Hogere productiviteit in de meetkamer
dankzij nieuwe technologie
De meetkamer is weliswaar niet het hart van een modern productiebedrijf, maar wel een onmisbaar onderdeel. De machines stoppen immers als vanuit de meetkamer niet het sein op groen wordt gezet. Met de alsmaar hogere eisen en toenemende vraag naar kwaliteitsrapporten, neemt de druk op de meetkamer toe. Hoe kunnen bedrijven de doorlooptijden in de meetkamer verkorten?
verlaging druk meetkamers
Méér meten op de machine; méér data gebruiken om het productieproces én de machines bij te sturen zodat de producten binnen de specificaties vallen: dat is de vaak gehoorde oplossing als het erom gaat de druk op de meetkamers te verlagen. Meten in de productie kan echter nog niet de meetkamer vervangen als er harde specificaties gelden, aan te tonen met meetrapporten uit de meetkamer.
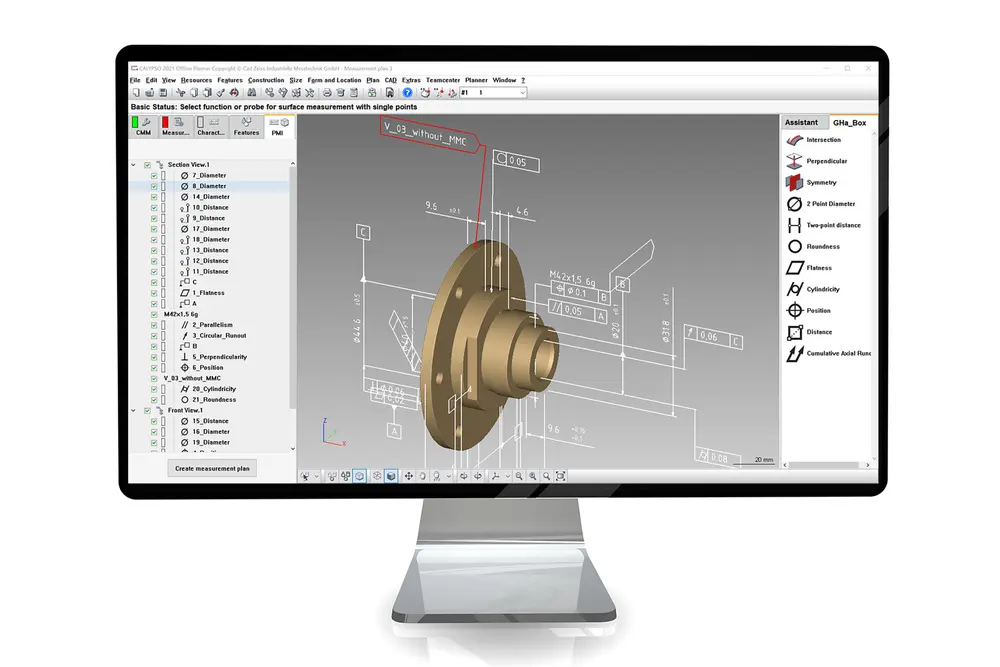
Met de nieuwe Zeiss Calypso-software wordt het meetproces versneld. Zeiss heeft onder andere de algoritmen die de data verwerken van het meten van 3D-vlakken aangepast, waardoor de berekening 20 keer sneller gaat dan met de vorige softwareversie. Ook worden de bewegingen van het optische meetelement geoptimaliseerd.
Foto: Zeiss
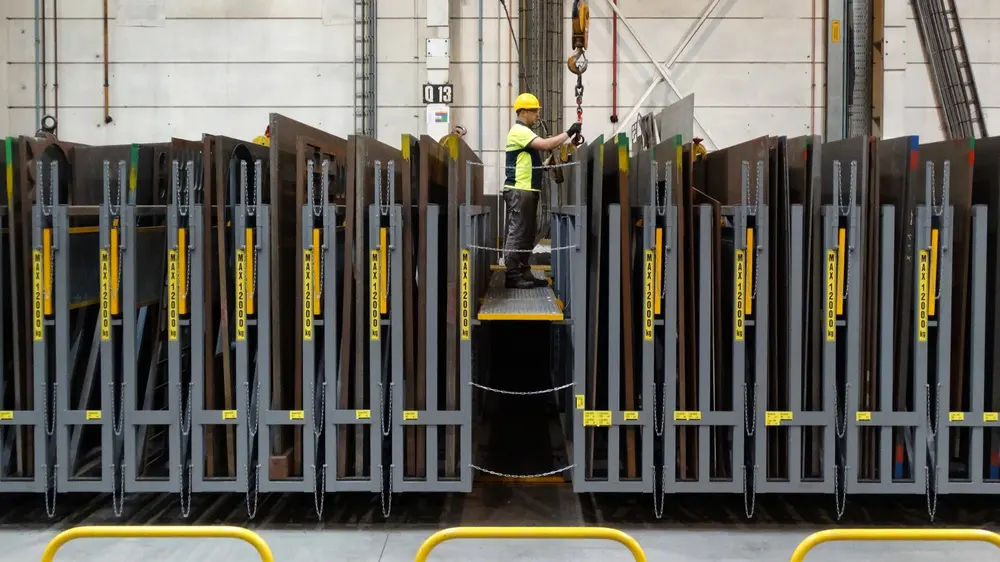
5-assige meetkoppen
De Coördinaten Meetmachine (CMM) blijft hierin een sleutelrol vervullen. Maar deze CMM kan wel met nieuwe technieken vaak sneller meten, waardoor producten eerder kunnen worden vrijgegeven voor de productie. Vanaf het moment dat niet enkel 2D meetdata nodig zijn maar ook 3D, is een 5-assige meetkop een vereiste.
