Vonkeroderen aan tweede jeugd begonnen
Technologie wordt toegankelijker
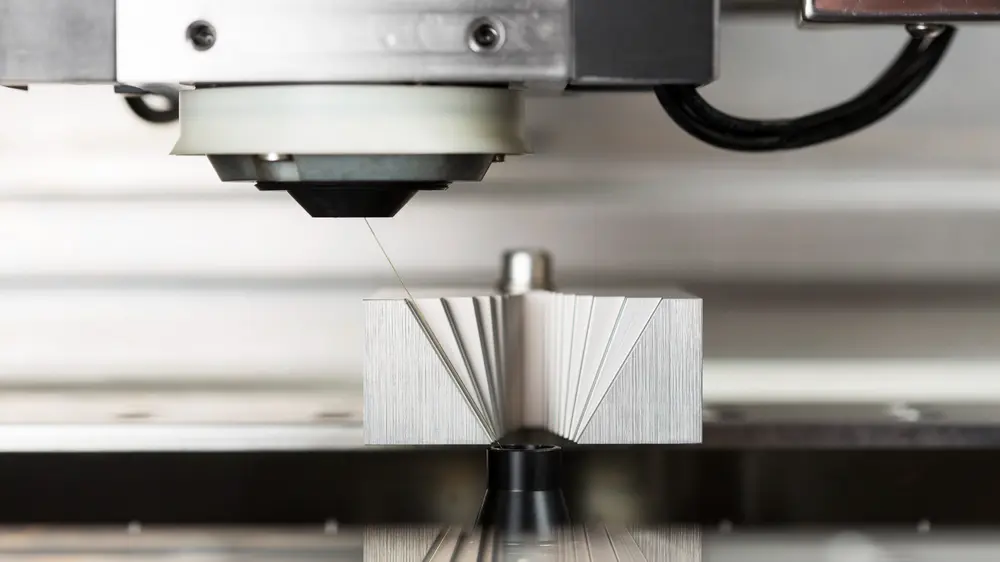
Draad- en zinkvonken zijn eigenlijk nooit weggeweest. Een aantal jaren stond de technologie misschien iets minder op het netvlies van precisieverspaners, maar recente ontwikkelingen van zowel de technologie als de nauwkeurigheden die de markt vraagt, maken vonkeroderen weer actueel. En nu niet alleen bij bedrijven die de traditionele vonktoepassingen maken, maar ook bij veel machinefabrieken.
Evolutie door de jaren heen
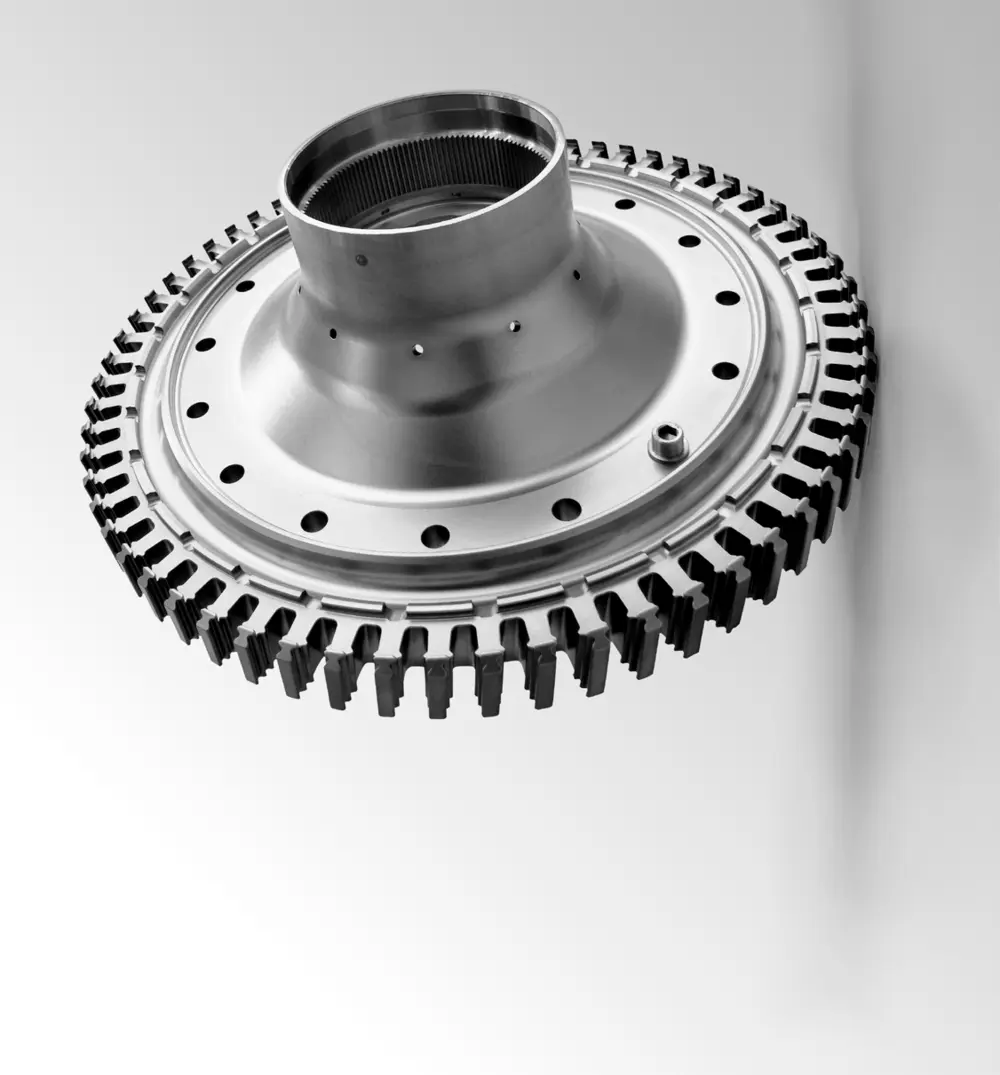
In de verspaning is vonkeroderen een relatief jonge technologie, die pas zo’n 60 jaar geleden echt is doorgedrongen tot de maakindustrie. De ontdekking dat je met een elektrische vonk tussen twee elektrodes metaal kunt wegnemen, dateert nochtans al van 1770. Maar pas aan het eind van de Tweede Wereldoorlog kwamen Russische onderzoekers erachter dat het onderdompelen van de elektrodes (de gereedschaps- en de werkstukelektrode) in een diëlektricum het proces beter beheersbaar maakt.
Dat is het begin geweest van de echte ontwikkeling van zinkvonken (voor 3D-vormen); later gevolgd door draadvonken. Pas eind de jaren zestig werd de technologie commercieel beschikbaar, waarbij in de jaren tachtig het gegeven dat je hardmetaal kon bewerken voor de echte doorbraak zorgde.
Een belangrijk voordeel van deze technologie is dat er geen beschadiging van het oppervlak van het werkstuk plaatsvindt, doordat er geen contact is met de gereedschapselektrode. Hierdoor haalt men hoge oppervlaktenauwkeurigheden.
VOORDELEN ten opzichte van andere bewerkingen
Dat vonkeroderen nu weer meer aandacht trekt, komt ook door het toenemend gebruik van moeilijk te bewerken materialen, de miniaturisatie en toenemende complexiteit van tal van producten en het gegeven dat OEM’s alsmaar hogere nauwkeurigheidseisen stellen. Met name zinkvonken levert een hoge maat- en vormnauwkeurigheid, doordat er geen mechanische belasting van de elektrode is.
