IN EEN OOGWENK HET JUISTE ONDERDEEL
DANKZIJ PATERNOSTERSYSTEEM
Beperkte plaatsinname groot voordeel ten opzichte van andere systemen
Om snel een stuk uit uw voorraad op te halen, is een efficiënt magazijnbeheer broodnodig. Te veel overbodig zoekwerk leidt al vlug tot frustraties bij medewerkers en langere wachttijden voor de klant. Bovendien stelt zich steeds vaker een ruimtelijk probleem, want magazijnruimte is duur en schaars.
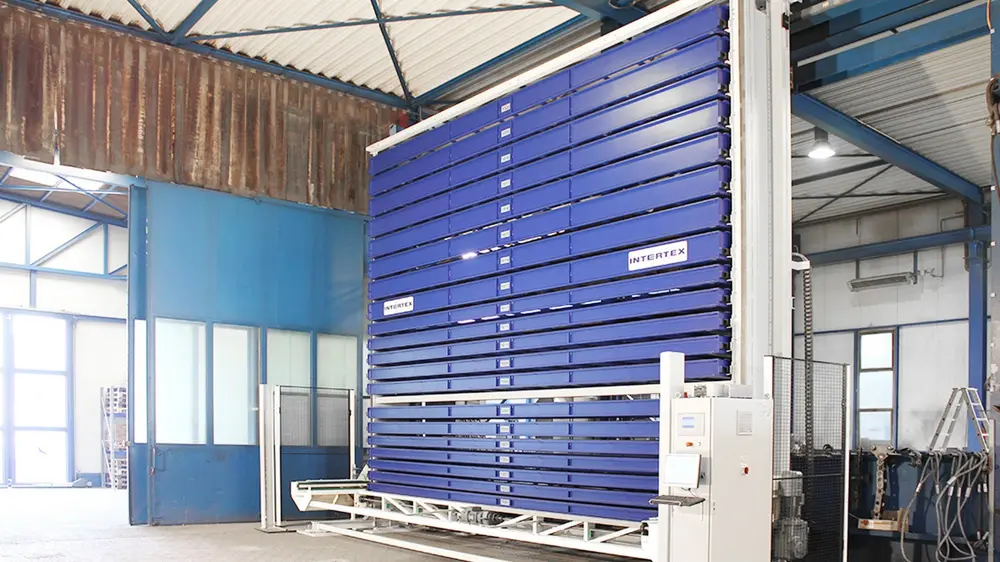
INZETTEN OP EFFICIENTIE
Voor wie met magazijnbeheer bezig is, komen bovenstaande opmerkingen waarschijnlijk meer dan bekend voor. Vandaag is dat meer dan ooit zonde, want klanten accepteren steeds minder lange wachttijden. De invloed van webshops - 'voor 23 uur besteld, morgen in huis' - sijpelt ook door naar de industriële handel. Klanten hebben nog maar weinig begrip als ze een week moeten wachten op een courant stuk. Maar ook intern leidt een slecht beheerd magazijn tot frustratie. Operatoren moeten langer wachten op werkstukken, de productie loopt achterstand op en deadlines worden niet gehaald. Veel stof voor conflicten op de werkvloer.
Een goede magazijnorganisatie en WMS (Warehouse Management System) horen bij de belangrijkste pijlers om klant en werknemer tevreden te houden. Een veelvoorkomend probleem is dat een groeiend bedrijf vooral investeert in machines om de stijgende productievraag bij te houden, maar dat het magazijn vergeten wordt. Het resultaat is een historisch gegroeide miskleun die de eerder gemaakte investeringen tenietdoet. In veel gevallen is het dan ook aan te raden om tabula rasa door te voeren, in plaats van telkens maar weer een pleister op een houten been aan te brengen. De vraag rest: welk systeem past het best bij uw situatie?
DIVERSE SYSTEMEN & PRINCIPES
Traditioneel magazijn
Dit is van oudsher de meest gebruikte oplossing. De stukken worden gestockeerd in palletrekken (voor grote stukken) of legborden (voor kleine stukken). In het eerste geval rijdt een heftruck af en aan om de stukken op stock te nemen of uit stock te halen, in het tweede geval verplaatst de magazijnmedewerker zich richting het juiste legbord. Het voordeel van deze manier van werken is voornamelijk het overzicht dat men heeft op de stock.
