Additive manufacturing trends om in de gaten te houden
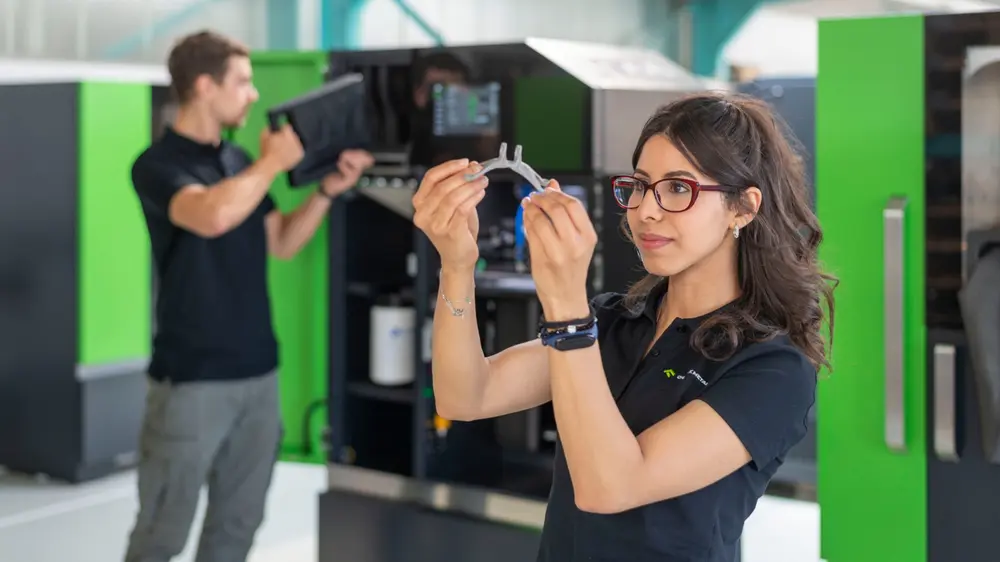
De additive manufacturing industrie is altijd optimistisch geweest over de groei. Toch was 2020 een minder goed jaar voor de sector, maar dat werd in 2021 goedgemaakt. Waar staat de AM-industrie nu? Welke zijn de trends in 3D-metaalprinten? En breekt de technologie in 2022 door dankzij nieuwe, goedkopere technieken?
Marktsituatie
De markt voor 3D-metaalprinten heeft zich in 2021 verder hersteld van de dip die veroorzaakt werd door de coronapandemie: voor het eerst sinds vele jaren daalden in 2020 de verkopen van 3D-metaalprinters licht.
Voor een deel is dit te verklaren doordat vliegtuigbouwers en grote toeleveranciers aan het begin van de crisis fors op de rem trapten. In de tweede helft van het jaar is dat verlies voor een belangrijk deel goed gemaakt door de Amerikaanse ruimtevaartindustrie en veel startups, die fors investeerden in additive manufacturing. Het Duitse onderzoeksbureau Ampower concludeert in een recente studie dan ook dat de VS momenteel veruit de grootste markt is voor additive manufacturing, met de hoogste groeiratio’s. China is de tweede grootste markt, aangejaagd door de ontwikkeling van de eigen vliegtuigindustrie; gevolgd door Duitsland.
Een andere sector die volgens de onderzoekers de investeringen in AM heeft teruggeschroefd, is de automobielindustrie. Deze industrietak herstelt echter snel.
