De juiste grijpers helpen cobots een handje
Meer nicheoplossingen en uitwisselbaarheid zijn de toekomst
Grijpen is vandaag veel meer dan een eenvoudige open-en-dichtbeweging van een parallelle tweepuntsgrijper. Samen met de toenemende complexiteit van cobots, nemen ook de mogelijkheden onder de bijhorende grijpers toe. Veiligheid blijft hierbij een cruciale zorg en fabrikanten vinden dan ook creatieve oplossingen om cobots zo functioneel mogelijk te houden zonder aan de veiligheid te raken.
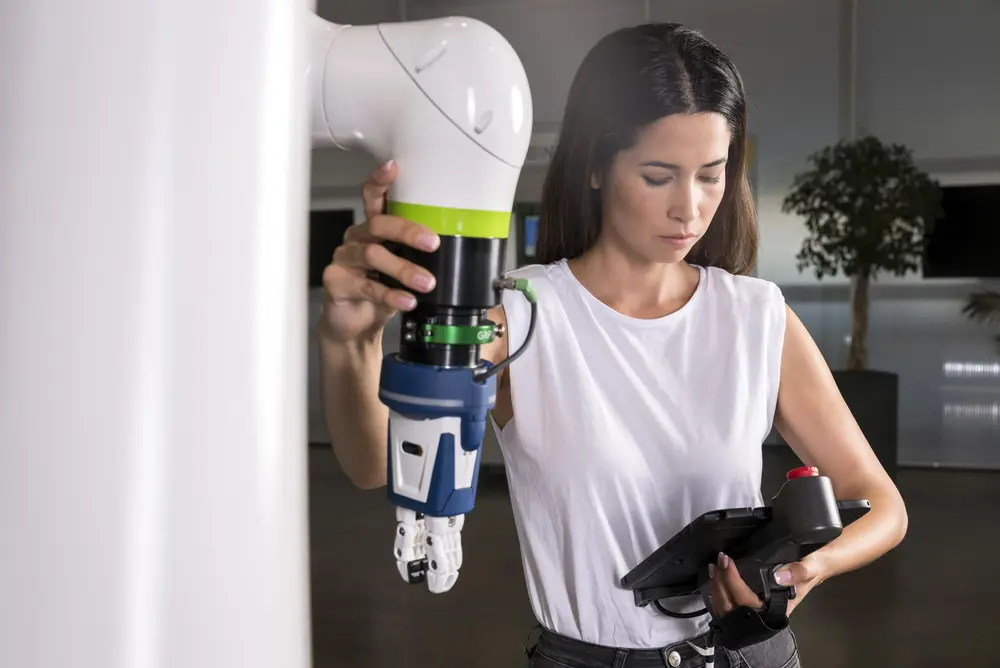
Even kort door de bocht gaan: een cobot is maar zo handig als de grijper die erop gemonteerd is. Met een vrij eenvoudige cobot kunnen met behulp van een slim gekozen of ontworpen grijper toch complexe taken verricht worden. Omgekeerd zal zelfs de beste cobot in combinatie met de foute grijper resulteren in ongewenste performantie. Uiteindelijk is het de specifieke toepassing die allesbepalend is en specifieke eisen stelt aan de cobot en grijper. Het is de grijper die van een standaard cobot een oplossing op maat maakt.
In het algemeen worden robots en dus ook cobots voor steeds complexere taken ingezet. Flexibele installaties zijn bovendien vaak noodzakelijk om de robotica te laten renderen. Zo ontstaat er doorgaans een nood aan zowel zeer algemeen inzetbare grijpers (om verschillende soorten objecten te kunnen manipuleren) als zeer specifieke grijpers (voor het manipuleren van complexe en unieke stukken). De grijpers zelf moeten dus betrouwbaar werken, maar moeten in veel gevallen ook flexibel uitwisselbaar zijn.
