Laser Metal Deposition: analyse du processus
principes de base, applications et defis
Le rechargement laser, ou Laser Metal Deposition (LMD), comme méthode d'impression 3D des métaux est actuellement moins connu que la fusion sur lit de poudre, etc. Afin de bien évaluer le potentiel de cette technologie, il est donc important de prendre en compte les principes de base, les applications actuelles et les développements.
Principes de base
Comme c'est le cas pour presque tous les autres procédés additifs, le rechargement laser, ou LMD en anglais, repose sur le principe de la combinaison d'un substrat (matériau de base), d'une source de chaleur et d'un matériau additif pour construire une géométrie couche par couche. Le LMD utilise une source laser (continue ou pulsée) et une poudre ou un fil métallique aux propriétés spécifiques (composition chimique, taille des particules, diamètre du fil ...) qui est ajouté au bain de fusion. Dans cet article, seule la variante à base de poudre de métal est traitée plus en détails.
Par l'action de la source de chaleur sur le substrat, un bain de fusion est créé, tout comme lors du soudage, dans lequel le métal d'apport est appliqué. Pour cela, la poudre est soufflée dans le bain de fusion sous protection gazeuse par une buse. Le dépôt répété de couches superposées selon un motif prédéterminé peut ainsi être appliqué pour imprimer une géométrie fonctionnelle. De cette manière, des structures peuvent être ajoutées à un composant existant, comme des soudures de réparation ou des revêtements laser, ou un composant entièrement neuf peut être construit.
Pour rendre le dépôt indépendant de la direction du déplacement, on préfère en général une buse avec alimentation coaxiale de la poudre (figure 1A) à la variante avec alimentation latérale séparée. Dans le premier cas, le faisceau laser est positionné au centre et la poudre est fournie de manière coaxiale, soit par plusieurs trous répartis radialement, soit par une ouverture annulaire continue. L'optique laser complète, avec la buse en bas, peut être montée soit sur un système de portique, soit sur un robot (figure 1B).
L'utilisation de paramètres de fusion définis de manière optimale et d'une stratégie d'impression appropriée peut augmenter l'efficacité de la consommation de poudre (rapport entre la poudre fondue et la poudre fournie) à plus de 85%. Cependant, l'efficacité énergétique du procédé laser dépend fortement du métal utilisé, principalement en raison des différences de réflectivité. Les lasers infrarouges conviennent aux applications sur l'acier, tandis que les lasers à lumière bleue ou verte sont plus adaptés au cuivre. En outre, ces sources laser sont de plus en plus compactes et de moins en moins chères.
