LES INNOVATIONS OFFRENT
DE NOUVELLES OPPORTUNITES AUX TOURS CNC?
Nouvelle ere pour le revolver d’outils
La technologie de tournage CNC se prête de mieux en mieux à la production de composants de mécanique de précision qui, jusqu’à il y a peu de temps encore, étaient réalisés le plus souvent sur une fraiseuse CNC. D’une part parce que les constructeurs de machines élargissent les possibilités avec par exemple une broche de fraise supplémentaire; d’autre part du fait que les possibilités d’effectuer des fraisages plus lourds avec des outils entraînés, augmentent encore. Quelques développements intéressants, notamment avec le revolver d’outils, ont été commercialisés récemment.
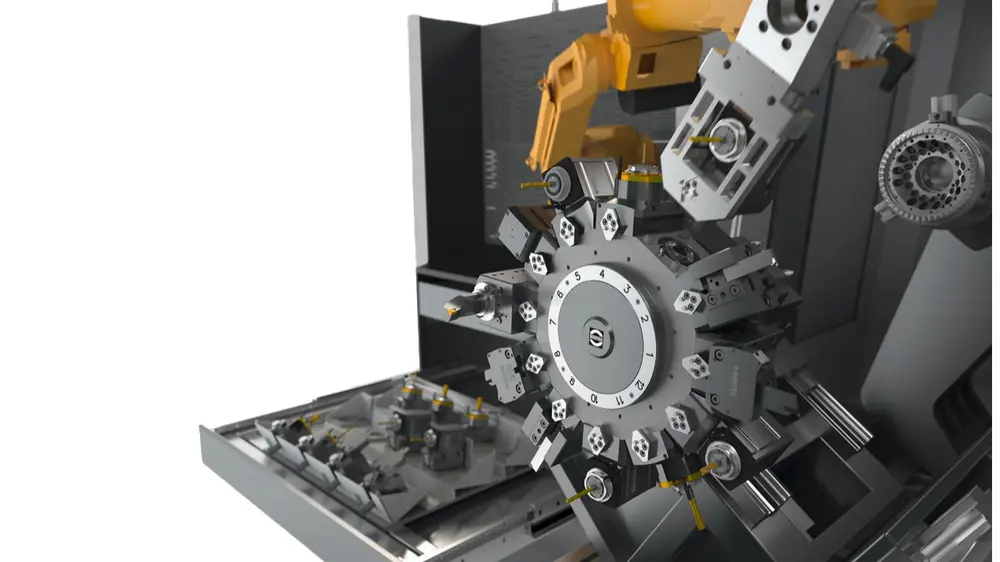
TOUR CNC
la principale raison pour laquelle un tour CNC peut être intéressant pour les parties prismatiques est l’automatisation simple. Ceci peut être une bonne solution pour réaliser davantage d’heures de production sans intervention humaine, notamment dans la production de petits éléments pour par exemple l’industrie médicale et la construction de machines. L’amenée de barres par un chargeur de barres standard suffit déjà souvent, tant que les produits restent dans le diamètre du matériau qui est usiné.
Sur les machines avec une broche de reprise, le verso peut de surcroît être achevé, de telle sorte que les produits sortent complètement finis de la machine. Une condition pour l’instant est bel et bien que les usinages doivent être surtout des usinages de tournage. L’usinage de fraisage doit se limiter à ce qui est possible avec des outils entraînés. Leurs puissances sont limitées. Sur ce point, les limites sont actuellement reculées.
OUTILS ENTRAINES PLUS PUISSANTS
A l’heure actuelle, de nombreux tours CNC sont équipés de deux, voire trois revolvers d’outils pour accroître l’efficacité de la machine. Ce revolver subit un renouvellement. Certains osent même affirmer que le revolver dans sa forme actuelle a fait son temps. Mais l’évolution ne sera pas si rapide. L’avantage d’un tour est que la puissance et le système de serrage rapide du revolver assure la stabilité pendant l’usinage avec un outil statique. Comme on veut actuellement effectuer un maximum d’usinages en un seul serrage, des tourelles pour outils entraînés ont été développées, de manière à pouvoir effectuer des fraisages supplémentaires sur le tour. Ces outils entraînés sont moins puissants que ce qui est souvent souhaité parce que l’entraînement doit être intégré dans le support.
Broche de moteur
Sur AMB 2018, l’un des exposants a montré un nouveau concept. Dans le cœur du revolver se trouve une puissante broche de moteur. Tout autour se trouve littéralement une enveloppe sur laquelle sont placés les outils, le magasin à tambour. Cela peut être des ciseaux de tournage statiques standard mais aussi rotatifs. Dans ce dernier cas, les outils sont traditionnellement serrés dans le mandrin de la broche de moteur.
La position de la broche de moteur dans le cœur du revolver agrandit l’espace, on peut donc choisir une broche avec une plus grande densité de puissance. Ceci signifie rapidement qu’une puissance de moteur accrue de 30 à 50% est disponible pour l’outil de tournage entraîné. Cela offre toutes sortes de possibilités d’application particulièrement intéressantes pour certaines usinages de fraisage et des matériaux plus nouveaux. Le second avantage de ce concept spécifique est que l’espace d’usinage pour l’outil s’agrandit par la suppression complète du contour perturbant.
Et en guise de troisième avantage, il devient désormais plus facile de changer les outils de façon robotisée dans un revolver. Ceci se fait à peine jusqu’ici: le plus souvent, le changement des outils s’effectue encore manuellement lors de la mise au point de la machine pour un nouveau job. Cette nouvelle construction offre également des avantages pour l’utilisation de lubrifiants réfrigérants parce que des milieux supplémentaires peuvent être acheminés.
