Les palettiseurs permettent d'empiler les paquets plus rapidement et plus efficacement
Le choix du modèle spécifique dépend du produit et de la capacité
Empiler des paquets selon un schéma fixe sur une palette est une tâche répétitive et stressante, également dans l'industrie alimentaire. Les palettiseurs permettent de soulager les travailleurs de cette tâche et de l'effectuer plus rapidement et plus efficacement. Toutefois, il existe de nombreux types de palettiseurs et le choix de l'un d'entre eux dépend entièrement des besoins spécifiques de la production.
What's in a name?
Il existe environ quatre types de palettiseurs, chacun ayant ses propres fonctions, avantages et inconvénients. Leur point commun est qu'ils sont utilisés à la fin du processus de production, pour y empiler des produits déjà emballés. Il faut savoir que ces appareils ne travaillent pas forcément plus vite que les humains. Certains palettiseurs, tels que les palettiseurs à couches, peuvent traiter jusqu'à 2.400 sacs par heure, un rythme impossible à tenir pendant plusieurs heures pour un travailleur. Mais d'autres modèles, tels que les cobots, fonctionnent à des vitesses beaucoup plus lentes. Le plus gros atout du palettiseur est donc qu'il permet d'épargner le personnel, qui est si difficile à trouver.
Palettiseur à couches
Le palettiseur à couches est un choix particulièrement populaire. Il a une surface au sol plus ou moins carrée et attrape les paquets d'un côté via un convoyeur. Ces paquets sont généralement acheminés par cette bande transporteuse vers le haut du palettiseur pour former une seule couche selon un schéma déterminé. Il est également possible d'introduire les paquets par le bas et de les soulever au moyen d'un ascenseur.
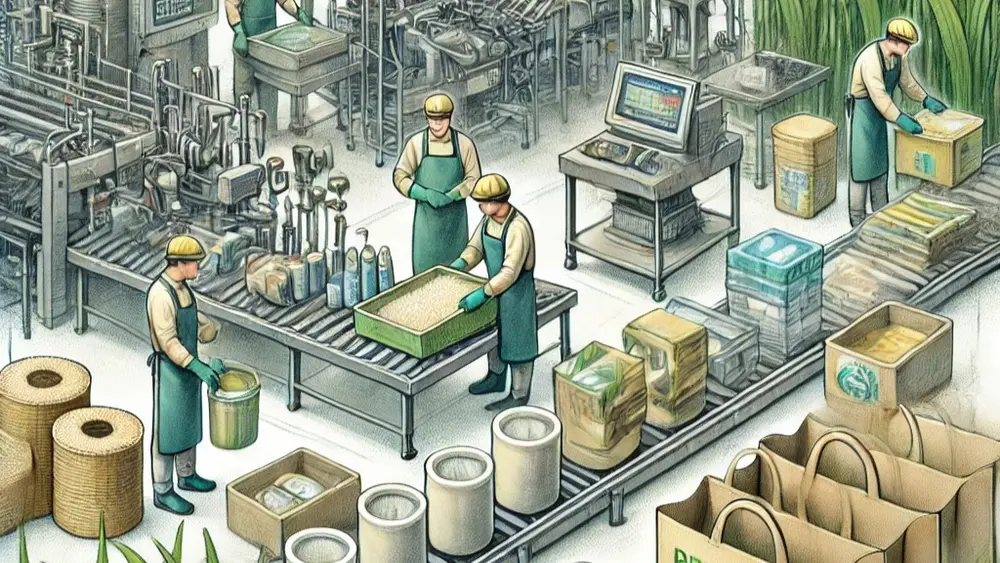
Tous les palettiseurs n'empilent pas plus vite que les humains; et d'ailleurs, ce n'est pas toujours nécessaire
Cependant, le principe de base reste toujours le même: une couche préformée - un schéma qui peut facilement être prédéfini à l'aide du logiciel fourni - est poussée vers l'avant et déposée sur la palette qui l'attend juste en dessous. Ensuite, la palette descend un peu puis la couche suivante est placée par-dessus, et ainsi de suite. La palette est ainsi remplie couche par couche, à une vitesse particulièrement élevée puisqu'on ne travaille pas paquet par paquet. Ce type de palettiseur est donc principalement utilisé pour les boîtes - bien que certains fabricants proposent également des versions pour les sacs - qui doivent être empilées à grande vitesse.
