OPENEN INNOVATIES NIEUWE KANSEN
VOOR CNC-DRAAIMACHINES?
Nieuw tijdperk voor de gereedschaprevolver
CNC-draaitechnologie leent zich steeds beter voor de productie van fijnmechanische componenten die tot voor kort meestal op een CNC-freesmachine werden gemaakt. Dit komt enerzijds doordat de machinebouwers de mogelijkheden vergroten met bijvoorbeeld een extra freesspindel; anderzijds doordat de mogelijkheden om zwaardere freesbewerkingen met aangedreven gereedschappen te doen, verder toenemen. Met name bij de gereedschaprevolver werden er enkele interessante ontwikkelingen recent ook op de markt beschikbaar.
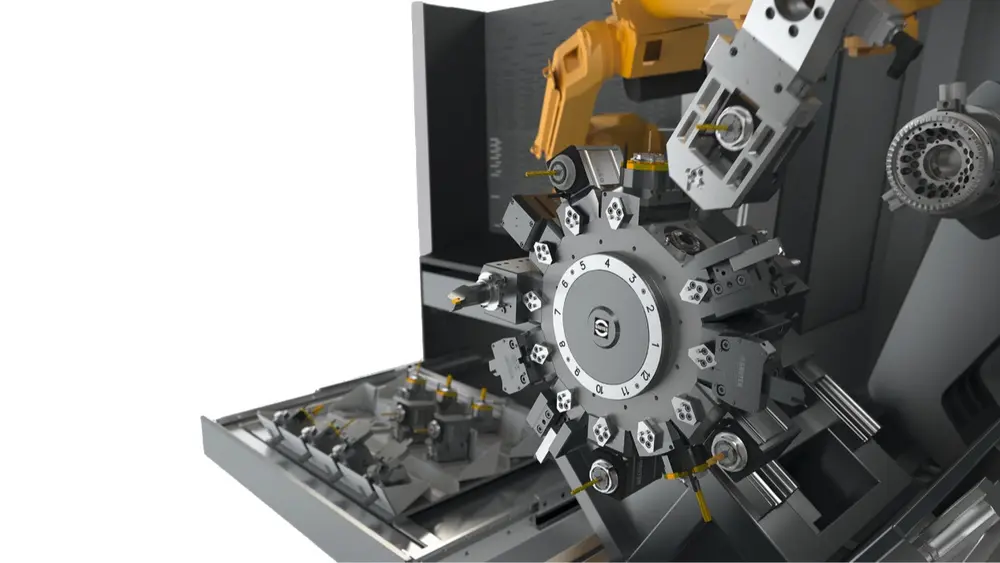
CNC-DRAAIMACHINE
De belangrijkste reden waarom een CNC-draaimachine voor prismatische delen interessant kan zijn, is de eenvoudige automatisering. Met name in de productie van kleine onderdelen voor bijvoorbeeld de medische industrie en machinebouw kan dit een goede oplossing zijn om meer manarme productieuren te realiseren. Stafaanvoer middels een standaardstangenlader volstaat dikwijls al, zolang de producten vallen binnen de diameter van het materiaal dat bewerkt wordt. Bij machines met een overnamespil kan tevens de achterzijde afgewerkt worden, zodat de producten compleet afgewerkt van de machine komen. Een voorwaarde is voorlopig wel dat de bewerkingen vooral draaibewerkingen moeten zijn. De freesbewerking moet zich beperken tot wat mogelijk is met aangedreven gereedschappen. De vermogens daarvan zijn beperkt. Op dit punt worden de grenzen momenteel verlegd.
