UMATI OF MTCONNECT?
De ontbrekende schakel in Industrie 4.0
Negen jaar nadat op de vakbeurs IMTS in Chicago zo’n 25 bedrijven voor het eerst de mogelijkheden van MTConnect demonstreerden, kondigde de VDW op de EMO 2017 het project umati aan. Terwijl in de VS al veel machines standaard worden geleverd met het communicatieprotocol aan boord, wil de Duitse machinebouwindustrie een nieuwe, wereldwijde standaard ontwikkelen. De EMO 2019 werd de eerste lakmoesproef: meer dan 100 CNC-machines van verschillende merken werden gekoppeld.
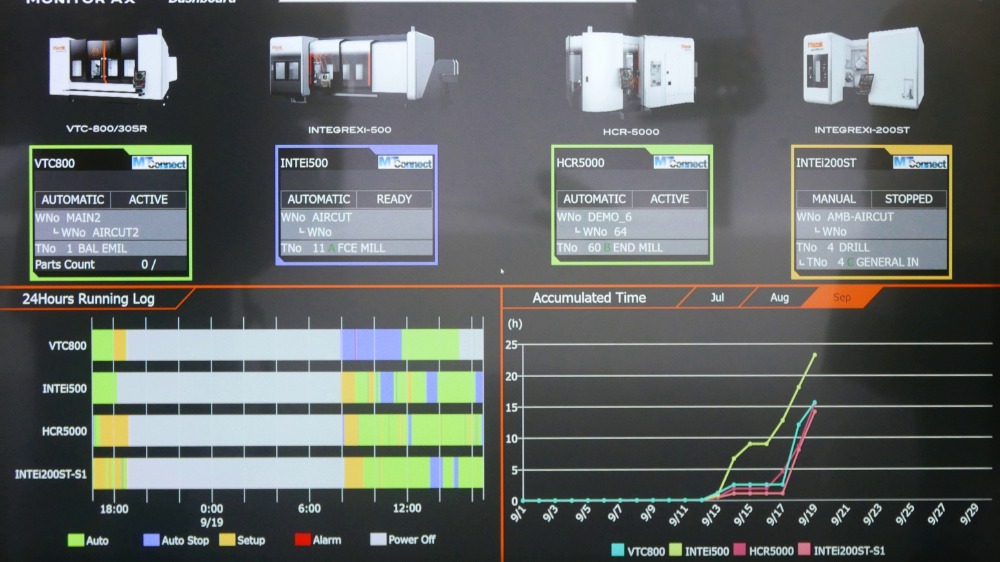
INDUSTRIE 4.0
De term Industrie 4.0 mag dan wel in Duitsland zijn uitgevonden, lange tijd heeft eigenlijk een wezenlijke bouwsteen voor een cyber-fysisch productiesysteem ontbroken. In de cyberfysische wereld worden voortdurend data van machines en componenten uitgelezen. Algoritmen verwerken deze data voor uiteenlopende toepassingen tot bruikbare informatie: van een dashboard dat weergeeft hoe de productie loopt, het optimaliseren van bewerkingen tot en met MES-systemen voor de planning en meer geavanceerde systemen die voorspellen wanneer onderhoud moet plaatsvinden. Bij het uitlezen van die data gaat het fout als de betrokken partijen er vooraf niet voor zorgen dat machine en software dezelfde taal spreken. Dit komt doordat de machinebouwers hun eigen codes hanteren. Er is nooit een wereldwijde standaard opgesteld. Het commando ‘deur open’, om een voorbeeld te geven, kan bij de ene machinebouwer semantisch heel anders omschreven zijn dan bij de andere. Iedere fabrikant bouwt namelijk zijn eigen interface. Dit betekent dat, voordat data kunnen worden uitgewisseld, systeemintegratoren eerst lange vertaaltabellen moeten opstellen. Vergelijk het met de beginjaren van de pc, toen elke printerfabrikant zijn eigen driver meeleverde. In 1996 loste Intel dit op met de ontwikkeling van de USB, de Universal Serial Bus. Hardware kan nu direct aangesloten worden.