Vonkerosie vormt oplossing voor moeilijk te bewerken materialen
Bepaalde features, zoals zeer kleine inwendige radii, zijn enkel met zinkvonken aan te brengen. Een andere zinvolle toepassing is het maken van spline-vertandingen. Weliswaar gebeurt dit met een afwikkelfrees in een veel hoger tempo en daardoor tegen lagere kosten per tandwiel, maar dergelijke gereedschappen zijn erg duur. Dit heeft dus pas zin als er een behoorlijke serie gemaakt moet worden. Bij prototypes of geringe aantallen wint vonkeroderen het pleit.
Ook in bepaalde slijptoepassingen kan zinkvonken een beter alternatief zijn qua kostprijs. De traagheid van vonkeroderen is dus een relatief begrip: het gaat om de toepassing en de kostprijs daarvan. De bewerking kost veel tijd, maar gebeurt vrijwel volledig onbemand en zelfs geautomatiseerd als het om zinkvonken gaat. Bij draadvonken verlengen de machinebouwers de autonomie door draadspoelen met een capaciteit tot 25 kg aan te bieden, of een dubbele spoel die automatisch wisselt.

Nadeel opheffen met lasertechnologie
Een belangrijk nadeel van het vonkeroderen is dan weer het ontstaan van de zogenaamde Heat Affected Zone: de witte laag aan de rand van het werkstuk, variërend van enkele tot honderden microns (bij het ruwen). De warmte leidt tot een verandering van de eigenschappen van de buitenste laag van het werkstuk. Hier kunnen microscheuren onder het oppervlak ontstaan en spanningen kunnen bijvoorbeeld de levensduur van een gereedschap, gemaakt met EDM, negatief beïnvloeden.
Met moderne, ultrakorte pulslasers kan men deze warmtebeïnvloede zone verwijderen, doordat de zeer korte pulsduur niet tot nieuwe warmte-inbreng leidt. Recente onderzoeken aan o.a. Zwitserse universiteiten laten zien dat de levensduur van bv. spuitgietgereedschappen verlengd wordt door de zogenaamde cold ablation-nabewerkingsstap, vergeleken met gevonkte gereedschappen zonder deze nabewerking. Met de lasertechnologie kan men de warmtebeïnvloede zone lokaal verwijderen, waar nodig.
Concurrentie voor EDM?Hoe staat het met andere technieken, zoals ECM en PECM ((Precision) Elektrochemical Machining)? Is dit concurrentie voor het vonkeroderen? Tien jaar geleden was er nog sprake van dat ECM binnen tien tot vijftien jaar concurrerend zou kunnen worden met vonkeroderen. Het voordeel dat toen werd genoemd, was dat de gereedschappen amper of niet slijten. Het nadeel: het is nog geen standaardtechnologie. Voor ECM geldt dat nog steeds. PECM daarentegen begint meer voeten aan de grond te krijgen in de Benelux.
PECM is een koud proces, zonder warmte-inbreng in het werkstuk. Dit is een belangrijk voordeel in toepassingen waar de Heat Affected Zone ongewenst is. De Z-as, met daarop de elektrode, beweegt elke keer tot op 10 µm van het werkstuk en haalt met de stroompuls op dat moment zo’n 30 nm materiaal weg. Direct hierna trekt de elektrode zich terug (het verschil met gewoon ECM) en wordt die gespoeld met elektrolyt. Doordat het gereedschap het werkstuk absoluut niet raakt, treedt er geen slijtage op. De opgeloste metaalionen krijgen niet de kans zich te hechten aan het gereedschap, doordat ze direct worden weggespoeld door het elektrolyt.
De oppervlakteruwheid is doorgaans beter dan bij vonkerosie; 2 tot 4 µm Ra voor PECM tegenover 6 tot 8 voor EDM.
Voor veel hightechtoepassingen is het een voordeel dat de technologie absoluut braamvrije producten oplevert. Ontbramen is in sectoren zoals de halfgeleider- en medische industrie een van de bottlenecks, omdat het vaak een manuele handeling is die volgt op een geautomatiseerd proces. Daar wint PECM het dus van andere processen. De technologie is wel het meest geschikt voor serieproductie, vanwege de investering in het gereedschap.