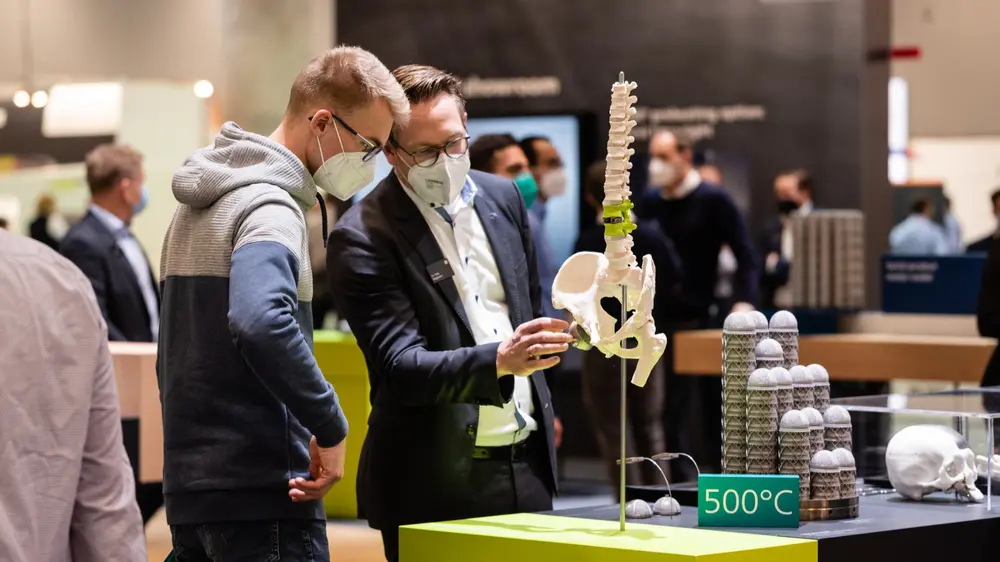
Meer lasers
De kosten per onderdeel dat van een AM-machine komt, moeten omlaag, om het aantal toepassingen substantieel te vergroten. Meer productiviteit is daarvoor een oplossing.
Lagere kosten zullen leiden tot meer toepassingen
Dit hebben de fabrikanten voor een deel al ingevuld door hun machines uit te rusten met meer lasers. Dual- en Quad-lasersystemen zijn al enkele jaren gemeengoed. Lange tijd is het bij vier lasers gebleven, maar onlangs is ook de eerste 3D-metaalprinter met 12 lasers van elk 1 kW gepresenteerd. Gecombineerd met een groot bouwvolume, leidt dit tot een aanzienlijk hogere productie in dezelfde tijd; minstens een factor 5 sneller. De productiviteitswinst kan oplopen tot 10 à 20 keer.
Toch denkt niet iedereen dat meer lasers de oplossing zijn om de stukkosten te verlagen. Dit betekent namelijk nog meer warmte in de bouwkamer en dat maakt het proces moeilijker beheersbaar. De laserpoederbedmachines vragen nu al een goede procesbeheersing om vervorming door de warmte en het ontstaan van microscheuren te voorkomen.
Procesoptimalisatie
Andere fabrikanten denken dat er nog voldoende winst te behalen valt door het hele proces te optimaliseren. Een algemeen gehoorde oplossing is dat de fabrikanten de Overall Equipment Effectiveness van hun systemen moeten verhogen. Sommige AM-bedrijven hanteren een eerste doel van 75% effectieve inzettijd van de machines. Dit vereist allereerst een stabiel proces. Monitoringssoftware en systemen om het smeltbad te bewaken, moeten hiertoe bijdragen. Recent onderzoek heeft ook duidelijk gemaakt dat de invloed van de gasstroom wellicht groter is dan gedacht. Helium toevoegen aan argon, blijkt tot een stabieler proces en dus tot een hogere productiviteit te leiden.
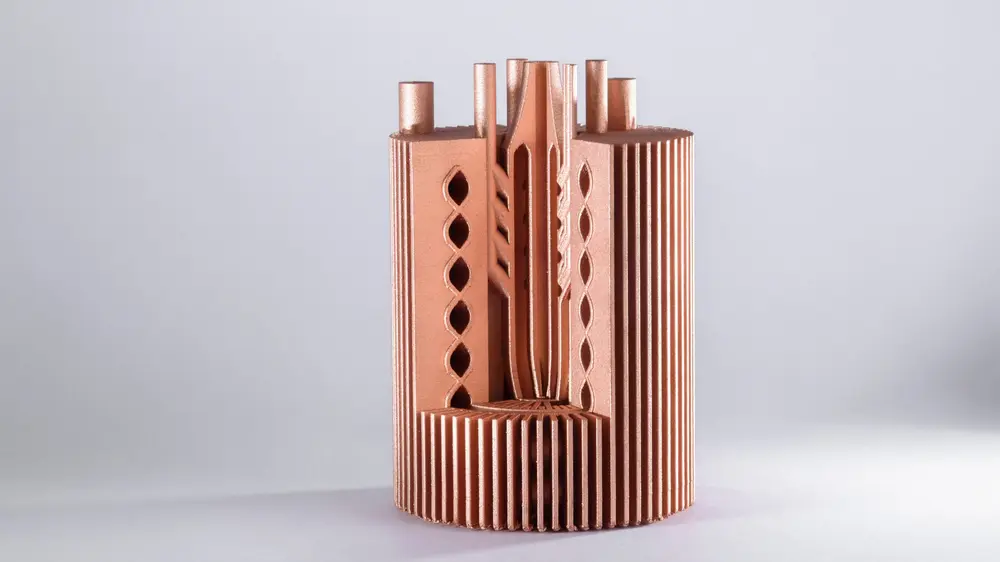
Supportstructuren reduceren
Een andere richting waaruit een hogere productiviteit kan komen, is de mogelijkheid om minder supportstructuren nodig te hebben. Deze ondersteuning wordt niet alleen geprint bij een overhangend deel van het werkstuk, maar ook om warmte vanuit het werkstuk te kunnen afleiden naar de bouwplaat. De kosten van supportstructuren zijn relatief hoog: ze vergen duur materiaal tijdens het printproces én ze moeten naderhand verwijderd worden, wat tijd en dus geld kost.
