Waterstraalsnijden: een niche met toekomst
Bundel heel wat voordelen in één techniek
Waterstraalsnijden – na knippen, zagen en ponsen/stansen de vierde koude snijtechniek – maakt het mogelijk om uiteenlopende materialen te snijden zonder dat daarbij sprake is van vervorming, structuur- of kleurveranderingen. De jongste jaren is er veel onderzoek gedaan naar de verdere mogelijkheden van de techniek, wat heeft geleid tot een aanzienlijke prestatieverbetering en een significante toename van de snijsnelheden. Wat kan waterstraalsnijden voor uw productie betekenen?
KOUDE SNIJTECHNIEK
Waterstraalsnijden maakt het mogelijk materialen te snijden zonder dat daarbij vervorming, structuur- of kleurveranderingen optreden, aangezien er geen sprake is van een heat-affected zone (HAZ). Hierdoor is er ook geen nabewerking nodig. Zo'n HAZ kan ook schade veroorzaken aan snijplaatjes en instrumenten, waardoor extra locaties nodig zijn in de 'tool belt'. Deze spaart u dus uit bij het gebruik van waterstraalsnijden.
Het materiaal bepaalt of dit kan met of zonder snijzand (abrasief), het feitelijke 'snijelement'. Het water laat de korreltjes gericht en met de juiste snelheid richting snijpunt bewegen. Het snijproces zelf vindt plaats met behulp van een spuitkop waarop robijn of (kunst)diamant − 'orifice' geheten − is aangebracht. Het mengsel van water en abrasief raakt het metaal met snelheden tot wel 700 m/s oftewel 2.520 km/u (de snelheid van het geluid bedraagt 194 km/u). Daarbij wordt het principe van de 'vliegende snijkop' gehanteerd: de gewenste werkstukcontour wordt gevolgd zonder dat de snijtafel zelf beweegt.
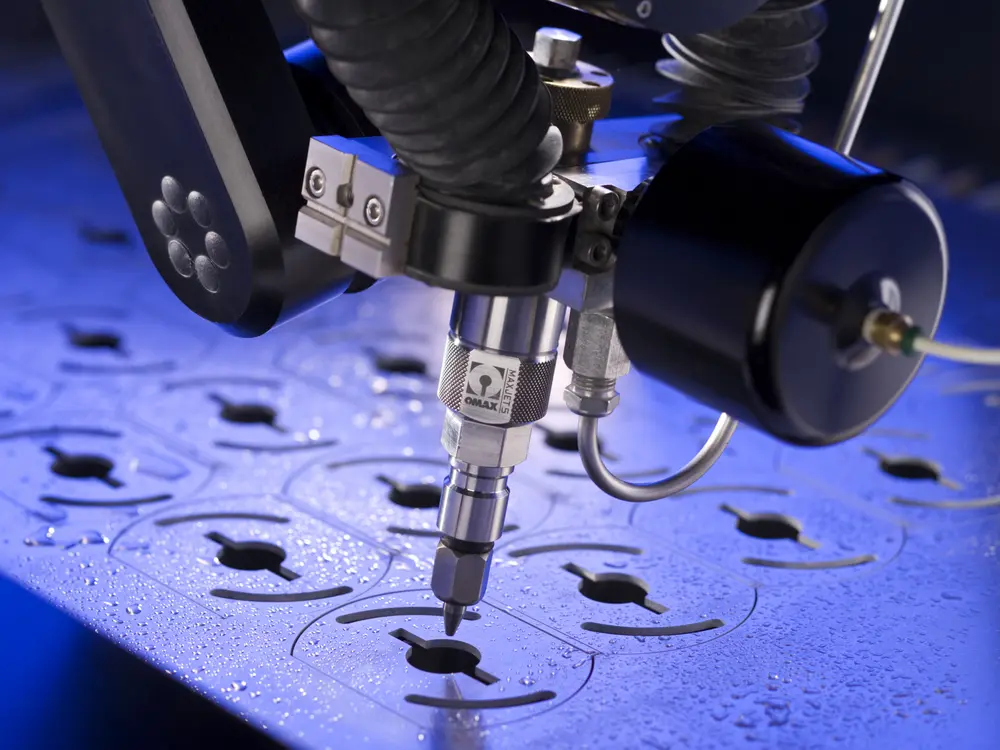
MET OF ZONDER ABRASIEF
Waterstraalsnijden kan dus met of zonder abrasief toegepast worden. Met een abrasief kan de waterstraal verschillende
soorten metaal, hout, steen, keramiek, glas en composieten snijden. Zonder abrasief zijn dat onder meer kunststoffen,
schuim en rubber. De 'koude' waterstraalsnede is bovendien de enige snijtechnologie waarmee het snijden van kunststof of composiet mogelijk is. Doordat de waterstraal relatief lang recht blijft, is het ook mogelijk om bijvoorbeeld meerdere dunne kunststofplaten tegelijk te snijden.