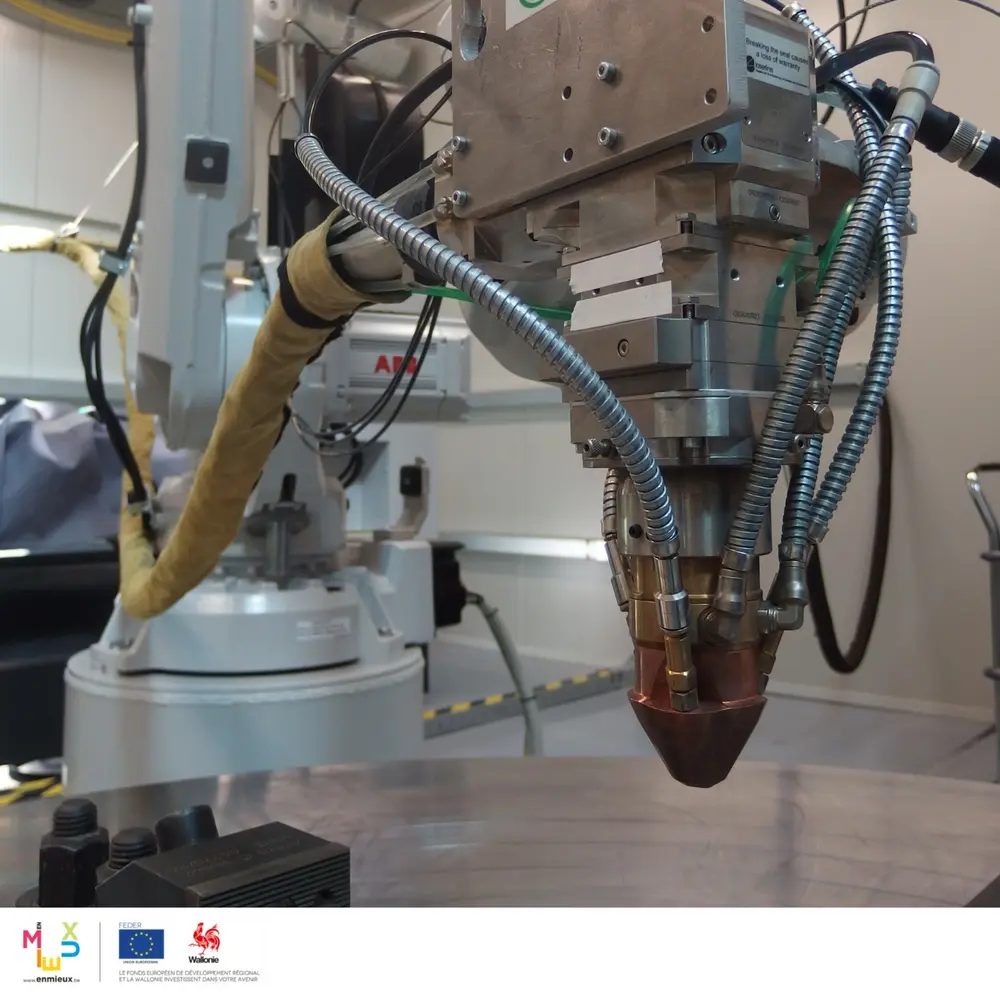
applications
Les composants adaptés à l'impression LMD ont généralement des dimensions comprises entre celles de la fusion sur lit de poudre (PBF en anglais) d'une part et les procédés basés sur l'arc électrique et le fil d’apport (WAAM) d'autre part. Les principales caractéristiques des techniques ci-dessus sont présentées dans le tableau 1. Toutefois, la PBF est limitée par la nécessité d'un espace clos, avec un volume limité. Des procédés tels que le LMD et le WAAM peuvent être utilisés dans des installations en espace confiné, mais aussi dans des environnements ouverts, à condition de respecter les mesures de sécurité appropriées, ce qui permet de produire des pièces plus grandes
Avantages
Le rechargement par dépôt laser offre un certain nombre d'avantages qui rendent cette technologie intéressante par rapport aux autres procédés d'impression. Il est par exemple possible d'ajouter des structures sur des pièces déjà existantes, ce qui permet de réparer des pièces endommagées ou de construire des fonctions spécifiques. Traditionnellement, ces réparations sont effectuées manuellement par soudage à l'arc. Elles peuvent prendre différentes formes: une fissure évolutive peut être enlevée et rebouchée (figure 2A), un coup dans une surface ou un coin cassé peut être comblé et les pièces usées ou cassées peuvent être reconstruites.
Limites
Mais le LMD présente également un certain nombre de limites, comme la production de surfaces en surplomb. Celles-ci posent un défi, en partie parce que l'application des structures de support, telles qu'elles sont appliquées en PBF, n'est pas encore bien développée. Soit le concepteur doit donner à la pièce une forme appropriée pour être compatible avec le LMD, soit la machine doit disposer des degrés de liberté suffisants pour faire face aux positions requises. Le LMD peut donc aussi être utilisé jusqu’à un certain point pour produire des surfaces horizontales, à condition que l'optique du laser puisse traiter un réglage d'angle allant jusqu'à 90°. Un robot équipé de manipulateurs externes peut convenir ici, mais même dans ce cas, cette application exige un logiciel puissant pour générer le parcours du laser. Autrement dit, plus la pièce est complexe et volumineuse, plus l'investissement nécessaire en termes de temps de conception et d'installation de la machine est important. La figure 2B présente un exemple de pièce relativement grande, construite à partir d'une plaque de base plane..