Bij deze technologie zijn er twee draaiassen in de meetkop verwerkt. Hierdoor kan de meettaster de geometrie van het product beter volgen én met een hogere snelheid dan het geval is bij meetsystemen die indexeren of een vaste meettaster hebben. Omdat er met een constante snelheid langs één vector wordt bewogen, kunnen de algoritmen die de beweging berekenen, deze optimaliseren.
Er wordt ook tijd gewonnen doordat complexe producten minder vaak omgespannen hoeven te worden om een deel ervan te meten, precies zoals ook voor een 5-assig bewerkingscentrum geldt. Dit betekent onder andere dat de CMM langere tijd onbemand kan werken.
Naast de hogere snelheid is met name de hogere kwaliteit een belangrijk voordeel van een 5-assige meetkop. De kans op dynamische meetfouten is geringer, want alleen de lichte meetkop beweegt en niet de totale, zwaardere opbouw van de CMM. Dynamische meetfouten ontstaan door minimale vervormingen van de structuur van een meetmachine als gevolg van de bewegingen.
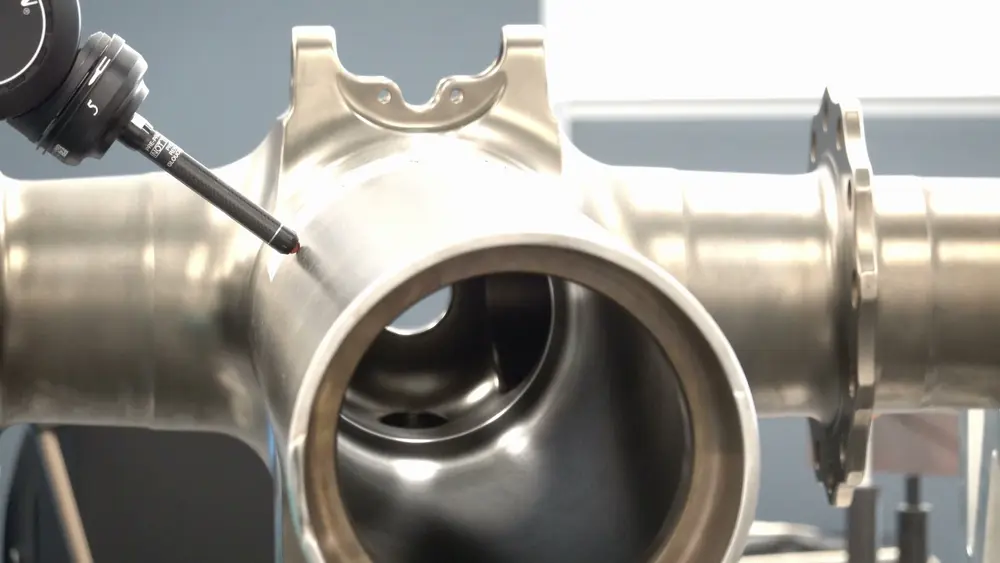
Scannende taster
Deze 5-assige meettechnologie is er niet alleen voor tactiele tasters maar net zo goed voor de scannende taster. Dit laatste type taster bestaat nog niet zo heel erg lang en begint eigenlijk pas sinds kort z’n weg te vinden naar de machinefabrieken die veel complexe precisie onderdelen produceren. Dit heeft veel te maken met de investeringskosten die hoger zijn.
