Une découpeuse laser 3D cruciale dans l'élastoformage
Phoenix 3D Metaal choisit la technologie de découpe laser Prima Power
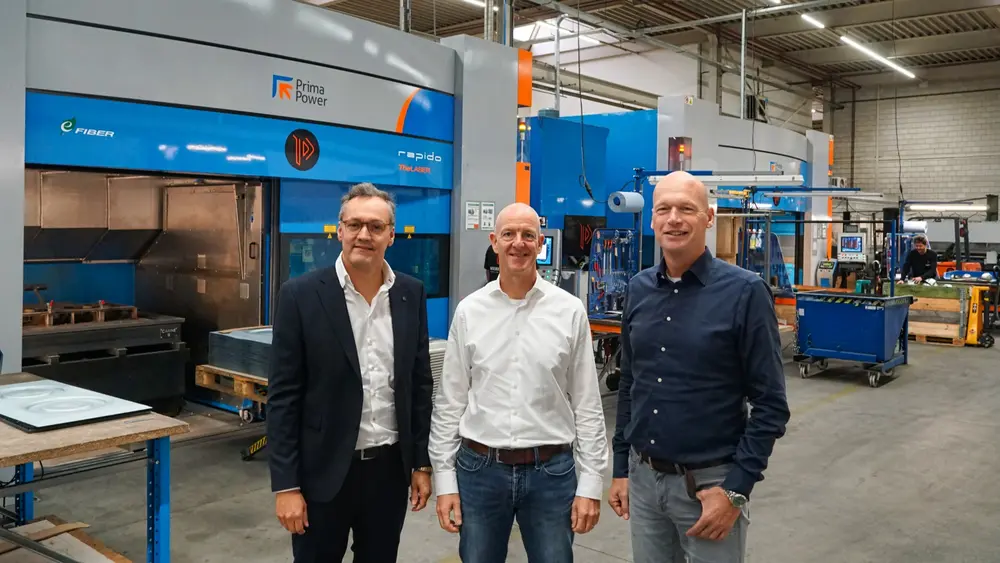
La tôle formée en 3D offre une valeur ajoutée esthétique qui est de plus en plus appréciée dans les produits industriels. Souvent, les ingénieurs l'associent encore à de grandes séries car les presses d'emboutissage nécessitent un 'hard tooling' coûteux. Mais avec les presses d'élastoformage, Phoenix 3D Metaal permet le formage de tôles en 3D pour des petites quantités, par exemple de 300 à 12.000 pièces par an. La découpe laser 3D constitue ici une étape de production indispensable pour l'entreprise d'Eindhoven, une fois que la tôle fine a été mise en forme dans l'une de ses trois presses d'élastoformage.
Presses d'élastoformage
Les pièces qui ornent les murs de la salle de réunion de Phoenix 3D Metaal donnent une bonne idée de la diversité de la clientèle de cette entreprise d'élastoformage. Cela va du revêtement pour des chariots élévateurs à fourche, un robot de fertilisation et des machines à café professionnelles aux plaques de protection de carter et aux boucliers thermiques pour les poids lourds, en passant par les boîtiers pour moniteurs dans des laboratoires. Il y a même un boîtier de flash; ce boîtier provient également de l'usine de tôlerie d'Eindhoven.