Aandrijving bepaalt nauwkeurigheid
De nauwkeurigheid van een draad- of zinkvonkmachine komt voor een belangrijk deel uit de aandrijving. Wrijvingsloze aandrijvingen zijn het uitgangspunt, maar daarbinnen kiezen machinebouwers hun eigen oplossingen.
Eigenlijk ziet men altijd lineaire motoren. Mitsubishi Electric past een eigen, gepatenteerd systeem toe: Tubular direct drive; een variant op de lineaire aandrijving. Het verschil is dat het Tubular direct drive-concept geen enkele weerstand voelt bij de overgang van de noord- naar de zuidpool.
De besturing is nog altijd de aanjager van de innovatie
Als een stator en robot langzaam draaien, kan hierdoor bij het wisselen van de richting een trilling ontstaan die zichtbaar is in het oppervlak van het werkstuk. Mitsubishi lost dit op met technologie die afkomstig is uit de medische sector, zoals MRI-scanners. De machinebouwer gebruikt niet-ijzerhoudende schijfmagneten met een buis erom heen (vandaar de naam Tubular). Hierover verplaatst zich de motor. Over de volledige lengte levert dit een positioneernauwkeurigheid van 2 µm.
De Japanse fabrikant Sodick past in de nauwkeurigste draadvonkmachines een nieuw type geleidingen toe. Hierin zijn de kogeltjes vervangen door kleine tonnetjes, zodat er geen puntbelasting meer bestaat. Het grotere oppervlak verhoogt de stijfheid van de geleiding. Hierdoor – en door een aantal andere verbeteringen – verdubbelt de pitchnauwkeurigheid van de machine, vergeleken met de standaard Sodick-draadvonkmachine.
Technologie wordt toegankelijker
Lange tijd was vonkeroderen een nichetechnologie die veel specifieke kennis van de operator vergde. Zo gangbaar als CNC-frezen en -draaien zijn draad- en zinkvonken nog niet, maar de machinebouwers hebben er de jongste tien jaar veel aan gedaan om de technologie toegankelijker te maken.
De rode draad hierin zijn digitalisering en het toenemend gebruik van Machine Learning-algoritmen. Hierdoor kunnen fabrikanten materialendatabases integreren, waarin de operator al veel vooraf gevalideerde instellingen terugvindt. Ook de parameters voor hoogwaardige materialen zoals titanium en bepaalde koperlegeringen zijn via de database met enkele klikken beschikbaar bij het programmeren.
Kunstmatige Intelligentie
Kunstmatige Intelligentie, beginnend met Machine Learning, is de volgende stap. De nieuwe besturingen 'leren' van elke bewerking en gebruiken deze data voor de volgende. Hierdoor wordt de bediening van een EDM-machine gemakkelijker en slagen de fabrikanten erin om de instapdrempel te verlagen. De nieuwste besturingen controleren voortdurend wat er in het proces gebeurt, detecteren in een vroeg stadium eventuele problemen en passen de procesparameters automatisch aan.
