Plooien is allang niet meer buigen of barsten
Verschillen in materiaal en plaatdikte minder van invloed
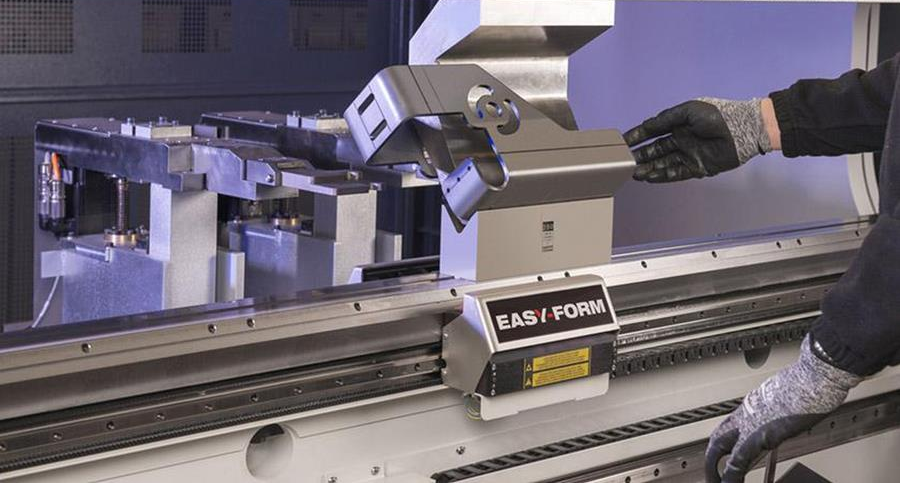
Bij het plooien, buigen of (af)kanten wordt sinds jaar en dag gestreefd naar een hoeknauwkeurigheid van circa 0,5° (soms zelfs al 0,3°). Om overschrijding van deze waarde te voorkomen, is het zaak tijdens de buigcyclus de hoek van het werkstuk te meten, bij voorkeur realtime. Dat gebeurt met hoekmeetsystemen onder gebruikmaking van sensor- dan wel lasertechnologie. De technologische waarde van het hoekmeetsysteem is afhankelijk van de door de fabrikant gekozen systematiek. Aangezien een goed hoekmeetsysteem zowel tijd- als materiaalverlies voorkomt, betaalt een investering hierin zich nagenoeg altijd uit.
hoeknauwkeurigheid
Plooien – in Nederland buigen of (af)kanten − is een bewerkingstechniek waarbij plastische deformatie optreedt van het plaatmateriaal door dit met grote kracht te buigen. De metaalplaat bevindt zich daarbij tussen een stempel en een (onder)matrijs. Door de stempel (doorgaans mesvormig) met veel kracht in de ondermatrijs/groef te drukken (doorgaans V-vormig) treedt een permanente vormverandering op.
Een hoekmeetsysteem controleert of de gebogen hoek voldoet aan de parameters
Het is precisiewerk dat handmatig kan worden uitgevoerd, maar als het aankomt op grote buigbreedten en/of dikke platen is het gebruik van een plooibank aangewezen. Het streven is te komen tot een hoeknauwkeurigheid van circa 0,5°. Bij sommige metaalbedrijven wordt tegenwoordig al gewerkt met een nauwkeurigheid 0,3°. De haalbaarheid daarvan wordt voornamelijk bepaald door:
- Het buigproces;
- De aard van de hoekmeting;
- De productradius (zie begrippenkader): een kleine(re) productradius resulteert in geringe(re) terugvering;
- De wijze van uitvoering en gegevensverwerking.
