3D-lasersnijmachine cruciale stap in rubberpersproces
Phoenix 3D Metaal kiest voor lasersnijtechnologie van Prima Power
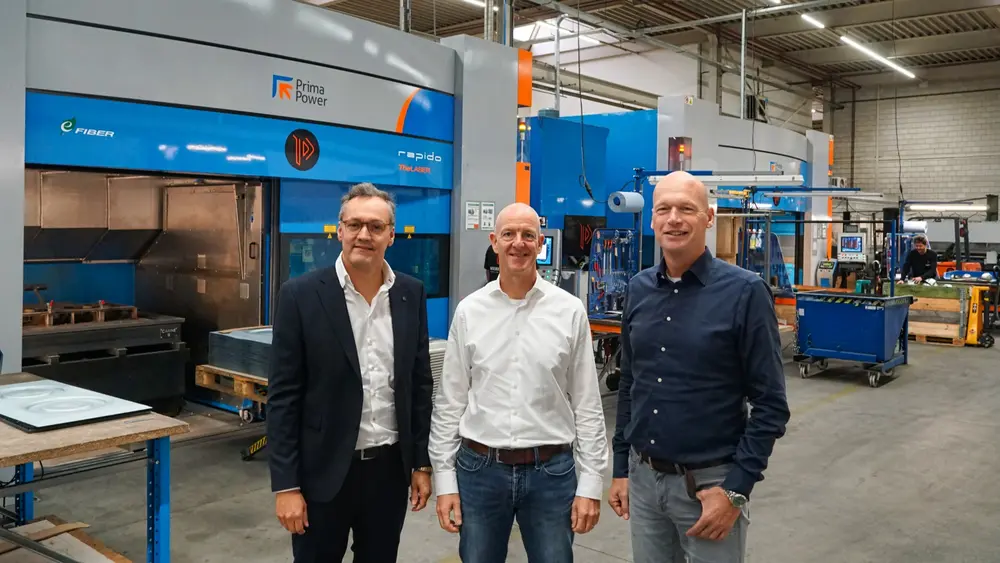
3D-gevormd plaatwerk biedt een esthetische meerwaarde die ook in industriële producten steeds meer gewaardeerd wordt. Dikwijls associëren engineers dit nog met grote series, omdat dieptrekpersen dure 'hard tooling' vereist. Met rubberpersen maakt Phoenix 3D Metaal het driedimensioneel vormen van plaat echter ook haalbaar voor kleinere aantallen. 3D-lasersnijden is voor het Eindhovense bedrijf een onmisbare productiestap nadat de dunne plaat in een van de drie rubberpersen zijn vorm heeft gekregen.
Rubberpersen
De werkstukken langs de wanden van de vergaderruimte bij Phoenix 3D Metaal geven een goed beeld hoe gevarieerd het klantenbestand van het rubberpersbedrijf is. Het gaat van beplating voor heftrucks, een mestrobot en professionele koffieautomaten tot carter beschermplaten en hitteschilden voor zware vrachtwagens en behuizingen voor monitoren in laboratoria. Er staat zelfs een flitskast; ook deze behuizing komt uit de Eindhovense plaatwerkfabriek.
