Schroefdraad uit een ander vaatje getapt
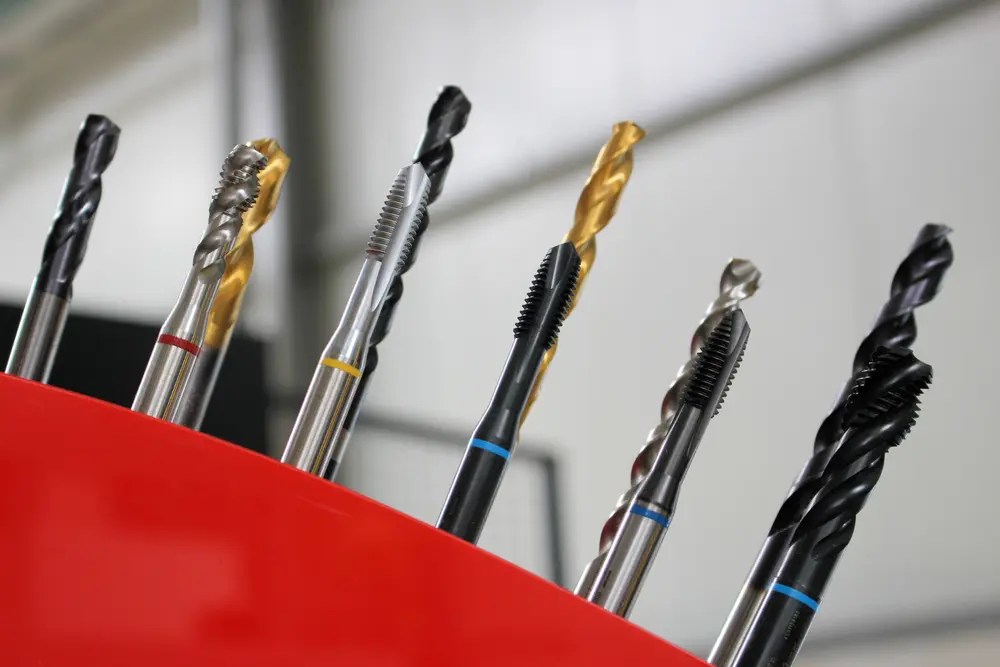
Schroefdraad aanbrengen in een werkstuk: een noodzakelijke bewerking die niet zonder risico is, want het onderdeel heeft dan al een aantal bewerkingsstappen ondergaan. Een afgebroken tapboor kan een forse schadepost betekenen. Hoe kun je nog op andere manieren proceszeker en betrouwbaar schroefdraad aanbrengen?
De uitkomst van het tappen hangt niet alleen van de gekozen techniek af, maar ook van het gereedschap en niet het minst het materiaal. Dat bepaalde legeringen lastiger te bewerken zijn is wel bekend. Wat men zich vaak niet realiseert, is dat voorafgaande bewerkingen ook van invloed kunnen zijn. Een lasergesneden plaat gedraagt zich bijvoorbeeld anders dan het materiaal in de oorspronkelijke gewalste vorm.
Een schroefdraad tappen is in een lasergesneden gat een heel andere bewerking dan in een geboord gat. Dat komt doordat de warmte die tijdens het lasersnijden in het materiaal komt, de randzone beïnvloedt en het materiaal hier verandert. Dat heeft een negatief effect op de standtijd en de kwaliteit van het tapgat, als men daar bij de gereedschapskeuze geen rekening mee houdt. Een tap met een coating is noodzakelijk om de wand van het gat open te breken, zodat de schroefdraad in het onderliggend materiaal kan worden aangebracht.
Juiste randvoorwaarden
Een aspect dat eigenlijk voor elke tapbewerking geldt, is de juiste opspanning van het werkstuk als men met een tapboor werkt. Een werkstuk dat niet goed is opgespannen, kan tot een slechte kwaliteit schroefdraad leiden of – nog erger – een afgebroken tap. Daarnaast is het juiste gebruik van koelsmeermiddel een van de succesfactoren. Om een optimale afvoer van de spanen te creëren, is interne koeling door de spindel en tapboor de ideale oplossing. Dat zorgt voor het kleinste risico op breuk. Vooral bij diepe gaten (2 tot 3xD) is dat de beste aanpak, waarmee ook de standtijd van het gereedschap verlengd wordt.