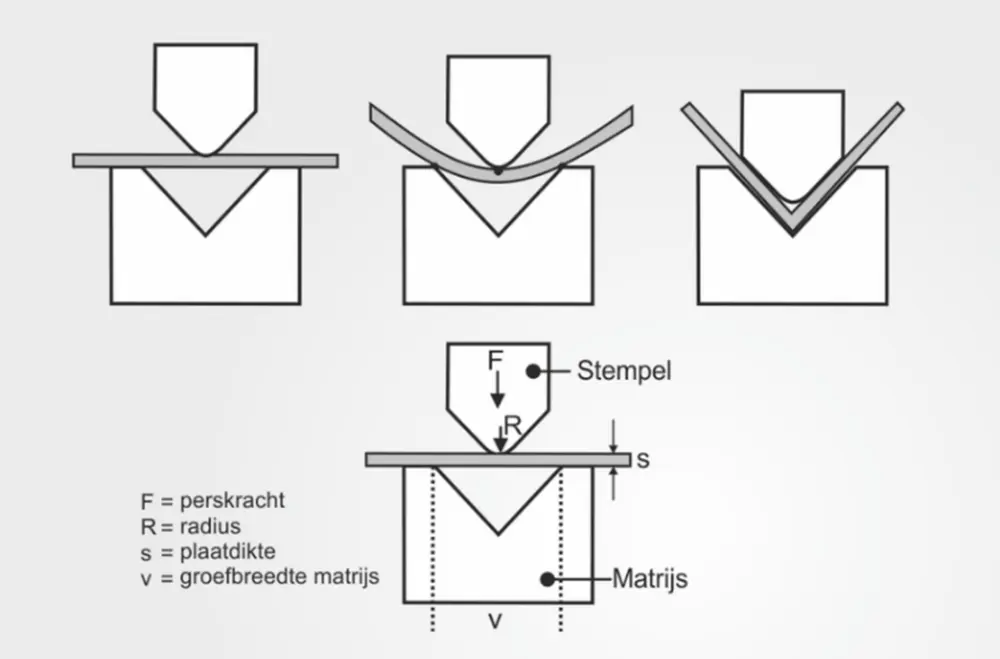
BELANGRIJKE BEGRIPPEN
Buigradius: parameter bepalend voor de plaateigenschappen na het plooien. Naarmate de buigradius groter is, zijn het breukgevaar en het sterkteverlies geringer; hoe kleiner de buigradius, hoe groter de afname van de materiaaldikte bij het buigpunt.
Maximale buighoek: in verband met de terugvering van het materiaal moet de plaat altijd iets verder worden gebogen dan de opgegeven hoek.
Minimale beenlengte: de minimale opleg van de plaat op de matrijs, nodig om de buiging te kunnen uitvoeren; deze wordt bepaald door de plaatdikte.
Productradius: een kleine(re) productradius resulteert in geringe(re) terugvering (zie hierna).
Terugveren: het na het plooien deels ‘terugkeren’ van het materiaal in de oorspronkelijke positie; elk materiaal heeft karakteristieke terugveringswaarden. Hiermee dient rekening te worden gehouden met het oog op de gewenste toleranties.
Vrijbuigen: plooitechniek waarbij de stempel het werkstuk in de matrijs drukt zonder daarbij de wanden te raken. Terwijl de stempel naar beneden beweegt, buigen de vlakken van het werkstuk naar boven en ontstaat een hoek die kleiner is naarmate de stempel het werkstuk dieper in de matrijs drukt.
voordelen
Door de variatie in plaatdikte en materiaalkwaliteiten – treksterkte, walsrichting − kan de hoek afwijken van de vooraf geprogrammeerde waarde. Het herstel hiervan gaat gepaard met materiaal- en tijdverlies. Om overschrijding van de voorgeschreven hoeknauwkeurigheid te voorkomen, is het zaak tijdens de buigcyclus de hoek van het werkstuk te meten.
Het hoekmeetsysteem mag het proces niet vertragen
Dit gebeurt met een hoekmeetsysteem, een systeem dat op basis van sensor- of lasertechnologie automatisch en realtime controleert of de gebogen hoek daadwerkelijk voldoet aan de ingestelde parameters. Daarbij wordt automatisch gecorrigeerd voor de treksterkte, de dikte en de walsrichting van het plaatmateriaal en voor de uitvoeringscorrectie. Een dergelijk systeem biedt uiteraard grote voordelen, zowel bij enkelstuks- als bij serieproductie. Het aantal proefbuigingen kan in dat geval namelijk drastisch worden beperkt of zelfs tot nul worden gereduceerd.