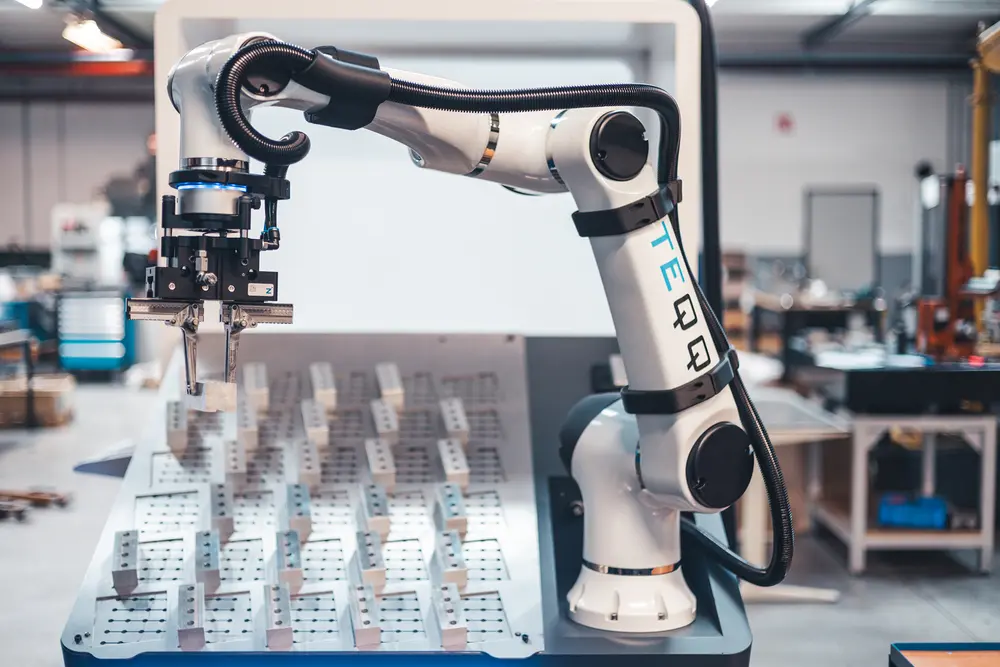
The usual suspects
Hoewel de toepassing met cobots wel degelijk specifieke ontwerpeisen stelt aan grijpers (zie verder), blijven de basistechnieken evenwel dezelfde. Het gaat dus nog steeds om mechanische grijpers (pneumatisch of met servo), vacuümgrijpers en in mindere mate magnetische grijpers. In toevoeging op een grijper wordt er vaak gekozen voor een compenserende module, een tussenstuk dat mechanische trillingen neutraliseert voor een preciezere manipulatie.
Mechanische grijpers
Een mechanische grijper kan zowel op basis van pneumatiek als met servo werken (hoewel er ook grijpers met een stappenmotor werken). Binnen deze soort grijpers zijn er diverse bouwvormen: parallel, hoek, driehoek en lange slag zijn de meest voorkomende. Daarnaast zijn er grijpers die gebaseerd zijn op de natuur: bijvoorbeeld een grijper die werkt als de tong van een kameleon of die een menselijke hand nabootst. Uiteindelijk wordt de keuze tussen deze vele vormen bepaald door het te grijpen product.
Een cobot is maar zo handig als de grijper die erop gemonteerd is
Servo-aangedreven grijpers hebben als voordeel dat ze zeer nauwkeurig, snel en aanpasbaar zijn. De positie en grijpkracht van deze grijpers kan erg precies ingesteld worden, wat bepaalde veiligheidsvoordelen oplevert (zie verder). Daarnaast heeft deze grijper meerdere posities, terwijl een klassieke pneumatische grijper ofwel open ofwel dicht is. Het voornaamste nadeel is dat servogrijpers vaak zwaar zijn en bovendien duur in aanschaf. Een grijper op perslucht waarbij de druk en de flow wordt geregeld combineert de voordelen van beide systemen. Uiteraard is hier wel een extra aansluiting voor perslucht nodig, iets dat wel steeds voorzien wordt.