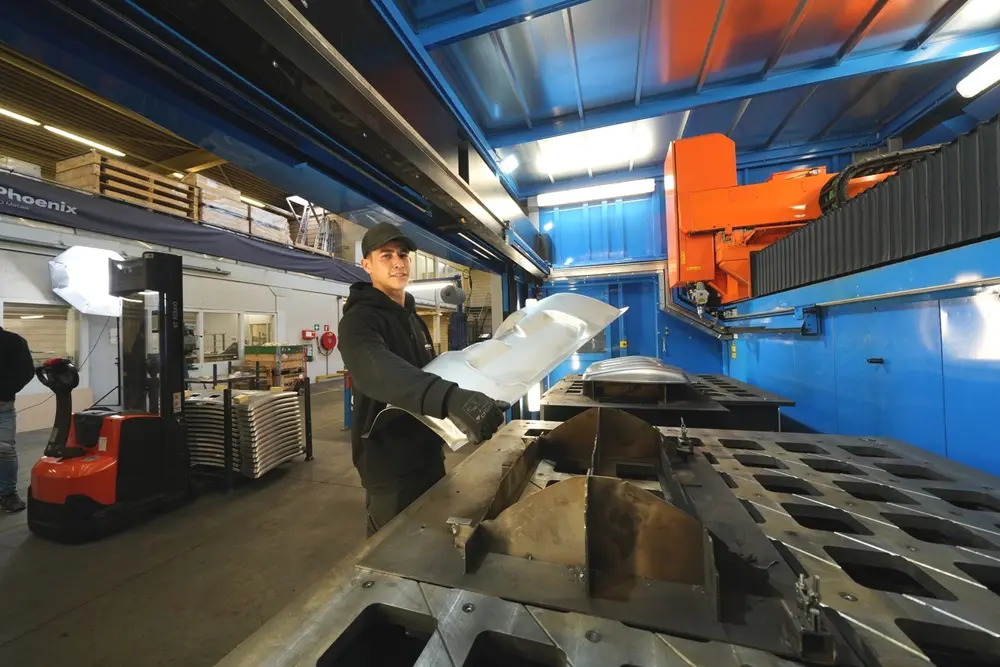
"Une forme en 3D ajoute de la valeur à un produit, en particulier à un produit de haute technologie", explique Jan-Willem van Hooft, propriétaire de Phoenix 3D Metaal avec Bernard van der Poel. Jan-Willem est responsable de la production, tandis que Bernard s'occupe du marketing et des ventes. L'entreprise date de 1960 et se concentre presque entièrement sur les presses d'élastoformage depuis 2010.
Après toutes ces années, il est encore nécessaire d'expliquer cette technique. En effet, elle ne figure pas dans les manuels scolaires et les ingénieurs ne pensent généralement pas en 3D s'ils n'ont pas besoin de grandes quantités de produits.
"Leur nombre est trop faible pour investir dans le hard tooling. En revanche, nous travaillons avec un outillage simple, qui ne nécessite qu'une moitié de moule dans laquelle nous pressons la tôle", explique Bernard van der Poel.
Le tableau des coûts est donc très différent. Chez Phoenix 3D Metaal, les séries vont de 300 à 12.000 pièces par an, avec des dimensions maximales de 1.100 x 2.200 mm. L'épaisseur de la tôle est généralement comprise entre 0,8 et 3 mm; 4 à 5 mm sont parfois possibles. Grâce à des solutions astucieuses, les ingénieurs parviennent à fabriquer des pièces solides, même avec des tôles fines. Si une vache s'assied sur un robot racleur en tôle élastoformée, cette dernière ne cède pas.
Technologie de découpe au laser
L'élastoformage remonte aux années '30 et a été développé pour l'industrie aéronautique. L'ancien propriétaire de Phoenix 3D Metaal a poursuivi le développement de cette technologie en collaboration avec TNO et Fokker.
"En 2010, nous avons pris la décision stratégique de nous concentrer entièrement sur l'élastoformage. Nous disposions alors de toutes les techniques nécessaires en interne", explique Bernard van der Poel. Outre les trois presses d'élastoformage - 8 000 tonnes et deux fois 3.500 tonnes - il s'agit principalement de la technologie de découpe au laser. En effet, la première étape du processus consiste à découper la platine à partir de laquelle le produit est formé. L'étape critique après l'emboutissage du caoutchouc est la découpe au laser de la forme 3D.
