FACTORY OF THE FUTURE: C-MEC
“Sans changements, nous n'existerions plus”
Lorsque l’entreprise de sous-traitance C-Mec a été confrontée à de sérieuses entraves dans l’exploitation il y a environ six ans, il a été décidé de changer radicalement le fusil d’épaule. En raison de la concurrence avec les pays à bas salaires, on s’est orienté encore plus sur l’approche ‘one-stop-shop’ et la production de séries plus petites. L’automatisation et la digitalisation constituent le fil rouge dans cette réussite.
racines chez Barco
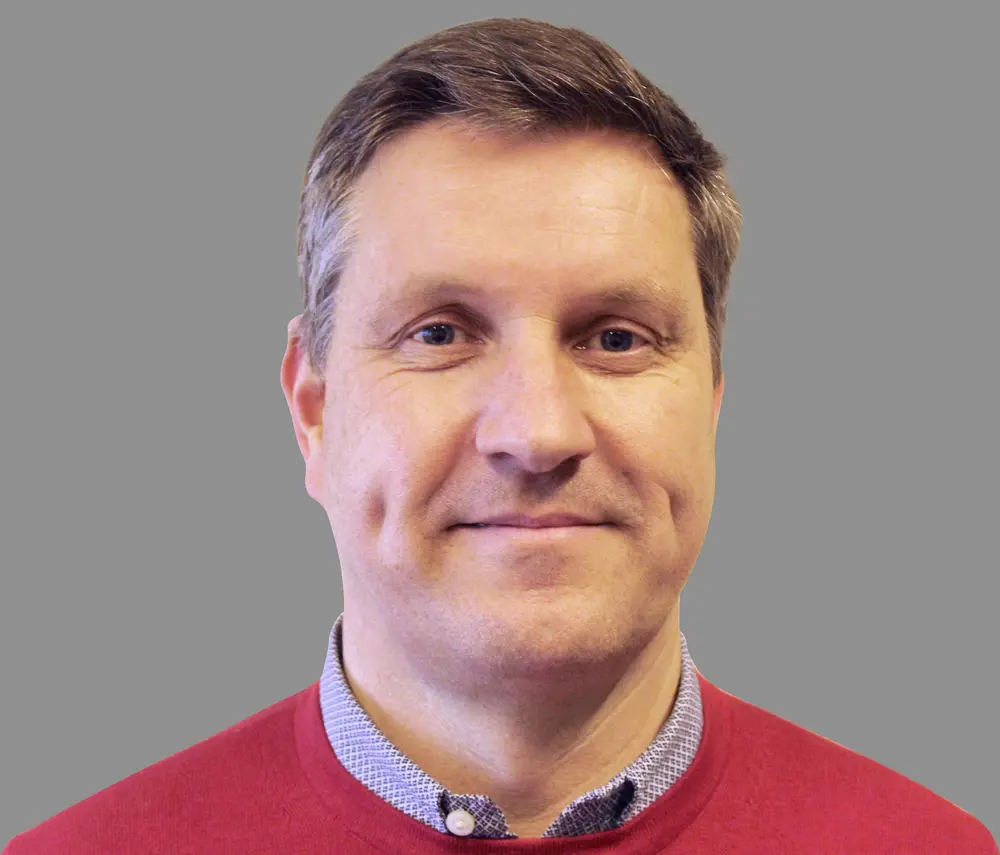
Nous rencontrons le DOP Tom Vandewoestijne dans le siège social à Courtrai. Il nous guide brièvement à travers l’histoire de l’entreprise: “Jusqu’en 2008, nous étions un département de Barco. Lorsque le département a été vendu, nous avons continué comme entreprise indépendante. Nous produisons des éléments métalliques pour des clients et applications très divers. Barco est toujours client mais nous produisons aussi des éléments pour d’autres noms connus tels qu’Atlas Copco. Au fil des années, nos activités se sont étendues de façon géographique grâce à des rachats. En Belgique, nous avons aussi un département à Bornem où sont produits les pièces un peu plus lourdes et plus grandes. Dans notre pays nous employons respectivement 100 et 40 salariés. A l’étranger nous avons entre-temps des départements en Roumanie et en République tchèque.”
