3D-PRINTEN OP DE DREMPELVAN DE WERKPLAATS
Meer dan alleen de technologie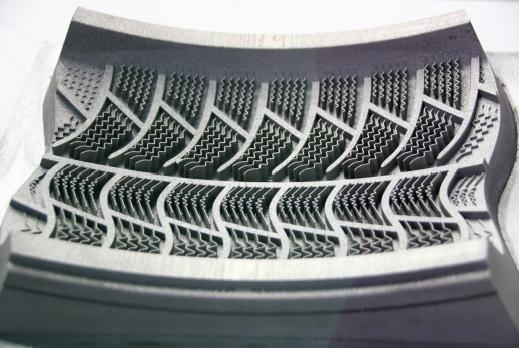
Wat hebben de Duitse bedrijven Siemens, MAN Diesel & Turbo, Schaeffler en het Italiaanse Aidro Hydraulics met elkaar gemeen? Alle vier produceren ze zwaar belaste componenten en systemen, voor uiteenlopende toepassingen, en ze hebben elk additief vervaardigde producten vrijgegeven voor verkoop. Bij deze bedrijven is industrieel 3D-metaalprinten dagelijkse kost. Alle vier hebben ze ook het ontwerp van hun producten aangepast aan de nieuwe technologie.
EXPONENTIELE ONTWIKKELING
3D-(metaal)printen is het stadium van prototyping gepasseerd, ook al bevindt het leeuwendeel van de toepassingen zich nog op dat terrein. Tijdens de Inside 3DPrinting conferentie die samen met de Metav eerder dit jaar plaatsvond, verwoordde professor Franz Josef Volmer het eigenlijk treffend: “3D-printing of additive manufacturing is een exponentiële ontwikkeling. We kunnen niet voorzien wat er gaat gebeuren. We zien sommige bedrijven versnellen, we zien integratie in fabrieken. De volgende stap wordt design voor additive manufacturing. Dat leidt tot nieuwe verdienmodellen."
ONTWERPSOFTWARE CRUCIAAL
Hiermee slaat Volmer de spijker op de kop. 3D-printen vraagt om meer dan alleen de technologie. Het begint met designs waarin de mogelijkheden van de technologie maximaal worden benut. Op dat vlak gebeurt er nu veel. Alle grote ontwikkelaars van CAD/CAM-software zijn bezig om additive manufacturing in hun software te integreren. Hiermee maken ze het voor de ingenieurs gemakkelijker om specifiek voor die technologie te gaan ontwerpen. Een belangrijke rol in deze nieuwe software is weggelegd voor simulatietechnologie. Het gaat dan onder meer om het simuleren van zowel thermisch gedrag, belastingen als vloeistofgedrag. Hiervoor zijn er al jaren gespecialiseerde softwareoplossingen beschikbaar. Momenteel wordt die technologie in een beknopte vorm geïntegreerd in softwaretools voor AM. Dit is een belangrijke stap om het principe 'design complexity for free' optimaal te benutten. Helemaal gratis is die designcomplexiteit echter niet. Bij 3D-metaalprinten hangen de uiteindelijke mechanische eigenschappen van het product namelijk mee af van hoe het onderdeel gepositioneerd wordt op de bouwplaat. Die positionering heeft ook een grote invloed op de uiteindelijke kostprijs van het onderdeel. Dat heeft met name te maken met de nodige supportstructuur. Enerzijds wordt die gebruikt om bij overhangen groter dan 45° het bouwdeel te ondersteunen, anderzijds is er support nodig om de warmte uit het werkstuk sneller af te voeren, zodat vervormingen voorkomen worden. Supportstructuren moeten echter worden verwijderd na het printen en daarna moet het oppervlak dikwijls nog licht worden nabewerkt. Hieruit blijkt al dat de kostprijs van een 3D-geprint werkstuk van veel factoren afhankelijk is, niet het minst de nabewerking. Er bestaan softwarepakketten om dat alles te testen en te optimaliseren. Sommige systemen gaan zelfs zo ver dat men de vervorming door de warmte-inbreng tijdens het proces berekent en het ontwerp daarvoor compenseert, zodat er een geometrisch vlak onderdeel geprint wordt.
METALLURGISCH PROCES
Hoewel sommige partijen best al ver zijn met de integratie van de hele workflow in één softwarepakket, staat deze ontwikkeling eigenlijk in de kinderschoenen. 3D-metaalprinten is namelijk een metallurgisch proces. Zoals gezegd kan men met positionering maar ook met procesparameters eigenschappen van het product beïnvloeden. Eigenlijk worden de eigenschappen van een legering tijdens het 3D-printen bepaald. Dit betekent dat er een veelvoud aan legeringen mogelijk wordt, veel meer dan de fabrikanten nu aanbieden. Dat wordt nog eens vele malen groter als in de toekomst multimateriaalprinters beschikbaar worden. Met Laser Metal Deposition is dat in feite nu al mogelijk, maar in de toekomst wil men nog veel meer combinaties mogelijk maken, waaronder ook metaal en keramiek en metaal met polymeren. Op sommige plaatsen ontwikkelt men technologie om binnen één laag verschillende materialen toe te passen, of eigenschappen te veranderen. Software om dat te ontwikkelen is noodzakelijk, omdat men anders nooit deze mogelijkheden kan toepassen.