MTCONNECT, DE AMERIKAANSE VARIANT
In de Verenigde Staten heeft de komst van de USB als open communicatiestandaard de Association of Manufacturing Technology (AMT) in 2006 geïnspireerd om een vergelijkbare open standaard voor de werktuigbouwmachines te ontwikkelen. Op IMTS 2008 in Chicago werd de eerste demonstratie gegeven. Het is een open, licentievrije standaard die de machinedata vertaalt naar een algemene, internetgebaseerde taal die begrepen wordt door software. Vanaf dat moment zijn steeds meer machinebouwers de MTConnect standaard op hun producten beginnen aanbieden. Tegelijkertijd was er in de beginjaren in de VS een sterke opmars van softwareontwikkelaars die een markt zagen en oplossingen bouwden om de data uit de machines te halen en bruikbaar te maken voor de operators, productieplanners en het management van de maakbedrijven. Dat deze ontwikkeling juist in de Verenigde Staten momentum kreeg, is te danken aan deze standaard. Hij maakt de software breder inzetbaar, omdat het type CNC-besturing minder van belang is. Tegenwoordig is MTConnect in de VS en in delen van Azië een geaccepteerde standaard. Ook Europese machinebouwers bieden deze aan.
Sinds een aantal jaren is het MTConnect Institute een verzelfstandigde organisatie waar partijen die er belang bij hebben, zich kunnen aansluiten. Het MTConnect Institute werkt samen met de OPC Foundation, de wereldwijde organisatie die OPC UA (Open Platform Communications Unified Architecture) als communicatieprotocol ontwikkelt en promoot.
UMATI
Hoewel er dus een standaard voor de werktuigmachines bestaat, vindt de VDW, de vereniging van Duitse machinebouwers, dat er plaats is voor een andere wereldwijde standaard. Op EMO 2017 werd de ontwikkeling hiervan aangekondigd, op AMB 2018 werd de eerste demonstratie gegeven met louter Duitse en Zwitserse machinebouwers. umati (Universal Machine Tool Interface) onderging op EMO 2019 in Hannover een grote testcase. Alle grote besturingsproducenten voor CNC-machines meldden zich inmiddels bij de VDW en deden mee. Meer dan 100 CNC-machines van uiteenlopende fabrikanten, dit keer ook niet-Duitse, worden gekoppeld, zodat data op een gemeenschappelijk platform gepresenteerd kunnen worden. Doordat de fabrikanten nu een gestandaardiseerde interface gebruiken, verloopt de koppeling van een machine met bijvoorbeeld een MES- of een ander planningssysteem veel sneller. De umati-software staat op de OPC UA-server die in de machine wordt geplaatst. Het MTConnect Institute en AMT hebben iets soortgelijks eigenlijk al op EMO 2011 in Milaan gedemonstreerd. Bezoekers konden toen live volgen hoe CNC-machines zowel op de beurs als in fabrieken verspreid over de hele wereld op dat moment presteerden.
umati is bidirectioneel
Maar waarom is in Duitsland het initiatief genomen om een nieuwe communicatiestandaard te ontwikkelen, als er al een standaard bestaat die in de VS en Azië wordt gebruikt? Volgens de VDW heeft dit enerzijds te maken met de fundamentele visie, anderzijds met een technisch aspect. Dit laatste betreft het feit dat MTConnect slechts in één richting communiceert: data vanuit de machine richting de software voor verdere analyse. Dat volstaat voor het analyseren van data voor een monitoringfunctie of het voorspellen van onderhoud. In de toekomst wil men echter naar meer autonome machines toe, de kern van het cyber-fysische productiesysteem waarin Industrie 4.0 voorziet. En dan moeten er ook data terug naar de machine kunnen. Lezen en schrijven, terwijl de standaard nu alleen kan lezen. Het MTConnect Institute zegt overigens ook te werken aan een bidirectionele communicatie. Op IMTS in Chicago werd in het Emerging Technology Center een project gedemonstreerd, samen met het ROS Instituut, dat een open robotbesturing ontwikkelt. Data uit de machine werden hier uiteindelijk gebruikt om autonoom de volgende productiestappen aan te sturen.