Door minder support te gebruiken, kan de productiviteit omhoog
De hoeveelheid support verminderen, kan door het werkstuk anders te positioneren op de bouwplaat. Hiervoor komt er steeds betere simulatiesoftware beschikbaar. Dit kan ook door de procesparameters aan te passen. Er zijn inmiddels meerdere 3D-metaalprinters op de markt die aanzienlijk minder vaak supportstructuren nodig hebben en ook het stapelen van producten in de bouwkamer toelaten; iets dat bij bijvoorbeeld elektronenstraal 3D-printen al langer kan. Ook dat verlaagt de kosten per geprint onderdeel. Een betere integratie met post processing kan eveneens bijdragen aan het verlagen van de kosten per 3D-geprint werkstuk. En de vierde richting is het vereenvoudigen van de workflow.
Integratie komt op gang
Deze workflow is echter een sta-in-de-weg als het gaat om echt seriematig produceren met additive manufacturing. De verschillende stappen in de voorbereiding van een 3D-print en de mechanische nabewerking moeten immers in verschillende programma’s gebeuren. Daar komt echter stilaan verandering in.
Meerdere CAM-ontwikkelaars hebben zich namelijk op additive manufacturing gestort en integreren de werkvoorbereiding voor de 3D-printer in de softwareomgeving waarin de werkvoorbereiding voor de mechanische nabewerking wordt gedaan. Daar voegen sommigen ook nog simulatiesoftware aan toe om het printproces te simuleren, zodat het risico op vervormingen door de warmte-inbreng wordt verkleind. Hiermee kan men de buildjobvoorbereiding voor een deel automatiseren én men kan kennis vastleggen en combineren met de specifieke settings voor een AM-machine. Een van de hordes die de softwarefabrikanten hiervoor hebben moeten nemen, is het combineren van mesh- met CAD-data in dezelfde software-omgeving. De doorbraak is versneld door de ontwikkeling van de Parasolid-kernel door Siemens, die inmiddels door meer dan 200 softwareontwikkelaars wordt gebruikt.
Ook komt het adaptief frezen naar voren. Net als bij gietstukken, zijn additief vervaardigde werkstukken qua maatvoering nooit exact identiek. Door het werkstuk in de bewerkingsmachine met een taster te meten en dan voor de afwijking ten opzichte van het CAD-model het NC-programma te corrigeren, kan men nabewerking verder automatiseren.
Noodzaak van toegankelijke machines
Er bestaat nog een ander hiaat in de workflow. Tot voor kort stond een aantal belangrijke fabrikanten van metaal AM-systemen onwelwillend tegenover het idee om software van derden toegang te bieden tot de machinedata. Stilaan begint dit te kantelen, omdat ze inzien dat software, Machine Learning algoritmen en Artificiële Intelligentie belangrijke bouwstenen zullen zijn voor het toekomstige AM-proces. Nu ontstaan er dus meer open systemen.
In het voorjaar van 2021 wees de Europese Commissie in een rapport overigens nog op het belang van wet- en regelgeving om juist dit soort zaken te regelen. De samenstellers van het rapport verwachten dat regelgeving de interoperabiliteit van AM-systemen helpt vergroten. Het zou kopers meer vertrouwen in de technologie moeten geven.