En savoir plus sous la photo...
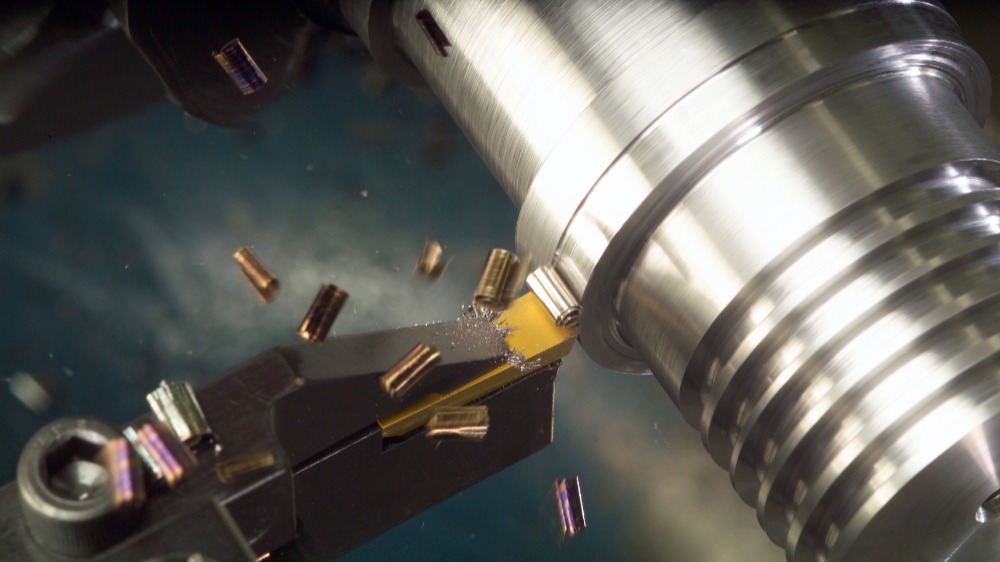
NOUVELLE INTERFACE, CHANGEMENT PLUS RAPIDE
Un second développement sur le revolver d’outils est une autre interface en guise d’alternative aux mandrins existants telles que VDI ou BMT, les deux standards actuels disponibles sous plusieurs marques. Dans ce développement également, les exigences plus élevées, notamment en termes de stabilité du mandrin, jouent en arrière-plan. Le nouveau système de serrage d’outils pti (polygonal turning interface) qui est développé par le WZL du RWTH Aix-la-Chapelle avec quelques acteurs du marché, atteint une force de serrage de 75 kN.
Dans la nouvelle exécution Torque drive encore montrée récemment sur AMB, il s’agit même de transmettre un couple de 85 Nm à 12.000 tours par minute. A titre de comparaison: des systèmes similaires dans une exécution VDI ou BMT sont capables de transmettre au maximum 63 Nm à 10.000 tours par minute. A l’avenir, les développeurs estiment même pouvoir atteindre un couple de 100 Nm. Par ailleurs, le changement des outils a été examiné lors du développement. On est également parvenu à le simplifier avec ce nouveau concept pti, entre-temps disponible sur le marché. Les temps de changement d’outil manuel peuvent être réduits de moitié par rapport au support BMT.
Bien que le revolver avec la nouvelle interface coûte le double d’une exécution BMT standard, les développeurs estiment le délai de récupération à moins de deux ans avec deux changements d’outil par jour. En comparaison des supports VDI, le délai de récupération est un peu plus court parce que ceux-ci s’intercalent entre les interfaces BMT et pti en termes de coûts d’investissement.
CHANGEMENT D’OUTIL AUTOMATIQUE
Sur les fraiseuses CNC, le changement d’outil est depuis tout un temps déjà une technologie standard. C’est avec une très grande prudence que les intégrateurs de systèmes cherchent également à appliquer le concept sur les tours. On parvient aussi bien à diminuer drastiquement les temps de conversion qu’à augmenter fortement la variation de produits pouvant être fabriquée sans intervention humaine sur un tour CNC.
A cette fin spécifique, la broche de moteur est placée au centre du revolver, tel que décrit, puis les outils entraînés sont changés par le robot. De surcroît, ceci offre la possibilité de travailler avec nettement plus que 12 ou 24 outils dans la tourelle, parce qu’on peut placer un magasin d’outils supplémentaire à côté du tour.
QUALITE DE RECTIFICATION AVEC LE TOURNAGE DUR
Des développements visent également à accroître la productivité du côté des outils. Il s’agit notamment du tournage dur. Des nuances d’acier et alliages haute résistance sont de plus en plus souvent demandés en raison du fait qu’ils résistent bien à la corrosion ou à la charge mécanique, par exemple. Pour les outils, il s’agit notamment de la combinaison de la géométrie de la plaquette et du revêtement. Ceux-ci déterminent si la tenue d’outil correspond à la qualité de l’usinage. Une technologie assez récente est la combinaison du tournage dur avec la super finition dans un seul serrage.
Elle permet ainsi d’atteindre une qualité de surface qui n’était réalisable jusqu’ici qu’avec une rectification ou un rodage. Des valeurs Rz de 0,18 micron sont réalisables. Le truc réside dans un outil spécialement développé à cet effet et une machine très stable. Les forces sur l’outil sont mesurées sur le revolver et cette information est directement renvoyée vers la commande de la machine qui adapte ensuite les paramètres de coupe.