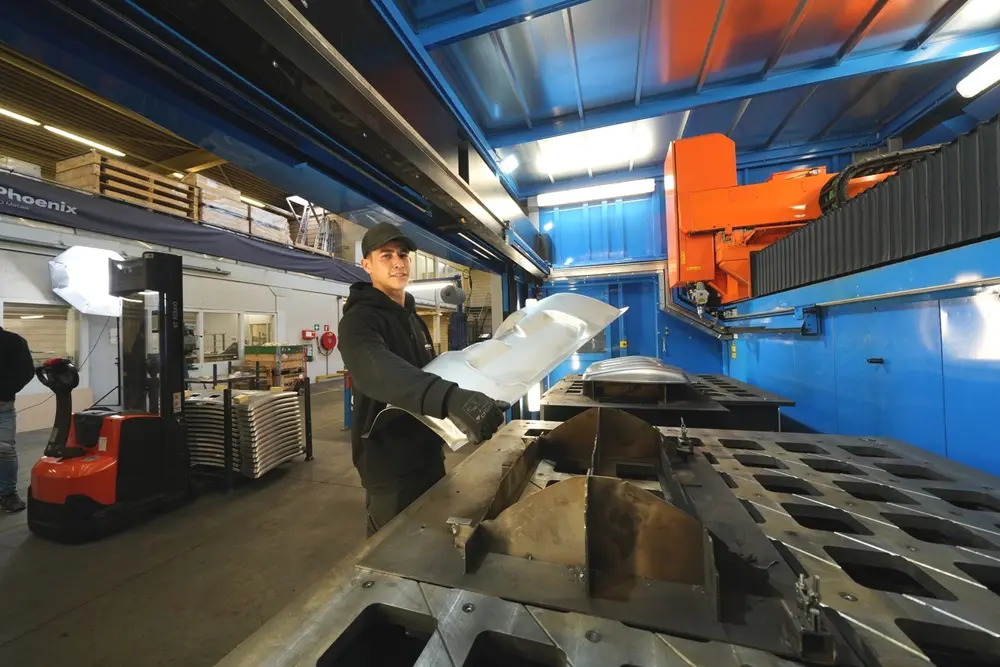
"Een 3D-vorm geeft meerwaarde aan een product, zeker een hightech product", stelt Jan-Willem van Hooft, die samen met Bernard van der Poel eigenaar is van Phoenix 3D Metaal. Jan-Willem is verantwoordelijk voor de productie, Bernard ontfermt zich over de marketing en sales. Het bedrijf stamt uit 1960 en richt zich sinds 2010 nagenoeg volledig op rubberpersen.
Na al die jaren is het nog steeds nodig om deze techniek uit te leggen. Ze staat immers niet in de studieboeken en engineers denken doorgaans niet in 3D als er geen grote aantallen van hun producten nodig zijn.
"Hun aantallen zijn te gering om de investering in hard tooling te kunnen doen. Wij werken echter met eenvoudige gereedschappen, waarbij je slechts één matrijshelft nodig hebt waar we de plaat in persen", aldus Bernard van der Poel.
Hierdoor ziet het kostenplaatje er heel anders uit. De seriegroottes bij Phoenix 3D Metaal lopen uiteen van pakweg 300 tot 12.000 stuks per jaar, met een maximaal formaat van 1.100 bij 2.200 mm. Meestal is de plaat tussen de 0,8 en 3 mm dik; 4 à 5 mm kan soms ook. Met slimme oplossingen weten de engineers ook met de dunne plaat sterke werkstukken te maken. Soms gaat een koe pardoes op de mestrobot zitten, maar dan geeft het rubbergeperste plaatwerk geen krimp.
Lasersnijtechnologie
Het rubberpersen stamt uit de jaren dertig en is ontwikkeld voor de luchtvaartindustrie. De vorige eigenaar van Phoenix 3D Metaal heeft de techniek samen met TNO en Fokker doorontwikkeld.
"In 2010 hebben we de strategische keuze gemaakt om ons volledig op rubberpersen toe te leggen. We hadden toen alle technieken daarvoor in huis", zegt Bernard van der Poel. Naast de drie rubberpersen – 8.000 ton en twee keer 3.500 ton – gaat het dan vooral om lasersnijtechnologie. De eerste stap in het proces is namelijk het snijden van de platine waaruit het product geperst wordt. De kritische stap na het rubberpersen is het lasersnijden van de 3D-vorm.
