"Il faut tisser un lien etroit entre le personnel et la technologie"
geert ostyn nous parle de ‘let’s make it together’ chez Picanol
Un acteur bien connu ... c‘est le moins qu‘on puisse dire à propos du groupe Picanol. Il s‘agit du plus grand fabricant de machines à tisser au monde, précurseur en matière d‘innovation et bien ancré en terres yproises. Nous nous sommes demandé comment une entreprise aussi impressionnante mettait en pratique les principes de la Factory of the Future. Geert Ostyn, senior vice president Business Transformation & Strategic Alignment de l‘entreprise, nous a donné la réponse.
Factory of the Future Award?
Le groupe Picanol est une entreprise qui opère totalement dans l‘esprit de Factory of the Future. Pourtant, elle n‘a pas encore décroché de Factory of the Future Award. Geert Ostyn nous explique pourquoi: “Cela fait longtemps que je suis actif au sein d‘Agoria dans tout ce qui a trait à la fabrication. J‘étais donc aux premières loges lorsque le programme ‘Made Different‘ a été élaboré. Picanol a même été l‘une des entreprises test qui ont fait l‘objet d‘un audit basé sur les 7 transformations. Nous avons également été une source d‘inspiration pour plusieurs entreprises qui ont été récompensées entre-temps. Pour nous, deux conditions importantes font obstacle à la certification: il faut obtenir une note de 4 sur 5 pour chacune des 7 transformations et ce, pour l‘ensemble du groupe. C‘est difficile pour nous car nous sommes constitués de plusieurs entreprises (voir encadré ci-dessous) et nous gérons la palette complète: le développement, la production et le marché de l‘après-vente. En outre, il y a aussi les processus logistiques avec les autres sociétés du groupe comme Proferro et Psicontrol. Elles aussi disposent de ce processus complet en interne. Structurellement, il est donc très difficile de remporter ce prix pour l‘ensemble du groupe.“
‘Let’s make it together’
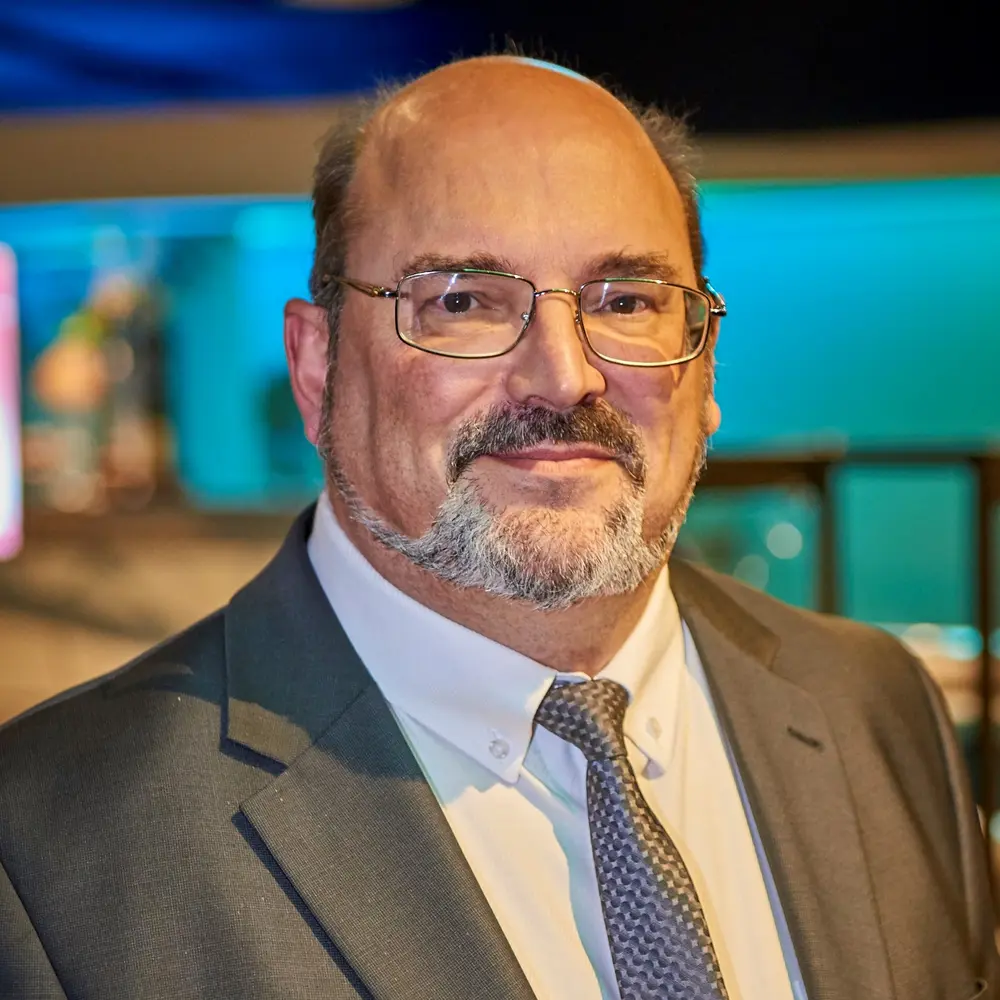
SVO Business Transformation & Strategic Alignment Picanol
“Mais cela ne signifie pas que nous n‘utilisons pas le programme Factory of the Future. De plus, les transformations ont inspiré l‘élaboration de notre propre approche. Notre programme interne s‘appelle ‘Let‘s make it together‘. Le but est d‘ancrer l‘avenir du groupe Picanol à Ypres. Les coûts salariaux et la pénurie de main-d‘œuvre qualifiée sont deux handicaps chez nous. Nous voulons y pallier avec ce programme. Nous travaillons donc avec trois piliers - World Class Manufacturing, Digital Factory et Human Centered Organisation – qui mènent à ce que nous appelons une entreprise intelligente.“
“Nous avons lancé ce programme il y a trois ans. Mais nous travaillions déjà sur ces transformations avant. Par exemple, nous avions déjà beaucoup investi dans la numérisation et l‘accent a toujours été mis sur l‘aspect humain. Nous n‘avons donc pas vraiment choisi ces trois piliers, ils étaient plutôt une conséquence logique de la réalité.“