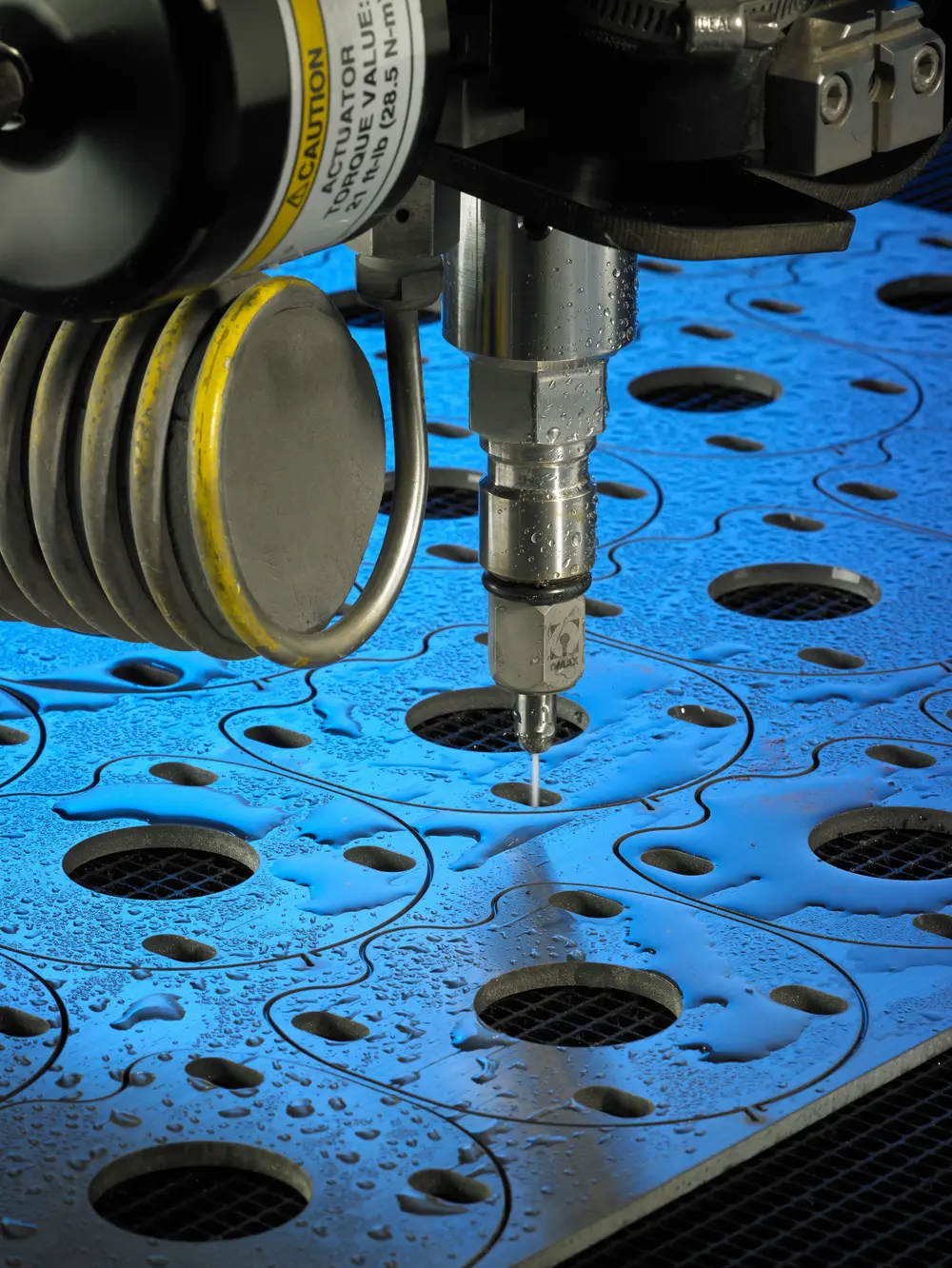
Hoe brosser het materiaal, hoe meer abrasief er nodig is om een optimale snede te maken. Het snijzand wordt op
het laatst mogelijke moment toegevoegd, om slijtage aan de machine te beperken. Dat gebeurt in het vacuüm dat ontstaat in de mengkamer onder de spuitkamer. Als er meer watervolume door de mengkamer gaat, wordt de onderdruk groter en wordt er meer abrasief aangezogen. Dit resulteert in een hogere snijsnelheid. De mix van water en zand komt in de focusbuis terecht.