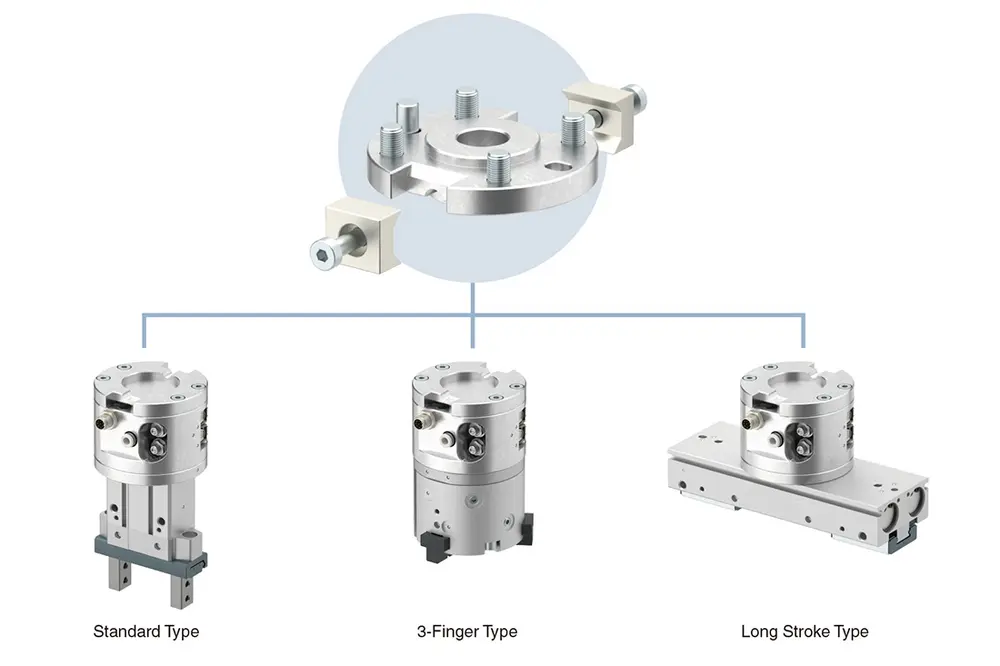
Vacuümgrijpers
Grijpers met vacuüm worden gebruikt voor lichte voorwerpen die slechts aan één zijde te grijpen zijn of die vrij fragiel zijn, zoals vlakke platen, eieren, zakjes ... Voor grotere oppervlakken wordt er steeds meer gewerkt met foamgrijpers, die een zuigkist gebruiken om hefkracht te genereren. Een variant op vacuüm is het Bernouilli-principe. Dit werkt net als de vleugel van een vliegtuig: lucht stroomt snel langs de oppervlakte van de grijper en creëert daardoor een onderdruk, waardoor het product tegen de grijper aan wordt geduwd. Vanwege het compacte en lichte ontwerp, wordt vaak gekozen voor een vacuümnozzle op de grijper.
De aanwezigheid van perslucht is niet altijd noodzakelijk om volgens het vacuümprincipe te werken. Er kan evengoed gebruik worden gemaakt van een compacte vacuümgenerator, die steeds meer specifiek voor cobots wordt ontworpen. Vaak werken deze vacuümgrijpers met een enkele zuignap of een kleine foamgrijper.
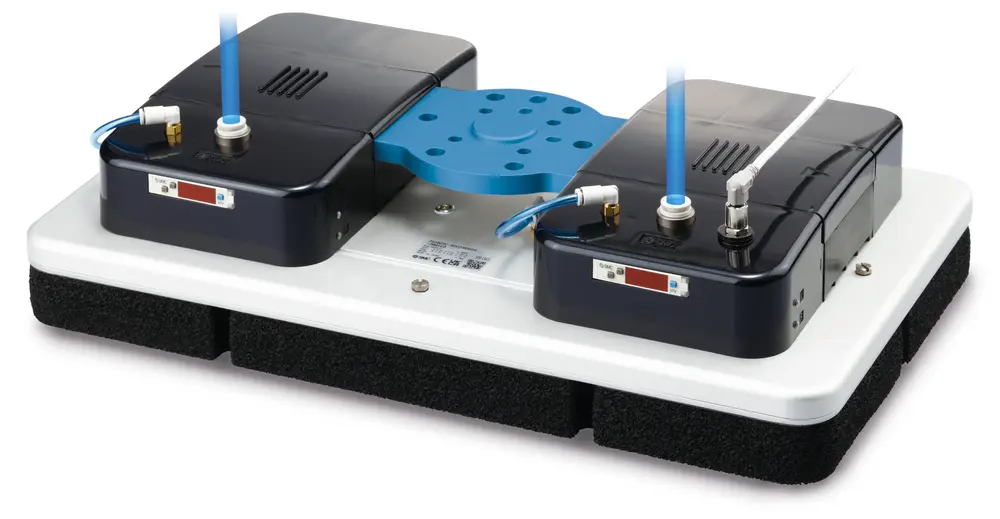
Keuzestress?