approche One-stop-shop
“Il y a quelques années, nous avons été confrontés à quelques embûches. Par exemple, le coût salarial qui nous handicapait - et nous handicape encore – face aux pays à bas salaires. Egalement la guerre aux talents, qui fait rage ici dans la région. Un processus de production efficace avec une logistique adaptée est notre réponse. Notre parc de machines complet est calqué sur le principe d’un ‘one stop shop’: nos clients industriels passent commande chez nous et nous voulons les livrer dans une approche make-to-order. Il est important de mentionner que nous n’avons pas de gamme de produits propre, nous travaillons purement sur ce que le client veut et nous le faisons en flux tendu. Parfois cela concerne des séries très petites de quelques pièces, allant des concepts simples aux éléments plus sophistiqués. Pour exécuter à temps tous les processus afférents, vous devez tout avoir en interne, ici nous pouvons notamment poinçonner, travailler au laser, couper, plier, usiner, tourner, fraiser, laquer à la poudre et mouillé, et pour terminer, exécuter des tâches d’assemblage. Cela nous donne un énorme avantage. Je cite l’exemple de notre chaîne de laquage mouillé, en 2014 l’un de nos premiers gros investissements dans le cadre de notre transition. Nous pouvons d’emblée peindre les pièces si cela est nécessaire. Avant nous devions le sous-traiter en externe, ce qui ne permettait plus de contrôler les délais de livraison. De plus, cela met fin aux discussions en cas de dégâts.
”Cette approche one-stop-shop séduit les clients, mais cela signifie bel et bien affronter à chaque fois une mission frénétique. Chaque jour, 3 à 400 cents commandes sont en préparation. Pour chaque nouveau produit, nous devons d’abord effectuer une analyse: quelles étapes exécuter, en combien de temps, où engager le personnel et quel prix demander en contrepartie.“
La taille de série peut être très petite. Des temps de conversion limités sont très importants
Factory of the future
“Depuis environ six ans, C-MEC est membre du comité directeur Advanced Manufacturing d’Agoria. Ainsi nous connaissons toutes les transformations du trajet vers les Factories of the Future mais pour nous, l’obtention de l’Award n’est pas un but final en soi, parce que le secteur dans lequel nous nous trouvons évolue si vite. En ce sens nous sommes un peu un original, parce que nous n’avons pas utilisé les sept transformations comme manuel. Nous pouvons ramener l’évolution subie depuis six ans sous l’une de ces transformations. C’est donc en fait le mouvement inverse, quoique les Factories of the Future constituent bien le fil rouge de notre méthode de travail.”
Advanced Manufacturing Technologies
Investir dans des machines avec plus-value
“Quiconque désire promouvoir la philosophie one-stop-shop doit bien écouter les exigences de ses clients. Pour satisfaire à leurs demandes, vous devez constamment investir dans une nouvelle technologie. Ceci est sans aucun doute le principal pilier dans notre transition. Nous avons notamment investi dans une nouvelle combinaison poinçonneuse/laser et une imprimante digitale pour imprimer des éléments. Lors de l’achat, elle répondait aux demandes actuelles des clients mais permettait aussi de se lancer sur de nouveaux marchés. Aujourd’hui la machine est constamment occupée, ce fut vraiment un coup dans le mille. Par ailleurs, nous avons constaté que la presse plieuse ordinaire nécessitait un temps de réglage de 15 à 20 minutes lors d’une nouvelle commande. Cela pose peu de problèmes pour de grandes séries mais pour celui qui vise les petites séries, c’est problématique. C’est pourquoi nous avons investi dans une presse plieuse dotée d’un changement d’outil automatique. Le temps de réglage a été réduit à deux minutes. Une presse plieuse entièrement automatique était aussi un bon investissement.”
