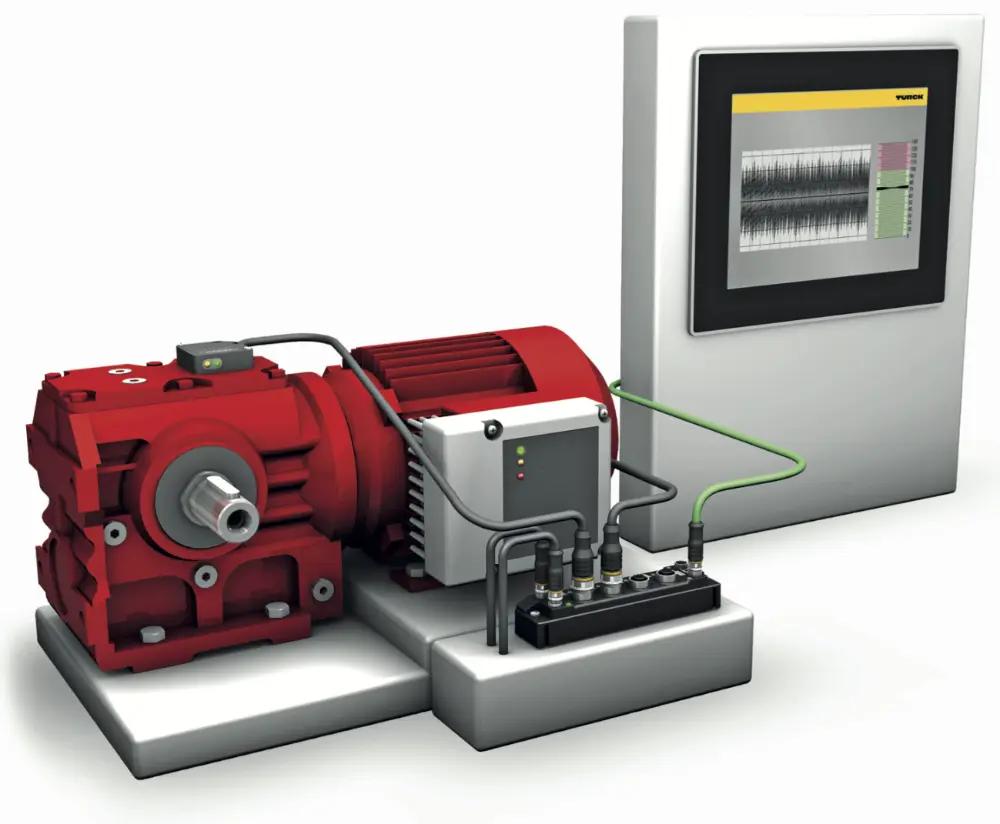
I/O-blok met PLC‑functionaliteiten
In bepaalde gevallen kan een field logic controller de taken van een PLC overnemen. Die field logic controller is in feite een standaard-I/O die voorzien is van PLC-software om logische taken uit te voeren. Hij kan ter plaatse eenvoudig parameters van drives en dergelijke opnemen en op basis daarvan zelf bepaalde acties ondernemen. Eerst terugkoppelen naar de PLC via de remote I/O block om dan van daaruit de bevelen te sturen naar actuatoren is dus niet langer nodig. Dat scheelt natuurlijk een pak in bekabeling. Voorwaarde is dat het I/O block in de mogelijkheid is om alle signalen van diverse I/O's te verwerken, dus alle gangbare protocollen zoals ethernet, Modbus, PROFINET en CANopen moeten aangesloten kunnen worden op het block. Twee eenvoudige voorbeelden illustreren deze werkwijze.
Stel dat we een kwaliteitscontrole hebben in een voedingsbedrijf door middel van een gewichtsmeting. Daarbij wordt nagegaan of het vulniveau van een zakje saus voldoet aan de vereisten van de batch. Via een field logic controller kan het gegenereerde signaal rechtstreeks de pneumatische arm aansturen die het betrokken zakje van de band duwt indien het te zwaar is. Er is dus geen terugkoppeling naar een PLC nodig om dergelijke eenvoudige acties uit te voeren.
Een tweede voorbeeld betreft een niveausensor in een vloeistoftank in een zeer corrosieve omgeving. Een PLC zou hier in een aparte kast geplaatst moeten worden, met alle extra kosten die daaraan zijn verbonden. Een I/O block met PLC-functionaliteit kan een beschermingsgraad IP69K hebben, waardoor deze wel onmiddellijk bij de tank geplaatst kan worden. Een overschrijding van de minimumwaarde kan dan de instructie geven om de tank bij te vullen, een overschrijding van de maximumwaarde kan bijvoorbeeld een pomp inschakelen om de overtollige vloeistof weg te krijgen. Merk ook op dat deze werkwijze toelaat om de I/O's rechtstreeks te integreren in een overkoepelend systeem, waarmee het systeem een mooie bijdrage levert aan 'de slimme fabriek'. Door de logica toe te voegen op I/O-niveau, kunnen gebruikers via ethernet rechtstreeks vanop hun pc of handheld hun componenten programmeren, terwijl ook de mogelijkheden voor monitoring op afstand in volle ontwikkeling zijn.
Daarnaast zijn er ook nog bijkomende voordelen zoals het ontlasten van de PLC, de mogelijkheid om ook veiligheidsfuncties in de I/O-block te laden en de goedkopere set-up van dit systeem.
Frequentieregelaar met PLC-functionaliteiten
Bij toestellen die werken op basis van frequentieregelaars zoals pompen en aandrijvingen is er ook de trend om de frequentieregelaar direct bij de aandrijving te plaatsen, om zo de bekabelingskosten te verminderen. Die frequentieregelaars kunnen voorzien worden van sommige PLC-functies, zodat er in het veld bepaalde zaken overgenomen kunnen worden. Dat is voornamelijk handig bij drives met kleinere vermogens in grotere installaties (intralogistiek, luchthaven, voedingssector …). Die kleinere drives zijn traditioneel 'domme' toestellen. Hen voorzien van een aparte PLC zou te veel van het goede betekenen, maar toch is er een wil om ook deze toestellen slimmer te maken. Dat kan door ze te voorzien van PLC-based functies, die niet alleen gecommuniceerd worden met de drive, maar ook met de andere drives en het overkoepelende systeem (Master/slave-werking). Zo kunnen remcontrole, STO, SS1 en andere veiligheidsfuncties ingeladen worden, kan men eenvoudige automatiseringstaken uitvoeren, is er een energiebesparende functie bij deellast, vierkwadrantenwerking, positiebepaling via vectorcontrole en ga zo maar door. Hoeft dit na veertig jaar het einde te betekenen van de PLC? Uiteraard niet. Deze vorm van decentraal aansturen kan enkel beperkte automatiseringstaken uitvoeren, voor complexe taken is en blijft een PLC absoluut nodig.