Laser metal deposition naderbij bekeken
Basisprincipes, Toepassingen en uitdagingen
Het gebruik van Laser Metal Deposition (LMD) als 3D-printmethode voor metalen is momenteel minder bekend dan poederbedfusie etc. Om het potentieel van deze technologie correct te kunnen inschatten is het dan ook van belang de basisprincipes, huidige toepassingen en ontwikkelingen even op een rijtje te zetten.
Basisprincipes
Zoals het geval is bij nagenoeg alle andere additieve processen is Laser Metal Deposition (LMD) gebaseerd op het principe waarbij een substraat (basismateriaal), warmtebron en toevoegmateriaal gecombineerd worden om laagsgewijs een geometrie op te bouwen. Bij LMD wordt daartoe gebruikgemaakt van een laserbron (continu of gepulseerd) en metaalpoeder of draad met welbepaalde eigenschappen (chemische samenstelling, deeltjesgrootte, draaddiameter ...) dat in het smeltbad wordt toegevoegd. In dit artikel wordt enkel de variant op basis van metaalpoeder verder behandeld.
Door inwerking van de warmtebron op het substraat wordt een smeltbad gecreëerd, net als bij het lassen, waarin het toevoegmateriaal aangebracht wordt. Het poeder wordt daartoe via een spuitstuk en onder gasbescherming in het smeltbad geblazen. Het herhaaldelijk neersmelten van elkaar overlappende laagjes volgens een vooraf bepaald patroon kan zo worden toegepast om een functionele geometrie te printen. Op deze wijze kunnen structuren op een bestaand onderdeel worden aangebracht, vergelijkbaar met herstellassen of lasercladding, of een volledig nieuwe component worden opgebouwd.
Om het neersmelten onafhankelijk te maken van de verplaatsingsrichting, geniet een spuitstuk met coaxiale poedertoevoer (Figuur 1A) meestal de voorkeur boven de variant met gescheiden zij-aanvoer. Bij het eerste type wordt de laserstraal in het midden gepositioneerd en wordt het poeder coaxiaal toegevoerd, hetzij door verschillende radiaal verdeelde gaatjes of door een continue ringvormige opening. De volledige laseroptiek, met onderaan het spuitstuk, kan zowel op een portaalsysteem als op een robot worden gemonteerd (Figuur 1B).
Het gebruik van optimaal ingestelde parameters voor het neersmelten en een passende printstrategie kan de efficiëntie van het poederverbruik (verhouding van gesmolten poeder tot aangevoerd poeder) tot meer dan 85% brengen. De energie-efficiëntie van het laserproces is echter sterk afhankelijk van het gebruikte metaal, voornamelijk vanwege de verschillen in reflectiviteit. Infraroodlasers zijn geschikt voor toepassingen met staal, lasers met blauw of groen licht zijn daarentegen beter geschikt voor koper. Deze laserbronnen worden bovendien steeds compacter en goedkoper.
