LE BON ELEMENT EN UN CLIN D’ŒIL
GRACE AU SYSTEME PATERNOSTER
Une occupation spatiale limitée, un grand avantage par rapport aux autres systèmes
Pour enlever rapidement une pièce de stock, une gestion de magasin efficace est vitale. Trop de recherche superflue induit vite des frustrations chez les collaborateurs et de longs délais d’attente pour le client. De plus, un problème spatial se pose de plus en plus souvent, car l’espace de magasin est cher et rare.
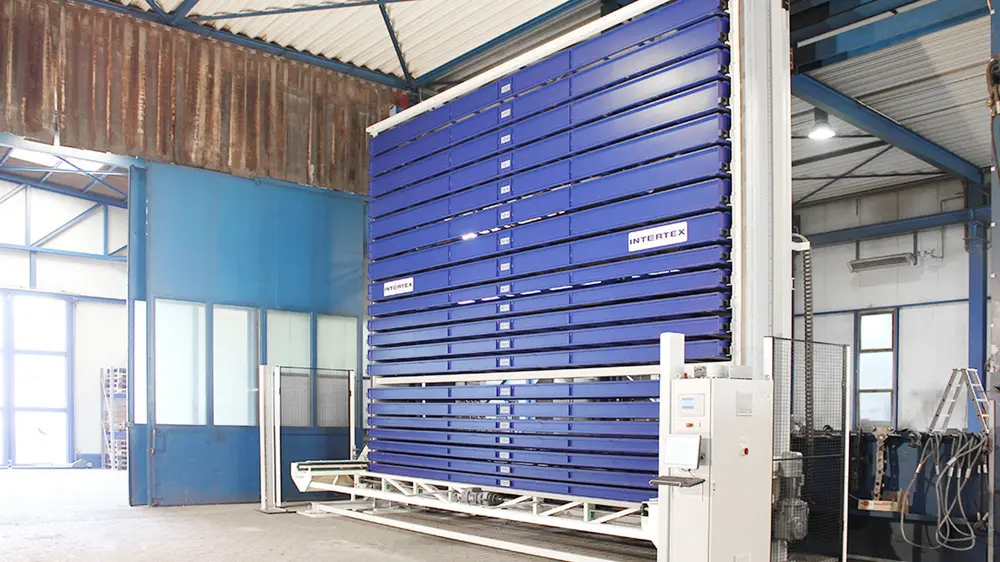
MISER SUR L’EFFICACITE
Pour celui qui s’occupe de la gestion du magasin, ces remarques seront probablement plus que connues. Aujourd’hui, c’est plus que jamais dommage, car les clients acceptent de moins en moins de longs temps d’attente. L’influence des webshops – ‘commandé avant 23h, demain à domicile’ – percole aussi dans le négoce industriel. Les clients n’ont que peu de compréhension s’ils doivent attendre une pièce courante pendant une semaine. Un magasin mal géré entraîne aussi la frustration en interne. Les opérateurs doivent attendre leurs pièces plus longtemps, la production accuse du retard et les dates limites ne sont pas respectées.
Grande source de conflits sur le lieu de travail. Une bonne organisation du magasin et un bon WMS (Warehouse Management System) sont l’un des principaux piliers pour préserver la satisfaction du client et du travailleur. Un problème fréquent est qu’une entreprise croissante investit surtout dans les machines pour répondre à la demande de production croissante, mais oublie le magasin. Le résultat est une bévue historique qui annihile les investissements consentis. Dans bien des cas, il est conseillé de faire table rase, au lieu d’appliquer un emplâtre sur une jambe de bois. La question demeure: quel est le système le plus indiqué pour votre situation?
“Je ne retrouve pas cette piece”
“Le stock de cette piece est epuise, mais il n’y a aucune nouvelle commande dans le systeme”
“Cette piece se trouve au mauvais endroit”
DIVERS SYSTEMES & PRINCIPES
Magasin traditionnel
De tout temps, ceci fut la solution la plus utilisée. Les pièces sont stockées dans des rayonnages à palettes (pour grandes pièces) ou des tablettes (pour petites pièces). Dans le premier cas, un chariot élévateur fait des trajets aller-retour pour déposer ou enlever une pièce du stock; dans le second cas, le collaborateur de magasin se déplace vers la bonne tablette.