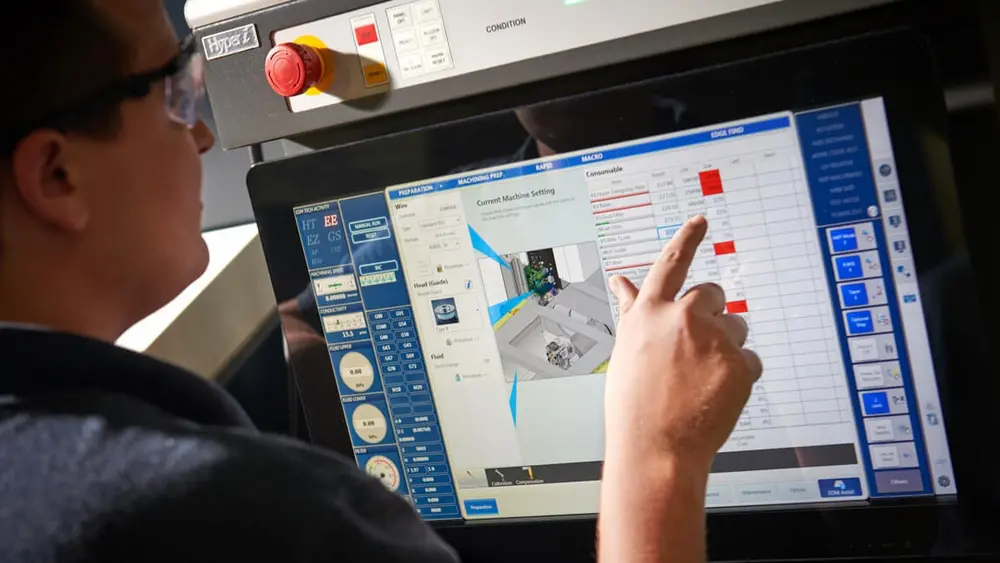
Daarnaast lukt het de machinebouwers om met de algoritmen de slijtage van de elektrode te verminderen. De nieuwste generatoren reageren veel sneller op wat er in het proces gebeurt, aangestuurd door de informatie die de besturing uit de data haalt.
Luchtvaartindustrie
Een van de nieuwe ontwikkelingen om de snelheid van de draadvonkmachines op te voeren, is de twin wire-technologie. GF Machining Solutions biedt dit aan op de nieuwe CUT X-serie: naast een spoel met dikkere draad zit er ook een spoel met dunne draad op de machine.
Afhankelijk van de bewerking – veel materiaal weghalen in korte tijd of langzamer maar wel heel nauwkeurig vonken – wordt in het programma een van beide draadsoorten geselecteerd. Men voorkomt zo dat de operator de draad moet wisselen als er van ruwen wordt overgestapt op finishen.
Deze technologie kan eveneens gebruikt worden om de autonomie van het systeem te verlengen door met twee identieke draden te werken. Doordat de machine automatisch wisselt als één spoel leeg is, verdubbelt de autonomie.
Roterende draad
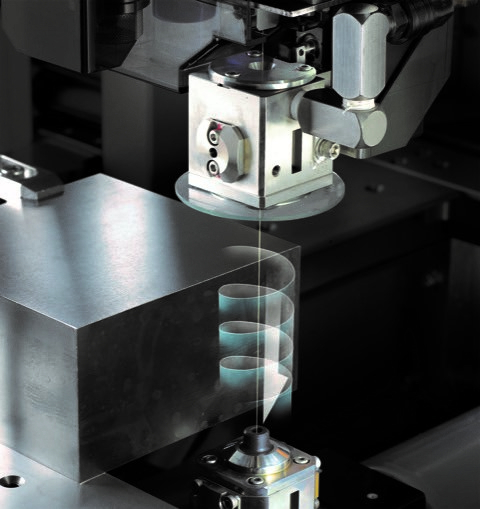
Ook na jaren is innovatie van het draadvonkproces nog steeds mogelijk. De besturing is nog altijd de aanjager van de innovatie.
Tot nog toe wordt de draad in een draadvonkmachine aangestuurd door spanning en loopsnelheid, terwijl ze worden ingeperkt door een matrijs in de geleiding. Door een rotatiemechanisme aan de draad toe te voegen, verhoogt Sodick met de iGroove-functie zowel de geometrische nauwkeurigheid als de oppervlaktekwaliteit.
De draad roteert om z’n eigen as tijdens de beweging omlaag. Hierdoor wordt het werkstuk altijd met het nieuwe, nog niet gebruikte oppervlak van de draad bewerkt, wat voor de betere kwaliteit zorgt, naast een lager draadverbruik. Ook neemt het breukrisico af, omdat het oppervlak waarmee de draad het werkstuk bewerkt door de rotatie niet op één plaats slijt, maar heel gelijkmatig. De noodzaak om te compenseren voor een taps toelopende wand vervalt.