Er zijn dus redelijk wat opties op de markt als het op een grijper aankomt. Alles start dus vanuit het te manipuleren object en de snelheid en productiecontext waarin dit dient te gebeuren. Eenmaal een keuze gemaakt voor een bepaalde techniek, kan met calculatiesoftware de juiste, specifieke grijper gekozen worden. Dit bespaart tijd en geeft een goede indicatie van de grootteorde en uitvoering die vereist zijn. Heel wat variabelen worden meegenomen in dit selectieproces: versnellingen, gewicht, afstand tot zwaartepunt ... Op deze manier kan men een gefundeerde keuze maken.
Bij projecten die wat complexer zijn en waar de keuze voor een oplossing niet evident is, is het aangewezen om een test te doen. Heel wat fabrikanten van grijpers bieden dan ook de mogelijkheid om deze installaties uit te testen. Bovendien is het vaak mogelijk om bij aankoop een uitgebreide opleiding te volgen. Enkele fabrikanten leggen hierbij de nadruk op individuele en rechtstreekse interactie met de installatie in kwestie.
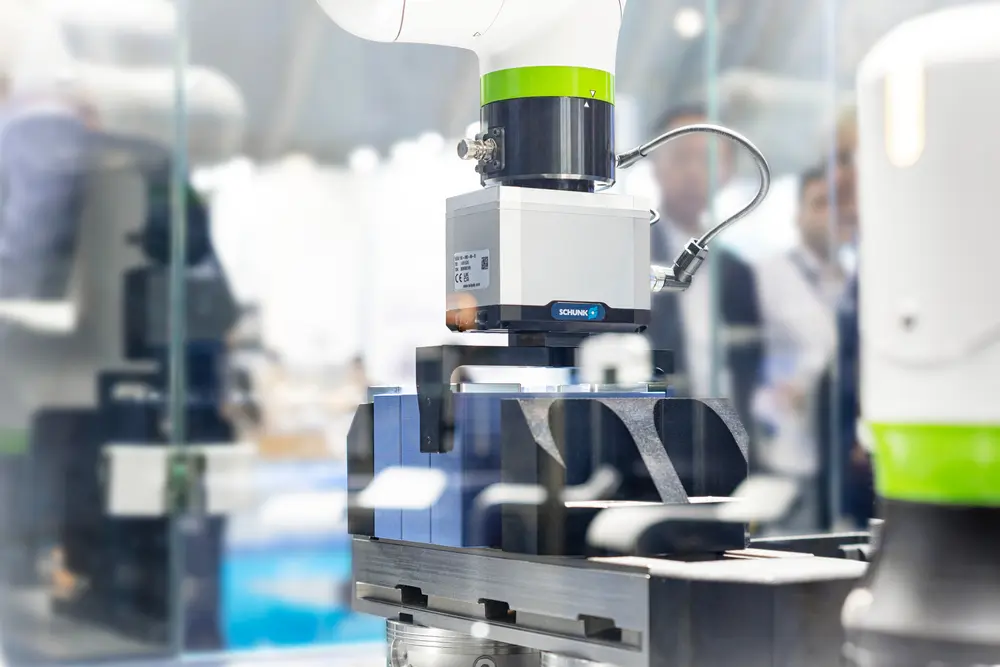
Veiligheid blijft primaire zorg
Wie 'cobot' zegt, denkt meteen ook aan veiligheidskwesties. Steeds meer benadrukken spelers binnen robotica de grijze zone op vlak van veiligheid die ontstaan is door het gebruik van cobots. Alles hangt immers af van de specifieke toepassing. Het gaat dus niet alleen om de snelheid waarmee de cobot beweegt of de kracht die de arm kan uitoefenen, maar ook de grijper en het gemanipuleerde object spelen een cruciale rol.