MEER DAN POEDERBED
3D-metaalprinten wordt vaak geassocieerd met Selective Laser Melting, in de Amerikaanse AM-normering tegenwoordig aangeduid als Laser Powder Bed Fusion. De tweede technologie die veelvuldig wordt toegepast, maar minder bekend is, is LMD, Laser Metal Deposition. Hierbij wordt poeder of lasdraad met de laser gesmolten en zo bouwt men laag voor laag het product op. Het is in feite een lasproces. Er zijn ook toepassingen waarbij met 'klassieke' lastechnologie het materiaal gesmolten wordt, zoals in het Rotterdamse RAMLab gebeurt. Daar hebben ze al een door Bureau Veritas gecertificeerde scheepsschroef voor een zeewaardig schip 3D-geprint.
Ded-technologie
In de VS zijn veel meer bedrijven hiermee bezig en het lijkt er veel op dat ze op het vlak van Direct Energy Deposition, zoals de officiële term luidt, verder zijn. Een van de Amerikaanse spelers op dit terrein is DM3D, dat meerdere machinetypes hiervoor heeft ontwikkeld. Die worden ingezet voor het repareren of modificeren van (grote) matrijzen. Het voordeel van de DED-technologie is dat er op bestaande producten 3D-features kunnen worden aangebracht. Ook bij het Fraunhofer ILT in Aken lopen er meerdere onderzoeken in die richting. Men denkt onder meer aan het modificeren van standaardcomponenten voor de automobielindustrie, bijvoorbeeld om die te versterken voor een ander model. De tweede toepassing die de Amerikanen voor ogen hebben, is het repareren van vliegtuigcomponenten. Recent is op dit vlak een belangrijke stap gezet doordat de Amerikaanse luchtvaartautoriteit FAA de technologie heeft goedgekeurd voor reparatiedoeleinden. Men verwacht nu dat deze technologie versneld zal worden geïntegreerd in de hele MRO- supplychain. In de olie- en gasindustrie is het onder andere Norsk Titanium dat met deze technologie voet aan de grond probeert te krijgen in de productie van zwaar verspaanbare materialen. Het bedrijf beweert bijna 2 keer zo snel te zijn als met poederbedtechnologie.
GOEDKOPE 3D-METAALPRINTERS
Naast de poederbed- en DED-technologie staan ook andere technieken op het punt naar de markt te komen. Of zijn ze er al. Tijdens de 3D-printconferentie op machinebeurs Metav in Düsseldorf liet de bekende Duitse AM consultant Bernard Langefeldvan Roland Berger zich positief uit over deze nieuwe technieken. “We zien nieuwe metaalprinttechnieken die de poederbedtechnologie uitdagen." Vijf jaar geleden, zo zei hij, zou hij gezegd hebben dat de poederbedtechnologie dé techniek was. Weliswaar duur tot extreem duur, maar voor nichetoepassingen in de luchtvaart en de medische wereld kan dat. Vandaag durft hij die uitspraak niet meer te doen. Er liggen namelijk kapers op de kust.
Binderjetting
Hoewel de nieuwe spelers schermen met eigen technologie en er zeker verschillen zijn, komt het wel neer op één basisprincipe: binderjetting. Ze werken met metaalpoeders die ook voor Metal Injection Molding (MIM) worden gebruikt, het metaalspuitgieten dat al decennialang wordt toegepast. Hierbij zijn de poederdeeltjes ingekapseld in een kunststof. Deze worden tijdens het 3D-printen met elkaar verbonden, wat een product oplevert dat nog niet de uiteindelijke maten en sterktes bezit. Daarvoor moet in vervolgstappen eerst het polymeer worden uitgewassen of verbrand, daarna worden de metaalpoeders gesinterd. Pas dan krijgt het product de definitieve maat. Net als bij MIM levert dat krimp op, maar deze fabrikanten zeggen dat ze die beheersen. Het voordeel van deze technologie is dat tijdens het sinteren in een oven de metaalpoeders in alle richtingen met elkaar versmelten en het product dus in alle richtingen homogene eigenschappen vertoont. Hoewel pas recent de eerste 3D-printers met deze technologie beschikbaar zijn, en over ervaringen nog weinig bekend is, biedt de technologie zeker twee belangrijke voordelen ten opzichte van poederbed- technologie. Allereerst is er geen dure lasertechnologie (inclusief scanner) nodig, waardoor de kostprijs van de machine lager wordt. Ten tweede kan men terugvallen op de MIM-poeders die al jarenlang in tal van varianten op de markt beschikbaar zijn. Vergeleken met poeders voor de poederbedtechnologie vallen de materiaalkosten van deze nieuwe technieken beduidend lager uit. Hierdoor dalen de kosten per geprint werkstuk aanzienlijk. En ook al zijn de eigenschappen onvoldoende voor bijvoorbeeld kritische toepassingen in de lucht- en ruimtevaart, niet alle metalen componenten hoeven aan deze extreem hoge eisen te voldoen.
