Sneller en efficiënter verpakkingen stapelen met palletizers
Keuze voor specifiek type hangt af van product en capaciteit
Het stapelen van verpakkingen in een vast patroon op een pallet is een repetitieve en belastende taak, ook binnen de voedingsindustrie. Palletizers maken het mogelijk om dit werk uit handen van de werknemers te nemen en het sneller en efficiënter uit te voeren. Er zijn echter heel wat types palletizers en de keuze voor een bepaalde variant hangt volledig af van de specifieke productienoden.
What's in a name?
Er zijn grosso modo vier soorten palletizers, met elk hun eigen functies en voor- en nadelen. Ze hebben wel allemaal gemeenschappelijk dat ze aan het einde van het productieproces worden ingeschakeld, om daar reeds verpakte producten te stapelen. Let wel: dit doen ze niet per se sneller dan de mens. Sommige palletizers - zoals layer-palletizers - gaan tot 2.400 zakken per uur, wat onhaalbaar is voor een arbeider om uren aan een stuk vol te houden, maar andere types - zoals een cobot - opereren aan veel lagere snelheden. Dé grootste troef van de palletizer is dus het uitsparen van moeilijk te vinden personeel.
Layer-palletizer
De layer-palletizer is een bijzonder populaire keuze. De machine heeft een min of meer vierkante voetafdruk en neemt via een transportband verpakkingen langs de ene kant in. Deze worden meestal via deze band naar de bovenkant van de palletizer gevoerd om daar in een vast patroon een enkele laag te vormen. Alternatief worden de verpakkingen onderaan aangevoerd en daarna omhoog gebracht via een lift.
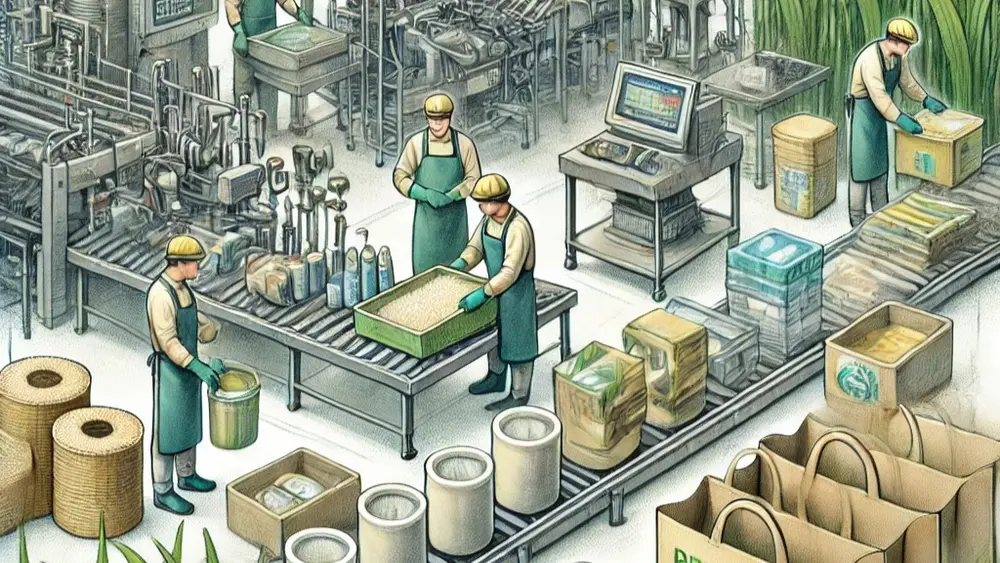
Niet alle palletizers stapelen sneller dan de mens; dit is ook niet altijd nodig
Het basisprincipe blijft evenwel steeds hetzelfde: een voorgevormde laag - een patroon dat makkelijk vooraf kan ingesteld worden met de meegeleverde software - wordt vooruitgeschoven en vervolgens gedropt op de pallet die daar net onder aan het wachten was. Vervolgens zakt de pallet een beetje, waarna de volgende laag erop gelegd wordt, enzovoort. Zo wordt de pallet laag per laag aangevuld en dit aan bijzonder hoge snelheden omdat er niet per verpakking wordt gewerkt. Dit type palletizer dient dan ook vooral voor dozen - hoewel sommige fabrikanten ook varianten voor zakken maken - die aan hoge snelheid moeten gestapeld worden.
