Laser Powderbed Fusion (LPBF): een kansrijke technologie
Holistische procesbenadering als succesfactor
Laser Powderbed Fusion is nog altijd de meest toegepaste metaalprinttechnologie, ondanks dat deze techniek duur en complex is. Met een brede kijk op het proces en een integrale benadering kan de techniek succesvol worden toegepast.
Introductie
Ontstaan en principe
Laser Powderbed Fusion (LPBF), zoals de officiële naam tegenwoordig luidt, is de oudste en eigenlijk meest doorontwikkelde metaalprinttechnologie. De techniek dateert uit de vorige eeuw en werd rond 2000 al eens op een beurs geïntroduceerd. Zowel de KU Leuven als Fraunhofer ILT (Duitsland) hebben een belangrijke rol gespeeld in de ontwikkeling van de technologie en doen dat eigenlijk nog steeds tot op de dag van vandaag.
Bij laserpoederbed metaalprinten worden zeer kleine metaalpoeders (doorsnede 25 – 45 µm) als het ware aan elkaar gelast met de energie van de laserstraal. De machine scant het oppervlak van de bouwplaat, waarover het poeder met een recoater is uitgestreken, en belicht alleen de poederdeeltjes waar in het eindproduct materiaal moet komen. De metaalpoeders worden in het horizontale vlak aan elkaar gelast en door de warmte ook verbonden met de onderliggende laag. Voor een goede dichtheid is een evenredige verdeling van de poeders noodzakelijk.
Nadat zo een hele laag is belicht, zakt de bouwplaat precies de dikte van de volgende laag. Er wordt een nieuwe laag poeder aangebracht en vlak gestreken en het hele proces begint van vooraf aan. Deze laagdikte is mede bepalend voor de mechanische eigenschappen van het werkstuk dat men print.
Afhankelijk van de hoogte van het werkstuk kunnen er duizenden lagen na elkaar worden geprint. Sommige grote builds, bijvoorbeeld voor raketmotoren, lopen dan ook meer dan een week.
Varianten op de technologie en hun aanbieders
Het principe van het smelten van poederdeeltjes met een laser dateert uit de jaren tachtig en werd aanvankelijk Selective Laser Sintering genoemd. De Amerikanen ontwikkelden SLS voor polymeren. Later is er metaalprinten bij gekomen, waarvoor de termen Selective Laser Melting (SLM) en Direct Metal Laser Sintering (DMLS) werden gebruikt. Tegenwoordig spreekt men over Laser PowderBed Fusion (LPBF).
Een variant hierop is dat men de laserstraal vervangt door een elektronenstraal, dan spreekt men over EPBF. Hierbij zijn de poeders groter (40 – 100 µm) wat resulteert in een iets grovere oppervlaktestructuur, wat bijvoorbeeld bij medische implantaten gewenst kan zijn.
Sinds de belangrijkste patenten voor LPBF zijn afgelopen, groeit het aantal fabrikanten sneller dan de markt. Hetzelfde ziet men nu bij de elektronenstraalprinters. Sinds het patent is afgelopen, zijn er nieuwe aanbieders op de markt gekomen.
De laserbronnen
Aanvankelijk gebruikte men voor de laserpoederbedmetaalprinters een CO2-laser; inmiddels heeft de fiberlaser deze rol overgenomen en experimenteren sommige fabrikanten ook met diodenlasers. De vermogens liggen tegenwoordig veel hoger dan voorheen. In de kleinere, compacte machines werkt men vaak met vermogens van 250 tot 500 Watt; in de grotere AM-systemen zijn het laserbronnen met 1.000 Watt vermogen.
Om tijd te winnen heeft men multilasertechnologie ontwikkeld: in één machine belichten meerdere laserstralen gelijktijdig het poederbed. In eerste instantie ging het hier om drie of vier lasers, bijvoorbeeld 4x 500 of 4x 1.000 Watt, ondertussen worden al machines gebouwd met 16 lasers of meer.