KRACHTIGERE AANGEDREVEN GEREEDSCHAPPEN
Veel CNC-draaimachines zijn tegenwoordig uitgerust met twee, soms zelfs drie gereedschaprevolvers om de efficiency van de machine te vergroten. Deze revolver is aan vernieuwing onderhevig. Sommigen durven zelfs te stellen dat de revolver in de huidige vorm zijn beste tijd heeft gehad. Zo snel zal het wel niet gaan. Het voordeel van een draaimachine is dat de hoge kracht en snelspansysteem van de revolver zorgt voor stabiliteit tijdens de bewerking met een statisch gereedschap. Omdat men tegenwoordig zoveel mogelijk bewerkingen in één opspanning wil doen, zijn er de turrets voor aangedreven gereedschappen ontwikkeld, zodat aanvullende freesbewerkingen op de draaimachine gedaan kunnen worden. Deze aangedreven gereedschappen zijn minder krachtig dan vaak gewenst omdat de aandrijving in de houder geïntegreerd moet worden.
Motorspindel
Op AMB 2018 toonde een van de exposanten een nieuw concept. In het hart van de revolver zit een krachtige motorspindel. Hieromheen zit als het ware een schil waarop de gereedschappen worden geplaatst, het trommelmagazijn. Dat kunnen standaard statische draaibeitels zijn maar ook roterende. In dat laatste geval worden de gereedschappen traditioneel in de opname van de motorspindel geklemd. De positie van de motorspindel in het hart van de revolver, zorgt voor meer ruimte dus kan men een spindel met een hogere vermogensdichtheid kiezen. Dit betekent al snel dat er 30 tot 50% meer motorvermogen beschikbaar is voor het aangedreven draaigereedschap. Dat opent voor bepaalde freesbewerkingen en nieuwere materialen interessante toepassingsmogelijkheden.
Het tweede voordeel van dit concept is dat de bewerkingsruimte voor het gereedschap groter wordt doordat de stoorcontour volledig wegvalt. En als derde voordeel geldt dat het nu makkelijker wordt om gereedschappen in een revolver gerobotiseerd te verwisselen. Tot nog toe gebeurt dat amper: het wisselen van de gereedschappen gebeurt veelal nog manueel bij het instellen van de machine op een nieuwe job. Ook voor het gebruik van koelsmeermiddelen biedt deze nieuwe constructie voordelen omdat extra media toegevoerd kunnen worden.
Lees verder onder de foto...
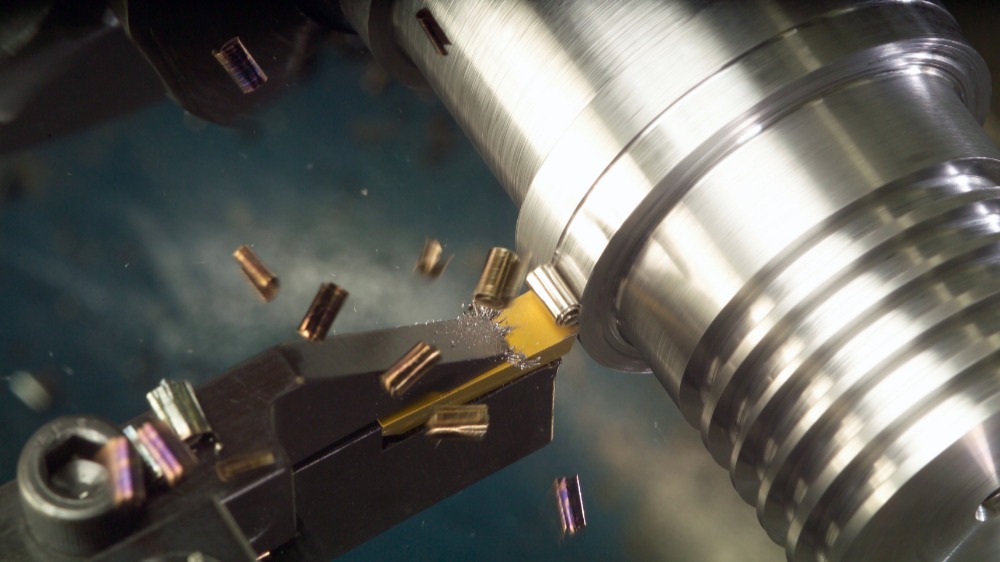
NIEUWE INTERFACE, SNELLER WISSELEN
Een tweede ontwikkeling bij de gereedschaprevolver is een andere interface als alternatief voor bestaande opnamen zoals VDI of BMT, de twee huidige standaards die onder meerdere merknamen beschikbaar zijn. Ook bij deze ontwikkeling speelt op de achtergrond dat er hogere eisen worden gesteld, onder andere aan de stabiliteit van de gereedschapopname. Het nieuwe gereedschapspansysteem pti (polygonal turning interface) dat door het WZL van de RWTH Aachen samen met enkele marktpartijen is ontwikkeld, haalt tot 75 kN spankracht.
