WATERSTRAALSNIJDEN STAAT VOOR VORMBEHOUD METAAL
Ontbreken heat affected zone voorkomt verkleuring en/of (vorm)verandering
Autogeen-, plasma- en lasersnijden waren lang dé technieken om in de metaalbewerking tot complexe(re) producten te komen. Bij deze technieken is er echter sprake van de inbreng van warmte, waardoor het te verwerken materiaal kan veranderen qua samenstelling, kleur en/of vorm. Ook zijn ze niet alle drie voor elke dikte geschikt. Waterstraalsnijden kent die beperkingen niet: de techniek is nauwkeurig, er is geen sprake van de inbreng van warmte en ook dikke materialen kunnen ermee worden gesneden. Bovendien is er ‒ afhankelijk van de gewenste tolerantie ‒ geen nabewerking nodig teneinde aan de maatvoering te voldoen.
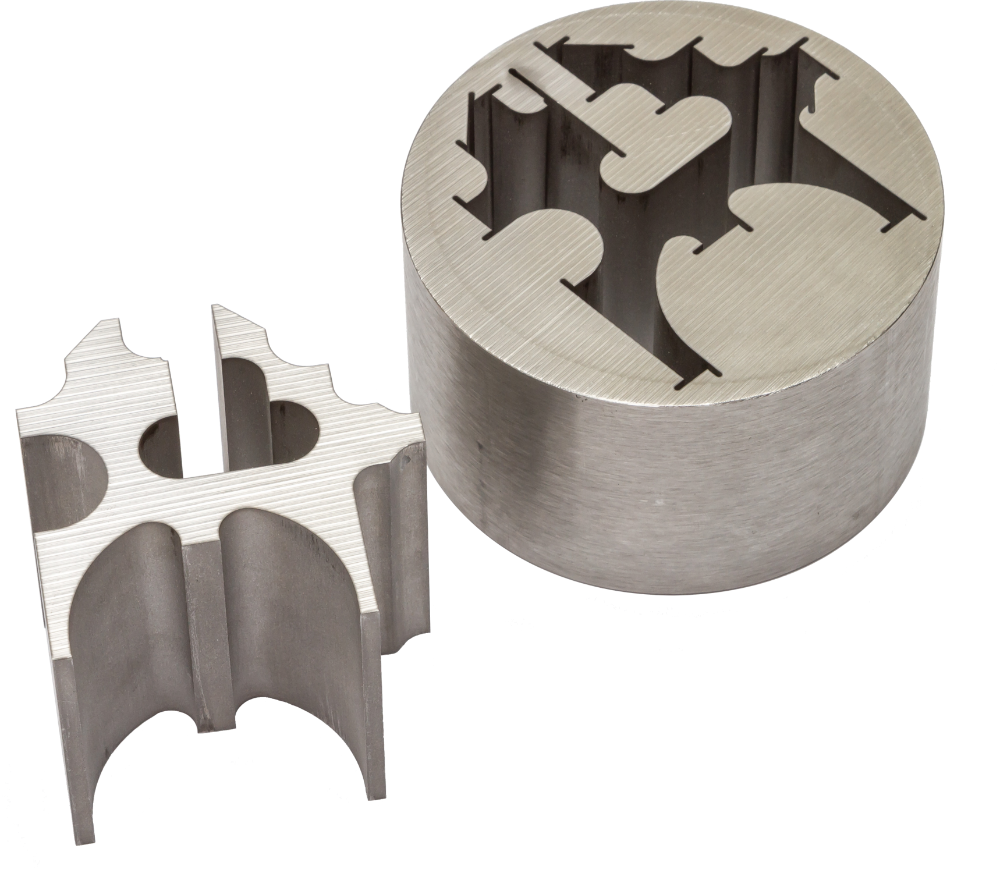
inclusief de laskanten
SNIJTECHNIEKEN
Voor het snijden van metaal zijn er diverse technieken voorhanden. Deze zijn onder te verdelen in twee categorieën: thermische snijtechnieken ‒ autogeen- of brandsnijden, plasma- en lasersnijden ‒ en de koude snijtechnieken: knippen, zagen, ponsen, stansen en waterstraalsnijden.