L’avantage de cette méthode de travail est essentiellement la vue globale sur le stock. Les aspects qui ne semblent pas coïncider, sont rapidement détectés par le grand apport humain.
Hélas, cette méthode de travail comporte quelques désavantages. L’espace qu’occupe ce système, est grand. Cet espace est rare et peut dans la plupart des cas être mis à profit pour des choses plus lucratives. Les collaborateurs doivent aussi se déplacer physiquement à chaque fois – avec un chariot élévateur ou à pied – pour effectuer le bon picking. Ceci comporte un grand coefficient de travail et exige un temps précieux.
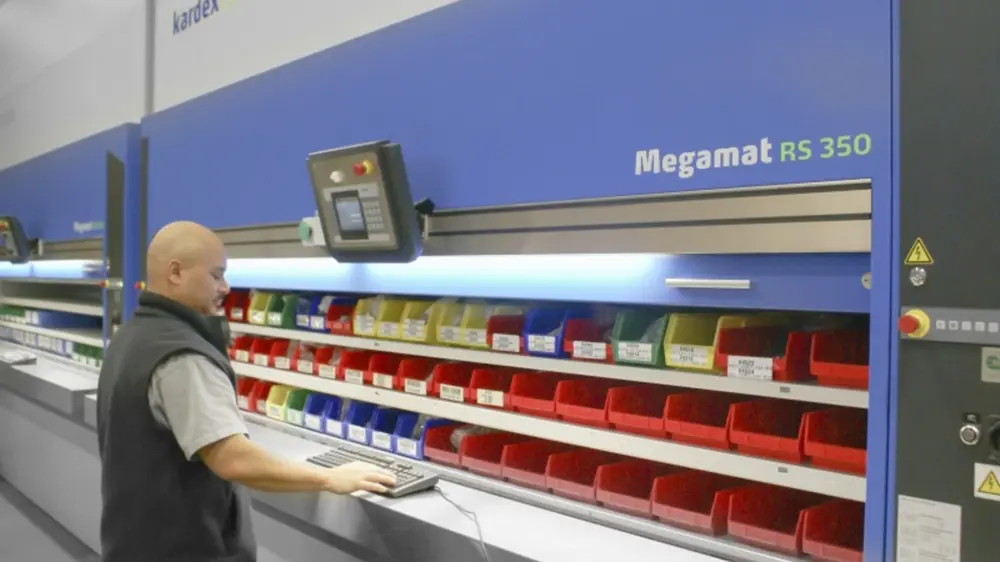
Echafaudages mobiles
Bien entendu, le temps ne s’arrête pas et il existe également des exécutions sur le marché qui tentent de contrer les désavantages des magasins traditionnels. Les magasins avec échafaudages mobiles automatiques en sont un parfait exemple.
Les échafaudages à palettes ou tablettes glissent simplement les uns contre les autres en cas de non-utilisation. Si un picking est exigé, le collaborateur indique par télécommande ou automatiquement via le système WMS quelle allée doit être activée.
Ensuite, cette allée est automatiquement libérée par le déplacement motorisé des échafaudages. L’important est que le déplacement des rayonnages soit suffisamment rapide pour limiter la perte de temps tout en garantissant toujours la sécurité. Lors du placement d’un tel système, on utilise toujours des capteurs de sécurité.
Miniload/grues à palette
Les systèmes entièrement automatisés constituent le meilleur du système précédent, l’apport humain étant minimisé. Pour de petites pièces, ceci fonctionne sur la base de plateaux pourvus d’une étiquette d’identification. Ceci peut être un code-barres ou une étiquette RFID.