Lang niet elke CNC-machine biedt echter die optie. In dat geval is het belangrijk de nozzle van het koelsmeersysteem goed te positioneren zodat die precies op het gereedschap is gericht. Voor deze externe toevoer moet de spaanvorming van het materiaal in elk geval goed zijn; bij andere materialen heeft interne koeling de voorkeur. De gebruikte emulsie kan eveneens van invloed zijn, bijvoorbeeld als er sprake is van snijkantenopbouw of uitbrokkeling van het hardmetaal in het gereedschap. Verkeerde emulsie kan dan een van de oorzaken zijn.
Wanneer is roltappen een alternatief?
Een alternatieve bewerking voor het aanbrengen van schroefdraad met een tapboor is roltappen. Er gelden wel enkele voorwaarden. Zo moet het materiaal een zekere taaiheid (meer dan 8 tot 10% rek) hebben en een maximale treksterkte van 1.200-1.400 N/mm², anders zijn de roltappen niet geschikt. Daarnaast is het belangrijk om het gat met de exact benodigde diameter te boren. Omdat men de draad ‘rolt’, moet het voorgeboorde gat een grotere diameter hebben dan de uiteindelijke tap. Fabrikanten van roltappen gebruiken hiervoor omrekentabellen.
Als aan alle uitgangspunten voldaan wordt, is roltappen een erg betrouwbaar en snel proces
Tot slot moet men er rekening mee houden dat roltappen meer vergt van de CNC-machine. Het benodigd koppel ligt hoger, tot wel 50 procent. Als aan die uitgangspunten voldaan kan worden, dan is roltappen een erg betrouwbaar proces omdat het spaanloos is. Bovendien wint men tijd, omdat de omvormsnelheid wezenlijk hoger ligt dan de doorsneesnijsnelheid van een tapboor. De schroefdraad ontstaat door de plastische vervorming van het materiaal (vandaar de maximale treksterkte en een zeker taaiheid).
Omdat roltappen een spaanloze bewerking is, vermijdt men de gevolgen van een spaan die klem komt te zitten tussen het gereedschap en de wand van het gat. De nauwkeurigheid van roltappen is hoger dan bij de spaanvormende tapbewerkingen. Dat geldt eveneens voor doorlopende gaten.
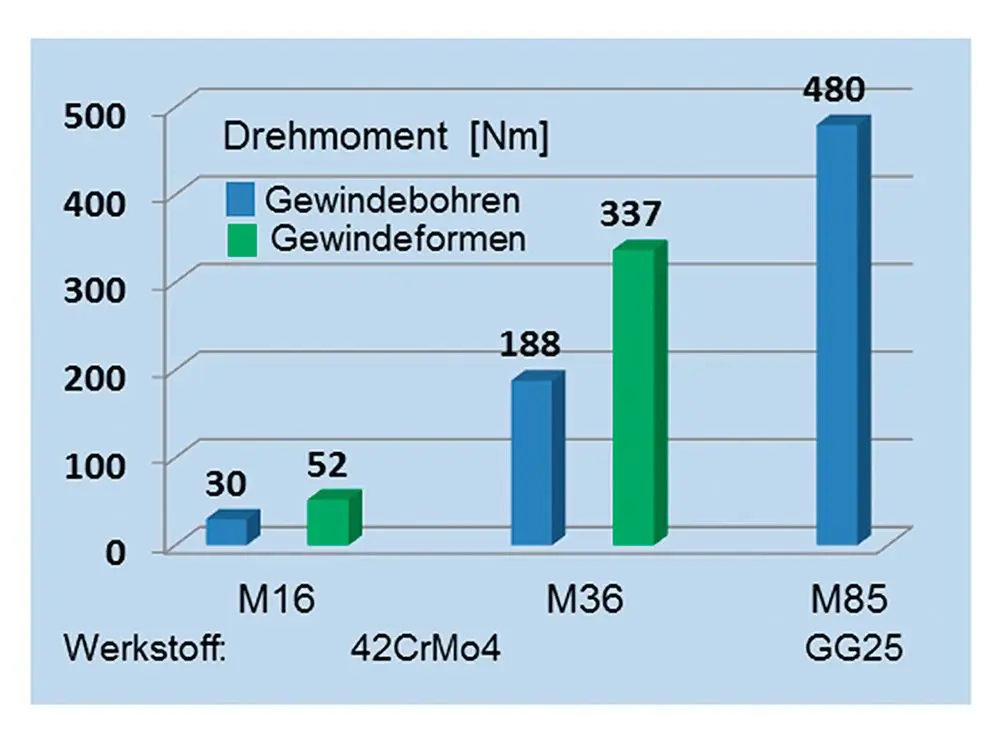
Sterkere schroefdraad
Roltappen is een betrouwbaar proces, ook voor grotere draaddieptes. In de eindtoepassing levert de technologie ook enkele voordelen op. Zo heeft de draad een hogere afschuifwaarde en is die dus sterker dan een