Bij de keuze tussen robijn of diamant wordt het verschil bepaald door de standtijd. Bij een robijn (kostprijs 40 euro) ligt die rond de 40 uren; bij een diamant (kostprijs 400 euro) is dat ongeveer 500 uren. Veel hangt ook af van de kwaliteit van het gebruikte water. Bevat dit veel onzuiverheden, dan kan dit invloed hebben op de levensduur. In België en Nederland is dit echter geen probleem.
VOOR- EN NADELEN
Naast het feit dat het plaatmateriaal niet thermisch beïnvloed wordt en de snedekwaliteit hoog en constant is, maakt ook de geringe waterstraaldiameter complexe snijvormen mogelijk. Doordat er geen direct contact is tussen het werkstuk en de snijkop is er geen risico op beschadigingen. Bovendien is waterstraalsnijden een niet-chemisch proces en dus vrij van giftige dampen.
Bij waterstraalsnijden speelt software een steeds grotere rol. Intelligente software bepaalt zelf hoelang de inloop, uitloop en de cornerpassing moet zijn. Afhankelijk van het soort materiaal en de dikte ervan levert dat een aanzienlijke tijdwinst op tot wel 45%. Daarnaast brengt waterstraalsnijden nagenoeg geen bramen teweeg, waardoor de nabewerkingskost minimaal is. Wel moet je rekening houden met het "afval" van water en schuurmiddelen dat opgeruimd dient te worden.
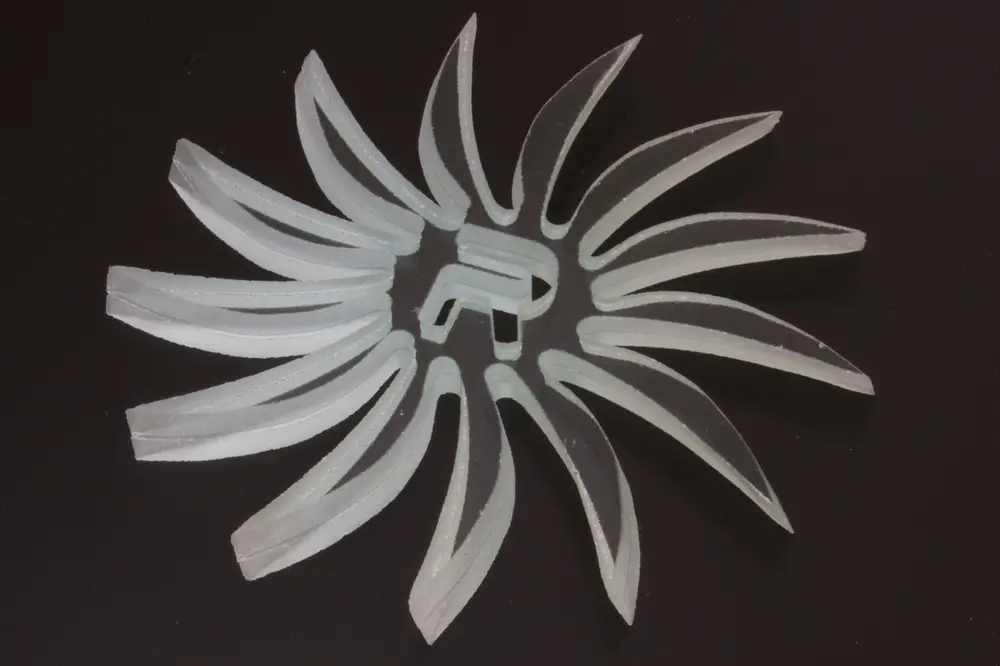
DE MACHINE ZELF
Sommige fabrikanten bieden hun waterstraalsnijmachine aan als modulair concept. Dat maakt het mogelijk om klein te beginnen en naarmate de tijd vordert nog andere componenten toe te voegen. Omdat de hogedrukpomp een druk van
bijna 4.000 bar moet leveren, kan die weleens een lawaaierige factor zijn bij het waterstraalsnijden. Veel hangt af van het formaat van de pomp. Fabrikanten zoeken ook voortdurend naar oplossingen om dergelijke problemen te minimaliseren.