Lors de la réception, le code-barres de la pièce est scanné et posé dans un plateau. Le code-barres de la pièce est lié à l’identification sur le bac, de telle sorte que l’emplacement exact peut être attribué via le WMS. Ensuite, tout est automatique. Les plateaux sont amenés vers un magasin miniload via des transrouleurs, où ils sont déposés en stock de façon automatique par une grue miniload ou une grue à palettes si l’on travaille avec des pièces plus grandes.
Pour de petites pièces, les plateaux peuvent aussi être scindés par des inserts en plusieurs petits compartiments. Bien entendu, un tel système automatique est un peu plus cher. Ce système est essentiellement utilisé dans les entreprises logistiques où l’amenée et l’enlèvement doivent être rapides, mais est peu utilisé pour les magasins techniques.
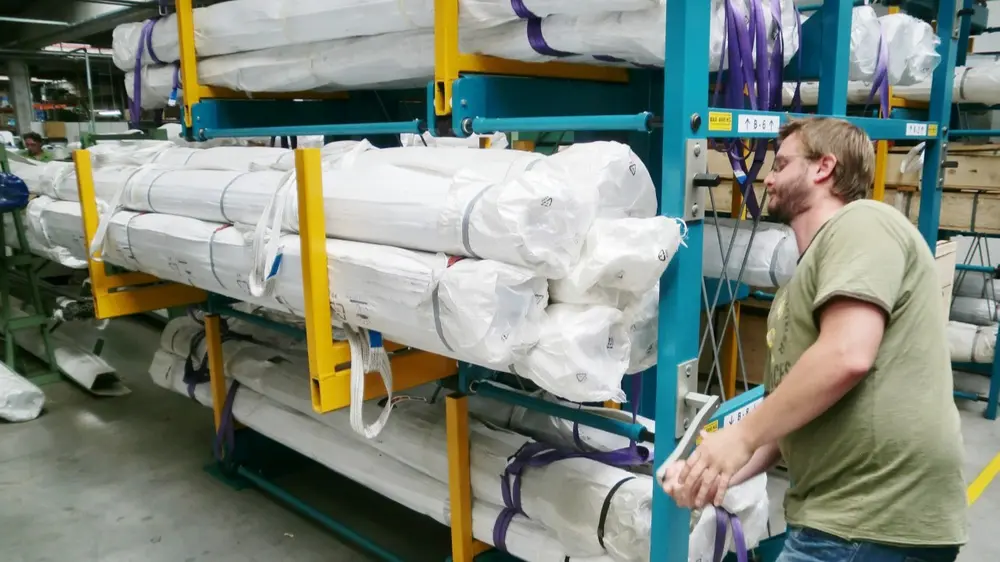
Plateforme en hauteur
Une plateforme en hauteur, un magasin au-dessus de l’espace de travail, est destinée aux slow movers. Comme on travaille en hauteur, ceci est une bonne solution pour contrer le manque de place. Mais l’enlèvement et le dépôt en stock sont parfois compliqués et/ou peu ergonomiques, ce qui en fait une solution moins adaptée aux fast movers.
PATERNOSTER
Les systèmes d’ascenseur verticaux ou systèmes paternoster sont devenus une solution populaire. C’est logique, car la solution allie le confort d’utilisation et la vitesse à un gain de place considérable. La méthode de travail est relativement simple. Les SKU sont placés dans des bacs ou des plateaux sur tiroirs. Ces tiroirs sont superposés dans un système d’ascenseur circulaire. Lors d’une action picking, le bon tiroir est amené de façon motorisée vers l’opérateur de service, qui doit uniquement retirer la pièce du bon bac.
La commande de l’installation est assurée par des encodeurs qui pilotent le moteur afin que le bon tiroir arrive jusqu’à l’opérateur. Le signal de picking est reçu par la commande intelligente qui, à son tour, pilote l’unité de mouvement centrale. Ce PLC traduit les instructions de commande via un convertisseur de fréquence vers les moteurs. Les mouvements verticaux et horizontaux sont contrôlés par des encodeurs, ce qui enlève le plateau demandé avec une précision maximale dans la machine. Ensuite, celui-ci est introduit dans l’ouverture d’enlèvement.