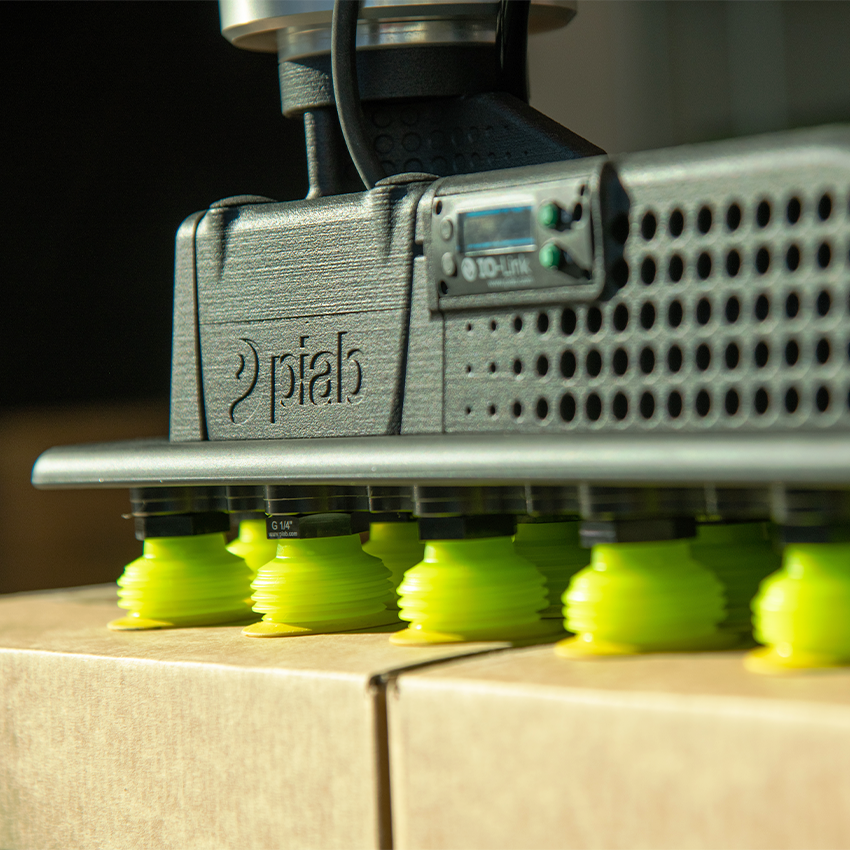
Zo kan een cobot die rubberen balletjes grijpt en verplaatst perfect veilig zijn, maar wanneer dezelfde cobot een scherp object manipuleert – denk aan metalen stukken met bramen – dan ontstaat plots een zeer gevaarlijke situatie, ook al is de installatie onveranderd. Het is dus belangrijk om elke toepassing te laten keuren en bij significante veranderingen – bijvoorbeeld de te manipuleren objecten, het soort grijper of het afgelegde traject – deze keuring opnieuw te laten uitvoeren.
Fabrikanten en integratoren van cobots werken creatieve oplossingen uit om deze installaties veilig én performant te houden. Zeker servogrijpers bieden hier opties. Zo kunnen de vingers van deze grijpers ingesteld worden om met zeer kleine marges naar het object toe te gaan en dit net genoeg te klemmen om het goed vast te houden. Het resultaat is dan ook dat er geen ruimte is om een vinger tussen grijper en object te krijgen, wat de veiligheid ten goede komt.
Een andere oplossing is om het object niet langs de buitenkant te grijpen – naar binnen toe dus – maar om van binnenuit te werken. Dit kan bijvoorbeeld bij holle buizen, waarbij de grijper zich in de buis zal begeven en dan naar buiten toe zal bewegen om zo de buis te klemmen. Ook bij dergelijke bewegingen is er geen gevaar om een lichaamsdeel te klemmen.
Alles begint bij het te manipuleren object en de snelheid en productiecontext waarin dit moet gebeuren
Sensoren spelen een belangrijke rol bij grijpers: of het nu gaat om terugkoppeling of energiebesparing. Positiesensoren geven aan of het object daadwerkelijk gegrepen is. Bij vacuümgrijpers vervullen vacuümsensoren deze functie. Dergelijke feedback zorgt ervoor dat de cobot betrouwbaar en veilig zijn werk kan doen.
Ten slotte hebben mechanische grijpers vaak nood aan specifieke vingers, om zo op maat van de objecten te kunnen werken. Bij cobots moeten deze eveneens ontworpen zijn met veiligheid in het achterhoofd. Zo zijn ze gemaakt of bedekt met zachte materialen en hebben ze afgeronde hoeken. Hierdoor is er veel minder gevaar voor verwondingen mocht er toch contact zijn tussen mens en cobot. Om de wrijving tussen vingers en werkstuk te optimaliseren, kan er gekozen worden voor specifieke inserts. Deze zijn voor steeds meer toepassingen beschikbaar.