getapte draad. Dat is eenvoudig te verklaren: bij draadtappen haalt men materiaal weg. De helling van de spoed wordt dus eigenlijk zwakker. Bij draadrollen wordt het materiaal verdrongen: de totale hoeveelheid materiaal blijft gelijk, ze wordt alleen anders verdeeld in de spoed. Daardoor is de draad sterker. Ook is de oppervlaktekwaliteit beter dan bij draadsnijden.
Fabrikanten hanteren gestandaardiseerde aansnijvormen voor de roltappen en ook hier kan men kiezen voor roltappen met een inwendige koeling. De levensduur van de roltappen wordt daardoor extra verlengd, hoewel dat argument minder zwaar weegt omdat die gereedschappen al een lange standtijd hebben. Wel biedt de inwendige koeling het voordeel dat het koelsmeermiddel precies op de plaats komt waar de wrijving het hoogst is. Een standtijdprobleem kon zich voorheen voordoen als spanen of vuil in de rolkop terechtkwamen. De nieuwste generatie rolkoppen heeft hiervoor speciale spaanschilden.
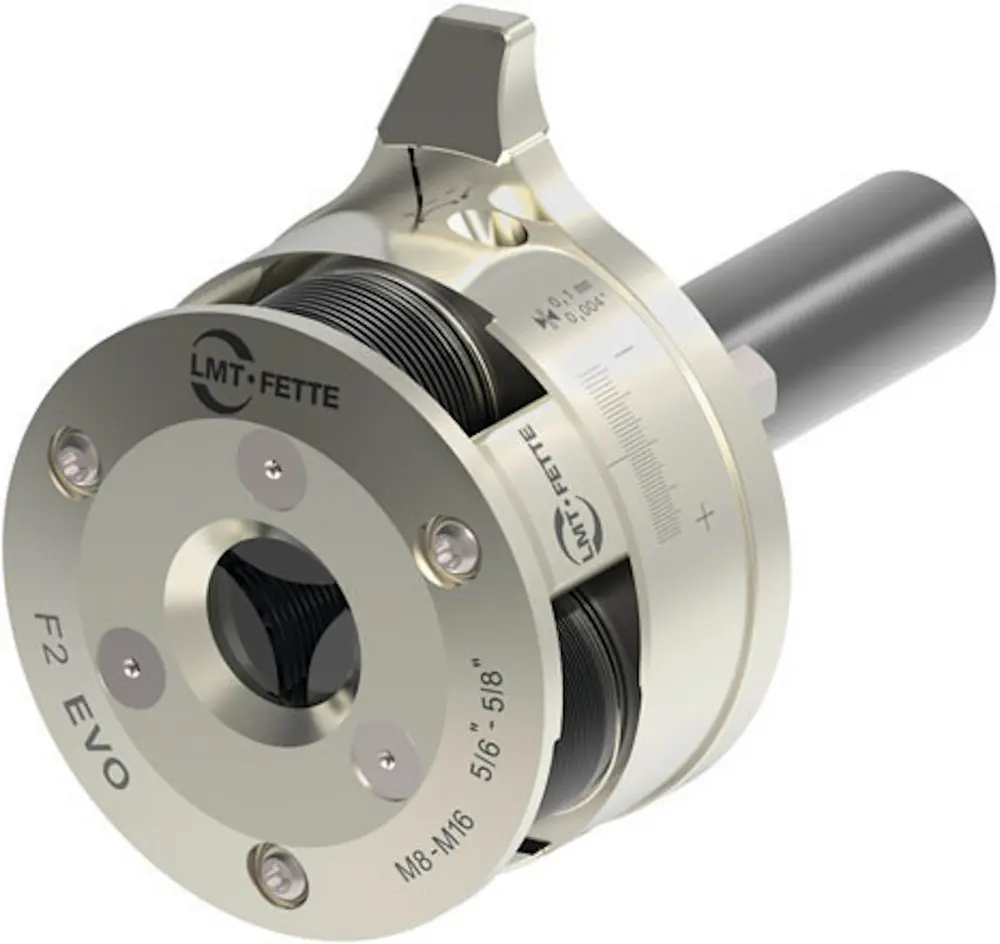
Draadfrezen