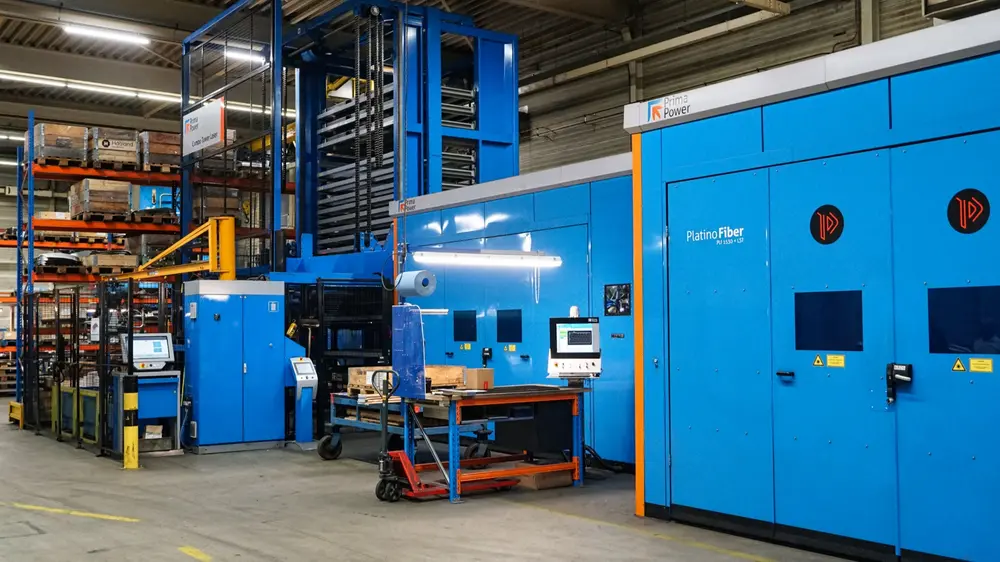
Aujourd'hui, les deux étapes sont réalisées sur des machines de découpe laser de Prima Power. Pour la découpe laser de tôles planes, il s'agit d'une Platino fibre PLTf1530 (4 kW), couplée à un magasin de tôles automatisé et à un robot d'extraction et de tri LST. Ce dernier dépose les pièces découpées (ou finies) une à une sur des palettes. "Il en résulte un processus très stable", explique Jan-Willem van Hooft. "Chaque matin, les produits découpés sont prêts."
L'empilage des produits semi-finis sur une palette est effectué par la LST d'une manière spéciale. En fait, chaque pièce de tôle suivante est décalée de 5 mm par rapport à la précédente. Cela permet aux opérateurs des presses d'élastoformage et des presses plieuses de saisir plus facilement les pièces.
Lasers 3D Rapido
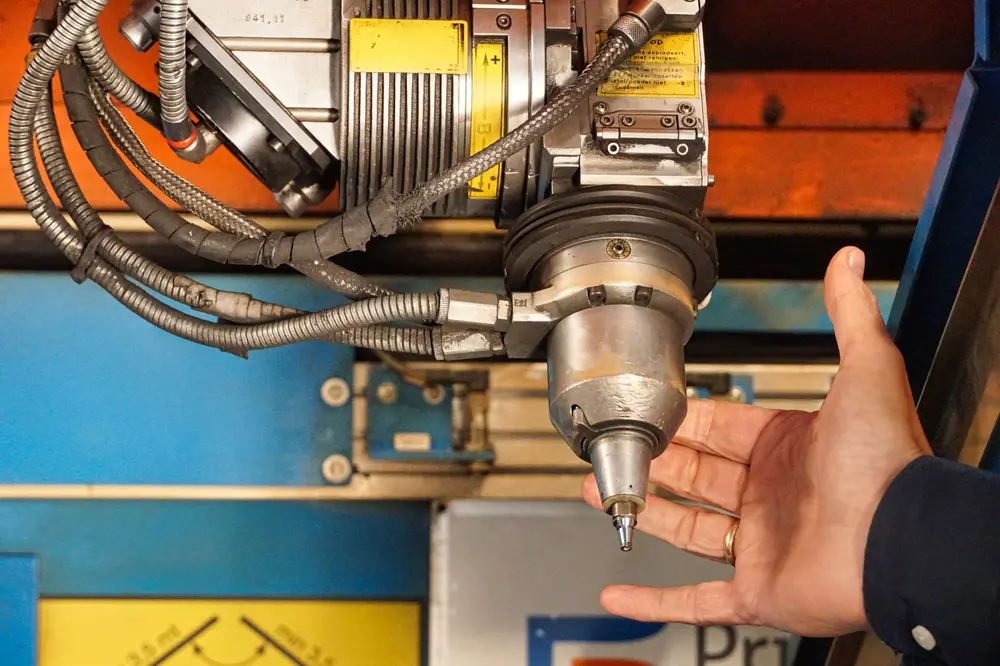
Il y a cinq ans, Phoenix 3D Metaal a acheté sa première machine de découpe laser 3D: la Rapido de Prima Power en version split cabin. Cela signifie que dans une cabine, l'opérateur retire le produit découpé et place un nouveau produit semi-fini dans le gabarit de serrage, tandis que le laser Rapido de 3 kW découpe dans l'autre cabine. La cloison peut être facilement retirée si l'on souhaite découper des produits de grande taille.