Le défaut a d'abord été fraisé, puis la cavité a été remplie par dépôt laser
Figure 2B A droite: Logo de CRM Group construit avec de la poudre 316L sur une plaque de base
Finition et reproductibilité optimisées
Dans de nombreux cas, un système LMD permet d'obtenir une meilleure finition et une meilleure reproductibilité grâce à l'automatisation du processus. En outre, la pièce subira généralement moins de déformations que dans les procédés à base de fil, grâce au diamètre contrôlé du point focal du laser et à l'apport de chaleur plus faible. Des tests antérieurs effectués par CRM Group sur l'inox ont démontré que les déformations peuvent être réduites d'un facteur cinq. En outre, il est relativement facile d'obtenir des compositions de poudre personnalisées compatibles avec la pièce à réparer. Cela contraste avec le fil d'apport, dont les compositions d'alliage sont plutôt limitées et où le fil sur mesure est difficile à trouver.
Fluidité de la poudre
Il convient également de mentionner que le LMD n'est pas aussi limité que la PBF en termes de fluidité de poudre. Par exemple, des poudres de forme moins régulière provenant d'autres sources que l'atomisation de gaz peuvent encore être utilisées. Par exemple, les poudres d'alliages mécaniques, fabriquées dans des broyeurs à boulets à haute énergie, et les poudres métalliques mélangées à des particules céramiques sub-microniques qui sont souvent assez facettées. Ces deux techniques sont intéressantes lorsque l'on souhaite intégrer des particules de renforcement ou fonctionnelles dans les composants imprimés.
Ajout de fonctions locales
Comme indiqué précédemment, le LMD peut également être utilisé pour ajouter certaines fonctions localement sur des composants existants. Une grande pièce peut ainsi être produite de manière très efficace et qualitative par forgeage ou moulage, puis finie avec le LMD pour ajouter des poignées, des dents, des renforts, etc. Les ajouts peuvent même être fabriqués dans un autre matériau si la compatibilité métallurgique peut être garantie (par exemple, une combinaison d'acier à outils et d'acier de construction). Une étude scientifique de Heilemann, Beckmann, Konigorski et Emmelmann (2018) s'est intéressée à la conception de renforts pour un fuselage d'avion en utilisant l'optimisation topologique. Les structures organiques résultantes ont ensuite été modifiées pour les rendre compatibles avec le LMD pour l'aluminium (figure 3A).
Combinaison de techniques
En outre, il est possible de concevoir des systèmes intégrés qui combinent diverses techniques, telles que les techniques additives et soustractives. Les surfaces imprimées ou réparées puissent être dotées d'une finition correcte au moyen, par exemple, d'un ponçage, d'un sablage ou d'un grenaillage. Différents procédés de fabrication additive peuvent également être combinés, par exemple LMD avec de la poudre ou du fil et la méthode WAAM. Divers avantages sont ainsi optimisés, notamment un taux de dépôt plus élevé avec le WAAM et des structures plus fines ou un autre matériau avec le LMD.
Defis et developpements
Les recherches actuelles en matière de LMD portent souvent sur le matériau d’apport. Pour le LMD, on utilise différents types de poudres:
- des poudres traditionnelles (316L, alliages Al-Si);
- des compositions déjà utilisées pour le rechargement laser où la fissuration se produit (Stellite®, acier à outils);
- des nouvelles compositions utilisées dans le cadre d’applications PBF pour l’aéronautique et l’aérospatiale (A20x®, Scalmalloy®).
Ajuster les paramètres
De nombreuses compositions sont déjà disponibles, mais trouver les bons paramètres de processus s'avère souvent difficile. En effet, ceux-ci dépendent du substrat, de la composition de la poudre, des dimensions et de la forme de la pièce, de sorte qu'il n'est pas facile de réussir du premier coup en raison de l'absence de modèles numériques facilement applicables. Le projet INSIDE metal AM, soutenu par Vlaio et SIM, vise à fournir aux fabricants et aux utilisateurs quelques directives qui les aideront à sélectionner la technologie d'impression appropriée pour les grandes pièces et les paramètres correspondants.