Dé kost van waterstraalsnijden valt moeilijk te bepalen. Er zijn heel wat factoren waarvan de uiteindelijke kostprijs van de bewerking afhankelijk is. Het abrasief is een van de duurste componenten binnen het proces. Doordat het aan een grote snelheid in de waterstraal gebracht wordt, krijgt de nozzle het bovendien hard te verduren.
Snelheid en kwaliteit
Ten aanzien van de snijtijd bestaat er een spanningsveld tussen snelheid en kwaliteit. Een hoge snijsnelheid betekent een lagere productieprijs, maar vaak is dan wel een nabewerking nodig. Bij toenemende snijsnelheden zal de straal
gaan 'na-ijlen' – het verschijnsel waarbij de straal aan de onderzijde van het materiaal achterblijft ten opzichte van de bovenkant – en zal het zogeheten 'tapereffect' optreden: de snede blijft niet haaks.
Om het waterstraalsnijproces te versnellen, kan er gekozen worden voor een lagere snijkwaliteit, wat natuurlijk een impact heeft op het eindresultaat. Er wordt tegelijkertijd ook minder energie verbruikt, dus het is een afweging die elke gebruiker moet maken. De energiekost (en de kost van het water, van het abrasief …) is bovendien nog een factor waarvan de uiteindelijke snijkost erg afhankelijk is – zeker nu water en grondstoffen steeds duurder worden.
De laatste jaren zijn er wel stappen vooruit gezet op het vlak van snelheid. Zo is er nu de zogenaamde Jet Performance Control (JPC), waarbij er sprake is van een oneindige rotatie van de c-as. Dit systeem zal de snijkop automatisch doen kantelen om het na-ijlen te compenseren en zo het tapereffect te voorkomen. Alternatief kan er met krachtige besturingssoftware in combinatie met een 3D-snijkop TAC of speciale compensatiekoppen voor taps toelopende hoeken voor gezorgd worden dat fouten als een conische hoekfout, vertraging en variabele groottefout worden gecorrigeerd.
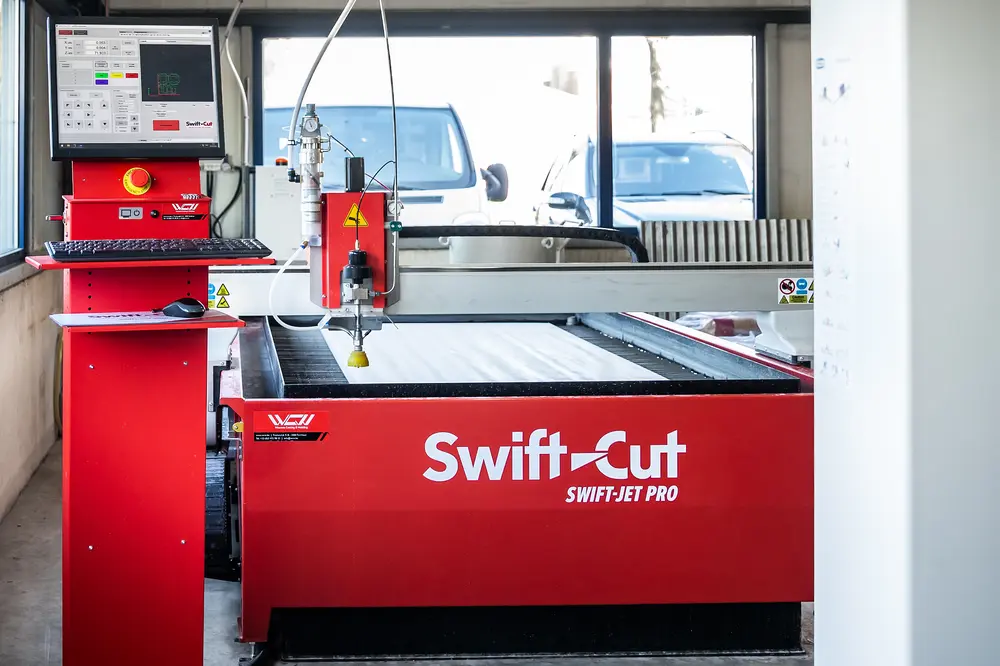
Evenwicht
De vraag is nu of er een bepaald "omslagpunt" bestaat waarop de nadelen van een hoge snijsnelheid groter worden dan de voordelen. Voor elke dikte is er een maximale snijsnelheid, afhankelijk van de gebruikte orifice/nozzle-combinatie. Hoe groter de diameter van orifice en snij-nozzle, hoe hoger de snelheid. Voor elke dikte geldt dat bij een te hoge snelheid een ruw snijoppervlak ontstaat en nabewerking vereist is.