Zaken die niet lijken te kloppen, kunnen al gauw worden gedetecteerd door de grote menselijke inbreng. Ook voor de grote stukken is dit een prima oplossing. Helaas zijn er aan deze traditionele manier van werken ook enkele nadelen verbonden. De ruimte die dit systeem inneemt, is groot. Die ruimte is schaars en kan in de meeste gevallen ingezet worden voor meer lucratieve zaken. Medewerkers moeten zich ook telkens fysiek verplaatsen - met een heftruck of te voet - om de juiste picking te maken. Dat is arbeidsintensief en vergt kostbare tijd.
“Ik vind dat stuk niet terug"
“De stock van dat stuk is uitgeput, maar er zit geen nieuwe bestelling in het systeem"
“Dat stuk ligt op de verkeerde locatie"
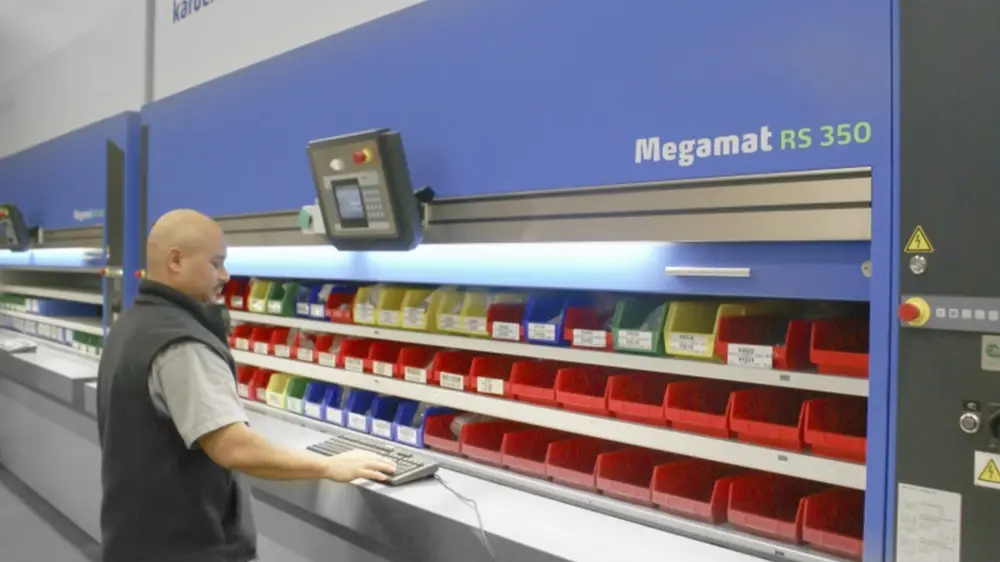
Verrijdbare stellingen
Uiteraard staat de tijd niet stil en zijn er ook uitvoeringen op de markt die de nadelen van traditionele magazijnen proberen te counteren. Magazijnen met automatisch verrijdbare stellingen zijn hier een prima voorbeeld van. De palletstellingen of legborden schuiven bij het niet in werking zijn gewoon tegen elkaar. Als een picking vereist is, geeft de medewerker via afstandsbediening of automatisch via het WMS-systeem aan welke gang geactiveerd moet worden.
Vervolgens wordt deze gang automatisch vrijgemaakt door motorisch de stellingen te verrijden. Belangrijk hierbij is dat de verplaatsing van de rekken voldoende snel moet gebeuren om tijdverlies te beperken, maar dat tegelijk de veiligheid altijd gegarandeerd moet worden. Bij de plaatsing van een dergelijk systeem wordt er dan ook altijd gebruikgemaakt van veiligheidssensoren.
Miniload/palletkranen
Volledig geautomatiseerde systemen vormen de overtreffende trap van het vorige systeem, waarbij ook de menselijke inbreng tot een minimum beperkt wordt. Voor kleine stukken werkt dit op basis van trays die voorzien worden van een identificatietag. Dat kan een barcode of een RFID-tag zijn. Bij ontvangst wordt de barcode van het stuk ingescand en in een tray gelegd. De barcode van het stuk wordt gelinkt aan de identificatie op de bak, zodat de exacte locatie via het WMS toegewezen kan worden.