Optimisation du matériau d’apport
A ce jour peu de poudres ont été optimisées pour le processus LMD. Les vitesses de refroidissement modérées, qui se situent entre celles du soudage et celles de la PBF, peuvent empêcher l'exploitation du potentiel d'une poudre spécifique. C'est le cas, par exemple, du Scalmalloy®, qui dépend d'une vitesse de refroidissement élevée pour obtenir les propriétés souhaitées (Kürnsteiner et al., 2020). D'autre part, les cycles thermiques successifs qui se produisent pendant l'impression peuvent provoquer des contraintes résiduelles et entraîner des fissures dans, par exemple, les aciers à outils à haute dureté (Kempen et al., 2014). Ces deux caractéristiques du procédé, à savoir une vitesse de refroidissement moyenne et des cycles thermiques successifs, doivent être à chaque fois prises en compte dans la sélection des paramètres du procédé et l'élaboration de compositions de poudre à haute performance.
Figure 3B A droite: Coupe transversale d'un cordon de soudage par dépôt laser de cuivre/inox
Structures en matériaux multiples
De nombreux efforts sont également déployés pour développer davantage les structures multi-matériaux, c'est-à-dire les composants dans lesquels différents matériaux sont combinés. La nature de l'approvisionnement en poudre permet au LMD d'utiliser un système de distribution qui peut être connecté à plusieurs conteneurs de poudre en même temps, permettant ainsi un mélange ‘in situ’. De cette manière, des structures bimatériaux (figure 3A) ou des composants dont la composition change progressivement peuvent également être construits (figure 3B).
Pour les applications d'usure et de structure, les composants constitués d'un noyau doux et une surface dure peuvent être imprimés sur base de deux métaux compatibles. Toutefois, cette approche n'est pas seulement utile pour améliorer les performances mécaniques. Par exemple, les structures bimatériaux, comme les combinaisons cuivre-inox, peuvent également optimiser le transfert de chaleur (Chen & Liou, 2018).
D'autres combinaisons de matériaux intéressantes en sont encore à un stade précoce de la recherche : Al-steel, Al-Ti, Steel-Ti, Al-Cu ... (Karnati, Zhang, Liou, & Newkirk, 2019). Cependant, les réactions entre ces métaux aboutissent souvent à des composés intermétalliques fragiles à des mécaniques correspondantes qui influencent trop négativement la facilité d'utilisation. Les recherches en cours portent donc également sur l'application de couches intermédiaires compatibles avec les deux matériaux et pouvant garantir une résistance mécanique suffisante.
Systèmes LMD plus compacts
En plus des matériaux, des développements liés aux machines sont également en cours. Cela concerne principalement le développement de systèmes LMD plus compacts avec des coûts d'investissement plus faibles. Certaines entreprises proposent des solutions dont les dimensions vont d'une petite pièce à un modèle de table. Des sources laser, des optiques, des unités d'alimentation en poudre et des manipulateurs plus compacts permettront d'offrir des systèmes transportables pour la fabrication de tout type de pièces détachées ou la réalisation d'opérations de haute précision dans des environnements difficiles et sans opérateur.
Plus d’informations?
Cette contribution a été réalisée dans le cadre du projet INSIDE Metal AM, soutenu par Sirris, CRM et IBS afin de développer l'impression 3D pour des aciers à haute résistance et aciers inoxydables, avec le soutien de l'Agence flamande pour l'innovation et les entreprises (Vlaio) et l'Initiative stratégique Matériaux (SIM-Flanders).
La fusion sur lit de poudre (PBF, SLM), le rechargement par dépôt laser (LMD) et la fabrication additive à l'arc électrique (WAAM) font tous l'objet de l'étude. Le projet se concentre sur les matériaux 316L, 17-4PH, H11/H13, M3 (pour le LMD), S355 et l'acier inoxydable duplex (pour le WAAM). Des démonstrateurs seront fabriqués en collaboration avec des partenaires industriels, puis une évaluation technique et économique sera réalisée.
Si vous êtes intéressé par le projet ou si vous avez des questions, n’hésitez pas à contacter frederik.hendrickx@crmgroup.be.