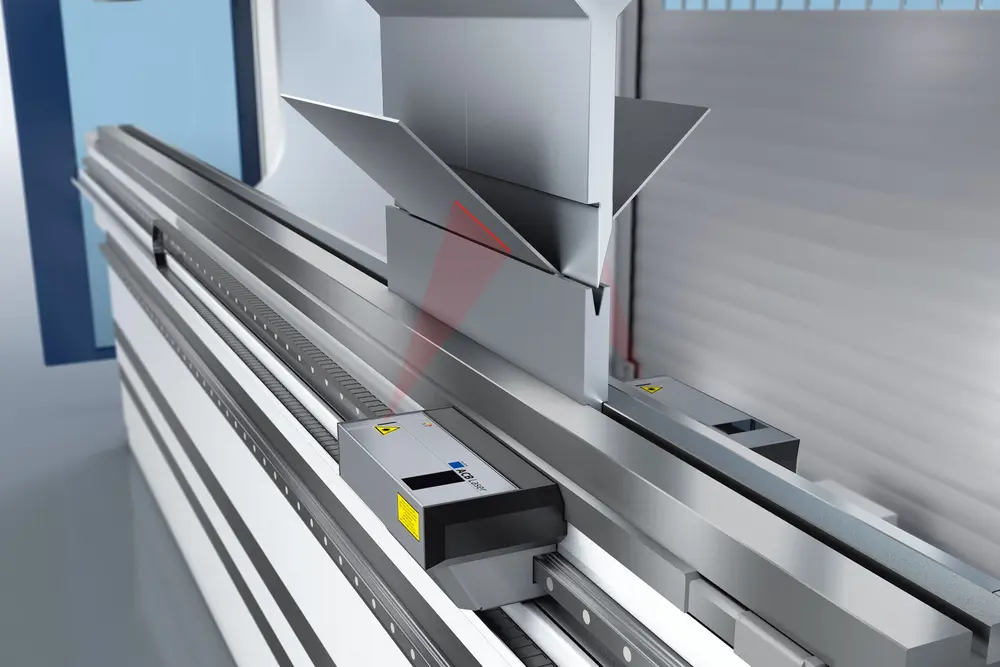
meetvoorwaarden
De belangrijkste voorwaarde is dat de hoekmeting het proces niet mag vertragen. Verder dient nog aan een tweetal andere voorwaarden te worden voldaan: de meting dient plaats te vinden volgens het triangulatieprincipe (driehoeksmeting) − omgevingsinvloeden worden op die manier grotendeels uitgesloten – en de meetpositie dient zo te worden gekozen dat invloeden van zwaartekracht (doorhangen) en traagheidseffecten (trillen) het meetresultaat minimaal beïnvloeden. Een hoekmeetsysteem maakt gebruik van sensor- dan wel lasertechnologie.
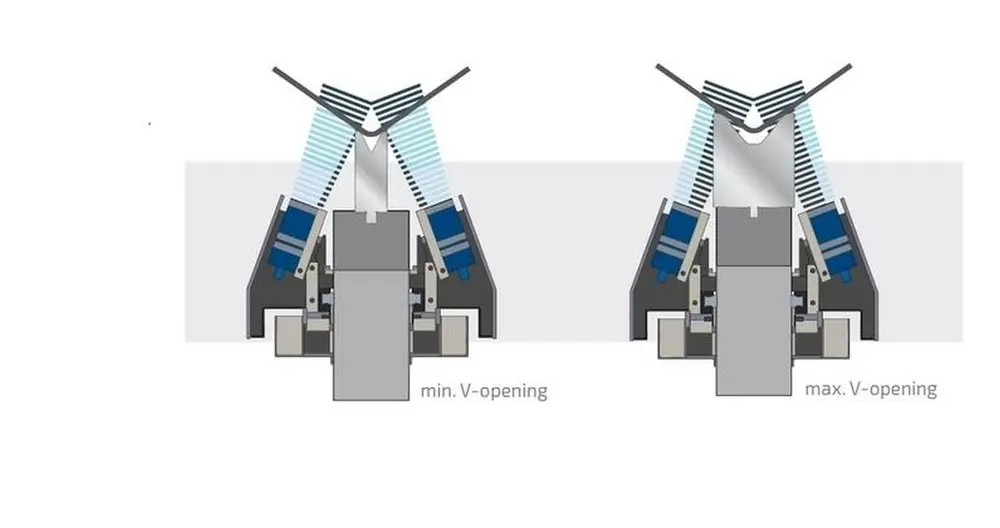
FACTOREN DIE DE HOEKMETING BEÏNVLOEDEN
• Doorhangen van de benen van het werkstuk: hangen deze (te) ver door, dan is een nauwkeurige meting niet langer mogelijk aangezien de gemeten hoek dan groter is dan de feitelijk gerealiseerde hoek;
• Terugvering: doordat het product in zekere mate elastisch blijft, zal het werkstuk na ontlasting weer enigszins terugveren met als gevolg dat de gerealiseerde hoek feitelijk groter is dan de vereiste hoek. Voor de terugvering kan alleen softwarematig worden gecorrigeerd;
• Traagheidseffecten: na de bewerking kunnen de benen van het werkstuk nog enige tijd natrillen. Derhalve is het voor een nauwkeurig meetresultaat noodzakelijk te wachten tot de trilling volledig is uitgedempt;
• Variatie van de buighoek: de buighoek blijkt als gevolg van vervormingen in de kantbank zelf niet over de gehele buigas constant te zijn. Variatie in plaatdikte en treksterkte kan een hoekvariatie veroorzaken, bijvoorbeeld bij warm gewalste plaat. Een twee- of driepuntsmeting kan dit probleem oplossen middels schuinstelling en bombering.