Daar staan echter verschillende voordelen tegenover. Een scannende meettaster bevat een sensor met een eigen systeem voor het meten van de verplaatsing. Als men de taster langs een contour beweegt, meet het systeem elke punt zolang er contact met het werkstuk is. Dit levert een veel nauwkeuriger beeld op van bijvoorbeeld de nauwkeurigheid van een gat dan wanneer een tactiele taster een handvol punten meet en de software op basis van deze meetpunten de rondheid berekent. Deze scannende tasters lenen zich met name voor complexe producten, zoals turbineschoepen.
Een oplossing om tijd te winnen is het gebruik van multisensorcoördinatenmeetmachines
Een ander verschil met de tactiele taster is dat deze laatste vaak relatief grote afmetingen hebben omdat de stylus zo stijf mogelijk moet zijn. Omdat de stylusschacht bij een scannende taster enkel gebruikt wordt om de meetkogel te positioneren, kan de schacht kort blijven. Het meetresultaat van een scannende tasterkop kan men omzetten naar een model dat weer ingelezen kan worden in het CAD-systeem. Dat maakt het bijvoorbeeld makkelijker om afwijkingen zichtbaar te maken en kan voordelen leveren bij het programmeren van de laatste bewerkingsstap.
De scannende taster moet overigens niet verwisseld worden met optisch meten: dit is een contactloze meting, hetzij met een lijnscanner of een 3D-scanner.
Voor kortere doorlooptijden van meetcycli op CMM’s levert Hexagon MI de HP-L-10.01, een lasersensor voor het contactloos meten van werkstukoppervlakken. De sensor meet tot 600.000 punten per seconde. De laserscanner is zeven keer sneller dan de voorgaande generatie. De nauwkeurigheid van de contactloze meting is volgens de fabrikant vergelijkbaar met die van een taster.
Multisensortechnologie
Bij een doorsnee CMM worden meerdere meetsystemen gebruikt, tactiel en optisch. Ze hebben allemaal hun eigen sterke en zwakkere kanten. Afhankelijk van de metingen die gedaan moeten worden, zal de programmeur de verschillende opties kiezen en opnemen in het meetprogramma. Dit kost extra tijd, niet alleen omdat tijdens het meetproces telkens gewisseld moet worden maar ook omdat er meerdere keren praktisch dezelfde beweging gemaakt zal worden.
Daarnaast gaat de ene meting snel, de andere langzamer. Een oplossing om tijd te winnen is het gebruik van multisensorcoördinatenmeetmachines. Deze combineren optische met tactiele metingen, eventueel zelfs met een 3D-scanner. Daarmee kan men vrijwel alle werkstukken meten en alle metingen doen, dus zonder dat het werkstuk omgespannen hoeft te worden. Bij sommige systemen kiest de software automatisch de snelste meetsensor. Een ander voorbeeld van tijdwinst is het gebruik van één meetinstrument om zowel de 2D-geometrie te meten als de oppervlakteruwheid.
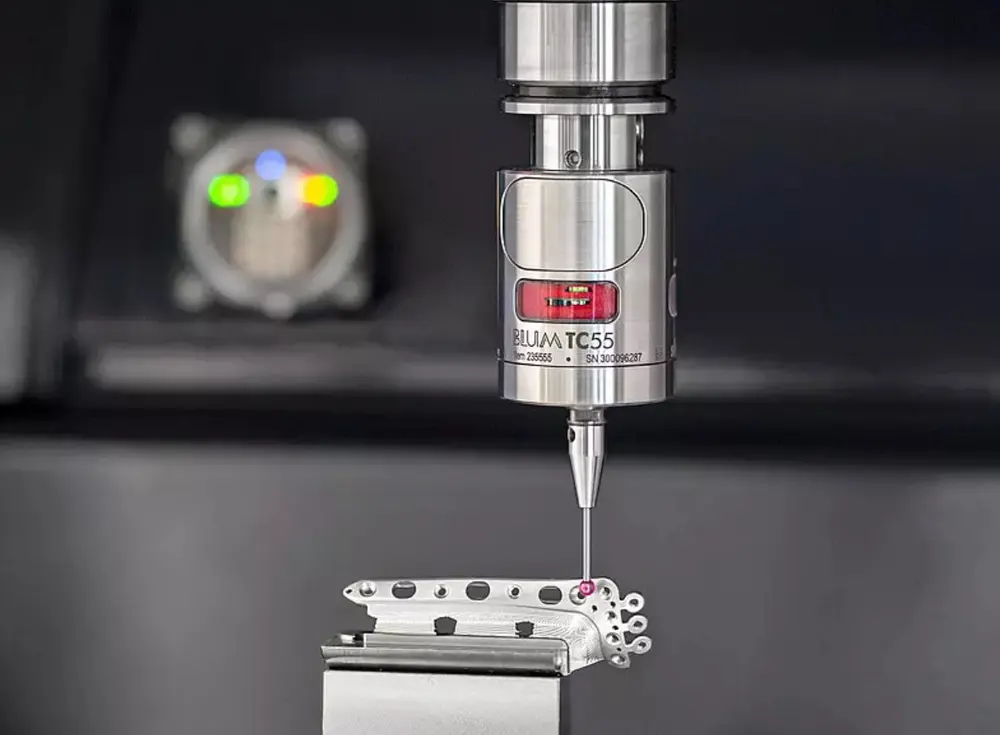
Blum-Novotest heeft op de EMO 2021 de nieuwe TC55-taster geïntroduceerd. Het signaal wordt niet gegenereerd door een mechanisch contact maar met een opto-elektronisch element. Hierdoor is de taster slijtagevrij en kan men veel sneller meten. De meetsnelheid kan oplopen tot 2.000 mm/min.
