big data, grote gevolgen
Productie proces automatisering 2022
De productie- en procesindustrie bevindt zich in woelige tijden. Technische ontwikkelingen op het vlak van communicatie, data vergaren, analyseren en ‘slim inzetten’ gaan hard. Dit laatste is echter niet eenvoudig en vraagt om inzicht, ondernemerschap, standaardisatie en het opbouwen van kennis en ervaring. Tijdens PPA 2022 – Productie Proces Automatisering – werden de uitdagingen rond Industrie 4.0, Industrial internet of things (IIoT) en big data behandeld.
snelle ontwikkelingen
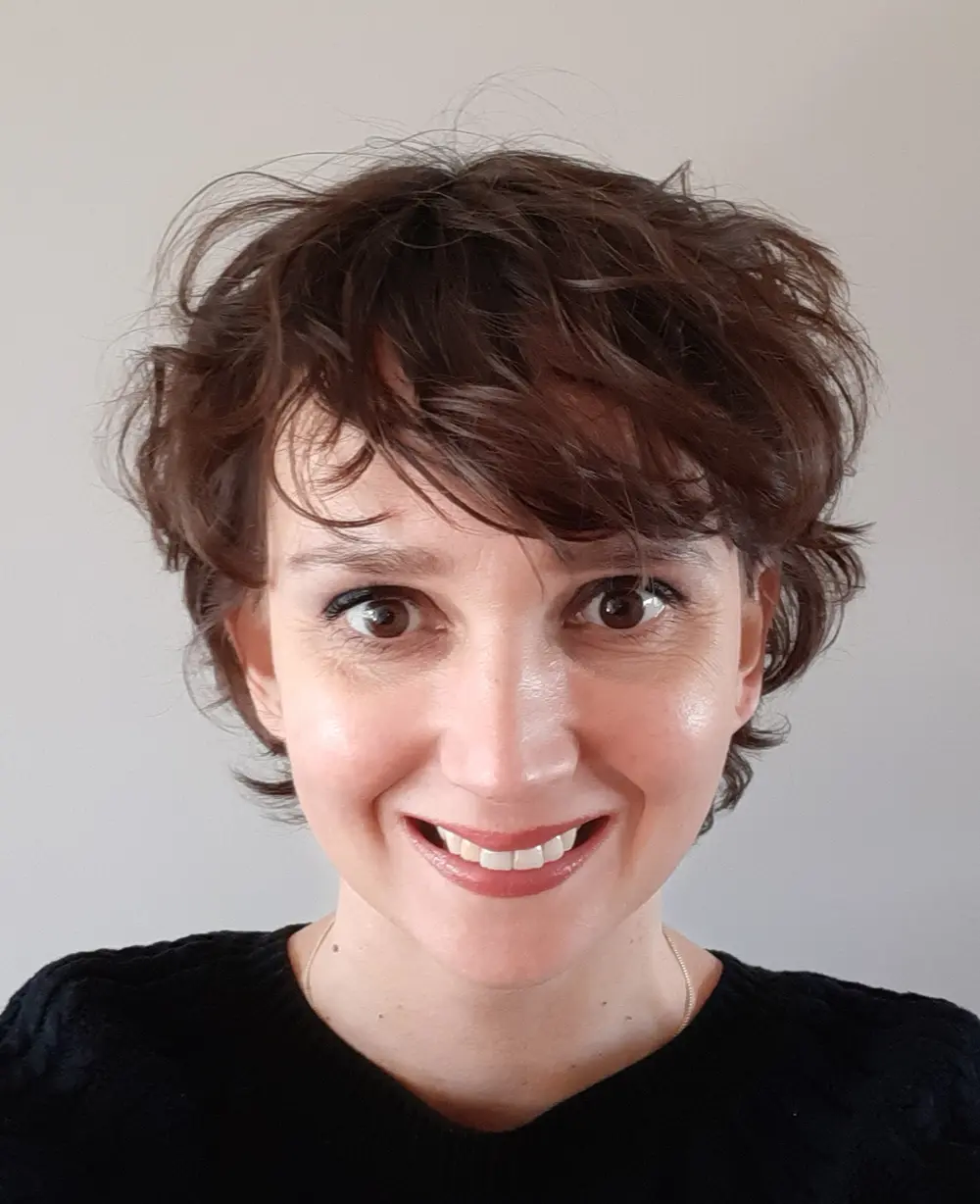
Dagvoorzitter van het PPA – georganiseerd door het Nederlandse collectief van technologiebedrijven FHI – was Susanne van Boxtel. Zij opende het evenement en schetste de situatie waar het onderzoeks- en werkveld op dit moment mee te maken heeft: "De technische ontwikkelingen binnen de productie- en procesautomatisering gaan snel. Big data staan centraal en vormen een basis voor onder meer condition based onderhoud maar ook aanleiding voor praktisch ieder bedrijf om serieus na te denken over cybersecurity."