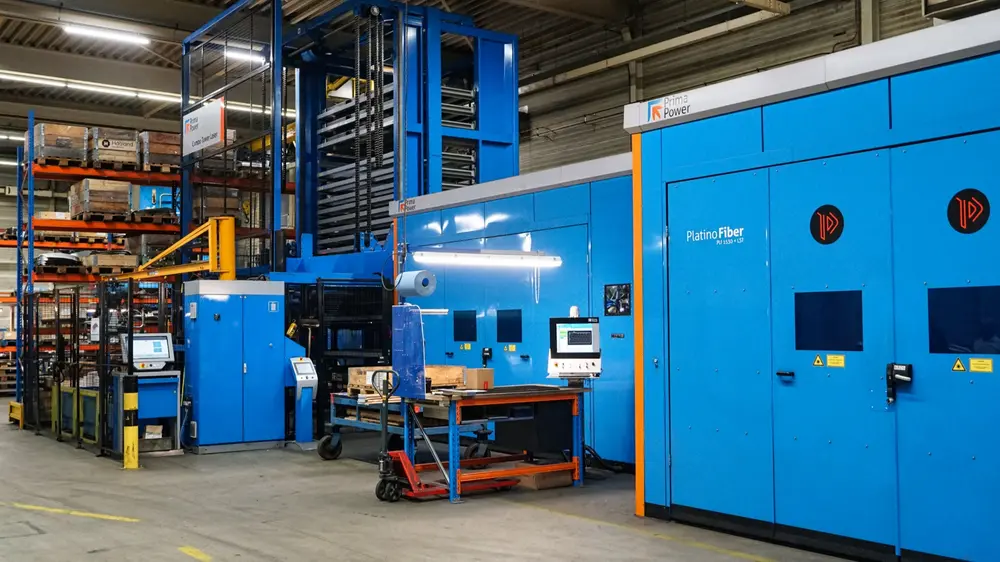
Tegenwoordig gebeuren beide stappen op lasersnijmachines van Prima Power. Voor het lasersnijden van de vlakke plaat gaat het om een Platino fiber PLTf1530 (4 kW), gekoppeld aan een geautomatiseerd plaatmagazijn en een LST uitneem- en sorteerrobot. Deze legt de gesneden (of afgewerkte) stukken een voor een weg op pallets. "Dit resulteert in een heel stabiel proces", legt Jan-Willem van Hooft uit. "Elke ochtend liggen de uitgesneden producten klaar."
Het stacken van de halffabricaten op een pallet doet de LST op een bijzondere wijze. Elk volgend plaatdeel wordt namelijk telkens 5 mm verschoven ten opzichte van het vorige. Hierdoor kunnen de operators aan de rubberpersen en kantbanken de stukken makkelijker pakken.
Rapido 3D-lasers
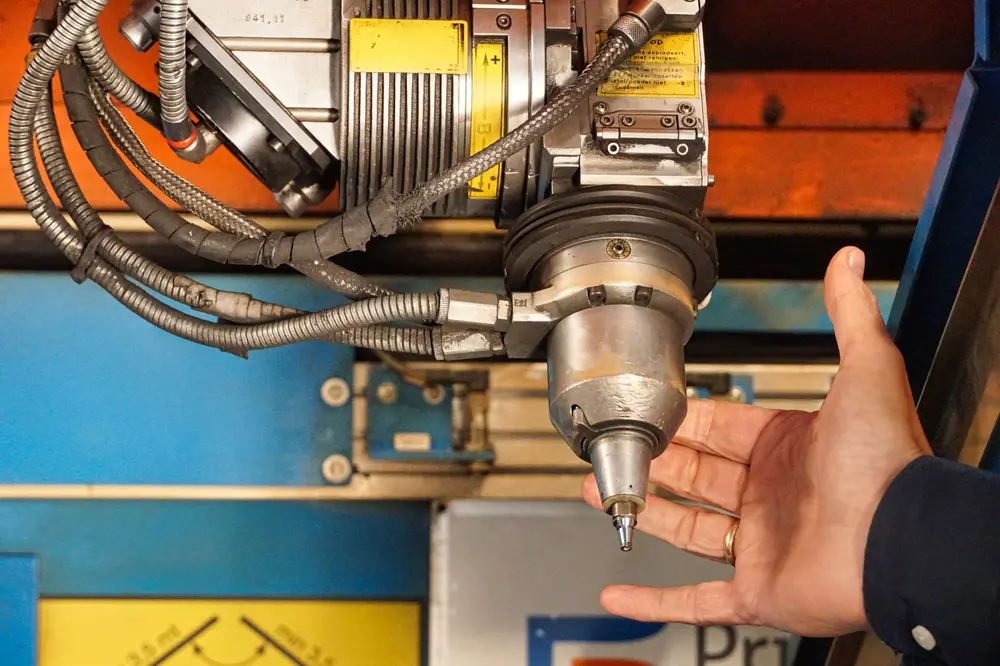
Vijf jaar geleden schafte Phoenix 3D Metaal haar eerste 3D-lasersnijmachine aan: de Rapido van Prima Power in een split cabin versie. Dit betekent dat de operator in één cabine het gesneden product uitneemt en een nieuw halffabricaat in de opspanmal legt, terwijl de 3 kW Rapido laser in de andere cabine snijdt. De tussenwand kan eveneens gemakkelijk verwijderd worden indien er grote producten gesneden moeten worden.