Uiteindelijk hangt alles af van de specifieke productie en de noden van de gebruiker. De snijsnelheden zijn
instelbaar, zodat men in principe voor elke toepassing de meest geschikte snijsnelheden en nauwkeurigheid kan kiezen. Het wordt echter steeds minder noodzakelijk om de juiste parameters te kiezen: de bijhorende software doet dit immers zelf, waardoor menselijke fouten tot een minimum herleid worden.
TOEPASSINGEN
Vandaag is waterstraalsnijden nog steeds een "nichebewerkingstechnologie". Toepassingen vinden we vooral in centra voor research & development, waar de hoge flexibiliteit van een waterstraalsnijder zich perfect leent tot het maken van prototypes. Van ontwerp tot afgewerkt product hoeft bij waterstraalsnijden immers niet lang te duren. Kleine bedrijven die veel verschillende materialen moeten snijden, kunnen baat hebben bij een waterstraalsnijder als universeel instrument.
Ook in de (petro)chemiesector en in (medische) onderzoekslabo's wordt waterstraalsnijden vaak toegepast. In dergelijke sectoren wordt ook traceerbaarheid steeds belangrijker. In de nieuwste softwarepakketten kan daar gemakkelijk een nauwkeurige database voor aangelegd worden.
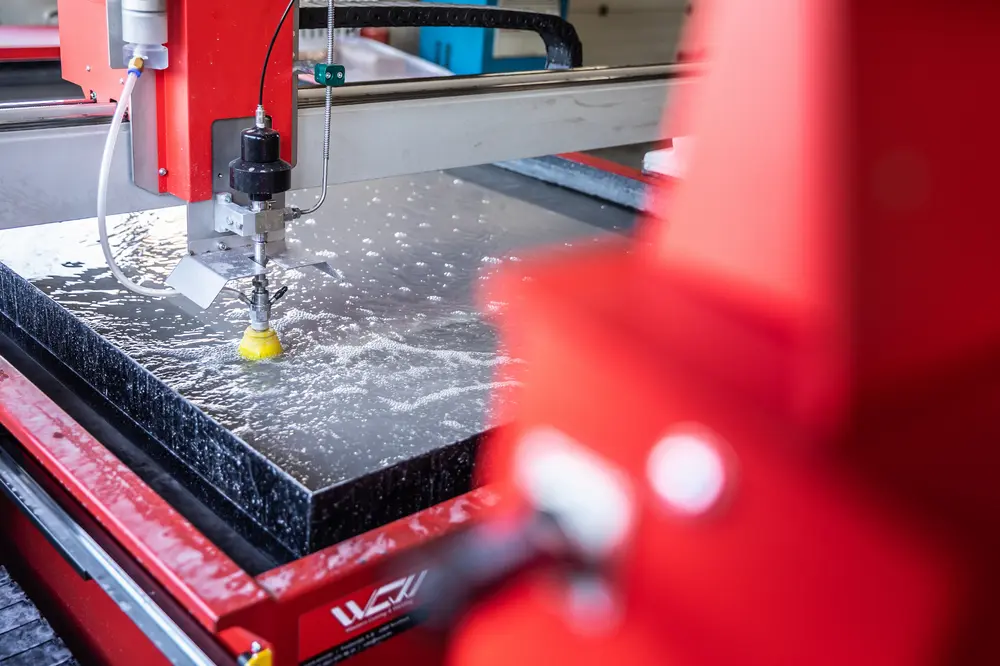
INNOVATIES
Over software gesproken: op dat vlak vonden de laatste jaren de grootste innovaties plaats als het gaat om waterstraalsnijden – niet alleen qua mogelijkheden, maar ook qua gebruiksgemak. De techniek an sich bestaat al enkele decennia en aan het basisconcept valt niet veel meer te verbeteren, aldus fabrikanten. Wel wordt elke component natuurlijk onder de loep genomen om te kijken of daar innovaties mogelijk zijn. Daardoor kunnen tegenwoordig ook "moeilijkere" plaatmaterialen gesneden worden met een waterstraal.