Layer-palletizers werden vroeger doorgaans aan slechts één productielijn gekoppeld, juist omdat er niet per product maar per laag wordt gewerkt. Wanneer er toch meerdere lijnen een palletizer nodig hebben, maar de capaciteit een afzonderlijke palletizer per lijn overbodig maakt, wordt er soms met bufferzones gewerkt. Tussen de aanvoerband en de palletizer worden op de rollenbanden telkens een aantal verpakkingen ter waarde van één pallet gebufferd. Wanneer de vorige pallet volledig klaar is, wordt de volgende lading uit de bufferzone naar de palletizer gestuurd en daar laag per laag op de volgende pallet geplaatst. Op deze manier krijgt de layer-palletizer toch extra flexibiliteit in het verwerken van verschillende producten.
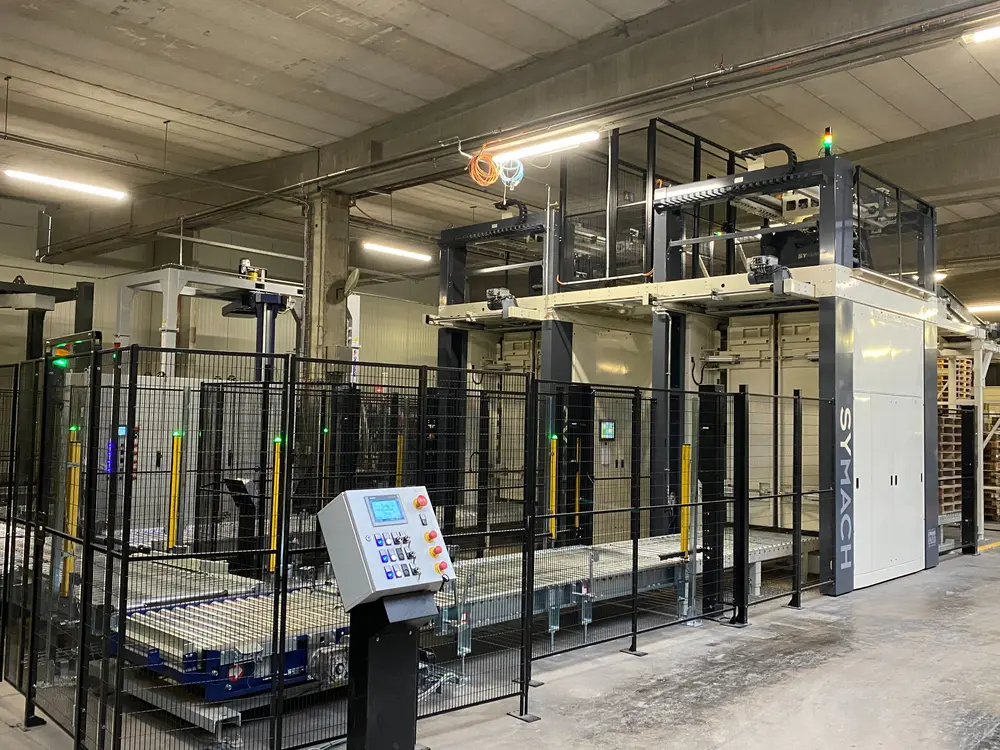
Portaalrobot
Bij een portaalrobot zijn er verschillende configuraties mogelijk, waarbij de pallet zowel handmatig of volledig automatisch kan aan- en afgevoerd worden. Om maximale continuïteit en snelheid te garanderen, wordt er vaak gekozen voor een opstelling waarbij twee pallets klaar staan om te vullen. Nadat de eerste vol is en er aan de tweede wordt begonnen, wordt de eerste afgevoerd en wordt er daar een lege geplaatst, die daarna dan aan de beurt is.