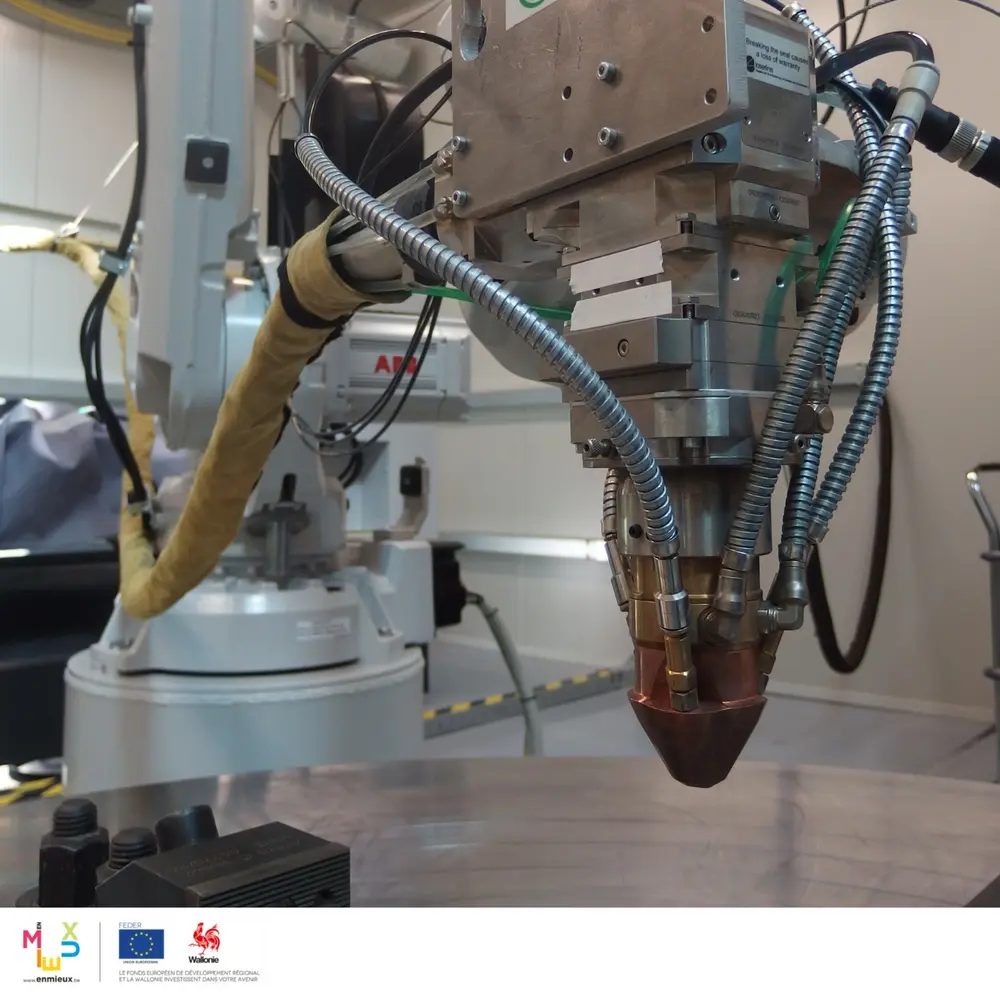
Toepassingen
Onderdelen die geschikt zijn om door middel van LMD te worden geprint, hebben doorgaans afmetingen gelegen tussen die van Powder Bed Fusion (PBF) enerzijds en processen gebaseerd op elektrische lasboog en toevoerdraad zoals Wire-Arc Additive Manufacturing (WAAM) anderzijds. De voornaamste kenmerken van de bovengenoemde technieken zijn weergegeven in Tabel 1. Een belangrijke beperking van PBF is de nood aan een afgesloten ruimte, met beperkt volume. Processen als LMD en WAAM kunnen worden toegepast in opstellingen in een afgesloten ruimte, maar ook in open omgevingen mits de gepaste veiligheidsmaatregelen gehanteerd worden, wat toelaat grotere stukken te produceren.
Voordelen
Laser Metal Deposition biedt een aantal voordelen die de technologie interessant maken ten opzichte van andere printprocessen. Zo is het mogelijk om structuren op reeds bestaande onderdelen toe te voegen, hetgeen reparaties aan beschadigde onderdelen toelaat of het opbouwen van specifieke functies. Traditioneel worden dit soort reparaties handmatig uitgevoerd door middel van booglassen. Die reparaties kunnen verschillende vormen aannemen: een zich ontwikkelende scheur kan worden verwijderd en opnieuw gevuld worden (Figuur 2A), een deuk in een oppervlak of een afgebroken hoek kan worden opgevuld en afgesleten of afgebroken vormen kunnen opnieuw worden opgebouwd.
Beperkingen
Maar LMD kent ook een aantal beperkingen zoals bij het produceren van overhangende oppervlakken. Deze vormen een uitdaging, onder andere omdat het aanbrengen van ondersteunende structuren, zoals toegepast bij PBF, nog niet goed ontwikkeld is. Ofwel moet de ontwerper het onderdeel een passende vorm geven om compatibel te zijn met LMD, ofwel moet de gebruikte productiemachine voldoende vrijheidsgraden bezitten om de vereiste posities aan te kunnen. LMD kan tot op zekere hoogte dus ook worden gebruikt om horizontale oppervlakken te vervaardigen, bijvoorbeeld mits de laseroptiek een hoekinstelling tot 90° aankan. Een robot met externe manipulatoren kan daarvoor worden gebruikt, maar ook dan is krachtige software nodig om de lasbanen te genereren. Met andere woorden hoe complexer en hoe groter het onderdeel is, hoe meer investeringen er nodig zijn inzake ontwerpduur en installatie van de machine. Een voorbeeld van een relatief groot onderdeel, opgebouwd vanaf een vlakke basisplaat, wordt voorgesteld in Figuur 2B.
nadien werd de holte opgevuld door middel van Laser Metal Deposition.