Bij lasersnijden wordt gebruikgemaakt van een laserstraal, een sterk gebundelde lichtbron die het materiaal laat smelten. De grote vormvrijheid en de hoge kwaliteit maken lasersnijden tot een van de meest gangbare industriële snijtechnieken.
Bij plasmasnijden wordt tussen een wolfraamelektrode en het werkstuk een elektrische boog opgewekt. Dankzij de elektrische lading wordt het aanwezige snijgas deels geïoniseerd waardoor dit overgaat in plasma (temperatuurbereik tot 30.000 ºC). Bij dergelijke temperaturen smelt het metaal en kan het zelfs deels sublimeren.
Bij autogeen- of brandsnijden wordt het materiaal rondom de snede verbrand. Het te verwijderen materiaal moet daartoe eerst tot 1.100 ºC worden (voor)verwarmd, waarna op die plek zuivere zuurstof wordt gericht. Door de reactie die dan ontstaat, vindt verbranding plaats van het metaal.
De drie thermische straalsnijtechnieken hebben als nadeel dat het materiaal kan veranderen qua samenstelling, mechanische eigenschappen, kleur en/of vorm.
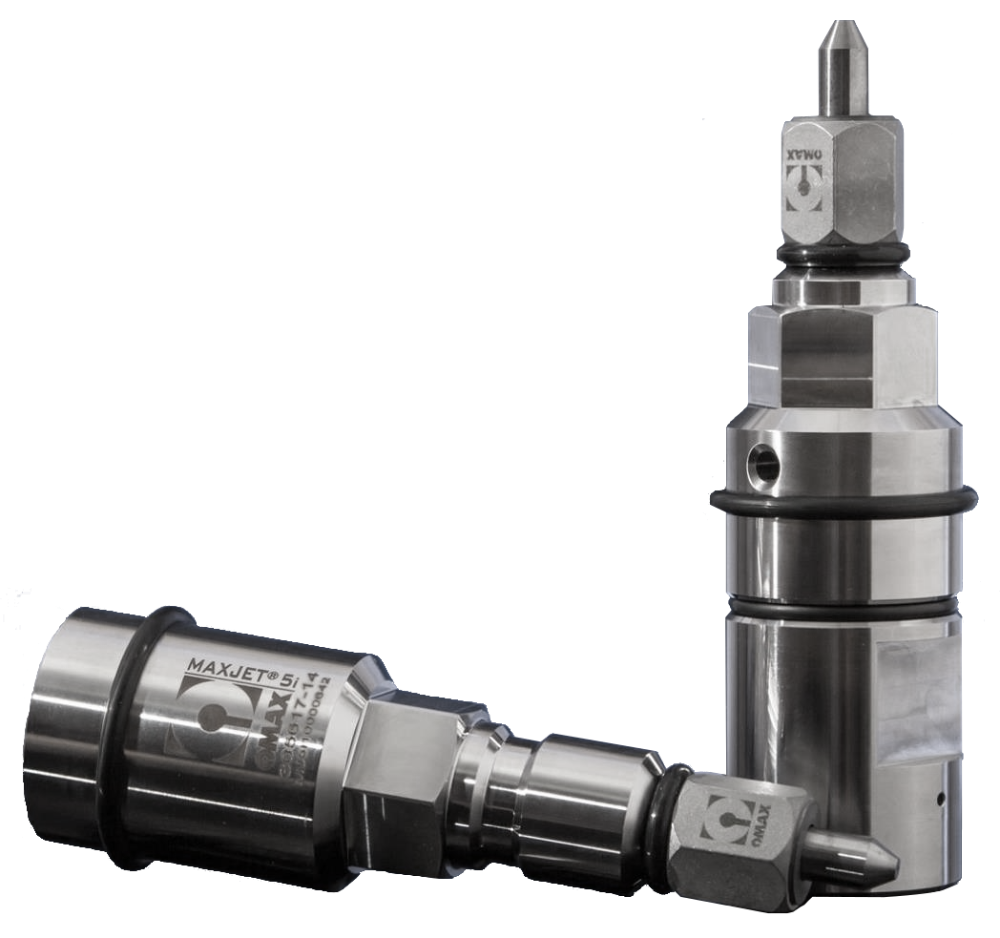
HEAT AFFECTED ZONE (HAZ)
De technieken knippen en zagen zijn genoegzaam bekend, maar ‘ponsen’ en ‘stansen’ worden nog weleens verward. De basis is hetzelfde, maar bij het stansen wordt verder gewerkt met datgene wat uit het plaatmateriaal wordt gedrukt, terwijl bij ponsen juist het raster een vervolgbewerking ondergaat. Van de genoemde koude snijtechnieken kent waterstraalsnijden zonder twijfel de kortste geschiedenis (zie kader). Het is een nauwkeurige techniek waarbij alle eigenschappen van het basismateriaal intact blijven aangezien er geen sprake is van een zogeheten heat affected zone (HAZ).