Het werkingsprincipe blijft ook hier steeds hetzelfde: het gaat om een grijper of klem die boven de verpakking(en) beweegt, zich correct situeert en vervolgens neerkomt om de verpakking vast te nemen. Daarna maakt de robot een beweging om de verpakking(en) op de correcte plaats boven de pallet te positioneren om ze daarna weer neer te zetten. Dit kan object per object gebeuren, maar afhankelijk van het gewicht en het soort verpakking - bv. een doos of een tray - is het mogelijk om er meerdere tegelijk op te nemen. De beweging van de grijper of klem kan zodanig ingesteld worden om de versnelling geleidelijker te maken, wat de integriteit van de verpakking kan beschermen.
Alles staat of valt bij dit tweede type met de grijper of klem die gekozen wordt. Dit instrument bepaalt wat de palletizer kan verwerken; niet alleen het type product, maar ook het aantal per cyclus. Een doos vereist een geheel ander soort grijper dan een emmer. Gelukkig bestaan er tegenwoordig toolchangers die automatisch tussen verschillende grijpers wisselen. Zo kan er - mits enige stilstand - toch vrij vlug van type te stapelen product veranderd worden.
Verder is een grote troef van de portaalrobot de enorme schaalbaarheid van dergelijke installatie. Ze kan zo hoog, breed en diep als gewenst gemaakt worden. Vaak is het efficiënter om per één of twee lijnen een aparte portaalrobot te voorzien, om zo de capaciteit van de lijn te kunnen volgen. Er moet immers steeds rekening gehouden worden met de cyclustijd van de robot. Hoe breder het traject, hoe langer het duurt vooraleer de grijper ergens is.
Knikarmrobot
Hier gaat het meestal om een variant op de klassieke 6-assige robot, waarbij er vaak maar 4 of 5 assen vereist zijn. De robot werkt hierbij in een cirkelvormig gebied rond zijn installatiepunt om verpakkingen op te nemen en weer neer te zetten. Ook hier is de specifieke grijper of klem cruciaal, want dit bepaalt welk object juist kan vastgenomen worden. Uiteraard zijn er hier eveneens toolchangers beschikbaar.
De knikarmrobot heeft een aantal nadelen. Zo is het werkgebied van dit type vrij groot ten opzichte van de andere types. Aangezien er een hekwerk rond de robot moet staan om aan hogere snelheden te kunnen werken, neemt deze installatie - die niet direct boven de lading hangt maar wel van de zijkant komt - veel plaats in. Daarnaast is de snelheid beperkt ten opzichte van de vorige twee types. De objecten worden gewoonlijk per stuk of per twee of drie verplaatst, waarbij elke keer een volledige cyclus nodig is om een gedeelte van de stapellaag aan te vullen.
Dit nadeel zorgt echter meteen voor een voordeel: meer flexibiliteit. Net als een portaalrobot kan een armvormige robot makkelijk afwisselen tussen verschillende producten. Afhankelijk van de benodigde grijper kan er gewerkt worden met verschillende lijnen, waarbij de verpakking gescand wordt en vervolgens op de correcte pallet geplaatst wordt. Door de grotere reikwijdte is het zo mogelijk om meerdere pallets aan te vullen. Bovendien kunnen de verpakkingen makkelijk georiënteerd worden.