Plus grande occupation, moins de déplacements
Comme la hauteur complète du bâtiment peut être utilisée, on peut réaliser des gains de place allant jusqu’à 90%. L’avantage complémentaire est de ne pas nécessiter de déplacements fastidieux: les pièces parviennent à l’opérateur. En vue d’une utilisation optimale du système, le système peut être pourvu d’un système pick-to-light. Ceci implique de prévoir une petite lampe sous ou au-dessus de chaque poutre d’approvisionnement, qui s‘allume quand la pièce à saisir se trouve dans ce bac.
L‘opérateur ne doit donc plus chercher dans quel bac se trouve la pièce, il le voit d’emblée. Nul besoin de démontrer que le gain de temps enregistré est ici phénoménal. Celui qui travaille avec des profilés et des tubes, peut faire appel à des paternosters pour longues marchandises. Des longueurs de profil de 7 mètres sont ainsi réalisables. Naturellement, il convient ici de toujours évaluer si le prix est en rapport avec d’autres modes de stockage pour longues pièces, comme des rayonnages extensibles.
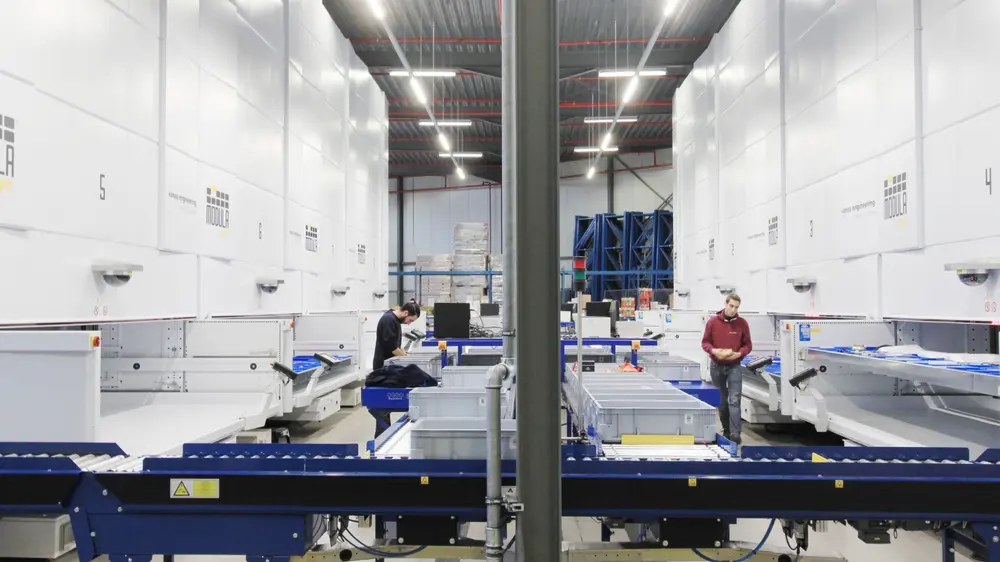
Grande capacité portante
Les lourdes pièces sont aussi de plus en plus stockées dans des paternosters. La capacité portante totale va de 30 tonnes en standard à plus de 120 tonnes. Dans ce dernier cas, on calcule le newton par mm² pour ne pas dépasser la charge maximale du sol. Ceci semble causer peu de problèmes dans la pratique. Les charges ponctuelles sont bien réparties, si bien que la charge n’est pas bien plus élevée que celle des rayonnages à palettes. La hauteur d’un paternoster peut atteindre aujourd’hui 30 mètres, et la largeur bien vite 10 mètres.
Variantes horizontales & verticales
On distingue encore le paternoster vertical (en hauteur) et horizontal (en longueur). Il existe aussi des systèmes paternoster en forme de carrousel, les plateaux étant amenés jusqu’à l’opérateur dans une forme elliptique. Plusieurs niveaux sont possibles par carrousel et on peut aussi utiliser ici des systèmes pick-to-light. Ce carrousel horizontal est le plus souvent engagé dans la combinaison de grandes quantités de produits avec de grandes hauteurs de magasin.