Vervolgens verloopt alles automatisch. De trays worden via rollenbanen tot bij een miniloadmagazijn gebracht, waar ze automatisch op stock gelegd worden door een miniloadkraan, of een palletkraan indien er gewerkt wordt met grotere stukken. Voor kleine stukken kunnen de trays ook met inlegstukken opgedeeld worden in meerdere kleine vakjes. Uiteraard is een dergelijk automatisch systeem een stuk prijziger. Het wordt dan ook voornamelijk toegepast bij logistieke bedrijven waar de aan- en afvoer snel moet verlopen, voor technische magazijnen wordt dit systeem weinig toegepast.
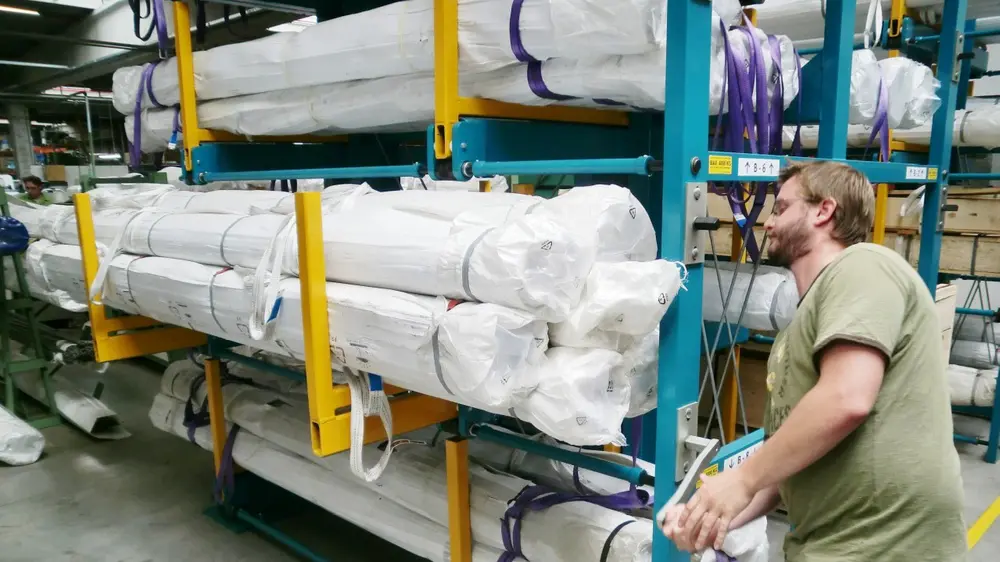
Hoogplatform
Een hoogplatform, een magazijn boven de werkruimte, is vooral geschikt voor slow movers. Omdat er in de hoogte wordt gewerkt, is dit een goede oplossing om plaatsgebrek aan te pakken. Wel is het op en van de stock nemen soms omslachtig en/of weinig ergonomisch, wat het voor fast movers een minder geschikte oplossing maakt.
PATERNOSTER
Verticale liftsystemen of paternostersystemen zijn een populaire oplossing geworden. Logisch ook, want de oplossing paart gebruiksgemak en snelheid aan een aanzienlijke plaatsbesparing. De werkwijze is relatief eenvoudig. De SKU's worden in bakjes of trays op lades geplaatst. Die lades worden boven elkaar in een circulair liftsysteem gestapeld. Bij een pickingactie wordt de juiste lade gemotoriseerd tot bij de picker van dienst gebracht, die enkel het stuk uit het juiste bakje moet nemen. De sturing van de installatie wordt verzorgd door encoders die de motor aansturen, zodat de juiste lade tot bij de operator komt. Andere systemen maken ook gebruik van een PLC en intelligente sturing.
Het pickingsignaal wordt ontvangen door de intelligente sturing, die op haar beurt de centrale bewegingsunit aanstuurt. Deze PLC vertaalt de bewegingscommando's via een frequentieomvormer naar de motoren. De verticale en horizontale bewegingen worden gecontroleerd door encoders, waardoor het gevraagde plateau met maximale nauwkeurigheid in de machine zal worden opgehaald. Deze wordt vervolgens in de uitnameopening gebracht. Bij het terugplaatsen zullen steeds de hoogte en het gewicht van het plateau worden gecontroleerd door de machine.