Waterstraalsnijden gebeurt met behulp van een spuitkop waarop robijn of (kunst)diamant is aangebracht in combinatie met een straalbuis ‒ diameter 0,2 tot 1,5 mm ‒ waarmee gefilterd water in combinatie met een abrasief (zie hierna) op het metaal wordt gespoten en aldus een erosieproces teweegbrengt. De druk varieert daarbij van 3.500 tot 6.000 bar (350 tot 600 MPa). De snelheid waarmee het water het metaal raakt, bedraagt 700 m/s of 2.520 km/h (onder normale omstandigheden is de geluidsnelheid 1.194 km/h). Een dergelijke waterkracht is voldoende om ook grote componenten uit vol materiaal te kunnen snijden.
HISTORIE
Waterstraalsnijden vindt zijn oorsprong in de bosbouw waar de techniek werd gebruikt om gekapt hout te verwerken tot planken. Een grote stap voorwaarts werd gemaakt toen men er eind jaren zeventig toe overging een abrasief aan het water toe te voegen. In 1980 werden de eerste abrasieve-watersnijders geïntroduceerd om staal, glas en beton te snijden. De techniek werd als eerste omarmd door de (militaire) lucht- en ruimtevaartindustrie, waar het werd gezien als dé manier om hoge-sterkte metalen als inconel, roestvaststaal en titanium, maar ook lichtgewicht hoge-sterkte composietmaterialen als carbon te bewerken. Voor hightech composieten, gelamineerde materialen en materialen met een honingraatstructuur voldeden de traditionele bewerkingsmethoden niet langer, onder meer doordat ze de structurele integriteit van het moedermateriaal aantastten, terwijl alle thermische processen vervorming van de snijkanten van gesneden componenten veroorzaakten. Ook waren die techniekenregelmatig de oorzaak voor spanning, haarscheuren en structurele materiaalverandering. Mede hierdoor zijn abrasieve watersnijders gangbaar geworden in een groot aantal takken van industrie. Gaandeweg is de techniek verder ontwikkeld resulterend in mogelijkheden als meerdimensionaal- en precisiesnijden.
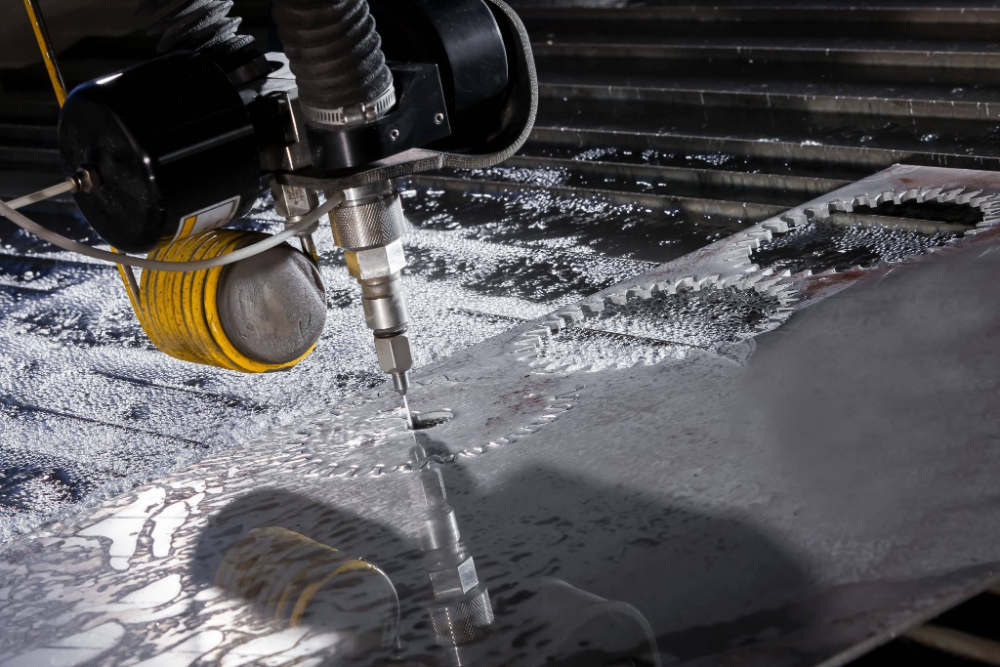
ABRASIEF
Bij het zogeheten puur of zuiver waterstraalsnijden wordt geen abrasief toegevoegd. Dit maakt deze methode geschikt voor de bewerking van zachte(re) materialen als stoffen, rubber of metaalfolies.