Standaardisatie en samenwerken
Na de opening gaf zij het woord aan Jacco Opmeer van Shell Global Solutions. Zijn verhaal ging onder meer in op de noodzaak om nauw met elkaar samen te werken in het kader van standaardisatie. De achterliggende gedachte is dat de industrie transformeert door de wensen en behoeften van de maatschappij. Dit is alleen mogelijk wanneer zowel middelen, apparatuur als instrumentatie vernieuwen. En dat kan weer alleen door samen te werken; zowel binnen de keten als met de eindgebruiker.
"Samenwerken binnen de keten en met eindgebruiker"
In een gesprek met Dimitri Reijerman van FHI vertelde Opmeer over de werkgroep ‘Open Process Automation Forum’ (OPAF): "We willen namens het OPAF ons ecosysteem – een groep van eindgebruikers – veel meer gaan betrekken bij technische ontwikkelingen. Daarbij gaat het niet om het verkopen van een product, maar om het ontwikkelen van gezamenlijke oplossingen. Dat is nodig om problemen binnen de procesautomatisering en de lock-in die is ontstaan met onze leveranciers op te lossen. Net als bij de eindgebruiker moeten ook bij leveranciers immers de productkosten omlaag. Hierdoor komen ze in een ‘squeeze’ naar wat zij voor eindgebruikers kunnen ontwikkelen; de ontwikkelkosten voor nieuwe platformen moeten uiteindelijk toch worden doorberekend. Via het OPAF proberen we tot standaardisatie binnen een platform te komen. Hiermee kunnen we sneller stappen maken en uit de lock-in komen. De eerste producten die Open zijn en daarnaast gecertificeerd, komen tegen het einde van dit jaar op de markt."
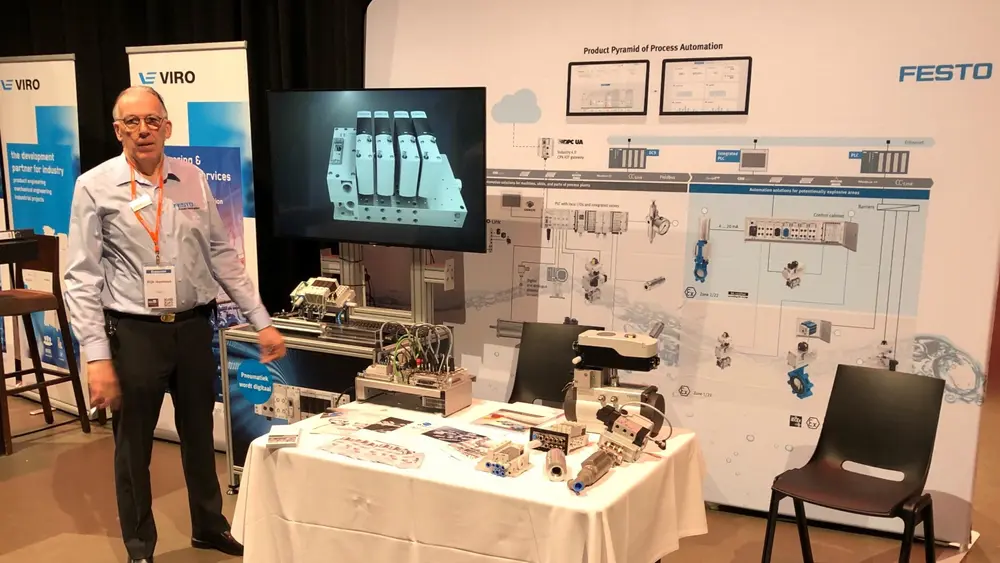
Slim onderhoud
Naast ontwikkelingen op strategisch niveau, waarin de zojuist genoemde standaardisatie en samenwerking zo belangrijk is, gaan ook veel sprekers in op de praktische toepassingen van alle beschikbare technieken. Onderhoud is hierin een geliefd thema. De basis betreft het verzamelen van relevante data om deze in te zetten om onderhoud op het juiste moment uit te voeren. Daarbij zijn een aantal zaken van belang.
Ten eerste de juiste data verzamelen. Hiervoor is het nodig het belangrijkste faalmechanisme van een installatie of asset te kennen. Deze bepaalt of je onderhoud moet uitvoeren op basis van bijvoorbeeld het aantal draaiuren, de warmteontwikkeling of juist trillingen.