Niet elke fabrikant gaat in deze race mee. Sommigen houden het aantal lasers in een machine bewust beperkt. Ze wijzen niet alleen op de zeer hoge investeringskosten als men meerdere laserbronnen gebruikt. Ook de warmte-inbreng is moeilijker te beheersen zodra meerdere lasers in het spel zijn. Tot slot neemt het risico op rookvorming toe naarmate op meerdere plaatsen op het bed metaalpoeders gesmolten wordt, net als de vorming van spetters. De rook en de lasspetters kunnen de laserstraal negatief beïnvloeden. De gasstroom in de bouwkamer (inert gas, vaak Argon) is daarom een cruciaal aspect in een 3D-metaalprinter.
Als alternatief voor meer lasers ontwikkelt men nieuwe scanstrategieën voor een hogere productiviteit. Eén hiervan houdt in dat de laser niet wacht totdat de recoater de volledige laag poeder heeft uitgestreken maar al direct achter de recoater begint met het belichten. Dit kan de productiviteit met een factor 4 verhogen.
Het poeder
LPBF biedt in de praktijk enkele belangrijke voordelen ten opzichte van andere 3D-metaalprinttechnieken. Het grootste voordeel is dat laserpoederbedmetaalprinten de meest fijne oppervlaktestructuur oplevert. Veel fijner dan bijvoorbeeld Wire Arc AM (WAAM). De mechanische eigenschappen zijn goed en inmiddels zijn er veel legeringen beschikbaar.
Efficiënt materiaalgebruik is een ander pluspunt. Men gebruikt alleen het materiaal dat nodig is voor het product en slechts een beetje poederafval. Dit is een heel ander verhaal dan sommige freesproducten waarvoor tot 90 procent van het materiaal eindigt als spanen.
Er moet echter wel vermeld worden dat niet alle poeder dat niet in het werkstuk komt, hergebruikt kan worden. Een deel van het poeder wordt beïnvloed door de warmte en kan samenklonteren. Daarom wordt het poeder altijd eerst gezeefd voor de volgende buildjob en moet men altijd vers poeder mengen met gebruikt poeder.
Ook de opslag van het poeder vraagt aandacht. Niet alleen omwille van veilige werkomstandigheden – het gaat hier om nanodeeltjes – maar ook om de poederkwaliteit te kunnen garanderen. Bedrijven die investeren in LPBF-technologie moeten er rekening mee houden dat er bijkomende investeringen zijn in opslag van poeder en transport richting de machine.
Omdat de productiekosten van poeder onder andere door de energiecomponent hoog zijn, zijn de materiaalkosten veel hoger dan men gewend is. In het eindproduct kunnen die meevallen als men specifiek voor additive manufacturing ontwerpt en met topologie-optimalisatie het gewicht tot een minimum reduceert. Topologie-optimalisatie is eigenlijk een conditie sine qua non in deze vorm van metaalprinten.
Topologie-optimalisatie is een conditie 'sine qua non' bij LPBF,
omwille van de materiaalkosten
Voordelen van LPBF: complexe vormen
Doordat men de bouwkamer altijd vult met poeder, kunnen met LPBF complexe vormen worden gemaakt, zoals producten met ondersnijdingen of samenstellingen van componenten. Omdat de producten in het poederbed blijven, kan men ook inwendige features printen, zoals koelkanalen.
Momenteel ziet men veel toepassingen waar deze mogelijkheid doorslaggevend is, bijvoorbeeld voor producten die inwendig gekoeld moeten worden. Men kan dan de koelkanalen dicht onder het oppervlak plaatsen, precies op de plek waar de meeste warmte afgevoerd moet worden. Of men optimaliseert de koelkanalen om de turbulentie te minimaliseren, een toepassing die vooral gebruikt wordt door fabrikanten van precisiemachines.
Functie-integratie is een ander voordeel van additive manufacturing. Meerdere losse onderdelen kunnen in één keer 3D-geprint worden, waardoor assemblagekosten vervallen. Dit heeft bovendien invloed op de supplychainkosten.