Sensormeting
Sensoren voor hoekmeetsystemen dienen aan een aantal voorwaarden te voldoen. Ze moeten:
- klein zijn, zodat ze eventueel in het mes of in de matrijs kunnen worden gemonteerd;
- de vereiste buighoek kunnen meten vrij van omgevingsinvloeden;
- geschikt zijn voor meervoudig gevouwen producten en voor producten met een geringe beenlengte;
- beschikken over een groot meetbereik en een variabele meethoek;
- een meetsnelheid hebben die is aangepast aan de servohydrauliek en aan een meetslag van circa 0,3 s voor dunne plaat;
- de volledige buigcyclus kunnen meten en metingen bij kleine buighoeken niet hinderen;
- onafhankelijk zijn van het plaatoppervlak (bekleed of onbekleed) en de materiaalsoort.
Het is voldoende om op een enkel punt te meten. Op basis van dat resultaat zullen de assen zo worden aangestuurd dat het plooiresultaat correct is.
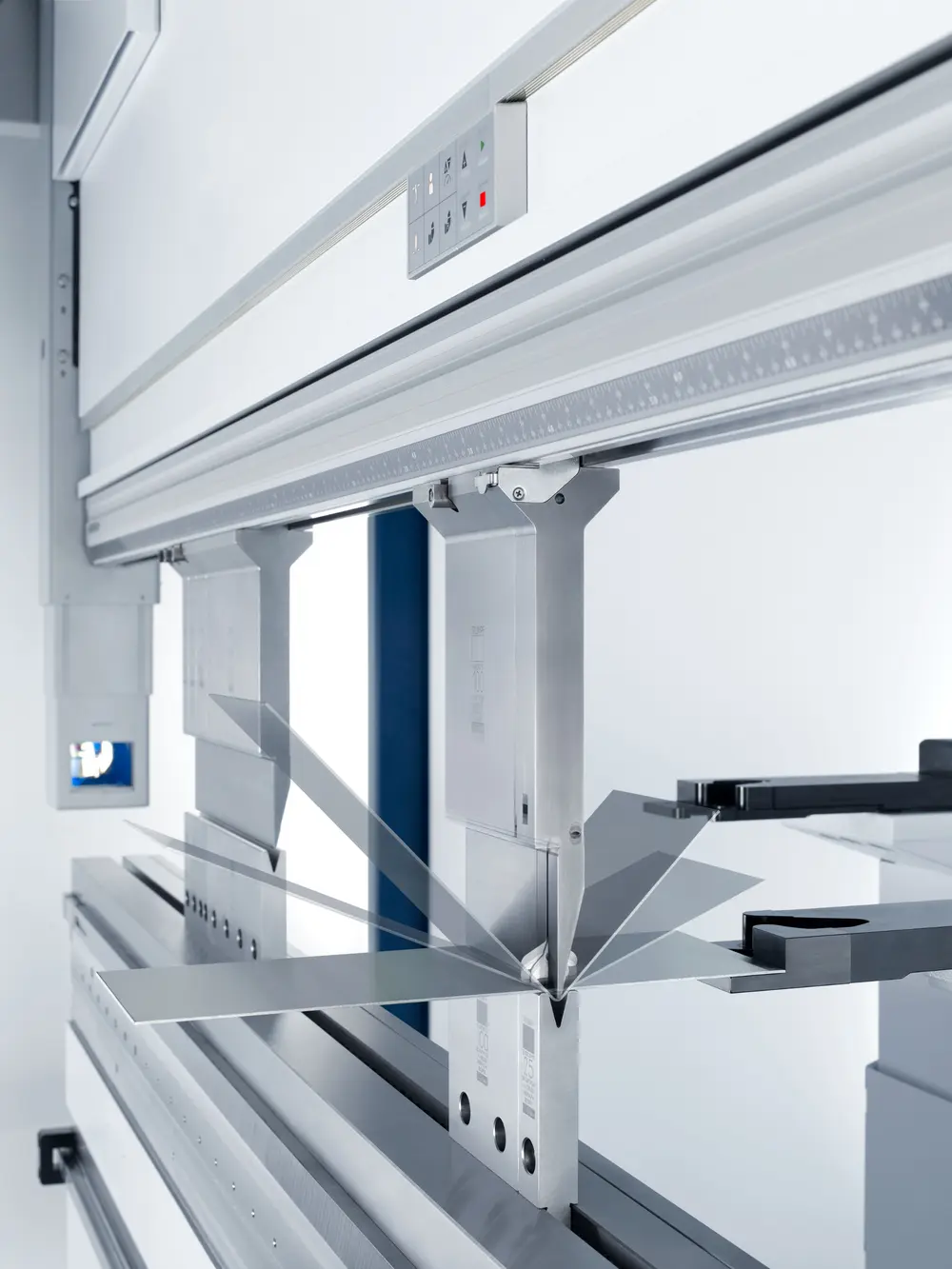
Systematiek
De technologische waarde van het hoekmeetsysteem is afhankelijk van de door de fabrikant gekozen systematiek.
Adaptief hoekmeetsysteem
Vanaf het begin van het plooiproces voedt het systeem de cnc-sturing realtime met digitale informatie. Aan de hand van die informatie wordt de positie van de ram of zetbalk en die van de stempel onmiddellijk aangepast teneinde (weer) de juiste hoek te verkrijgen. Doordat de encoders zijn verbonden met de tafel heeft eventueel optredende vervorming tijdens het plooien geen invloed op de positioneernauwkeurigheid van de ram. Het lasersysteem is zodanig geconstrueerd dat er automatisch wordt gecompenseerd voor materiaalvariaties als plaatdikte, koudversteviging en walsrichting.
Database hoekmeetsysteem