Een tweede alternatief voor tapboren is het frezen van de schroefdraad met een draadfrees. Met name voor grotere diameters is dat een goede oplossing omdat de nauwkeurigheid hoger ligt dan bij een snijtap. Een voorwaarde is wel dat de CNC-machine een spiraalbeweging kan maken; qua belasting liggen de snijkrachten onder de krachten die vrijkomen bij het klassieke tappen van draad. De spiraalbeweging wordt geprogrammeerd met een radiuscompensatie om de schroefdraadtolerantie eenvoudig aan te passen. Draadfrezen kan zowel voor blinde als doorlopende gaten worden toegepast. De nauwkeurigheid is hoog omdat men de schroefdraadbewerking exact programmeert. Bij blinde gaten controleert men eenvoudig de diepte van het gat.
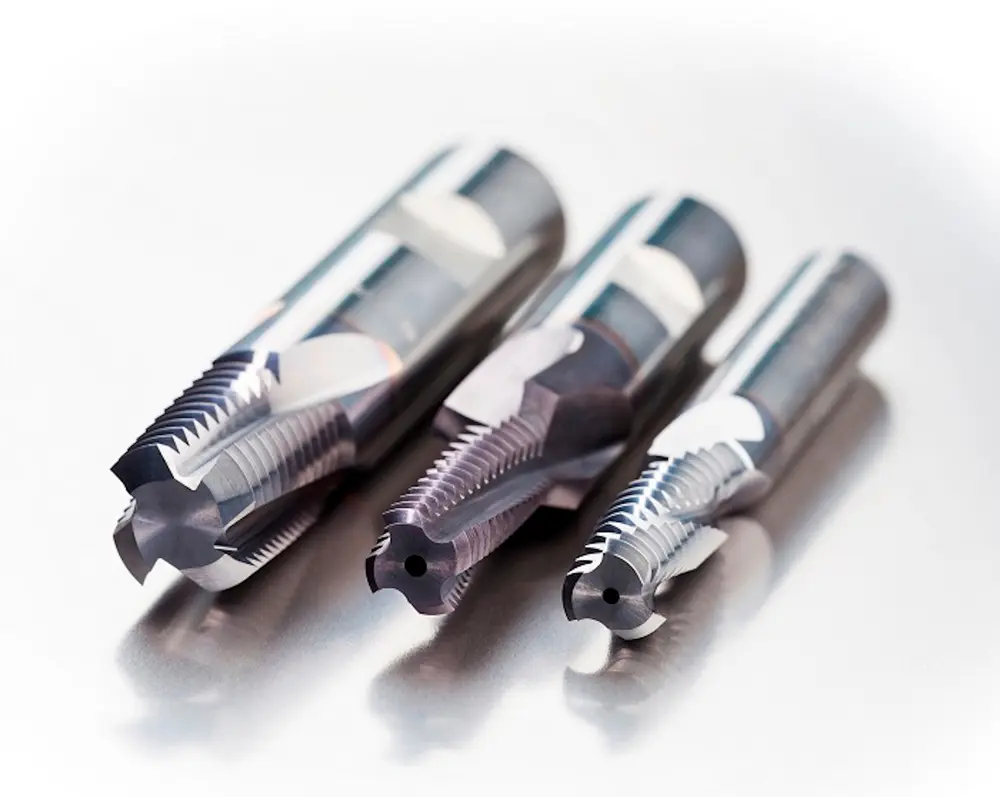
Dormer Pramet biedt ook draadfrezen aan, bijvoorbeeld voor materialen als Inconel en titanium. Bij een eventuele breuk kan men het gat uitboren zonder de diameter te wijzigen
Een van de voordelen van draadfrezen is dat er korte spanen ontstaan. Het risico neemt verder af doordat de diameter van de frees kleiner is dan de voorboordiameter. Bij een gereedschapsbreuk kan men dus het restant van het gereedschap uit het materiaal verwijderen en het draadsnijden met een nieuw gereedschap herstarten; de