Autrefois, les palettiseurs à couches étaient généralement rattachés à une seule ligne de production, précisément parce qu'ils ne travaillent pas par produit mais par couche. Lorsque plusieurs lignes ont besoin d'un palettiseur, mais que la capacité rend inutile d'avoir un palettiseur séparé pour chaque ligne, on utilise parfois des zones tampons. Entre le convoyeur d'alimentation et le palettiseur, le nombre de paquets équivalent à une palette est mis en tampon sur les convoyeurs à rouleaux. Lorsque la palette précédente est complètement terminée, le chargement suivant est envoyé de la zone tampon au palettiseur, où elle est placée couche par couche sur la palette suivante. De cette manière, le palettiseur à couches bénéficie encore d'une plus grande flexibilité dans le traitement de différents produits.
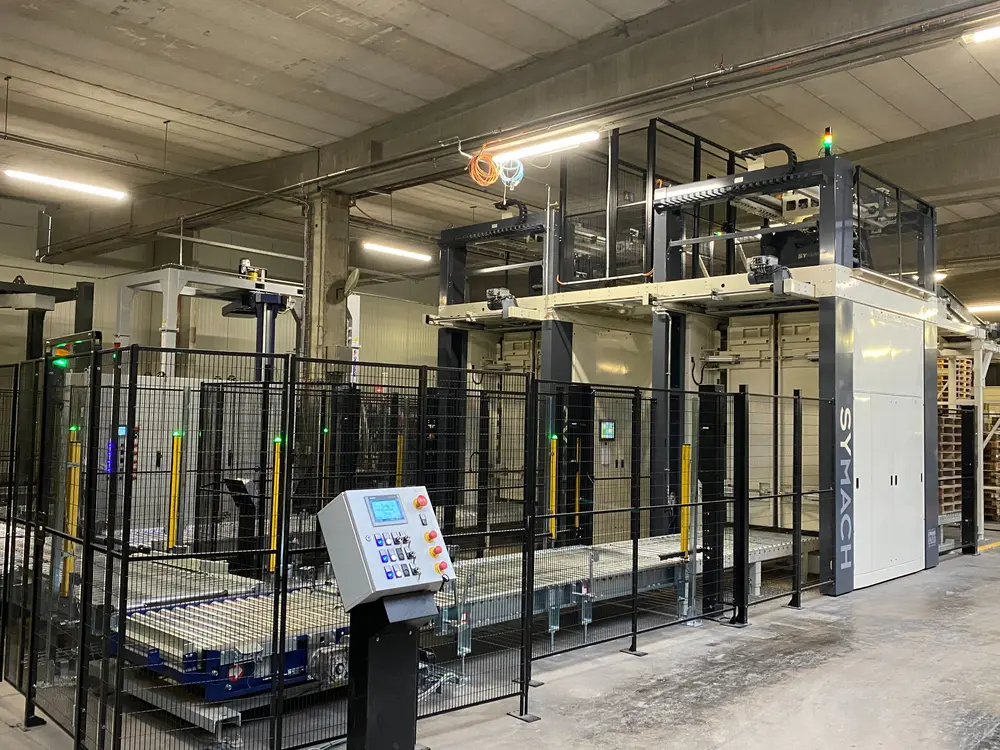
Robot portique
Dans le cas d'un robot portique, plusieurs configurations sont possibles, la palette pouvant être amenée et retirée manuellement ou de manière entièrement automatique. Pour assurer une continuité et une rapidité maximales, on opte souvent pour une configuration où deux palettes sont prêtes à être remplies. Lorsque la première palette est pleine et que le travail commence sur la deuxième, la première est retirée et on place à cet endroit une palette vide, qui sera remplie ensuite.