Figuur 2B (rechts): CRM Group-logo opgebouwd met 316L-poeder vanaf de basisplaat
Betere afwerkingsgraad en reproduceerbaarheid
Veelal kan met behulp van een LMD-systeem een betere afwerkingsgraad en reproduceerbaarheid bereikt worden dankzij automatisering van het proces. Bovendien zal het onderdeel doorgaans minder vervorming ondergaan dan bij draadgebaseerd processen vanwege de gecontroleerde diameter van de laserfocus en de lagere warmtetoevoer. Uit eerdere testen bij CRM Group op roestvrij staal is gebleken dat de vervormingen met een factor vijf kunnen worden verminderd. Bovendien is het relatief eenvoudig om op maat gemaakte poedersamenstellingen te verkrijgen die compatibel zijn met het te repareren onderdeel. Dit in tegenstelling tot toevoegdraad, waar legeringssamenstellingen vrij beperkt zijn en op maat gemaakte draad moeilijk te vinden is.
Poedervloeibaarheid
Ook dient te worden vermeld dat LMD inzake poedervloeibaarheid niet zo beperkt is als PBF. Zo kunnen poeders met minder regelmatige vorm uit andere bronnen dan gasverneveling toch gebruikt worden. Bijvoorbeeld mechanisch gelegeerde poeders, die vervaardigd worden in hoge energie kogelmolens, en metaalpoeders vermengd met sub-micron keramische deeltjes die veelal behoorlijk gefacetteerd zijn. Beide technieken zijn interessant om versterkende of functionele deeltjes in de geprinte componenten te integreren.
Functies lokaal toevoegen
Zoals eerder aangegeven is LMD ook bruikbaar om bepaalde functies lokaal toe te voegen op bestaande onderdelen. Een groot werkstuk kan zo initieel heel efficiënt en kwalitatief worden vervaardigd door middel van smeden of gieten en daarna verder worden afgewerkt met LMD om handvatten, vertanding, verstevigingen etc. toe te voegen. Deze kunnen zelfs uit een ander materiaal zijn, indien de metallurgische compatibiliteit gegarandeerd kan worden (bv. een combinatie van gereedschapsstaal en constructiestaal). Een wetenschappelijk werk van Heilemann, Beckmann, Konigorski en Emmelmann (2018) bestudeerde het ontwerp van verstevigingen voor een vliegtuigromp met behulp van topologische optimalisatie. De resulterende organische structuren werden later aangepast om ze compatibel te maken met LMD voor aluminium (Figuur 3A).
Combinatie van technieken
Bovendien is het mogelijk om geïntegreerde systemen te ontwerpen die verschillende technieken combineren zoals additieve en subtractieve technieken zodat bijvoorbeeld door middel van slijpen, zandstralen of kogelstralen de geprinte of gerepareerde oppervlakken van de juiste afwerking kunnen worden voorzien. Ook kunnen verschillende additieve fabricageprocessen worden gecombineerd, bijvoorbeeld LMD met poeder of draad en WAAM. Op die manier worden diverse voordelen geoptimaliseerd, met name een hogere neersmelt met WAAM en de fijnere structuren of een ander materiaal met LMD.
Uitdagingen en ontwikkelingen
Huidig onderzoek met betrekking tot LMD heeft veelal betrekking op het toevoegmateriaal. Meestal zijn de poeders die voor LMD gebruikt worden:
- traditionele poeders (316L, Al-Si-legeringen);
- samenstellingen die reeds worden gebruikt bij lasercladding waarbij mogelijk scheurvorming optreedt (Stellite®, gereedschapsstaal);
- nieuw ontwikkelde samenstellingen die reeds voor PBF toepassingen gebruikt worden in lucht- en ruimtevaart (A20x®, Scalmalloy®).
Juiste procesparameters vinden
Vele samenstellingen zijn dus reeds beschikbaar, maar het vinden van de juiste procesparameters blijkt vaak een uitdaging. Deze zijn immers afhankelijk van substraat, poedersamenstelling, onderdeelafmetingen en de vorm, zodat wegens gebrek aan eenvoudig toepasbare numerieke modellen 'first time right' niet makkelijk is. Het INSIDE metal AM-project, dat door Vlaio en SIM ondersteund wordt, heeft tot doel enkele richtlijnen te bieden aan producenten en gebruikers ter selectie van de passende printtechnologie voor grote onderdelen en indicatie voor de bijhorende parameters.