Innovatie zit steeds meer in het reduceren van menselijke fouten, vooral door het automatisch herkennen en instellen van de relevante parameters. Software innoveert nog steeds, vooral wat het sneller tekenen en snijden betreft. De nieuwste generatie software wordt almaar intelligenter, met volledig automatische instellingen.
NAUWKEURIGHEID
Fabrikanten proberen bijvoorbeeld de nauwkeurigheid steeds te verbeteren. Bij microwaterstraalsnijden kan tegenwoordig een nauwkeurigheid tot 2,5 µm gehaald worden. Hierbij liggen de snijsnelheden tot wel vier à vijf keer hoger dan bij andere CNC-technieken. Afhankelijk van de benodigde contour, materiaalsoort en -dikte neemt de bewerking doorgaans slechts één tot twee minuten in beslag. Dergelijke machines komen echter met een hoge aankoopprijs, waardoor ze enkel relevant zijn in geavanceerde, niche-industrie.
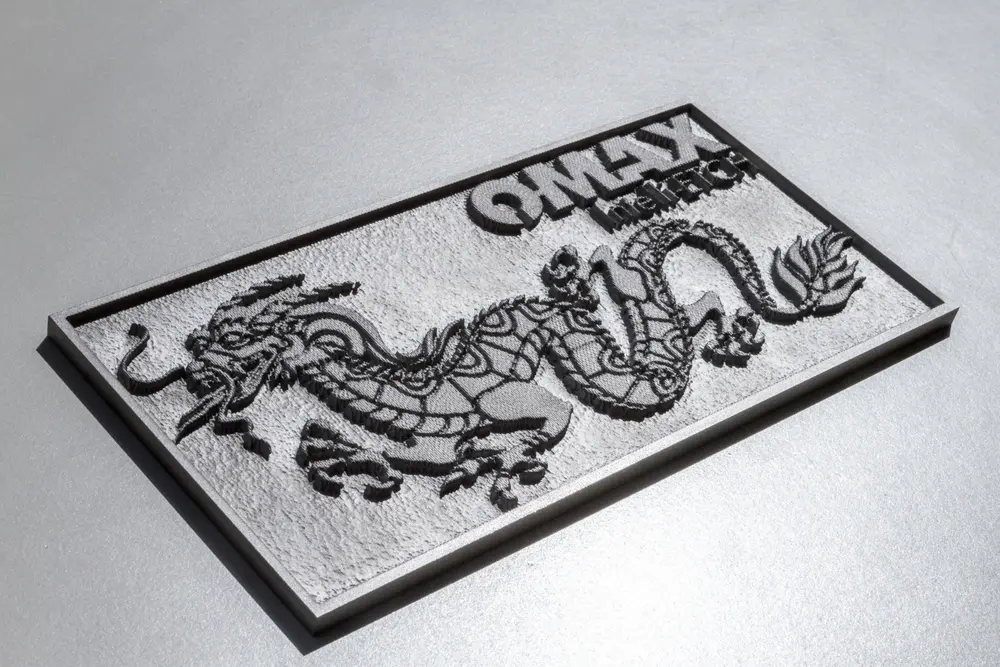
DE HOGEDRUKPOMP
Zoals eerder vermeld, besteden fabrikanten van hogedrukpompen steeds meer aandacht aan het geluidsniveau. Daarnaast wordt er ook ingezet op duurzaamheid en energiezuinigheid – in de huidige tijden allerminst onbelangrijk. Sommige pompen hebben bovendien koeling nodig, wat voor een enorm verlies aan energie zorgt. Waterstraalsnijden is niet bijzonder energiezuinig, vooral omdat het een meestal relatief traag proces is.