Hogere benutting, minder verplaatsingen
Omdat de volledige hoogte van het gebouw benut kan worden, kunnen er zo plaatsbesparingen tot 90% gerealiseerd worden. Bijkomend voordeel is dat er geen tijdrovende verplaatsingen meer nodig zijn: de stukken komen tot bij de picker. Om optimaal gebruik te maken van het systeem, kan het systeem voorzien worden van een pick-to-lightsysteem. Dit houdt in dat er onder of boven elk voorraadbakje een lampje voorzien wordt, dat oplicht als het te picken stuk zich in dat bakje bevindt.
De operator hoeft dus niet meer uit te zoeken in welk bakje zijn stuk zit, hij ziet het meteen. Het hoeft geen betoog dat de geboekte tijdwinst hier fenomenaal is. Wie veel met profielen en buizen werkt, kan een beroep doen op langgoedpaternosters. Profiellengtes tot 7 meter zijn zo haalbaar. Natuurlijk moet hier altijd de afweging gemaakt worden of de prijs in verhouding staat tot andere opslagwijzes voor langgoed, zoals uittrekbare rekken.
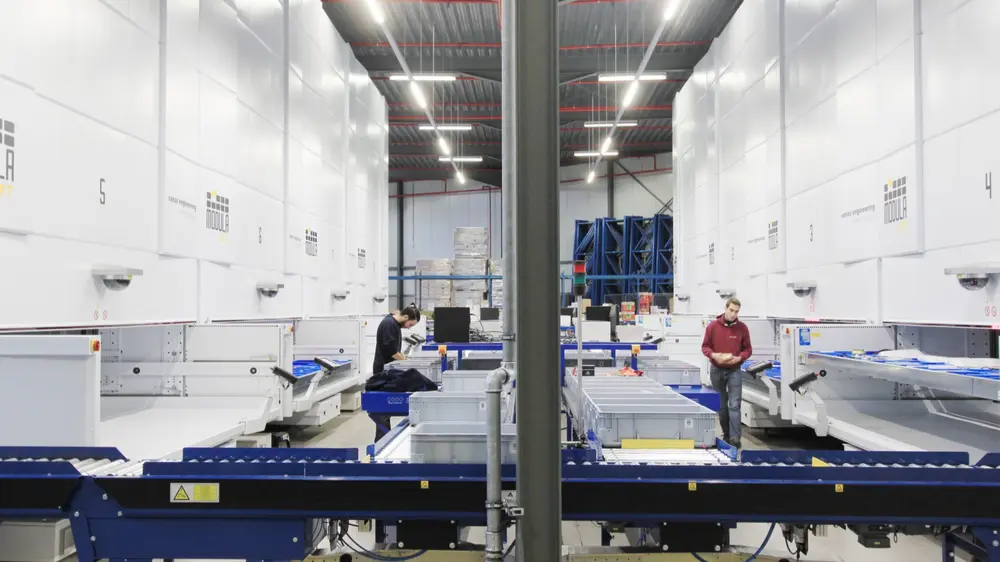
Hoog laadvermogen
Ook zware stukken worden meer en meer in paternosters opgeslagen. Het totale laadvermogen gaat standaard van 30 ton tot meer dan 120 ton. In dit laatste geval wordt de newton per mm² berekend om de maximale vloerbelasting niet te overschrijden. In de praktijk blijken hier weinig problemen mee te zijn. De puntlasten worden goed gespreid, waardoor de last niet veel hoger is dan van palletrekken. De hoogte van een paternoster kan vandaag tot 30 meter gaan, de breedte al gauw tot 10 meter.
Horizontale & verticale varianten
Er wordt verder nog een onderscheid gemaakt tussen verticale (in de hoogte) en horizontale paternoster (in de lengte). Verder zijn er ook paternostersystemen in carrouselvorm, waarbij de trays in een ellipsvormige vorm tot bij de operator worden gebracht. Er kunnen meerdere niveaus zijn per carrousel. Per werkstation zijn er meestal meerdere carrousels en ook hier kan er gebruikgemaakt worden van pick-to-lightsystemen. Deze horizontale carrousel wordt meestal ingezet bij de combinatie van grote hoeveelheden producten met lage magazijnhoogtes.