Là encore, le principe de fonctionnement reste toujours le même: il s'agit d'une pince qui se déplace au-dessus du (des) paquet(s), se positionne correctement et redescend pour attraper le(s) paquet(s). Le robot effectue ensuite un mouvement pour positionner le(s) paquet(s) au bon endroit au-dessus de la palette, avant de le(s) reposer. Cette opération peut être effectuée objet par objet, mais en fonction du poids et du type d'emballage - par exemple une boîte ou un plateau -, il est possible d'en attraper plusieurs à la fois. Le mouvement de la pince peut être réglé de manière à rendre l'accélération plus progressive, ce qui permet de préserver l'intégrité du paquet.
Tout dépend de la pince ou du préhenseur choisi pour ce deuxième type. Cet instrument détermine ce que le palettiseur peut traiter; non seulement le type de produit, mais aussi le nombre par cycle. Une boîte nécessite un tout autre type de pince qu'un seau. Heureusement, il existe aujourd'hui des changeurs d'outils qui passent automatiquement d'une pince à l'autre. Ainsi, à condition qu'il y ait un certain temps d'arrêt, le type de produit à empiler peut être modifié assez rapidement.
Un autre grand avantage du robot portique est l'énorme évolutivité de ce type d'installation. Elle peut être aussi haute, large et profonde que souhaité. Il est souvent plus efficace de prévoir un robot portique pour une ligne ou deux, afin de pouvoir suivre la capacité de la ligne. En effet, le temps de cycle du robot doit toujours être pris en compte. Plus la ligne est large, plus il faut de temps au préhenseur pour arriver là où il doit.
Robot à bras articulé
Il s'agit généralement d'une variante du robot classique à 6 axes, qui ne nécessite souvent que 4 ou 5 axes. Dans ce cas, le robot opère dans une zone circulaire autour de son point d'installation pour prendre et déposer des paquets. Ici aussi, le choix du préhenseur ou de la pince est crucial, car il détermine quel objet peut être saisi correctement. Bien entendu, des changeurs d'outils sont également disponibles.
Le robot à bras articulé présente un certain nombre d'inconvénients. Par exemple, la zone de travail de ce type de robot est assez grande par rapport aux autres types de robots. Étant donné que le robot doit être entouré d'une clôture pour pouvoir travailler à des vitesses plus élevées, cette installation - qui n'est pas accrochée directement au-dessus de la charge, mais qui vient du côté - prend beaucoup de place. En outre, la vitesse est limitée par rapport aux deux types précédents. Les objets sont généralement déplacés une pièce à la fois ou deux ou trois à la fois, ce qui nécessite un cycle complet à chaque fois pour remplir une partie de la couche d'empilage.
Toutefois, cet inconvénient offre aussi un avantage: une plus grande flexibilité. Comme le robot portique, le robot à bras peut facilement alterner entre différents produits. En fonction de la pince requise, il peut travailler avec différentes lignes, en scannant le paquet et en le plaçant ensuite sur la bonne palette. La portée accrue permet ainsi de remplir plusieurs palettes. En outre, les emballages peuvent facilement être orientés.