“Si nous examinons ces piliers de près, nous constatons qu‘ils sont fortement imbriqués, avec la qualité comme fil conducteur. Par exemple, nous avons récemment investi massivement dans le parc de machines: nous disposons de 50 machines CNC de pointe et de divers robots sur le lieu de travail. L‘aspect numérique a également été abordé dans ce cycle d‘investissement: des tablettes ont été introduites, le réseau a été étendu et des configurateurs de produit ont été développés. Je voudrais également mentionner l‘expansion des systèmes MES, EMS et WMS. Nous avons également fait des investissements considérables dans les infrastructures et la sécurité. Il est difficile de calculer le retour sur investissement de toutes ces mesures mais elles sont importantes dans l‘esprit des gens. Ceux qui voient leur employeur investir dans de nouvelles toilettes ou un réfectoire savent que cette entreprise est ‘là pour rester‘.“
un container pour rendre la technologie plus accessible
Geert Ostyn: “Aujourd‘hui, nous avons réalisé plusieurs sous-projets autour de cet aspect. Un bon exemple est notre Cube. Une enquête a montré que nos employés avaient de nombreuses questions à propos de la technologie. Par exemple, 85% ignoraient ce qu‘était une imprimante 3D. C‘est pourquoi nous avons cherché un moyen de les familiariser avec ces innovations. Le résultat a été le Cube, un container dans lequel sont présentés une imprimante 3D mais aussi un robot de soins, une application AR/VR, un cobot et un exosquelette. Tout le monde a la possibilité de visiter le Cube pendant les heures de travail. Par souci de clarté, il ne s‘agit pas d‘un outil de formation; il y a certaines de ces technologies que nous n‘utilisons même pas. Par exemple, nous avons testé les exosquelettes mais le projet a été mis en attente pour le moment car nous voulons d‘abord voir quelques ajustements pratiques: par exemple, il faut que le dispositif s‘enlève facilement et qu‘il puisse être réinitialisé rapidement lorsqu‘un autre opérateur commence à l‘utiliser. D‘ici quelques années, il sera probablement utilisable dans notre contexte. Ce processus a-t-il été une perte de temps? Pas du tout. D‘abord, nous avons appris énormément et ensuite, notre personnel sent que nous prenons leur santé à cœur.“
Forums technologiques & V-box
“Nos forums technologiques sont un autre exemple de cet engagement. Une fois l‘investissement réalisé, les opérateurs font une démonstration de la technologie aux collègues intéressés. Chaque session attire environ 30 personnes, dont des employés des ressources humaines ou des finances, par exemple. Cela favorise la compréhension mutuelle et indique que les notions ‘human centered’ et ‘world class manufacturing’ sont fortement imbriquées ici. Un autre bon exemple est la V-box. Dans cette boîte, les employés peuvent discuter de toutes les données pertinentes et récentes. Cela garantit une plus grande interaction mutuelle et permet de prendre les mesures nécessaires de manière réfléchie.