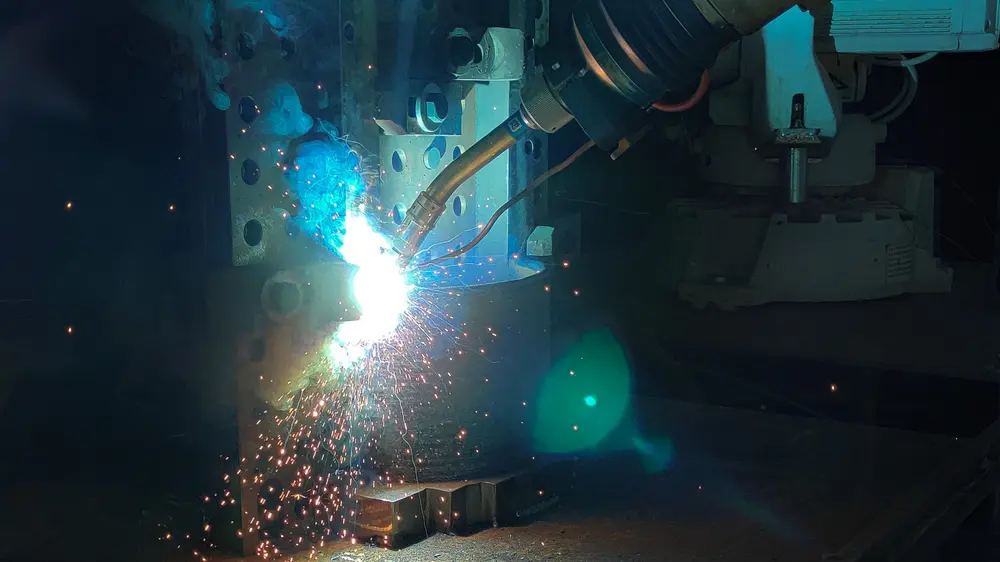
Nieuwe AM-technieken op punt VAN DOORBRAAK
Jarenlang is laser powderbed fusion dé metaalprinttechnologie geweest. Dit is nog steeds zo, maar de markten beginnen te verschuiven. Het eerder aangehaalde Ampower verwacht dat tegen 2025 alternatieve technieken marktaandeel gaan winnen, ten koste van de klassieke techniek. Twee AM-technologieën om in de gaten te houden, zijn Binder Jetting en Directed Energy Deposition. Twee spelers op het vlak van Binder Jetting zijn Desktop Metal en HP; fabrikanten die DED-technologie aanbieden, zijn talrijker. Het gaat hier om systemen waarmee met draad of poeder wordt opgelast. Denk aan de systemen zoals bijvoorbeeld Mazak en DMG Mori in de hybridemachines toepassen, of de AM-machine van Chiron.
Twee AM-technologieën om in de gaten te houden, zijn Binder Jetting en Directed Energy Deposition
Directed Energy Deposition
Recent komen vooral rond de DED-technologie veel positieve signalen over toepassingen naar buiten. Een van de sectoren die veel met deze technologie bezig zijn, is de olie- en gasindustrie. Daar willen ze additive manufacturing namelijk gaan inzetten om de voorraad reserve-onderdelen voor de kostbare installaties te verkleinen. Deze voorraden worden nu aangehouden omdat stilstand van een booreiland of een petrochemische fabriek zeer kostbaar is, tot wel 1 miljoen euro per dag. Additive manufacturing verkort de doorlooptijden in de productie en is geschikt voor seriegrootte 1. Hierdoor kan men de voorraden dus reduceren en bovendien is lokale productie mogelijk.