In de nieuwe Torque drive-uitvoering die recent nog op AMB werd getoond, is het zelfs 85 Nm aan koppel over te brengen bij 12.000 omwentelingen per minuut. Ter vergelijking: gelijkaardige systemen in een VDI- of BMT-uitvoering kunnen maximaal 63 Nm overbrengen bij 10.000 toeren per minuut. In de komende tijd denken de ontwikkelaars dat zelfs 100 Nm koppel haalbaar is.
Daarnaast is bij de ontwikkeling gekeken naar het wisselen van de gereedschappen. Ook dat heeft men weten te vereenvoudigen bij dit nieuwe pti-concept, dat inmiddels in de markt verkrijgbaar is. De gereedschapwisseltijden kunnen bij het manueel wisselen van de gereedschappen gehalveerd worden ten opzichte van de BMT-houder. Alhoewel de revolver met de nieuwe interface verhoudingsgewijs het dubbele kost van een standaard BMT-uitvoering, schatten de ontwikkelaars de terugverdientijd op minder dan twee jaar bij twee gereedschapwisselingen per dag. Vergeleken met de VDI-houders is de terugverdientijd iets korter omdat deze qua investeringskosten tussen de BMT- en pti-interface in zit.
AUTOMATISCH GEREEDSCHAPPEN WISSELEN
Bij de CNC-freesmachines is het automatisch wisselen van de gereedschappen al een hele tijd een standaardtechnologie. Heel voorzichtig zoeken de system integrators ook naar een concept om dit bij de draaimachines toe te passen. Daarmee slaagt men erin om de omsteltijden drastisch te verminderen en de productvariatie die men onbemand op een CNC-draaibank kan produceren sterk te vergroten.
Daartoe wordt zoals hiervoor beschreven de motorspindel centraal in de revolver geplaatst waarna de aangedreven gereedschappen gewisseld worden door de robot. Dit biedt tevens de mogelijkheid om met veel meer dan 12 of 24 gereedschappen in de turret te werken, omdat naast de draaimachine een extra gereedschapmagazijn kan worden geplaatst.
SLIJPKWALITEIT MET HARDDRAAIEN
Ook aan de gereedschappenkant zijn er ontwikkelingen om de productiviteit te verhogen. Onder andere gaat het dan om harddraaien. Hoogsterkte staalsoorten en legeringen worden steeds vaker gevraagd vanwege het feit dat ze goed bestand zijn tegen bijvoorbeeld corrosie of mechanische belasting. Bij de gereedschappen draait het met name om de combinatie van de geometrie van de snijplaat en de coating. Deze bepalen of de standtijd van het gereedschap overeenstemt met de kwaliteit van de bewerking.
Een vrij jonge technologie is het combineren van harddraaien met superfinish in één opspanning. Hiermee haalt men een oppervlaktekwaliteit die tot nu toe alleen met een slijpbewerking of met lappen realiseerbaar is. Rz-waarden van 0,18 micron zijn zonder meer realiseerbaar. De truc zit in een speciaal hiervoor ontwikkeld gereedschap en een zeer stabiele machine. Aan de revolver worden de krachten op het gereedschap gemeten en deze informatie wordt direct teruggeleid naar de besturing van de machine, die daarna de snijparameters aanpast.