Ce moment a lieu plusieurs fois par jour. Là encore, le retour sur investissement de ce genre de chose est difficile à calculer: dans 80% des cas, la boîte est vide. Si on utilisait les mêmes critères qu‘avec les machines, le retour sur investissement serait lamentable. Mais lorsqu‘on n‘est motivé que par les coûts, on néglige certaines choses importantes.“
Roadmap technologique
On voit souvent Picanol apparaître dans diverses recherches en collaboration avec des organisations comme Flanders Make et les universités.
“Nous suivons les innovations technologiques avec une attention toute particulière. Nous voulons développer une usine numérique et analyser quelles techniques sont les mieux adaptées pour ce vers quoi nous voulons aller. A cet égard, nous parlons en interne d‘une histoire fondamentale ou d‘une histoire clé. Dans une histoire fondamentale, nous développons nous-mêmes la technologie en interne, c‘est ainsi que nous faisons la différence. Avec une histoire clé, d‘autres organisations sont mieux placées pour développer la technologie et nous recherchons des collaborations, comme c‘est le cas dans les projets ICON.“
Comment déterminer?
“L‘innovation a deux approches. Dans le premier cas, un service ressent un besoin et cherche des solutions. La technologie n‘est alors disponible que dans ce département. Souvent, la direction hiérarchique de ce service ne considère pas qu‘il lui incombe d‘étendre cette innovation aux autres services de l‘entreprise. Une deuxième approche consiste à sensibiliser les gens à la technologie, à les faire réfléchir à la manière dont nous pouvons utiliser les innovations. Nous leur montrons alors la technologie dans le Cube. Notre personnel a besoin de sentir qu‘il est autorisé à expérimenter, nous voulons le stimuler en le familiarisant avec la technologie. Les nouvelles générations sont aussi demandeuses et veulent pouvoir expérimenter.“
Production en série avec des exigences spécifiques
“C‘est une question avec laquelle plusieurs entreprises se débattent: quelle technologie utiliser? Nous essayons de maintenir notre portée technologique aussi large que possible afin de pouvoir changer rapidement en cas de besoin. Nous sommes également confrontés à des séries de plus en plus petites. Nous en faisons l‘expérience depuis la crise bancaire de 2008. A cette époque, les entreprises se débattaient avec des liquidités limitées car les stocks étaient bloqués partout. Les leçons que nous en avons tirées sont que nous devons aborder notre réseau de fournisseurs différemment afin de pouvoir réagir rapidement. Nous nous sommes maintenant adaptés à ces gammes plus petites. Nous ne produisons rien pour stocker. Tout ce qui est fabriqué aujourd‘hui part chez le client dans les trois jours. Notre production est structurée de manière à ce que nous n‘ajoutions des caractéristiques spécifiques au client qu‘en fin de chaîne. Ainsi, le prix reste sous contrôle et nous pouvons offrir la valeur ajoutée nécessaire. Le réseau local est également très important pour notre ancrage en Belgique. Sans les universités, les organismes de connaissance et les PME locales, cela serait très difficile. Par exemple, nous sommes très actifs au sein de Flanders Make, où nous collaborons avec d‘autres entreprises. Nous avons aussi des projets en cours avec quatre de nos universités. Cette interaction enrichit le projet. On apprend à connaître d‘autres personnes et d‘autres entreprises, ce qui permet d‘obtenir des résultats immédiats lors de collaborations ultérieures.“