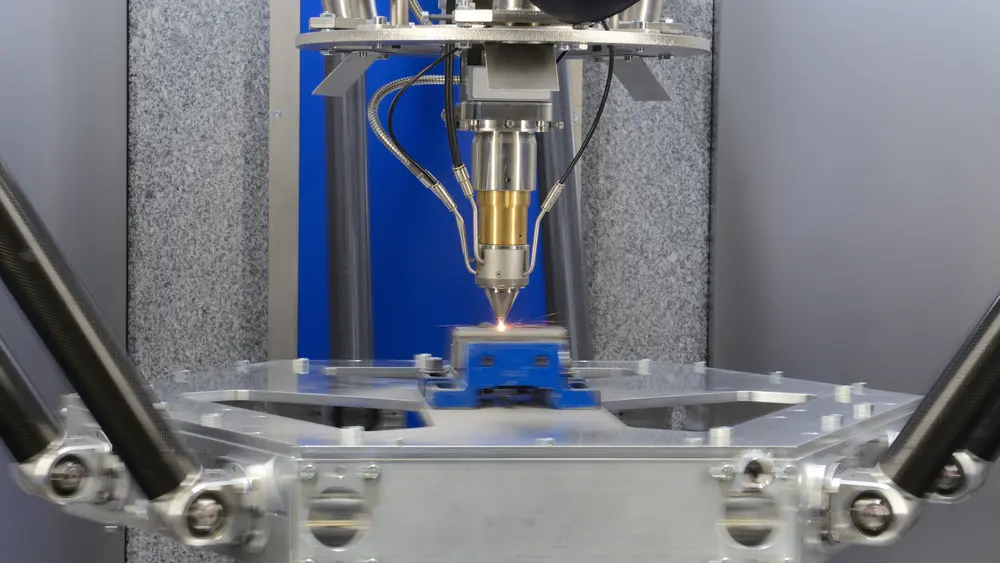
De grote voordelen van DED-technologie zijn dat men grote werkstukken kan produceren en dat de materiaalopbouw veel sneller verloopt dan bij de poederbedmachines. Met deze technologie is het tevens makkelijker om meerdere legeringen in één werkstuk te combineren, omdat men poeders of lasdraden kan samenvoegen. Denk bijvoorbeeld aan een gereedschap waarin koper wordt gebruikt voor een snelle warmte-afvoer en een Inconel toplaag voor slijtvastheid. Daarnaast speelt ook het thema duurzaamheid een rol. Met DED-technologie kan men op bestaande materialen verder 3D-printen. Zo kan men versleten, kostbare gereedschappen repareren. In een aantal onderzoeksprojecten is de kwaliteit van deze AM-werkstukken aangetoond. Deze technologie leent zich voorts ook voor minder kritische onderdelen, bijvoorbeeld in de machinebouw. Sinds de uitbraak van de coronapandemie hebben veel OEM’ers hier oog voor gekregen, omdat ze dit zien als een mogelijke oplossing om minder afhankelijk te worden van kwetsbare aanvoerlijnen uit bijvoorbeeld China.
Binder jetting
Binder Jetting is de andere metaalprinttechnologie waar veel van verwacht wordt. Een van de voordelen is hier dat er geen warmte in de stukken komt. Voorts zijn supportstructuren overbodig. Omdat de materialen vaak gebaseerd zijn op die voor Metal Injection Moulding (MIM), wordt dikwijls dezelfde standaard gebruikt. Volgens de meeste fabrikanten voldoen de onderdelen aan de internationale standaarden voor MIM-technologie, of zijn ze zelfs beter. Ze wijzen altijd op het verschil dat de MIM-poeders voor 93% van het gewicht metaaldeeltjes bevatten en de 3D-printpoeders tot 99% van het gewicht. Er zit dus minder bindmiddel in dat verwijderd moet worden. Fabrikanten zeggen dat binder jetting tot een betere isotropische korrelstructuur van het materiaal leidt dan het lasersmelten. Doordat er weinig warmte bij dit proces vrijkomt, kan men onderdelen nesten, wat de kostprijs per stuk omlaag brengt.
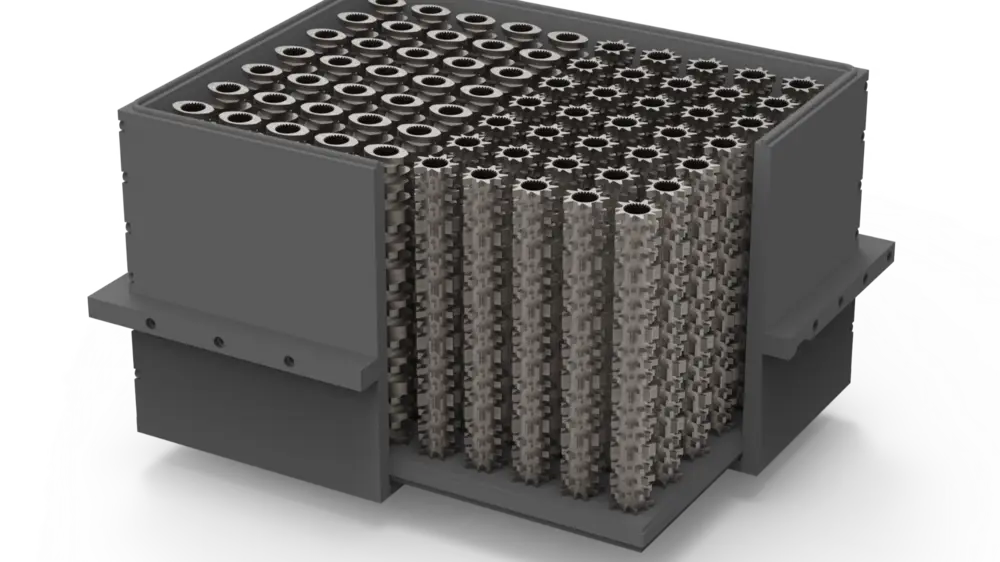
De nadelen zijn dat de techniek tot nog toe vooral geschikt is voor kleine onderdelen én dat de sinterstap veel expertise of een geïntegreerde oplossing vraagt; AM-systeem met sinteroven aangestuurd vanuit één centraal systeem. De grote doorbraak laat nog op zich wachten.