Nadelen van LPBF: complexe en dure techniek
De nauwkeurigheid waarmee men met LPBF 3D-print ligt op een relatief hoog niveau vergeleken met andere AM-technieken. Maar men zal nooit de nauwkeurigheden en oppervlakteruwheden halen die bijvoorbeeld met verspanende technieken haalbaar zijn, omdat men in beginsel twee poederdeeltjes aan elkaar last.
Zelfs het kleinste poederdeel is nog altijd veel grover dan een nauwkeurig gefreesd of gevonkt stukje metaal. Er zal dus bijna altijd nabewerking moeten gebeuren, wat aandacht vergt aan het begin van het proces. Men moet bijvoorbeeld zorgen dat complexe onderdelen wel nog spanningsvrij opgespannen kunnen worden als er nagefreesd moet worden.
De twee grootste nadelen van LPBF-technologie zijn echter dat het een complexe en dure techniek is. De hoge kosten hebben onder andere te maken met de lasertechnologie. Daarnaast onderschatten bedrijven vaak de bijkomende kosten, bijvoorbeeld voor de opslag van metaalpoeder, zeker als dit in een ATEX-conforme omgeving opgeslagen moet worden.
De complexiteit heeft veel te maken met het feit dat het eindresultaat van veel factoren afhankelijk is. De warmte-inbreng in het werkstuk kan een spelbreker zijn, bijvoorbeeld doordat er vervormingen ontstaan. Met simulatiesoftware kan men dit probleem weliswaar verkleinen, maar helemaal uitsluiten vergt een langdurig traject.
Om de warmte af te voeren, zijn supportstructuren vaak noodzakelijk. Dit betekent extra printtijd – en materiaal – en extra nabewerking want ze moeten allemaal weer verwijderd worden. Met zowel software voor het optimaliseren van deze supportstructuren alsook het automatisch verwijderen probeert de AM-industrie dit nadeel te verkleinen.
Kwaliteit waarborgen
Het valideren van een AM-proces kan lang duren, zeker als het kritische onderdelen betreft die certificering vereisen. Dit heeft onder andere te maken met het gegeven dat de manier waarop men een onderdeel op de bouwplaat positioneert van invloed is op de materiaaleigenschappen.
In tegenstelling tot wat gangbaar is in metaalbewerking, zijn materialen niet gestandaardiseerd. De eigenschappen worden immers voor een belangrijk deel pas tijdens het printproces zelf gevormd. Daarom wordt een integrale benadering van het hele proces als een kritische succesfactor gezien: design engineer, de werkvoorbereider en de procesoperator zijn gezamenlijk verantwoordelijk voor de kwaliteit van het eindproduct.
En omdat men niet elk onderdeel kan controleren met bijvoorbeeld CT-scanners, is Statistische Procescontrole (SPC) noodzakelijk om de kwaliteit te borgen. De kwaliteit van een AM-onderdeel moet bij serieproductie geborgd worden vanuit het proces. Fabrikanten spelen hierop in met onder andere meltpool monitoring-systemen, die met hogesnelheidscamera’s data van het smeltproces verzamelen. Met behulp van Machine Learning worden eventuele afwijkingen in een laag gedetecteerd. Daarna is het aan de proces engineer om te bepalen of een afwijking acceptabel is of niet.
Een holistische procesbenadering is de grootste horde die men moet nemen als men met 3D-metaalprinten begint
In-situ monitoring onvoldoende uitgerijpt
Het Amerikaanse standaardisatie-instituut ASTM International constateerde vorig jaar in een studie echter dat er nog haken en ogen kleven aan in-situ monitoring. Het monitoren van het smeltbad is één van de ISM-technieken, naast het monitoren van de materiaaldepositie en de totale procesbewaking.
De door ASTM International bevraagde onderzoekers concluderen dat de resultaten van deze systemen om het proces te monitoren onvoldoende zijn om de werkstukken hiermee te certificeren. Zij wijzen erop dat een closed loop-systeem, waarbij instellingen veranderen op basis van gevonden waarden, momenteel niet past binnen de normen. Deze gaan er namelijk van uit dat de instellingen na de validatie niet meer gewijzigd worden.