Daarbij is het noodzakelijk de juiste meetapparatuur op de juiste manier te plaatsen en uit te lezen. Het lijkt een open deur, maar de praktijk leert dat het foutief kiezen van de sensoren of een foutieve installatie ervan de bron is van veel ellende.
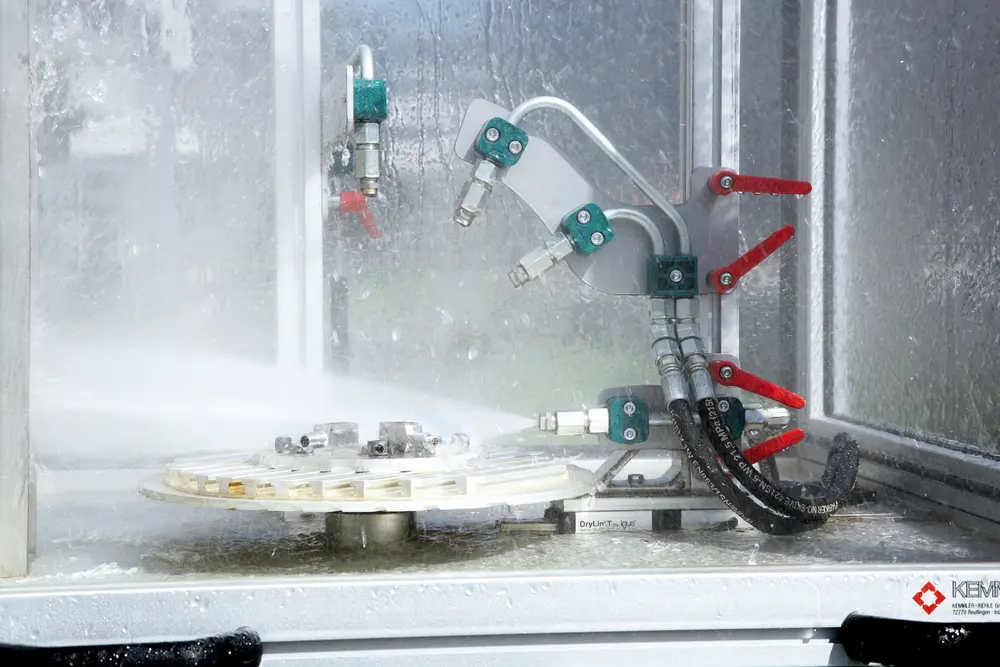
Verder is een geschikte infrastructuur cruciaal voor het kunnen ontsluiten van de benodigde data.
Tot slot is het belangrijk een specialist in huis te hebben die de gemeten waarden op de juiste manier kan interpreteren én op basis hiervan de juiste acties kan formuleren en in gang zetten. Wanneer dit proces goed is opgezet, kunnen bedrijven profiteren van kostenverlaging op vele fronten. Niet alleen gekoppeld aan een lagere onderhoudsbehoefte waarmee wordt bespaard op mensuren en componenten, maar tevens door een hogere betrouwbaarheid en beschikbaarheid van machines en installaties.
Voorbeelden
Tijdens het PPA werden hiervan verschillende voorbeelden gegeven. Zo legde Krohne Nederland uit hoe met specifieke apparatuur pijpleidingen op afstand zijn te monitoren. Het meten van druk, temperatuur en stroomsnelheid in pijpleidingen – en het slim processen van deze data – maakt het mogelijk in een vroeg stadium een eventuele lekkage te detecteren, maar ook om nauwkeurig de plaats van de lekkage te bepalen zodat deze snel en efficiënt is op te lossen. Niet alleen ten behoeve van de inzetbaarheid van het systeem, maar tevens om de veiligheid voor mens, machine en omgeving te waarborgen en milieurampen te voorkomen.
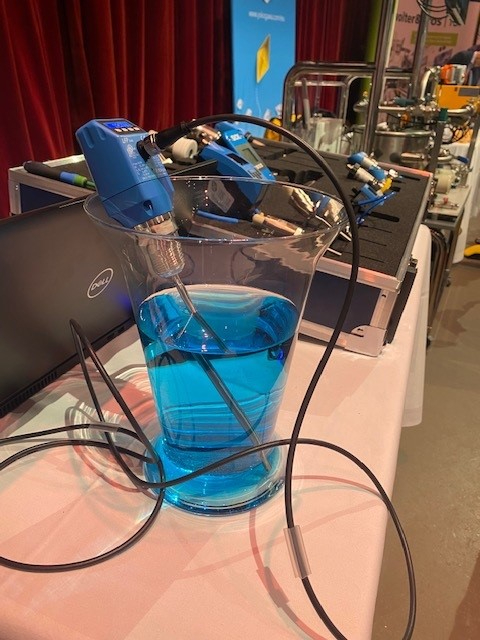
Op eenzelfde manier zijn ook machines in de productietechniek te monitoren. Bijvoorbeeld middels het meten van warmteontwikkeling, opgenomen vermogen (elektromotor), trillingen en drukken. Op de markt zijn vele sensoren en softwarepakketten beschikbaar waarmee deze data zijn te genereren, te analyseren en om te zetten naar bruikbare onderhoudsinformatie of het vastleggen van trends.