Verhouding kostprijs en meeropbrengst
De economische haalbaarheid van 3D-metaalprinten als productietechnologie wordt nog steeds vooral bepaald door de verhouding tussen kostprijs en meeropbrengst van het geprinte onderdeel. Sommige toepassingen kunnen zich een hoge kostprijs permitteren. Een voorbeeld: in de ruimtevaart levert elke kilo gewichtsbesparing bij een satelliet een kostenbesparing op van € 20.000 als het er om gaat de satelliet in een baan om de aarde te brengen. Een bracket die dankzij 3D-printen een halve kilo gewicht bespaart, mag dus best enkele duizenden euro's kosten. Voor een onderdeel in een auto ligt deze factor fors lager. Bij de poederbed- printtechnologie zelf staan de ontwikkelingen evenmin stil. Hier verandert de focus duidelijk van tijdsbesparing op het productieproces naar onderdelen die betere prestaties leveren. Qua technologie wordt in de poederbedtechnologie verwacht dat er machines komen met nog méér lasers omde productiviteit te verhogen. Tot nu toe ligt het maximum op vier lasers. Een Duitse producent werkt aan een machine met twaalf laserbronnen. Daarnaast wordt de mogelijkheid onderzocht om de fiberlaserte vervangen door een diodelaser om de kostprijs te verlagen. Bijkomend voordeel hiervan is dat men denkt de 3D-printers makkelijker te kunnen opschalen voor het printen van grotere stukken door meerdere diodelasers te combineren. Fraunhofer ILT past dit toe in een instap-3D-metaalprinter.
MATERIAL JETTING: HOGERE RESOLUTIE
Material jetting is een andere technologie die we meer gaan zien. het Israëlische XJet is de eerste die een commerciële machine bouwt en de eerste twee heeft verkocht. Bij deze techniek word het materiaal gesmolten en worden nanodruppels nauwkeurig gepositioneerd om zo het productop te bouwen. Feitelijk is deze technologie vergelijkbaar met wat in een inkjetprinter gebeurt, alleen gebruikt men nu metaal of keramiek en gebeurt het in 3D. Het Israëlische bedrijf doet dit met 18.000 nanodruppels per seconde. Zelf zegt men dat het voordeel van deze technologie is dat de druppels veel kleiner zijn dan de poeders die poederbedprinters gebruiken: 5 tot 6 µm versus 40 µm bij poederbed en tot 90 µm bij lmd. Het gevolg hiervan is dat de oppervlaktekwaliteit aanzienlijk hoger is. En doordat de druppels niet rond zijn, is de materiaaldichtheid van het printdeel hoog: nagenoeg 100% met mechanische eigenschappen die in alle richtingen gelijk zijn. Let op: pas na het sinteren. Vader is een Amerikaans bedrijf dat deze techniek ontwikkelt voor onder andere aluminium. Zij pakken het anders aan, ze vertrekken namelijk vanuit aluminium lasdraad om hiermee razendsnel producten te printen. Bij Vader is de oppervlaktekwaliteit zeer grof, de snelheid echter extreem hoog.
KUNSTSTOF ALS ALTERNATIEF?
De metaalverwerkende industrie heeft altijd de neiging om naar de 3D-metaalprinterste kijken. Onterecht. Want juist bij het 3D-printen met filament zijn er interessante ontwikkelingen op het gebied van materialen die in verschillende toepassingen aluminium freesdelen vervangen. Er komen betere filamenten op de markt, onder andere gevuld met koolstofdeeltjes waardoor de mechanische eigenschappen van de onderdelen sterk verbeteren. Met name dan in X- en Y-richting, waar men nagenoeg de materiaaleigenschappen behaalt. 3D-printen met filament betekent helaas nog steeds dat men in de Z-richting flink aan sterkte inboet. Met name in de machinebouw, waar een aantal machinebouwersal is overgestapt om bepaalde delen die stuk gaan te vervangen door 3D-geprinte onderdelen van carbon gevulde materialen. Zij kiezen hiervoor omdat ze dan geen voorraad meer hoeven aan te houden.