Lowcostmetaalprinten
De noodzakelijke investeringen om te kunnen beginnen met 3D-metaalprinten, zijn hoog. Of men nu investeert in een laserpoederbed of in een binderjettingsysteem; het gaat al gauw om vele honderdduizenden euro’s tot méér dan een miljoen voor een op productie gericht AM-systeem. Enkele kleinere partijen denken dat dit voor met name kmo’s een te hoge drempel is en komen daarom met lowcostoplossingen op de markt.
Lowcostoplossingen kunnen de investeringsdrempel verlagen
Het vervangen van de fiberlaser met een hoge straalkwaliteit door een kwalitatief mindere diodelaser, draagt bijvoorbeeld bij aan de lagere kosten van een poederbedsysteem. In dat geval kan men bovendien het complexe spiegelstelsel (galvosysteem) achterwege laten. Dit wordt vervangen door een goedkoper mechanisch systeem. De diodelaser wordt op een cartesisch assenstelsel geplaatst. Hierdoor verliest men snelheid en enigszins ook nauwkeurigheid, maar voor kleinere werkstukken en onderdelen die toch mechanisch nabewerkt worden, hoeft dat geen onoverkomelijk probleem te zijn. Deze fabrikanten besteden daarnaast veel aandacht aan het vereenvoudigen van de bediening van de 3D-metaalprinter.
Er komen ook nieuwe AM-technieken die beloven dat het proces veel eenvoudiger wordt, de materiaalprijzen lager zijn en de kwaliteit van de stukken dicht tegen gietkwaliteit aan ligt. Liqiuid Metal is een voorbeeld van zo’n technologie, die werkt met standaard lasdraad die gesmolten wordt. Met een speciale techniek worden talloze kleine druppels van het vloeibaar materiaal 'gejet' op het op te bouwen onderdeel. In de laatste stap ondergaan de onderdelen een warmtebehandeling om spanningen uit het materiaal te halen. Lithografische metaalprintprocessen zijn een andere ontwikkeling, gebaseerd op de technologie om technisch keramiek te printen. In dit geval wordt het metaalpoeder gedispergeerd in een pasta die met een digitale projector wordt belicht.
Geïnspireerd door de metaalprinters van Markforged en Desktop Metal, zijn zowel filamentproducenten als ontwikkelaars van desktop-FFF-printers gaan experimenteren met het 3D-printen met filament dat voor een belangrijk deel gevuld is met metaalpoeder. Daarmee 3D-print men met een industriële FFF-printer onderdelen die daarna nog – afhankelijk van het filament – één of twee processtappen moeten doorlopen om een metalen onderdeel over te houden. De eerste stap is debinding: het verwijderen van het aandeel polymeer. Dit kan zowel thermisch als katalytisch. De tweede stap is het sinteren. Sommigen combineren beide stappen. De dichtheid van deze onderdelen is na het sinteren vergelijkbaar met fijngietwerk. Het oppervlak is ruw, maar kan goed worden nabewerkt. Het grootste voordeel van deze aanpak is dat de investeringen extreem laag zijn. Daarnaast is het een vrij eenvoudige technologie. Nadelen zijn de meerdere processtappen en het feit dat het sinteren veelal speciale en dure sinterovens vergt, én specifieke kennis.