Het systeem beschikt over een database met een groot aantal terugveringswaarden voor een grote variëteit aan materialen. Op grond hiervan wordt een correctie op de diepte-instelling berekend teneinde tot de juiste hoek te komen. Ook is dan een hoekmeting met een actieve meting van de terugvering mogelijk. Er wordt tijdens het buigproces gemeten op één of op drie posities. Daaruit kan – na correctie voor bombering en schuinstelling − de terugvering worden vastgesteld die worden opgeslagen in de database. Het buigproces verloopt hierdoor sneller waardoor er minder productietijd verloren gaat.
Thickness-Controlled-Bending (TCB)
TCB is een eenvoudige functie die bij het buigen compenseert voor variaties in plaatdikte. Die worden veroorzaakt tijdens de fabricage zelf en tijdens het rolproces: de dikte kan daardoor bijvoorbeeld aan de randen anders zijn dan in het midden. Met behulp van rekstrookjes op de kolommen wordt de werkelijke plaatdikte bepaald. In de machine aanwezige sectoren detecteren de dikte van de volgende plaat en passen de invaldiepte van het bovengereedschap daarop aan.
Investering
Dankzij een hoekmeetsysteem beschikt de gebruiker continu over informatie over de hoek waaronder het plaatmateriaal staat. Ontstane afwijkingen ten gevolge van materiaal- en plaatdikteverschillen, walsrichting en dergelijke worden direct gesignaleerd en automatisch gecompenseerd. Daarnaast is er nog een belangrijke reden om te investeren in een goed hoekmeetsysteem: bij geautomatiseerd buigen werken proefbuigingen en metingen verstorend op het proces, en bovendien vergt proefbuigen doorgaans al gauw twee keer zoveel tijd dan regulier buigen. Tijd = geld, en investeren in een hoekmeetsysteem is dan dus al gauw een zinvolle investering.
Met dank aan: LVD, V.A.C. Machines