De laatste jaren zijn pompfabrikanten ook steeds meer gaan inzetten op de toegankelijkheid van onderdelen en op het servicegemak. Daardoor is het tegenwoordig eenvoudiger om aan zo'n pomp te sleutelen dan jaren geleden. Daarnaast gaan de pompen steeds efficiënter energie omzetten in druk.
Bovendien heeft ook bij waterstraalsnijden Industrie 4.0 zijn opwachting gemaakt. Er wordt veel meer gemonitord aan de hand van allerlei sensoren. Zo kan de gebruiker ook een melding ontvangen op zijn smartphone of via e-mail als er een actie ondernomen moet worden (bijvoorbeeld op basis van het aantal snijuren).
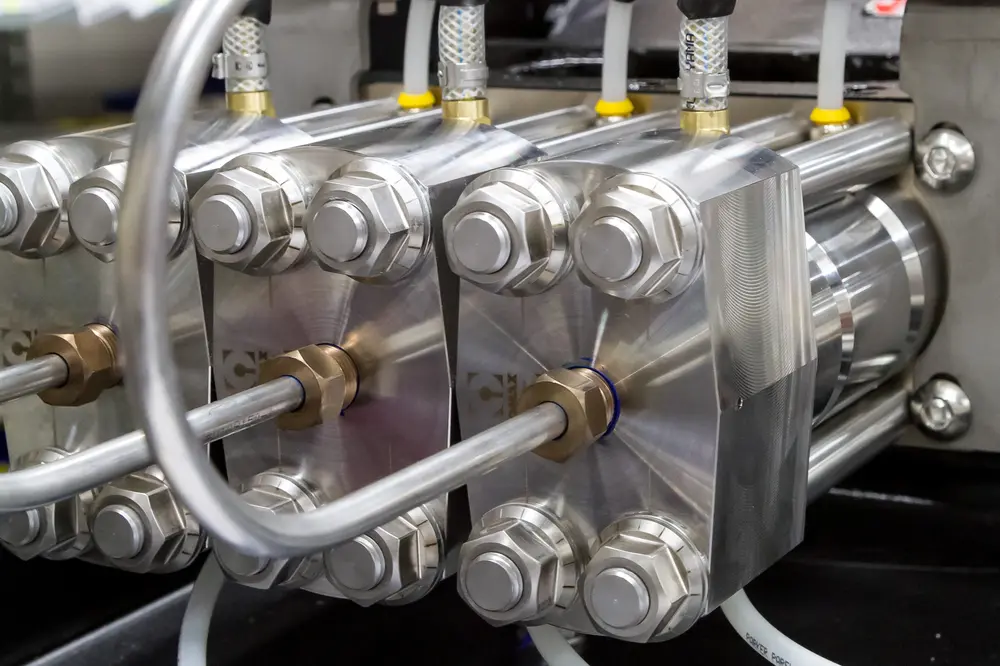
SNIJKOP
Het spuitstuk is een cruciaal onderdeel in het hogedruksysteem en om die reden is er naar de constructie daarvan al veel onderzoek gedaan. De aard van de straal wordt bepaald door de maatvoering en vorm van de spuitopening en de straalbuis, en door de mate waarin beide op één lijn liggen. Van belang daarbij zijn onder meer de diameter van de spuitopening, de plaats waar het abrasief intreedt, de hoek tussen waterstraal en intrederichting van het abrasief en de lengte van de straalbuis.
De snijkoppen worden steeds beter gedimensioneerd om nóg fijnere contouren met nóg fijner abrasief aan te kunnen en om de flow van het abrasief zo optimaal mogelijk te laten zijn, voor een kwalitatief nóg betere en gladdere snede. Tegenwoordig zijn spuitkoppen ook verkrijgbaar met synthetische diamanten die zich prijstechnisch bevinden in het middensegment. Ook is de behandeling van het inlaatwater verbeterd. Er zijn inmiddels aparte behandelingen voorhanden voor onder meer hardheid, gehalte aan silicaat, chloride en fijne deeltjes.
Met medewerking van IWE, Resato Waterjet en WCW