Tous les produits sont découpés avec une précision de 0,1 mm. Comme il s'agit de petites séries, la machine de découpe laser 3D est modifiée jusqu'à quatre fois en une journée. Cette transformation est rapide grâce à la numérotation des trous dans la table de découpe où est positionné le gabarit de serrage.
Le passage du laser CO2 au laser à fibre a non seulement permis de réaliser des économies d'énergie substantielles, mais également entraîné une augmentation considérable de la capacité. "Dès les premières semaines, nous avons été surpris par les performances de la machine, sa précision, le positionnement des moules et la vitesse de coupe", déclare Jan-Willem van Hooft.
Pour lui, l'accouplement magnétique de la tête de coupe est un détail important. En cas de crash, la tête peut se déplacer librement et il n'y a pas de dommages permanents, entraînant des coûts et des temps d'arrêt imprévus. "Il suffit de remettre la tête en place puis de la calibrer si nécessaire et on peut ensuite recommencer à découper", explique-t-il.
Capacité de coupe supplémentaire
L'année dernière, Phoenix 3D Metaal a constaté un manque de capacité de découpe laser. Le fournisseur veut toujours être en mesure de livrer à temps et souhaite donc disposer d'une capacité excédentaire. "Nous avons alors sérieusement réfléchi à l'achat d'une deuxième machine de découpe laser 3D", explique Jan-Willem van Hooft. Finalement, le choix s'est porté sur la même machine de découpe laser 3D Rapido 3kW avec split cabin.
"Nous ne voulions pas prendre de risque et être sûrs d'avoir une bonne machine et un bon partenaire. La collaboration avec Prima Power se passe très bien, ce sont des machines compactes qui ont été rapidement opérationnelles. Pendant un certain temps, nous avons envisagé d'acheter la Laser Next de Prima Power, la version la plus rapide. "Mais nous devons souvent transformer notre machine; le temps réel de découpe au laser est moins important pour nous. La valeur ajoutée de ce genre de Formule 1 ne nous intéressait donc pas".