Optimalisatie toevoegmaterialen
Slechts weinig toevoegmaterialen werden al geoptimaliseerd voor het LMD-proces. De middelmatige afkoelsnelheden, gelegen tussen die van het lassen en PBF, kunnen ervoor zorgen dat het potentieel van een specifiek poeder niet benut kan worden. Dat is onder andere het geval voor Scalmalloy®, dat afhankelijk is van een hoge afkoelsnelheid om de gewenste eigenschappen te bereiken (Kürnsteiner et al., 2020). Anderzijds kunnen de opeenvolgende thermische cycli die optreden tijden het printen spanningen veroorzaken en resulteren in bijvoorbeeld scheuren bij gereedschapsstalen met hoge hardheid (Kempen et al., 2014). Met deze twee kenmerken van het proces, namelijk een middelmatige afkoelsnelheid en de opeenvolgende thermische cycli, moet rekening gehouden worden bij de selectie van de procesparameters en de ontwikkeling van hoogwaardige poedersamenstellingen.
Figuur 3B (rechts): Dwarsdoorsnede van een koper-rvs Laser Metal Deposition lasrups
Multimateriaalstructuren
Er worden ook heel wat inspanningen geleverd om multimateriaalstructuren, oftewel onderdelen waarin verschillende materialen gecombineerd worden, verder te ontwikkelen. De aard van de poedertoevoer maakt het bij LMD mogelijk om een aanvoersysteem te gebruiken dat op meerdere poedercontainers tegelijk kan worden aangesloten en zodoende ‘in situ’ menging toelaat. Ook kunnen zo bi-materiaalstructuren (Figuur 3A) of componenten met gradueel veranderende samenstelling worden opgebouwd (Figuur 3B).
Voor slijtage en structurele toepassingen kunnen onderdelen bestaande uit een zachte kern met een hard oppervlak worden geprint op basis van twee compatibele metaalsoorten. Deze aanpak is echter niet alleen nuttig om de mechanische performantie te verbeteren. Ook kunnen bi-materiaalstructuren, zoals bij koper-rvs combinaties, de warmteoverdracht optimaliseren (Chen & Liou, 2018).
Andere interessante materiaalcombinaties bevinden zich nog in een vroeg stadium van onderzoek: Al-staal, Al-Ti, Staal-Ti, Al-Cu, ... (Karnati, Zhang, Liou, & Newkirk, 2019). De reacties tussen deze metalen levert echter veelal broze intermetallische verbindingen op en bijhorende mechanische eigenschappen die de bruikbaarheid te sterk negatief beïnvloeden. Lopend onderzoek richt zich daarom ook op het aanbrengen van tussenlagen die compatibel zijn met beide materialen en voldoende mechanische sterkte kunnen garanderen.
Compactere LMD-systemem
Naast de materialen zijn er ook nog machinegerelateerde ontwikkelingen gaande. Het gaat hem daarbij vooral om het ontwikkelen van compactere LMD-systemen met lagere investeringskosten. Sommige bedrijven bieden oplossingen aan met afmetingen gaande van een kleine kamer tot een tafelmodel. Compactere laserbronnen, optieken, poederaanvoer units en manipulatoren zullen het mogelijk maken om transporteerbare systemen aan te kunnen bieden om eender waar wisselstukken te maken of uiterst precieze bewerkingen uit te voeren in moeilijke omgevingen en zonder operator.
Meer informatie?
Deze bijdrage werd gerealiseerd in het kader van het INSIDE Metal AM-project, waarmee Sirris, CRM en BIL actief werken aan het ondersteunen van 3D-printen met hoogsterkte- en roestvast staal, met de steun van het Vlaams Agentschap voor Innoveren en Ondernemen (Vlaio) en het Strategisch Initiatief Materialen (SIM-Flanders).
Zowel Selective Laser Melting (SLM), Laser Metal Deposition (LMD) als Wire Arc Additive Manufacturing (WAAM) worden onderzocht. De focus van het project ligt op de materiaalsoorten 316L, 17-4PH, H11/H13, M3 (voor LMD), S355 en duplex RVS (voor WAAM). Er worden concrete demonstratoren uitgewerkt in samenwerking met industriële partners, gevolgd door een technische en economische evaluatie.
Indien u interesse hebt in het project of met concrete vragen zit, contacteer dan frederik.hendrickx@crmgroup.be.