Bij hardere materialen als (roestvast)staal, titanium en aluminium is het gebruik van een abrasief noodzakelijk. Al deze metalen lenen zich bij uitstek voor waterstraalsnijden; door de goede warmtegeleiding is de kans op beschadiging bij het gebruik van een van de drie thermische snijtechnieken namelijk (te) groot.
Het abrasief is een van de duurste componenten binnen het proces, en bestaat uit korrels die qua afmeting variëren van 0,001 tot 2 mm. Het abrasief wordt aangezogen door de in de mengkamer heersende onderdruk. In de straalbuis (nozzle) vindt vervolgens vermenging plaats van het water en het abrasief. Als het watervolume door de mengkamer stijgt, dan wordt de onderdruk hoger en wordt meer abrasief aangezogen. Dit resulteert in een grotere snijsnelheid. Met de toevoeging van een abrasief kan een waterstraalsnijmachine kwaliteitssneden uitvoeren op materialen tot een dikte van 200 mm, in sommige gevallen tot wel 400 of 500 mm. Het abrasiefverbruik is onder meer afhankelijk van de korrelgrootte het watervolume in de snijkop, en varieert van 300 – 450 gram per snijminuut.
SNIJSNELHEID
Het abrasief is het ‘snijelement’, het water geeft de korreltjes de snelheid die nodig is om effectief te kunnen snijden en deze zo optimaal mogelijk richting het snijpunt te sturen. De ontstane centrifugaalkrachten zijn verantwoordelijk voor het feitelijke snijwerk. Factoren die van invloed zijn op de snijsnelheid en de kwaliteit van de snede zijn onder meer het watervolume (aan de snijkop) , de hoeveelheid water die de (kunst)diamant passeert, de kwaliteit en de korrelgrootte van het abrasief en de te snijden contour. Uiteraard valt of staat het geheel bij de kwaliteit van de aansturende software.
Lange tijd was plasma- of lasersnijden de standaard als het ging om verspanen. Wanneer metalen in combinatie met grove toleranties uit kunnen, dan komen autogeen- en (HD)plasmasnijden in beeld, technieken waarbij de snijsnelheid verhoudingsgewijs hoog ligt. Geleid een metaal de warmte echter (te) goed, zoals aluminium doet, dan zijn autogeen-, plasma- en lasersnijden niet de aangewezen technieken, omdat bij alle drie sprake is van warmte-inbreng. Het gevolg is dat er veranderingen (kunnen) optreden in de samenstelling, de kleur en/of de vorm van het betreffende materiaal. Metaal kan zelfs wegsmelten waarbij scherpe punten of uitsteeksels ontstaan.
VOOR- EN NADELEN
Waterstraalsnijden kent behalve voordelen ook nadelen. Er wordt altijd met een natte substantie gesneden en de snijdiamant, de straalbuis, de leidingen en de pompdelen zijn met name ook door het gebruik van een abrasief zijn sterk aan slijtage onderhevig. Dit maakt de techniek tamelijk kostenintensief.