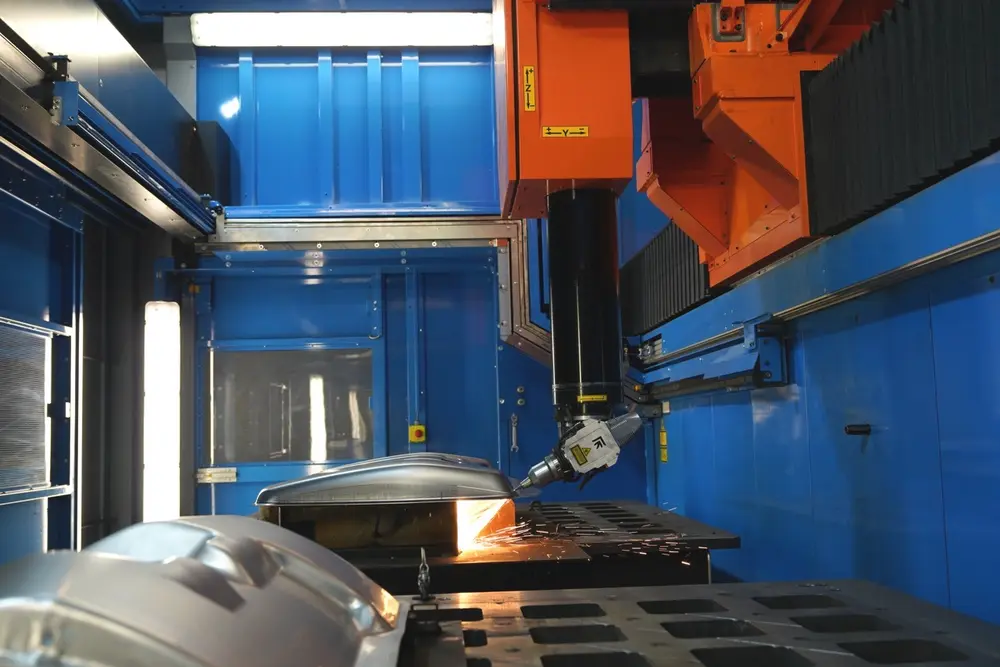
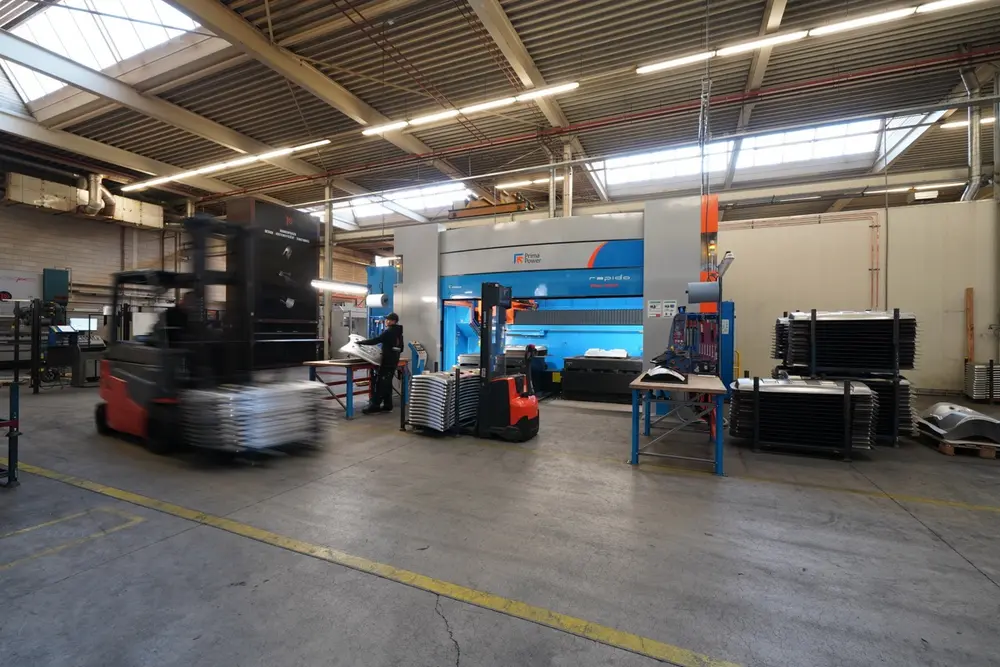
Franky Van Semmertier, directeur de Prima Power Benelux, estime que c'est une bonne décision. "La Laser Next prend tout son sens dans l'industrie automobile, où chaque seconde compte. Ici, cette vitesse ne fait pas le poids face à deux machines identiques, où l'on ne doit plus penser à la programmation et à la commande."
De plus, les opérateurs peuvent désormais passer facilement d'une machine à l'autre. Le logiciel convivial de Prima Power Rapido a également joué un rôle dans la décision, tout comme le faible temps d'arrêt de la première machine. Selon Franky Van Semmertier, l'expérience de Prima Power dans le domaine de l'automobile, qui remonte aux années 1970, se vérifie ici. "Les temps d'installation et d'immobilisation doivent être courts", explique-t-il.