Alle producten worden met een nauwkeurigheid van 0,1 mm gesneden. Omdat het om kleine series gaat, wordt de 3D-lasersnijmachine wel tot vier keer op een dag omgebouwd. Dankzij het genummerde gatenpatroon in de snijtafel waar de opspanmal in gepositioneerd wordt, verloopt dit ombouwen snel.
De overstap van CO2-laser naar fiberlaser heeft niet alleen een forse energiebesparing opgeleverd, maar bracht ook fors meer capaciteit met zich mee. "De eerste weken waren we verbaasd over de prestaties van de machine, de nauwkeurigheid, het positioneren van de mallen en de snijsnelheid", zegt Jan-Willem van Hooft.
Een belangrijk detail vindt hij de magneetkoppeling in de snijkop. Bij een eventuele crash kan deze vrij bewegen en ontstaat er geen blijvende schade met de daarbij horende kosten en ongeplande stilstand. "Je klikt de kop terug, kalibreert deze eventueel en je kunt weer snijden."
Extra snijcapaciteit
Vorig jaar merkte Phoenix 3D Metaal dat er te weinig lasersnijcapaciteit was. De toeleverancier wil altijd op tijd kunnen leveren en wil daarom overcapaciteit. "We hebben toen serieus nagedacht in welke tweede 3D-lasersnijmachine we zouden investeren", zegt Jan-Willem van Hooft. Uiteindelijk is gekozen voor exact dezelfde Rapido 3 kW 3D-lasersnijmachine met split cabin.
"We wilden geen risico nemen en zeker zijn van een goede machine en partner. De samenwerking met Prima Power verloopt heel goed, het zijn compacte machines die snel up and running waren." Even is wel overwogen om de Laser Next van Prima Power te kopen, de snellere versie. "Wij moeten echter vaak ombouwen; de echte lasersnijtijd is voor ons minder belangrijk. De meerwaarde van zo’n Formule 1-variant was er voor ons dan ook niet", klinkt het.