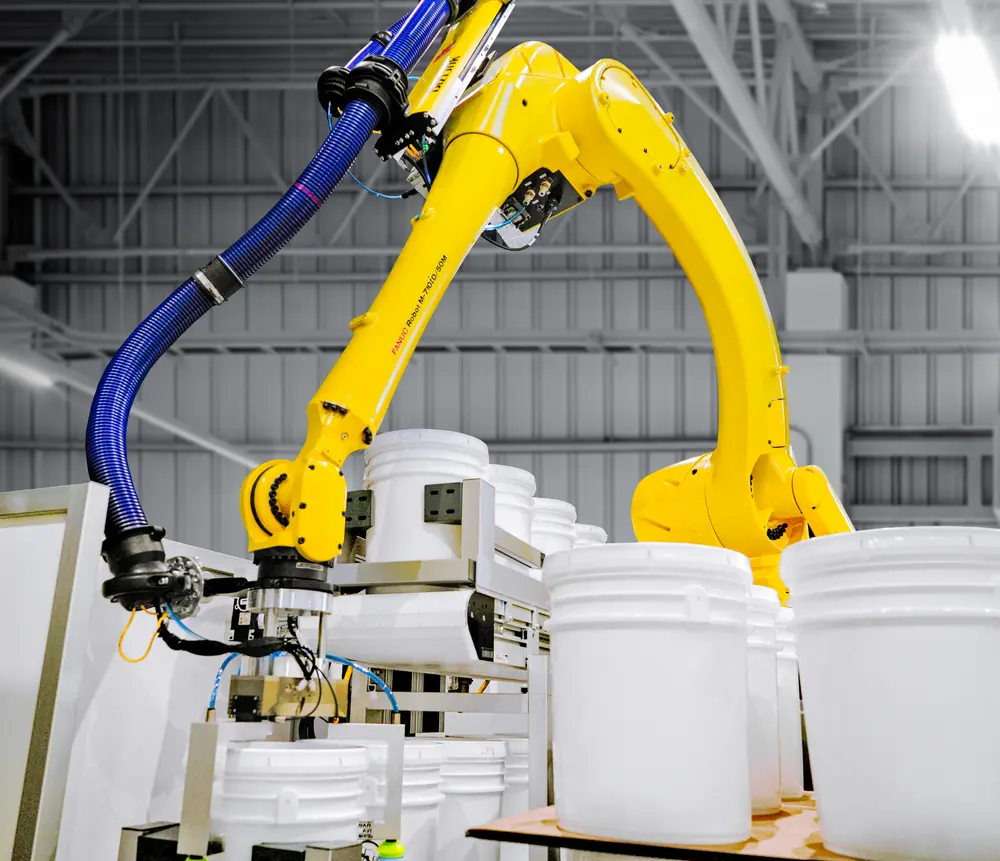
Cobot
Un cobot fonctionne essentiellement de la même manière qu'un robot à bras articulé, mais il n'est pas clôturé. Par conséquent, son poids et sa vitesse sont moindres afin de garantir la sécurité. Toutefois, le poids n'est pas vraiment un inconvénient: de nombreux cobots sont désormais autorisés et aptes à manipuler jusqu'à 30 kg, ce qui est plus que suffisant pour la plupart des emballages alimentaires.
La sécurité reste le principal point de discussion avec les cobots. C'est pourquoi divers mécanismes sont nécessaires pour les rendre sûrs. Pensez aux capteurs qui détectent lorsque la machine touche quelque chose ou quelqu'un, ou lorsque quelqu'un s'en approche de trop près. La conséquence de tout cela est qu'un cobot doit fonctionner très lentement pour rester sûr. Il reste donc à voir quand un cobot sera vraiment rentable pour la palettisation. En outre, l'ensemble de l'installation du cobot doit être inspecté pour être sûr, et ce processus doit être répété pour chaque changement substantiel. L'empilage d'un autre produit nécessite donc une nouvelle analyse des risques.
Facteurs de choix
Le choix du palettiseur approprié dépend avant tout du type de produit et de la capacité que le palettiseur doit atteindre. Les types cités ici sont classés par ordre décroissant de vitesse. Si votre ligne de production est lente et ne traite, par exemple, qu'une boîte par minute, l'achat d'un palettiseur à couches n'a aucun sens. Grosso modo, on peut dire que les modèles les plus rapides sont plus chers.
En fin de compte, le palettiseur doit être parfaitement adapté à la production en question pour être vraiment rentable
Un autre critère est donc le type de produit à empiler. C'est pourquoi de nombreux fabricants ne se concentrent que sur un type particulier, comme les boîtes. D'autres adoptent une approche plus large et s'intéressent également aux sacs et aux seaux. Les sacs, en particulier, sont des objets délicats car ils peuvent changer de forme. Les seaux peuvent également être partiellement comprimés et nécessitent donc une attention particulière. Si vous devez empiler des boîtes similaires en permanence et à un rythme soutenu, un palettiseur à couches sera probablement le meilleur choix. Pour une plus large gamme de produits et à des vitesses moindres, un robot à bras articulé est souvent préférable.