Indirect 3D-printen
Naast de hoge investeringskosten, lopen plannen voor 3D-metaalprinten ook dikwijls stuk op de materiaalcertificeringen. Indirect 3D-printen voorkomt dit laatste. Met name voor composietverwerkende bedrijven wordt 3D-printen van mallen interessanter. Nieuwe materialen met betere eigenschappen, waardoor de standtijd van de mallen verbetert, en de beschikbaarheid van groot formaat 3D-printers openen heel nieuwe mogelijkheden. Doorlooptijden zijn veel korter dan wanneer men de mallen gaat frezen. Zeker nu gewichtsbesparing in veel toepassingen hoog op de agenda staat, helpt het als men geen dure gereedschappen meer hoeft te maken voor enkelstuks of kleine series. Er wordt zelfs al onderzocht of voor prototypes van plaatwerkdelen een van kunststof geprinte matrijs volstaat.
We praten hier dus over een indirecte toepassing van 3D-printen. Daar toont ook de automobielindustrie veel interesse voor, maar dan wel metalen gereedschappen die additief worden geproduceerd. Het voordeel is dat men het bestaand productieproces in stand kan houden, en met de gevalideerde en soms gecertificeerde materialen kan blijven werken. De investering in een duur gereedschap blijft echter achterwege. Dat verkleint het risico en zorgt ervoor dat een nieuw product sneller op de markt kan komen. De productie van een gereedschap kost immers al gauw vele weken tot soms zelfs maanden. De ervaringen van Duitse autofabrikanten laten zien dat met deze additief gemaakte inserts in de plaatbewerking standtijden van vele honderdduizenden perscycli haalbaar zijn. Dankzij de betere koeling gaan cyclustijden omlaag en de kwaliteit van de buiging omhoog.
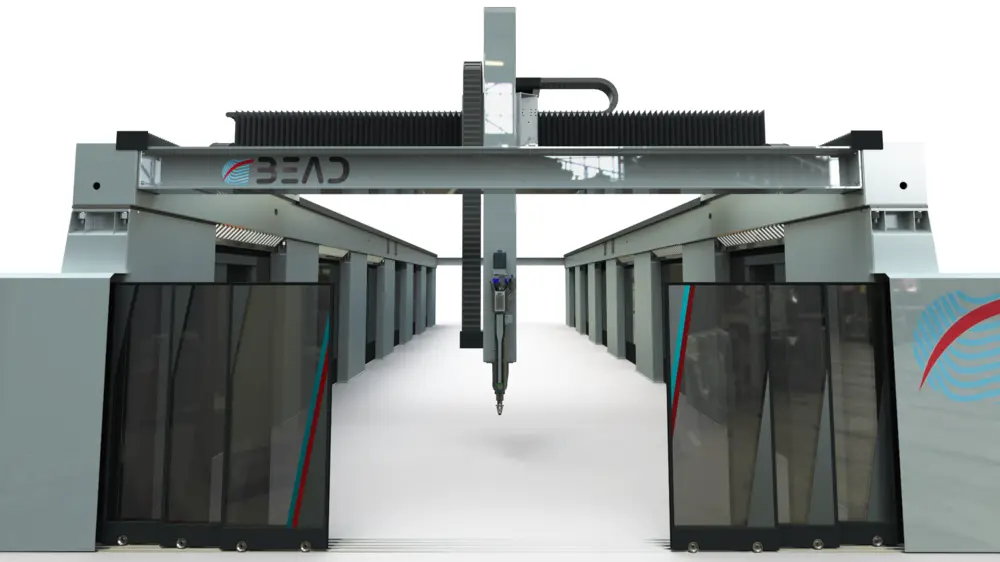
Ook in de gietindustrie neemt de interesse voor het 3D-printen van gietkernen en mallen toe, hoewel deze technologie al zo’n 20 jaar beschikbaar is. Korte doorlooptijd, de productie van de gereedschappen volledig in eigen huis houden, en lagere kosten terwijl men met de goedgekeurde materialen kan blijven gieten, beginnen steeds zwaarder te wegen in de afweging om te investeren in een zandprinter voor het maken van gietmallen en kernen. Een van de laatste aankondigingen op dit vlak betreft de bouw van ’s werelds grootste 3D-printer voor een windmolen in een offshore windmolenpark. In twee weken tijd moeten deze mallen klaar zijn voor het gieten van grote metalen onderdelen van 9,5 meter doorsnede en meer dan 60 ton eigen gewicht. De doorlooptijd voor de tooling bedraagt nu nog zo’n 10 weken. Daarnaast rekenen de initiatiefnemers op een betere oppervlaktekwaliteit en maatnauwkeurigheid.