doorsnede van het gat is immers gelijk gebleven. Omdat men de spiraalbeweging in de CNC-besturing programmeert, kan men met één gereedschap meerdere diameters maken. Een M8- of M12-gat met schroefdraad wordt dus met dezelfde frees gemaakt. Wel moet de spoed van de draad gelijk blijven.
Het feit dat men de gebroken draadfrees uit het werkstuk kan halen, maakt draadfrezen aantrekkelijk voor dure werkstukken
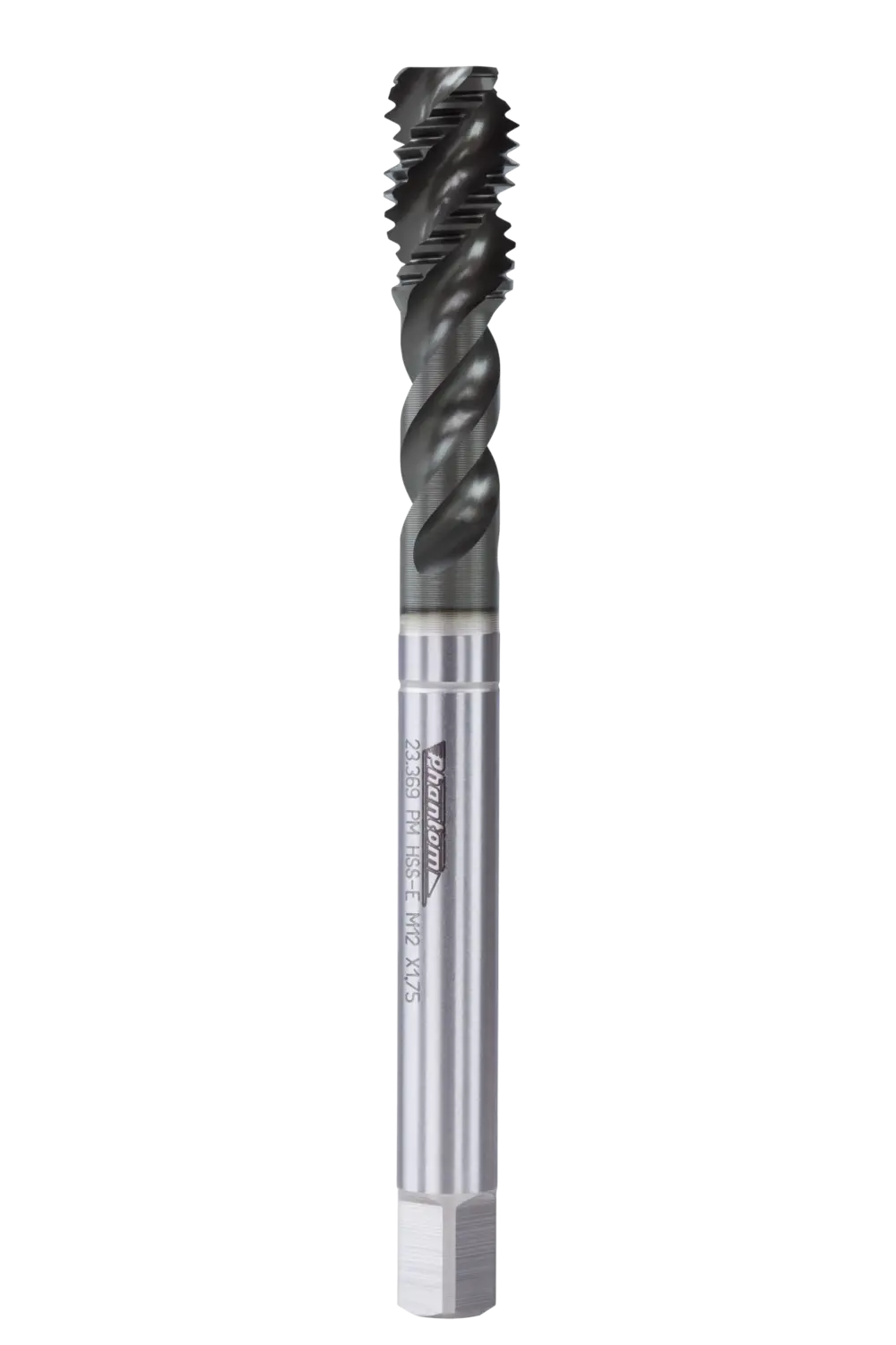
Het feit dat men de gebroken draadfrees uit het werkstuk kan halen, maakt draadfrezen aantrekkelijk voor dure werkstukken in materialen zoals Inconel of titanium. Omdat er relatief lage snijkrachten optreden, leent het draadfrezen zich voor dunwandige producten. Een nadeel van draadfrezen is wel dat de frees slijt, wat ten koste gaat van de nauwkeurigheid. Die slijtage moet men in het programma compenseren.
Er zijn tegenwoordig gereedschappen verkrijgbaar, de microdraadfrezen, waarmee men zowel het gat boort, verzinkt en de draad freest in één bewerking. De beperking van draadfrezen is wel de diepte van het gat waarin men de schroefdraad aanbrengt. De limiet is door sommige fabrikanten inmiddels opgetrokken naar 3xD, 2xD is de standaard maximale diepte.