“La robotisation est aussi un solide pilier dans notre transformation, vous trouvez des robots partout dans notre production. Une arrivée robotisée de notre presse-plieuse permet de décharger nos collaborateurs d’une tâche très physique. Pour des tâches de chargement et de déchargement simples, nous recourons aussi à des robots. Il a fallu du temps avant de maîtriser les mouvements de ces appareils mais aujourd’hui ils accomplissent parfaitement leur tâche. Avant les salariés devaient tout charger et décharger. Maintenant ils doivent uniquement veiller à compléter les stocks à temps. Tous les exemples cités ne signifient pas que notre automatisation a diminué l’emploi, au contraire.”
Human Centered Organisation
L’impact sur le personnel
“Les tâches de nos collaborateurs ont bel et bien fortement évolué. Avant chacun avait un peu sa ‘propre’ machine, avec le travail physique qui en découle: amener, retenir, fixer les pièces et ainsi de suite. Aujourd’hui ils sont souvent responsables de plusieurs machines, mais les tâches physiques sont dorénavant exécutées par un robot. Leur job est davantage la supervision, ce qui exige quand même plus de réflexion et de planning. Nos collaborateurs ont bien rejoint ce processus progressif. Je pense que chacun exerce un meilleur job qu’il y a six ans. L’ergonomie est améliorée. Nous avons investi dans un système de levage pour le montage de lourds bâtis. Avant le levage se faisait avec un chariot élévateur à fourches, ce qui était fastidieux. Nous avons trouvé la solution grâce à une visite d’entreprise dans un secteur différent, dans le cadre du programme Factory of the Future. Le réseautage est donc payant.”
Nous remarquons de nombreux cobots sur l’atelier. Vandewoestijne: “Il a fallu du temps avant de bien maîtriser les mouvements de ces appareils, mais aujourd’hui ils accomplissent parfaitement leur tâche”
Networked Factory
“Ce qui est aussi important, c’est que nous avons amélioré les lignes de communication entre les départements par quelques petites interventions physiques. Nous avons placé le bureau du responsable du département au milieu de l’atelier. Avant les salariés devaient se rendre au bureau pour discuter ou poser une question. Maintenant ceci se fait de façon bien plus directe, ce qui fait gagner beaucoup de temps. Une autre mesure qui contribue à la vitesse et à l’efficacité est le contrôle de qualité. Avant, les pièces qui entraient devaient attendre que le département contrôle de qualité ait le temps d’exécuter un contrôle. C’est pourquoi nous avons formé notre personnel de l’usinage pour exécuter certaines tâches de contrôle, sans devoir attendre.“
Pas totalement sans papier
“En théorie nous pourrions travailler de façon totalement digitale mais en concertation avec le personnel, il a été décidé de travailler en partie avec du papier. De nombreux ouvriers veulent avoir leur mission sur papier, celui qui travaille avec des gants de protection trouve que le travail avec des écrans est moins idéal.“
La communication rationalisée met de l’ordre
Nous avons donc une entreprise qui travaille sur commande, les commandes étant traitées très vite. De plus, il s’agit souvent de petites séries de pièces spécialisées. Un robuste système de communication sous-jacent nous semble alors vital. Nous nous sommes demandés comment se déroule une commande dans la pratique. “Le plus gros du travail se situe au début de chaque commande, certainement pour une pièce complètement neuve. Tous les programmes pour le traitement laser, le soudage, le pliage et autre sont d’abord préparés offline, ce qui prend le plus de temps. Une fois achevés, on peut très vite composer les ‘bill of materials’ et ‘bill of labour’ via le système ERP. Il ne reste qu’à vérifier que les centres de travail ne sont pas surchargés, que tout est disponible et que le personnel pour traiter la commande est suffisant. A chaque fois créer l’ordre dans le fonctionnement est un superbe défi.”