Digital twin
Een apart fenomeen dat steeds meer zijn weg vindt in de industrie betreft de zogenaamde ‘digital twin’: een digitaal model van de werkelijkheid. Afhankelijk van het doel bevat de digital twin bepaalde eigenschappen. Een model dat wordt gebruikt voor voorspellend onderhoud van een productiemachine, vraagt – naast de maatvoering – ook om data over de levensduur van componenten, snelheden, drukken, belastingen, dynamische eigenschappen ... Alles wat invloed heeft op de werking van deze machine kan worden opgenomen in het model.
Gaat het om de duurzaamheid van een oplossing, dan zijn weer andere parameters van belang: energie-efficiëntie van de gebruikte assets, wrijving, smering, warmteontwikkeling, inzet van hernieuwbare energiebronnen, tijdstippen waarop de machine draait, regelstrategieën ... Uiteraard ontstaan daarbij overlappen en zullen modellen die door de tijd heen worden opgebouwd en uitgebreid, uiteindelijk geschikt zijn voor diverse doeleinden.
In de markt zijn onder meer oplossingen beschikbaar waarbij een digital twin wordt opgebouwd door het koppelen van verschillende systemen die verschillende soorten data en informatie verzamelen.
Sprekers van AVEVA Select Benelux geven aan: "Al jarenlang passen wij het concept van een Operations Management Interface voor HMI, SCADA en MES toe. Bij deze benadering werkt de operatorinterface over diverse schermen samen en passen deelgebieden zich automatisch aan bij selectie van een specifiek procesdeel door bijhorende informatie weer te geven. De praktijk leert dat dit goed werkt waardoor dit verder is doorgezet naar aanvullende applicaties in het IT- & OT-domein."
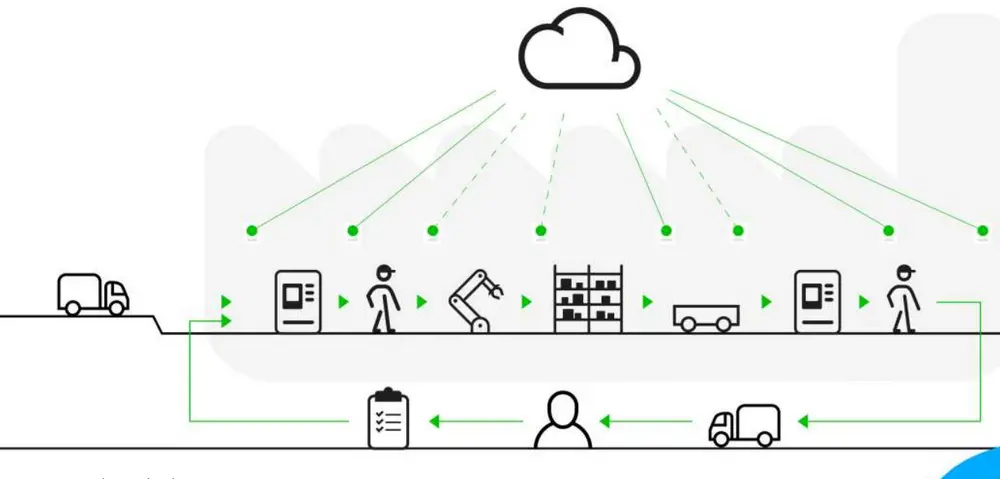
Draadloze data delen
Met als kern ‘big data’ sloot Paul Cobben, sector developer manufacturing bij KPN af met een lezing over ‘the wireless factory’. Zowel in de maak- als de procesindustrie zal het aantal draadloze toepassingen groeien om alle data te verzamelen. Technologieën als 5G, nauwkeurige lokalisatie en edge computing spelen hierin een belangrijke rol.
"Vergeet nooit het aspect cybersecurity mee te nemen"
Overigens niet alleen voor een eenrichtingsverkeer bij het verzamelen van data, maar tevens voor het terugsturen van gegevens om machines aan te sturen waarbij zaken als ultra low latency, inzicht in quality of service en time sensitive networks een rol spelen. Vergeet daarbij nooit het aspect cybersecurity mee te nemen; bewust zijn dat dit fenomeen alles en iedereen betreft is een eerste goede stap.