Foto: Blum-Novotest
Optische meetsystemen
Optische meetsystemen zijn hier eveneens toe in staat. De technologie achter de optische meetinstrumenten is het laatste decennium sterk doorontwikkeld zodat er nu veel meer metingen kunnen worden gedaan. Door het licht anders op het product te projecteren en anders te meten, kan men met een optisch systeem tegenwoordig zelfs een flank van meer dan 90 graden snel en goed meten. Hierdoor kan men boringen, schuine vlakken, eigenlijk alle onderdelen met een verticaal oppervlak, goed meten, zowel om de lengte, de contour en de oppervlakteruwheid in kaart te brengen. Het voordeel hiervan tegenover een tactiele meting is dat vanuit één richting hele delen van een product gemeten kunnen worden. Anders positioneren in de klem is niet nodig.
Sommige optische meetsystemen herkennen een product en zoeken dan automatisch het juiste meetprogramma hierbij
Optische metingen leveren daarnaast veel meer meetdata op dan puntmetingen. Dit kan met vene tactiele meting nooit worden bereikt: het volledig oppervlak wordt gemeten en de data kunnen worden gebruikt om een nieuw 3D-model te genereren, Bij de scanners worden naast laserstralen (zeer snel maar minder nauwkeurig) ook gestructureerd wit of blauw licht gebruikt. Blauw licht is minder gevoelig voor invloed van het omgevingslicht dan de witlichtscanners. De blauwlichtscanners hebben een hogere resolutie.
Een probleem bij scannen kan wel ontstaan als men een glanzend oppervlak wil meten omdat er dan te veel reflectie ontstaat. Met spray is dit probleem op te lossen. Ook zwarte oppervlakken laten zich moeilijker scannen. Scannen is minder nauwkeurig dan een CMM, maar de resultaten zijn wel veel sneller beschikbaar.
Sommige optische meetsystemen herkennen een product en zoeken dan automatisch het juiste meetprogramma hierbij. Daarmee wordt de inzet van een cobot in de meetkamer denkbaar. Tegenover de voordelen van optische meetsensoren staat echter het nadeel dat ze vandaag de dag nog niet de nauwkeurigheid halen die men met een tactiele meting haalt.
Een CMM met een nauwkeurige taster meet op 1 µm nauwkeurig; optische meetsystemen zijn goed als de nauwkeurigheid binnen een honderdste mm moet vallen. Een vuistregel is dat de nauwkeurigheid van het meetsysteem een factor vijf tot 10 keer zo nauwkeurig moet zijn als de meetnauwkeurigheid die nodig is.