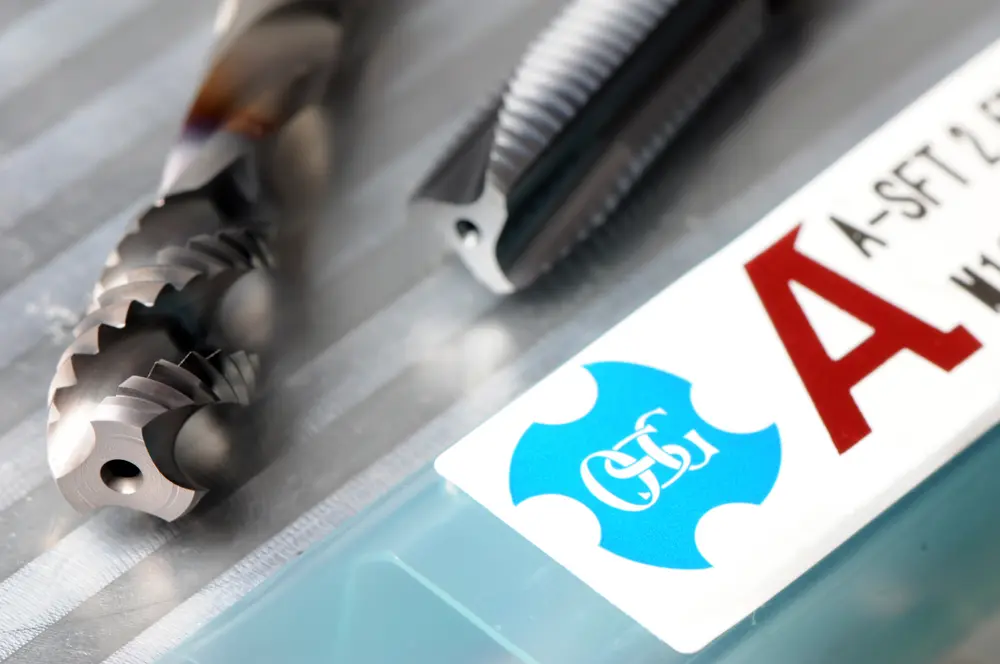
Draadwervelen
Een variant op het draadfrezen is het draadwervelen. Hierbij worden wisselplaten in een speciale ring geplaatst die over een asvormige component gaat om de uitwendige schroefdraad aan te brengen. Deze techniek leent zich goed voor speciale schroefdraadvormen, omdat de vorm vrij programmeerbaar is. Ook is de oplossing geschikt voor lange, slanke componenten. Inwendige schroefdraad kan men hiermee niet aanbrengen. Daarvoor kan men wel overstappen naar het draaien van schroefdraad.
Welke techniek men kiest voor het aanbrengen van schroefdraad in een werkstuk, wordt uiteindelijk bepaald door de toepassing, de combinatie van werkstukgeometrie, materiaal, seriegrootte en gevraagde procesbetrouwbaarheid. Het is evenwel goed bewust te zijn dat er meerdere oplossingen beschikbaar zijn.
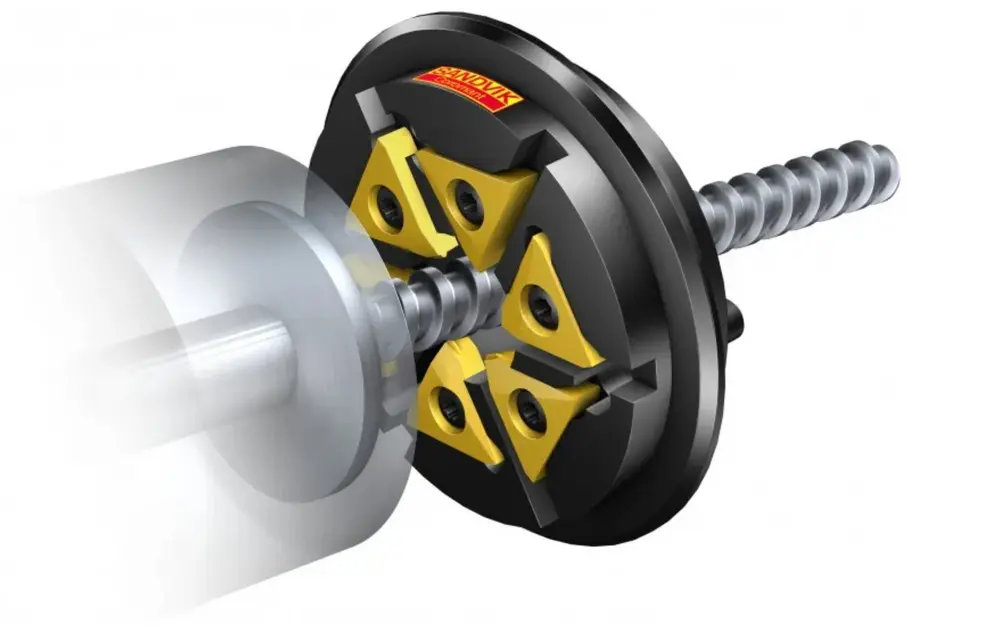
Het draadwervelen, zoals onder andere Sandvik Coromant aanbiedt, is een nichetechnologie voor het aanbrengen van uitwendige schroefdraad met een hoge nauwkeurigheid