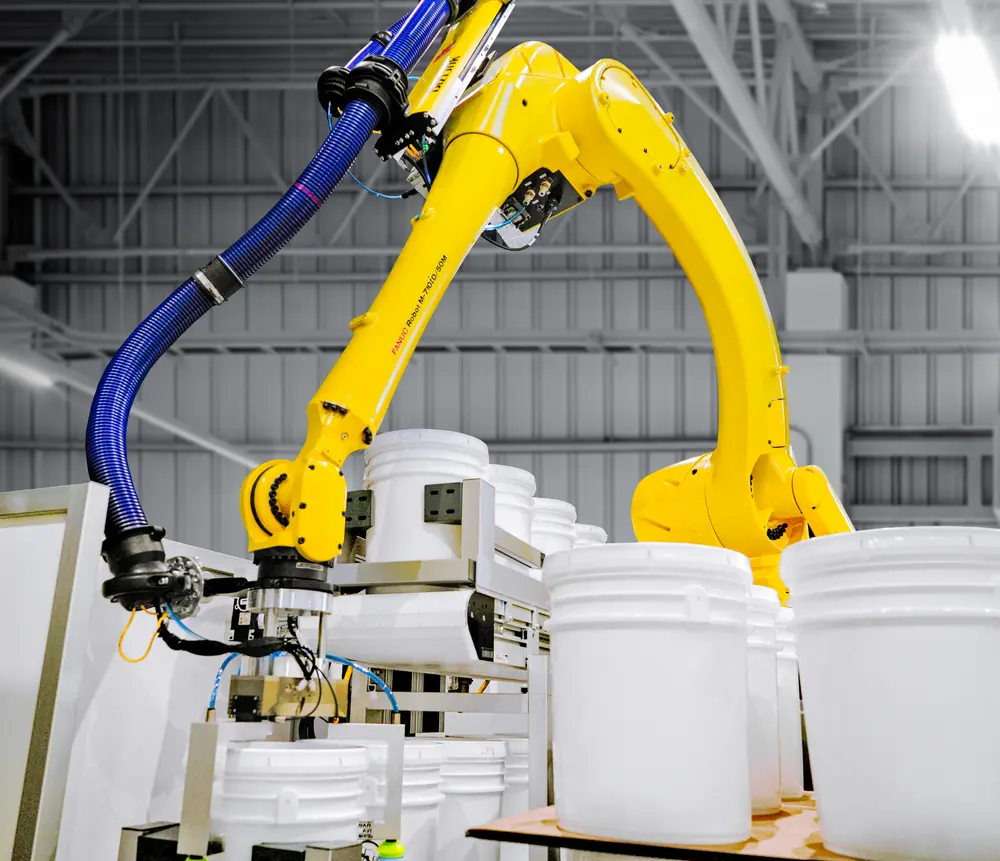
Cobot
Een cobot zal in principe op dezelfde manier werken als de knikarmrobot, maar dan niet omheind en dus met lagere gewichten en aan lagere snelheden om toch veilig te blijven. Het gewicht is evenwel niet echt een euvel: veel cobots mogen en kunnen ondertussen tot 30 kg manipuleren, wat meer dan genoeg is voor de meeste voedingsverpakkingen.
Veiligheid blijft het belangrijkste gespreksonderwerp bij cobots. Zo zijn er allerlei mechanismen nodig om de installatie veilig te maken. Denk maar aan sensoren die voelen wanneer de machine iets of iemand aanraakt of wanneer iemand te dicht komt. Het gevolg van dit alles is dat een cobot erg traag zal werken om toch nog veilig te zijn. Het is dus maar de vraag wanneer een cobot echt rendeert voor palletiseren. Bovendien moet de volledige cobot-installatie gekeurd worden om veilig te zijn, én moet dit proces bij elke substantiële wijziging herhaald worden. Het stapelen van een ander product vergt dus meteen weer een nieuwe risicoanalyse.
Keuzefactoren
Het bepalen van de geschikte palletizer hangt in de eerste plaats af van het type product en de capaciteit dat de palletizer moet halen. De aangehaalde types zijn hierbij gerangschikt volgens afnemende snelheid. Wanneer u een trage productielijn heeft met bv. maar één doos per minuut, heeft het geen zin om een layer-palletizer aan te schaffen. Grosso modo zijn de snellere types ook duurder.
Uiteindelijk moet de palletizer volledig afgesteld zijn op de productie in kwestie om echt te renderen
Een ander criterium is dus het type te stapelen product. Veel fabrikanten leggen zich dan ook maar toe op één bepaald type, zoals dozen. Anderen kiezen voor een bredere aanpak en richten zich ook op zakken en emmers. Vooral zakken zijn lastige objecten omdat ze van vorm kunnen veranderen. Ook emmers kunnen deels ingedrukt worden en vereisen dus bijzondere aandacht. Wanneer u constant en aan snel tempo gelijkaardige dozen moet stapelen, zal een layer-palletizer waarschijnlijk de beste keuze zijn. Bij een breder gamma aan producten en aan lagere snelheden geniet een knikarmrobot vaak de voorkeur.