En fin de compte, le palettiseur doit être parfaitement adapté à la production concernée pour être réellement rentable. Le nombre de lignes, la vitesse de production et le type d'emballage sont les facteurs les plus importants. Cependant, il existe un autre critère qui peut sembler banal: l'espace disponible. Comme on l'a dit, certains types de robots, comme le robot à bras articulé mais aussi le palettiseur à couches, sont plus encombrants que d'autres. N'oubliez pas de prendre en compte une marge pour la sécurité et l'entretien nécessaires.
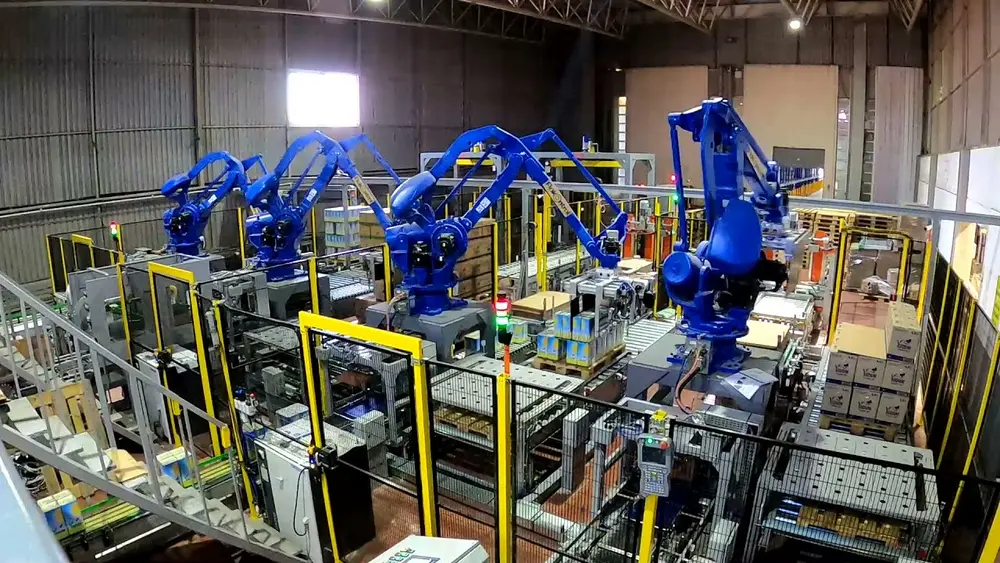
Applications dans le secteur alimentaire
Pour les applications dans le secteur alimentaire, la première chose qui vient à l'esprit est l'hygiène comme facteur de différenciation. C'est également le cas ici, mais l'expérience montre que tous les utilisateurs finaux n'y attachent pas la même importance. Parfois, il s'agit de manipuler des aliments emballés dans un environnement où la production n'a pas lieu, avec peu de probabilités d'interaction entre le produit et la machine.
Les emballages tels que ceux des pommes de terre ou des carottes font exception à cette règle: pour ces produits, on travaille souvent avec des filets partiels. On opte donc plus volontiers pour des solutions plus hygiéniques. Pensez aux palettiseurs (partiellement) en acier inoxydable ou lubrifiés avec des lubrifiants de qualité alimentaire. La conception de palettiseurs nettoyables et hygiéniques est de toute façon devenue une norme dans ce secteur. Ces dernières années, les fabricants ont remarqué que les utilisateurs finaux se préoccupent de plus en plus de la sécurité alimentaire.
Une situation spécifique à l'alimentation est la nécessité d'empiler à des températures très froides. Par exemple, certains produits, comme les viennoiseries et la crème glacée, ne peuvent être laissés dans des environnements chauds que pendant de très courtes périodes. Une solution consiste à rendre l'ensemble du palettiseur résistant au froid, ce qui est assez coûteux. Une autre solution consiste à placer le reste de l'itinéraire logistique dans un environnement frais et le palettiseur dans une pièce 'normale' entre les deux, de manière à ce que l'exposition à des températures plus élevées soit extrêmement limitée. Bien entendu, tout dépend du produit en question et de la vitesse de production.
Avec la collaboration d'Alphatech, Ausloos Verpakkingstechniek, Engisol, Fanuc, Montech, Scott Automation, SigmaControl, Symach et Yaskawa