De belangrijkste voordelen zijn dat er geen thermische belaste zones en mechanische spanningen ontstaan. Doordat het aantal handelingen vergeleken met de thermische technieken beperkt is, is de kans op menselijke falen bovendien geringer en is er veel tijdwinst te behalen doordat een nabewerking doorgaans achterwege kan blijven. Ook is de hoeveelheid metaalafval beduidend kleiner. Het water met abrasief wordt doorgaans opgevangen in een big bag waarin het zand als bezinksel achterblijft. Het bovenstaande water wordt eventueel nog door een cascadefilter geleid om ongerechtigheden te verwijderen en vervolgens geloosd op het riool. De inhoud van de big bag wordt gereinigd of gestort, tenzij er sprake is van zware metalen; dan wordt de inhoud afgevoerd als chemisch afval. Zeker niet onbelangrijk tot slot is het feit dat er geen gevaarlijke dampen en gassen veroorzaakt, terwijl dit bij de thermische technieken wel het geval is.
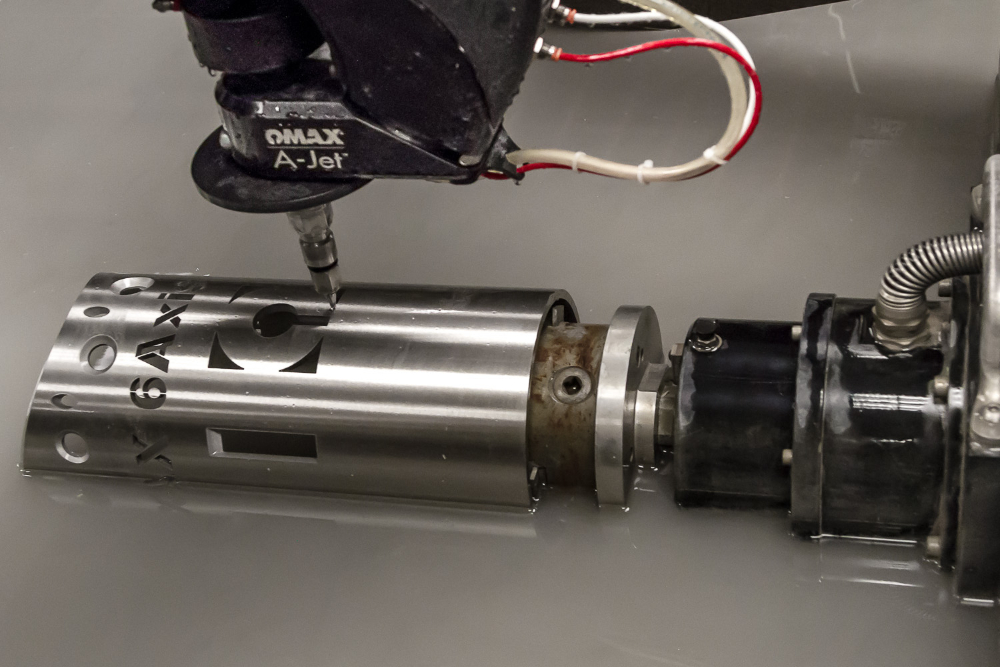
DIMENSIES
Watersnijmachines zijn in veel gevallen uitgerust met een 2D-snijkop. Er zijn daarbij twee soorten bewegingen mogelijk: links- en rechtsaf volgens de X-as en voor- en achteruit volgens de Y-as. Er is echter de mogelijkheid ook in meer dimensies te werken. Bij 2,5D-snijden is de hoek kleiner dan 45°, wat het snijden van schuine kanten, bijvoorbeeld conusvormen, mogelijk maakt. Bij 5-assig (3D)-watersnijden beweegt de snijkop in de richtingen x, y en z, draait deze om zijn eigen as van -360° tot 360° en is er sprake van een zwenking van 90° tot -90°. Het voordeel hiervan is dat het basismateriaal optimaal wordt gebruikt en nabewerking ‒ ook hier ‒ overbodig is. Complexe vormen worden in een enkele bewerking gesneden, inclusief de laskanten.