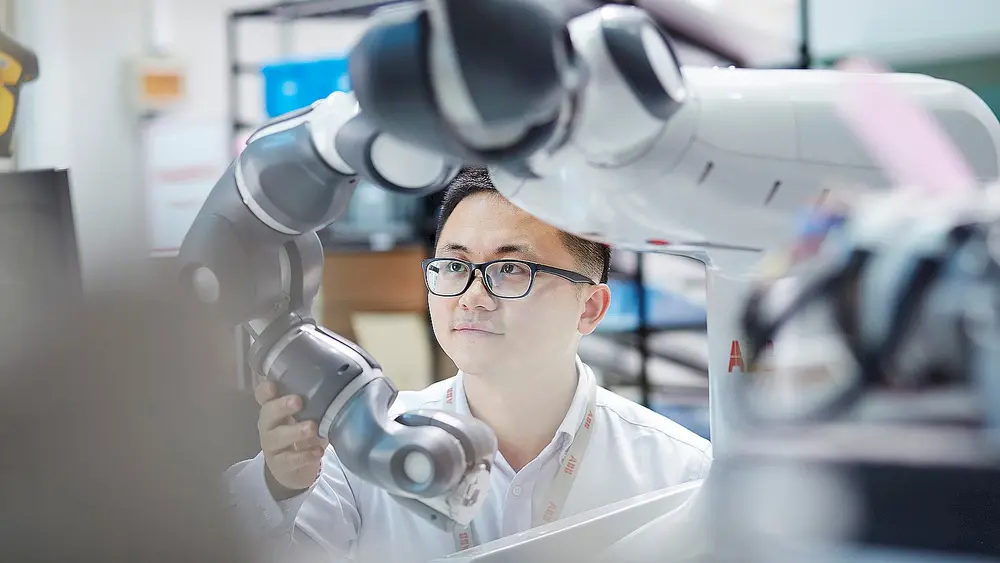
Recente ontwikkelingen
Cobots staan niet stil in hun ontwikkeling en grijpers dus ook niet. Heel wat vernieuwingen binnen grijpers zijn algemeen, ongeacht het type robot. Sommige zijn dan weer sterk gerelateerd aan de unieke gebruikscontext van cobots. Een continue ontwikkeling onder de cobots is de trend naar steeds zwaardere payloads. De meeste fabrikanten bieden ondertussen modellen aan die tot 30 kg aankunnen en sommige gaan hier nog over. Onder dit maximumgewicht moet men echter ook het gewicht van de grijper rekenen: een zware grijper doet het netto hefpotentieel dus sterk afnemen. Bijgevolg zetten fabrikanten van grijpers in op een lichter design met dito materialen.
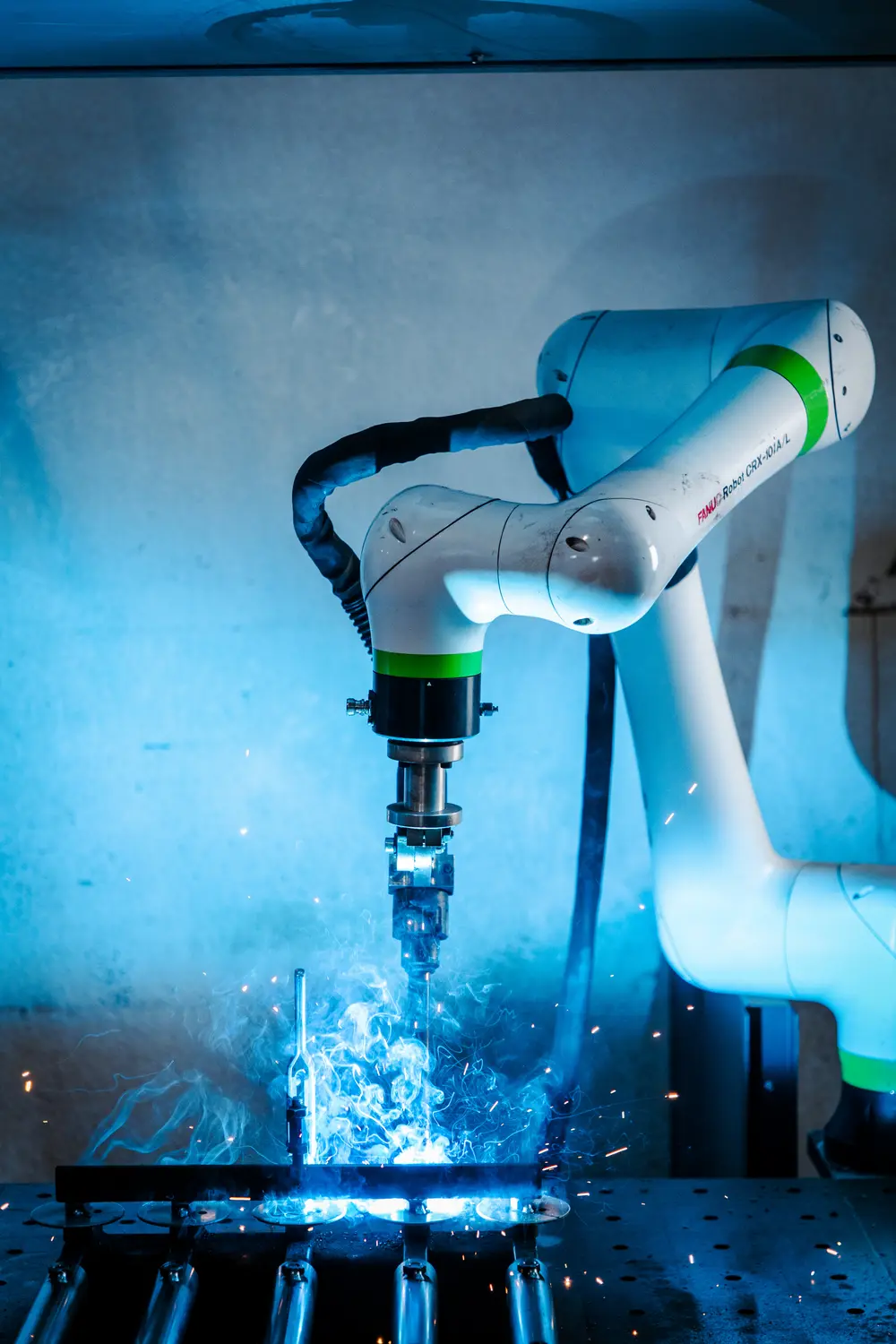
Een andere trend is gerelateerd aan het gebruiksgemak. Het is namelijk één van de grote troeven van cobots dat ze makkelijk te bedienen zijn en bovendien flexibel inzetbaar zijn. Dan moet de bediening en programmering van de grijper natuurlijk even intuïtief zijn. Hier wordt de laatste tijd veel vooruitgang in gemaakt, waarbij fabrikanten van grijpers kant-en-klare applicaties aanbieden die bij bepaalde types robots te gebruiken vallen. Vaak kan deze applicatie gewoon binnen de software van de cobot gebruikt worden, zodat alles geïntegreerd is.
Cobots worden voor steeds meer toepassingen gebruikt. Zo neemt gebruik binnen de voedingsindustrie sterk toe en ook lascobots zijn in opmars. Voor deze laatste toepassing is een speciaal instrument vereist, dat eveneens aan het einde van een cobot moet worden aangesloten. De diversiteit onder de cobotgrijpers neemt dus toe, met oplossingen voor steeds meer soorten objecten en gewichten. Daarnaast evolueren veel maakbedrijven naar een model met meerdere, kleinere batches in plaats van massaproductie. Hierdoor moet een cobot – en nog meer de industriële robot – vaak geregeld wisselen tussen grijpers.
Dit uitwisselen van grijpers is de afgelopen jaren een stuk makkelijker geworden. Heel wat fabrikanten voorzien nu universele flenzen waaraan al hun grijpers – en soms ook die van concurrenten – eenvoudig gekoppeld kunnen worden. Dit kan zelfs automatisch gebeuren, met tool changers die grijpers uit een docking station halen. Deze koppelstukken voorzien ook de nodige aansluitingen voor perslucht.
Met medewerking van Fanuc, Festo, Pick-It 3D, Pneuvano, Schunk, SMC Belgium en Zimmer Group