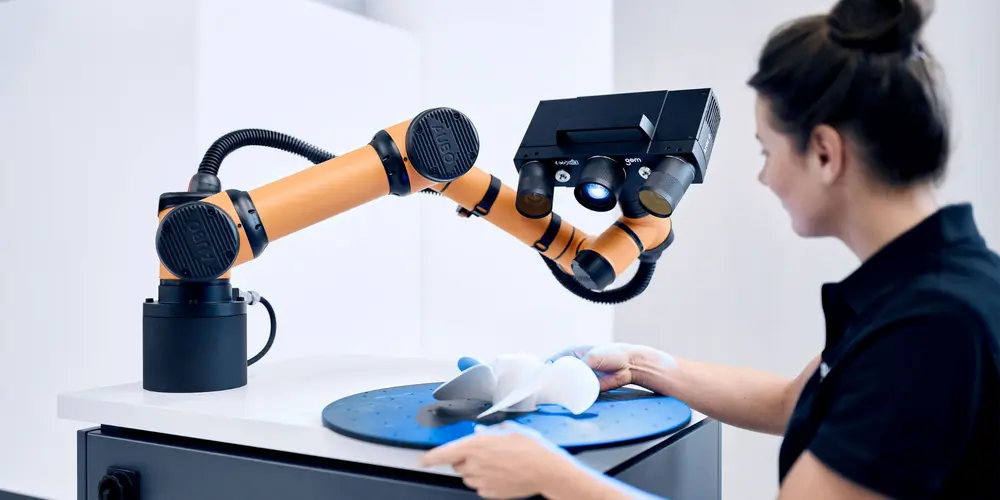
Toekomst: slim meten
Aan de productiekant is de digitalisering serieus op gang gekomen. Hoe kan de meetkamer aansluiten op deze trend? Dat gaat voor een deel gebeuren doordat meetdata steeds vaker direct teruggevoerd worden naar de software waarmee machines worden geprogrammeerd of zelfs naar de besturing van de machines. De communicatie van de meetkamer naar de CAM-programmeur verloopt al digitaal, daarvoor zijn de tools al beschikbaar. Dankzij de inzet van algoritmen kunnen de probleemgebieden waar de programmeur naar moet kijken, direct zichtbaar worden gemaakt.
De volgende stap zal zijn dat deze data quasi automatisch verwerkt worden om het programma voor de volgende batch producten aan te passen. Zeker wanneer komende jaren het gebruik van Model Based Definition toeneemt, kunnen op dit vlak grote stappen worden gezet om de kwaliteit van de productie te verbeteren en de doorlooptijd in de hele fabriek te verkorten. De meetkamer blijft echter een centrale rol spelen in de kwaliteitscontrole.
De CMM in de productiehal
Een manier om de druk op de meetkamer te verlagen is meer naast de machine te meten, alhoewel dit altijd de beperking heeft dat dit dan niet in ene geconditioneerde ruimte gebeurt. Meerdere fabrikanten van CMM’s hebben hier speciale meetmachines voor ontwikkeld. Het Zwitserse Trimos 3D heeft zelfs een draagbare CMM ontwikkeld, die slechts 13,5 kg weegt. Deze is speciaal voor in de productie-omgeving ontwikkeld, zodat men de werkstukken niet langer naar de meetkamer hoeft te brengen en naast de machine kan controleren. De C-Line CMM wordt geleverd als 4-assig model, kan zowel manueel worden bediend als via CNC en is compatibel met meerdere meetpakketten zoals Verisurf, CMM Manager en Polyworks.
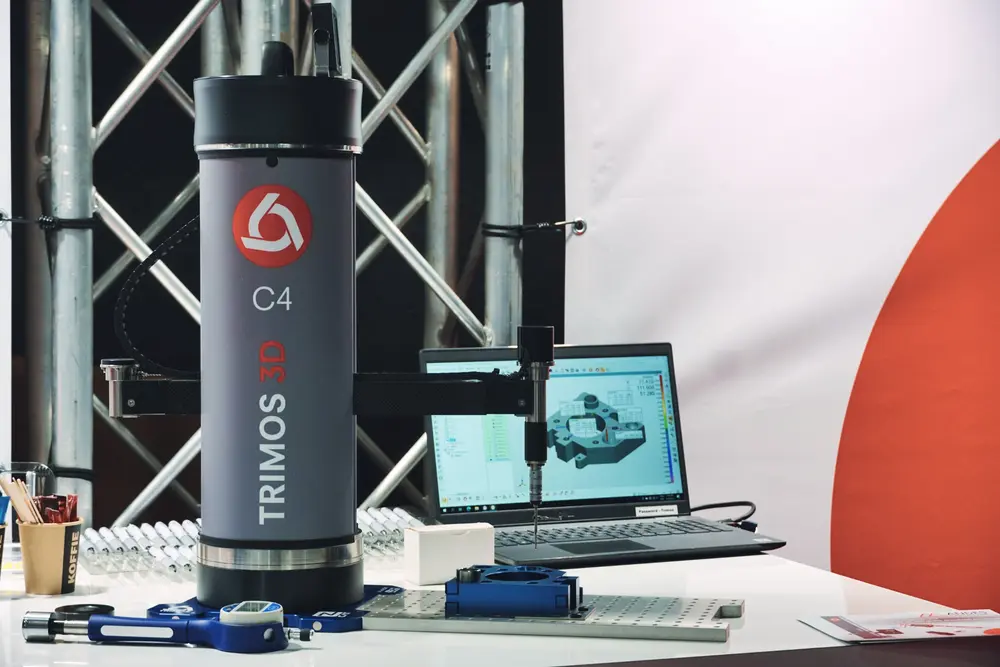