De toepassingen van waterstraalsnijden op microniveau sluiten naadloos aan bij de ontwikkeling dat componenten en modules steeds kleiner worden. Bij dit micro- of precisiewatersnijden kunnen inmiddels hoge nauwkeurigheden worden bereikt; een lineaire nauwkeurigheid van 2,5 µm en Ra-waarden – een maat voor de ruwheid ‒ van 2 µm zijn daarbij geen uitzondering. Omdat er met een ronde waterstraal wordt gewerkt van doorgaans minimaal 0,2 mm, is een inwendige radius 0,25 mm of minder niet haalbaar.
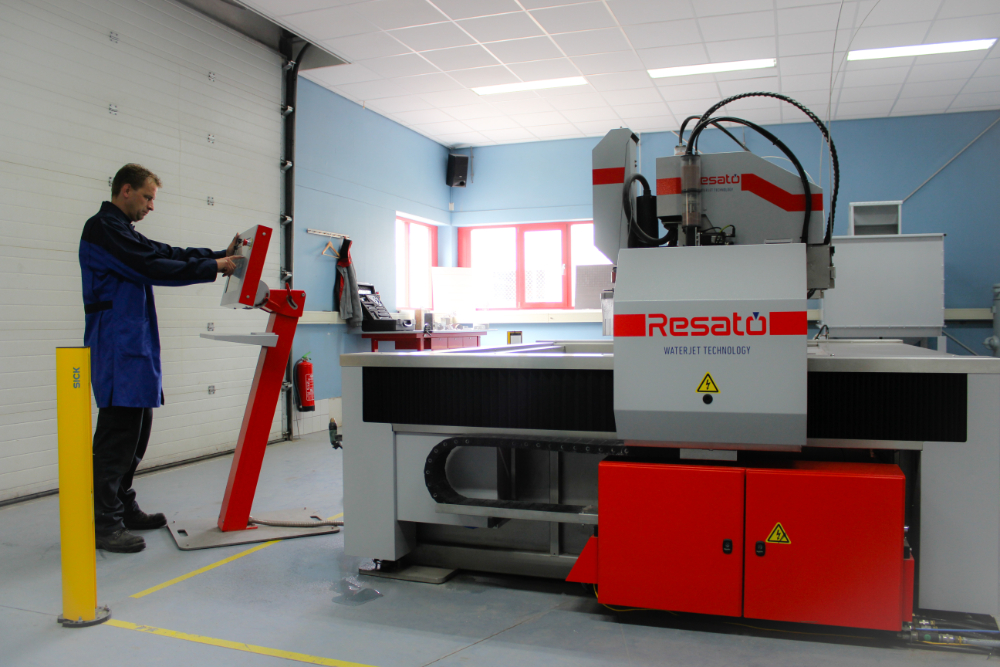
CONCENTRICITEIT
De laatste jaren is er hard gewerkt aan manieren om de waterstraalsnijtechniek verder te verbeteren, met de nadruk op het verbeteren van de spuitkop.
De aard van de straal wordt zowel bepaald door de maatvoering en vorm van de spuitopening, als door die van de straalbuis en door de mate waarin beide op een lijn liggen. Van belang daarbij zijn onder meer de diameter van de spuitopening, de plaats waar het abrasief intreedt, de hoek tussen waterstraal en intreerichting van het abrasief en de lengte van de straalbuis. Verbetering van de nauwkeurigheid hiervan heeft ertoe geleid dat de concentriciteit tussen de binnen- en buitendiameter inmiddels beter is dan 0,01 mm over de gehele lengte. En door het verbeteren van de inlijnligging, is het proces daarenboven nog eens betrouwbaarder geworden.
Door dit alles zijn de prestaties van het waterstraalsnijden de laatste jaren aanzienlijk verbeterd en zijn de snijsnelheden significant toegenomen. Innovatief bij het precisiewatersnijden is het gebruik van een zogeheten tilted snijkop. Continu wordt daarbij de stand van de snijkop gecorrigeerd, waardoor er met meer precisie kan worden gesneden. Bij de nadering van een hoek hoeft de machine niet langer af te remmen, wat een positief effect heeft op de snijsnelheid.
Met dank aan: Helaxa, Industrial Waterjetsystems Europe, L&D Jet-techniek en Resato International