Machine Learning wordt wel als kansrijk beschouwd, maar er liggen nog een aantal uitdagingen die opgelost moeten worden. De grootste hinderpaal is dat er enorm veel data nodig zijn om de ML-algoritmen mee te trainen.
Integratie met CAD/CAM
De integrale benadering van additive manufacturing wordt opgepakt door de markt. Dat blijkt bijvoorbeeld uit het feit dat een groeiend aantal CAD/CAM-ontwikkelaars met software komt waarmee men zowel de buildjob voor de metaalprinter voorbereidt, als de CNC-freesmachine voor de nabewerking. Dit scheelt niet alleen tijd in de werkvoorbereiding, maar maakt eveneens automatisering mogelijk, doordat wijzigingen in het ontwerp direct beoordeeld kunnen worden op de consequenties voor het nabewerken.
Ook kan men dan al bij het programmeren van de 3D-metaalprinter bijvoorbeeld extra materiaal mee laten printen om het onderdeel makkelijker te kunnen opspannen. Onderzoeken wijzen namelijk uit dat de kosten van 3D-metaalprinten met name gaan zitten in alles dat om het feitelijke printproces heen gebeurt. Afhankelijk van de complexiteit en de hoeveelheid nabewerking, kan dit oplopen tot 80 procent en meer.
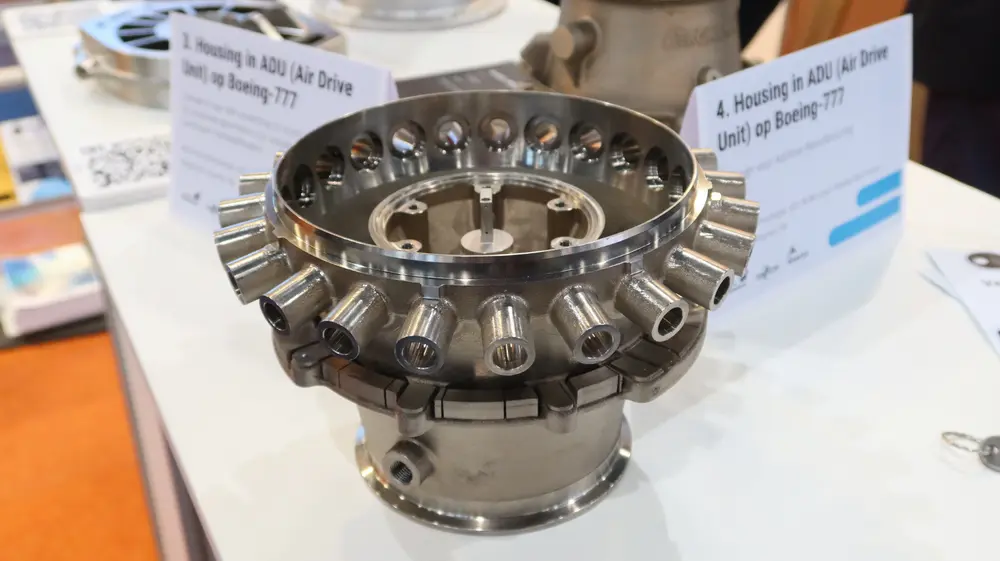
Conclusie
LPBF-technologie is nog steeds de aangewezen technologie voor de additieve productie van hoogwaardige componenten. Maar de technologie gaat niet andere productietechnieken zomaar vervangen. Er moet duidelijk gezocht worden naar de meerwaarde van additive manufacturing om de investeringen rendabel te maken. En dat vergt dat men verder kijkt dan de pure productiekosten.
Bovendien vereist de technologie een integrale procesbenadering, aangezien de optimalisatie van een deelaspect van het AM-proces kan leiden tot een suboptimaal totaal. Extra materiaal meeprinten, wat direct de kosten verhoogt, kan uiteindelijk zoveel kosten schelen in de nabewerking, dat de totale kosten lager uitvallen. Misschien is deze holistische benadering wel de grootste horde die men moet nemen als men met 3D-metaalprinten begint.