Uiteindelijk moet de palletizer volledig afgesteld zijn op de productie in kwestie om echt te renderen. Het aantal lijnen, de productiesnelheid en het type verpakking zijn hierbij de belangrijkste factoren. Er is echter nog een ogenschijnlijk banaal criterium: de beschikbare plaats. Zoals gezegd nemen sommige types, zoals de knikarmrobot maar ook de layer-palletizer, meer plaats in dan andere. Vergeet niet om hierbij een marge te berekenen voor de benodigde veiligheid en het te plegen onderhoud.
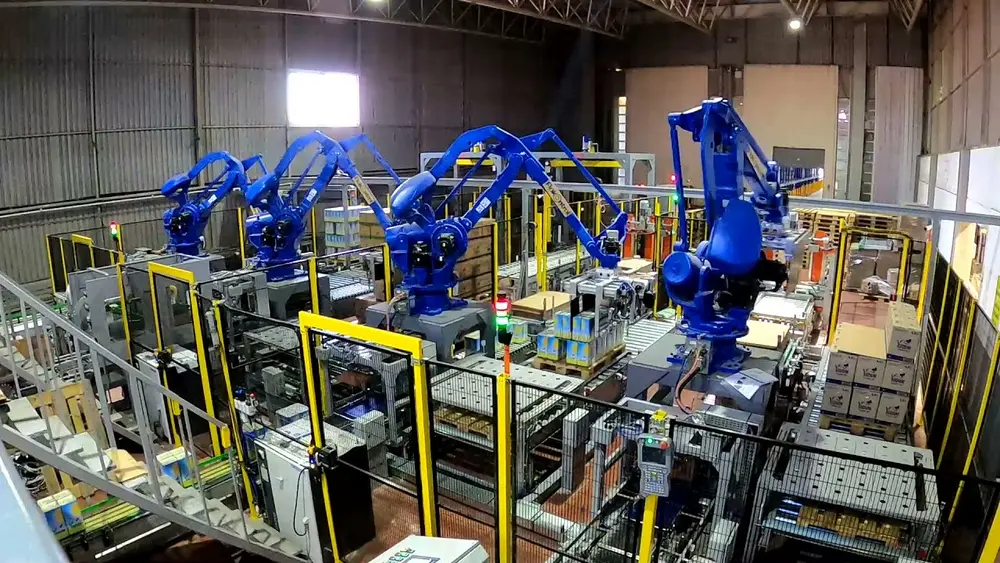
Toepassing in food
Bij toepassingen in de voedingssector denkt men in de eerste plaats altijd aan hygiëne als onderscheidende factor. Dat is ook hier zo, maar de ervaring leert dat niet elke eindgebruiker daar even hard mee bezig is. Zo gaat het om het verhandelen van verpakte voeding in een omgeving waar vaak niet effectief geproduceerd wordt, met weinig kans op interactie tussen product en machine.
Uitzonderingen hierop zijn verpakkingen zoals die voor aardappelen of wortels: men werkt hier vaak deels met netten. In deze gevallen zal men dan ook sneller voor hygiënischere oplossingen kiezen. Denk dan aan palletizers (deels) in rvs of die gesmeerd zijn met foodgrade smeermiddelen. Reinigbaar en hygiënisch ontwerp van de palletizer is sowieso een standaard geworden binnen deze sector. Fabrikanten hebben de laatste jaren gemerkt dat de zorg voor voedselveiligheid een pak is toegenomen onder de eindgebruikers.
Een situatie eigen aan voeding is de nood om in zeer koude temperaturen te stapelen. Zo zijn er bepaalde producten - zoals viennoiserie en roomijs - die maar heel kort in warmere omgevingen mogen staan. Een oplossing hier is om de volledige palletizer bestand te maken tegen de koude, wat vrij prijzig is. Een alternatief is om de rest van het logistieke traject in een koele omgeving te plaatsen en de palletizer in een 'normale' kamer ertussenin, zodat de blootstelling aan hogere temperaturen uiterst beperkt blijft. Uiteraard hangt dit alles af van het product in kwestie en de productiesnelheid.
Met medewerking van Alphatech, Ausloos Verpakkingstechniek, Engisol, Fanuc, Montech, Scott Automation, SigmaControl, Symach en Yaskawa