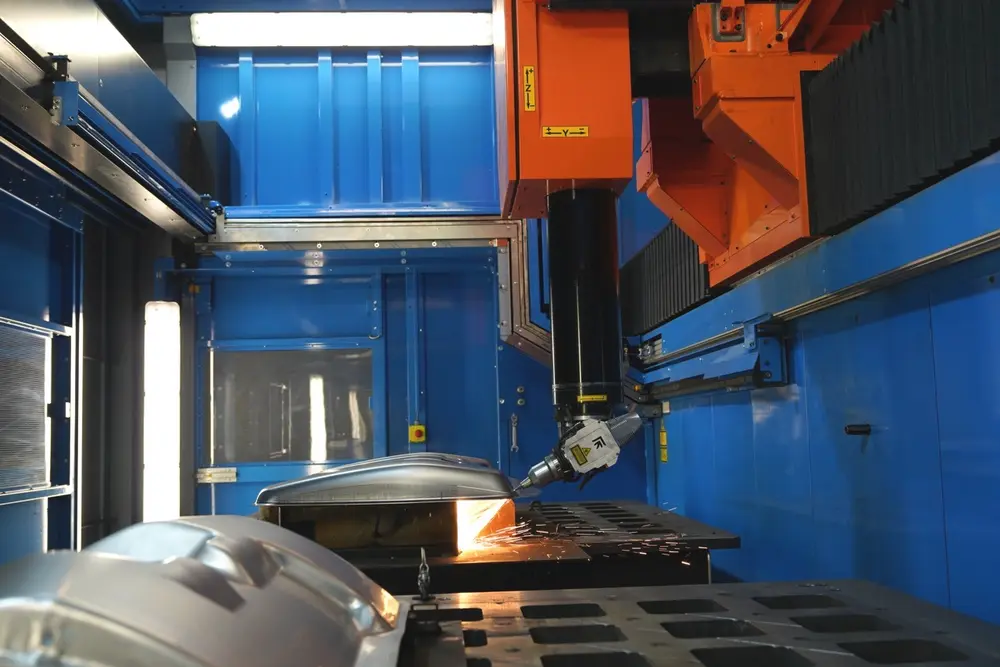
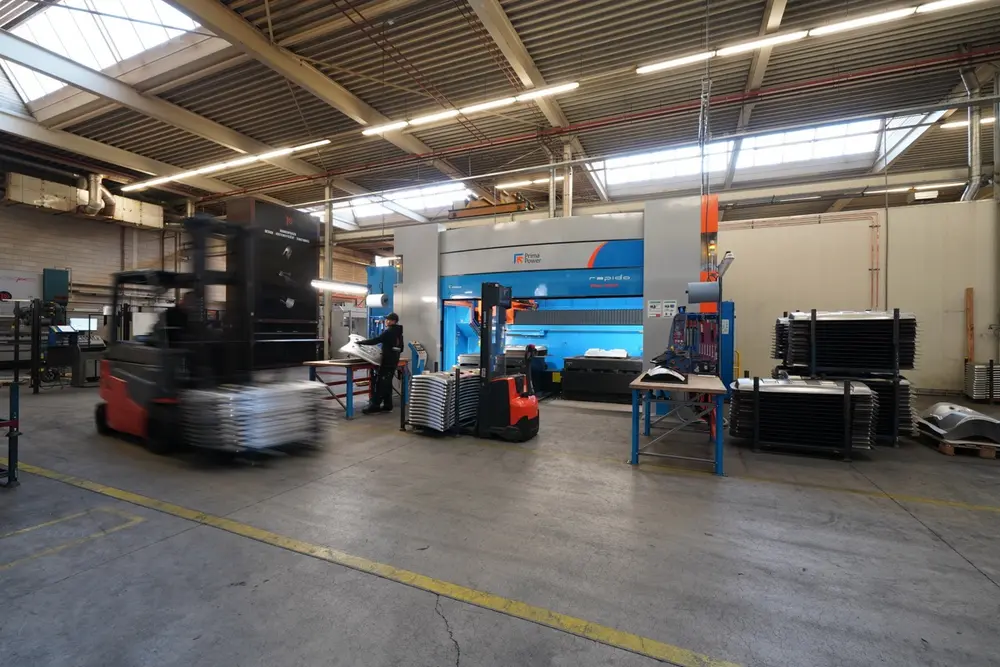
Een correcte beslissing, vindt Franky Van Semmertier, directeur Prima Power Benelux. "De Laser Next komt goed tot zijn recht in de automotive industrie, waar elke seconde telt. Die snelheid weegt hier niet op tegen twee identieke machines, waarbij je niet meer hoeft na te denken over programmering en bediening."
Nu kunnen operators bovendien makkelijk wisselen van de ene naar de andere machine. Ook de gebruiksvriendelijke software van Prima Power Rapido heeft meegespeeld in de beslissing, net als de geringe downtime van de eerste machine. Volgens Franky Van Semmertier bewijst zich hier de automotive-ervaring van Prima Power, die al uit de jaren zeventig stamt. "Steltijd en downtime moeten daar kort zijn."