(lees verder onder de foto)
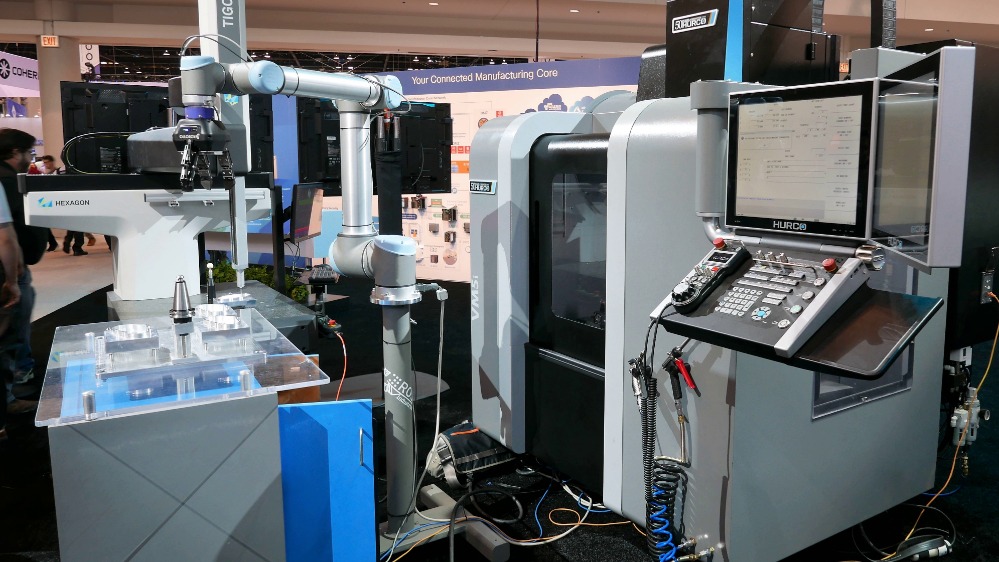
Via MTConnect en een testversie van een opensourcerobotbesturingssysteem kan deze productiecel volledig autonoom produceren
VERSCHILLENDE VISIE
Het eerste punt dat de VDW aanhaalt, de andere visie, is een argument dat meer steek houdt. De Duitse machinebouwers vinden dat de MTConnect-standaard vooral ontwikkeld is vanuit de visie van de gebruikers, zonder voldoende rekening te houden met de fabrikanten. umati wordt ontwikkeld vanuit de machinebouwers en houdt dus meer rekening met hun belangen, zoals het afschermen van specifieke technologie in de besturing van de machine. De VDW benadrukt overigens voortdurend dat men geen concurrentie zoekt met de Amerikanen, maar waar mogelijk wil samenwerken. Belangrijk is te weten dat enkele maanden geleden MTConnect officieel erkend is als een Amerikaanse standaard, voor het eerst in het tienjarige bestaan. Het MTConnect Institute heeft bewust de stap gezet om een geaccrediteerde organisatie voor de ontwikkeling van standaarden te worden. Wat umati en MTConnect weer gemeenschappelijk hebben, is dat de standaard licentievrij beschikbaar is.
STANDAARD VOOR DIGITALISERING
Zowel MTConnect als umati is gebaseerd op de OPC UA standaard, een protocol dat snel terrein heeft gewonnen in de machine-installatiebouw. OPC UA is een architectuur die systemen compatibel met elkaar maakt. Anders gezegd: OPC UA is een standaard die data uit PLC’s beschikbaar maakt. MTConnect en umati zijn de oplossingen om de data zodanig aan te bieden dat de software (van derden) er iets mee kan; dat er acties uit kunnen voortvloeien.
Er zijn echter ook andere partijen die CNC-machines met planningssoftware koppelen om data uit te lezen en beslissingen te nemen of managementinformatie te genereren. Die gebruiken noch umati, noch MTConnect, maar slagen erin om met name PLC’s uit te lezen. Het voordeel van deze aanpak is dat ook oudere machines gekoppeld kunnen worden aan een monitoringsysteem, iets wat met de nieuwe interfaces moeilijk wordt. Bij sommige van deze systemen betekent het koppelen van een machine met een ander type besturing wel extra werk, precies wat de standaard voorkomt. Dus betekent dit dat er kosten gemaakt moeten worden om de verschillende begrippen zogenaamd te mappen; anders gezegd tabellen te schrijven waarin de verschillende terminologie aan elkaar wordt gekoppeld.
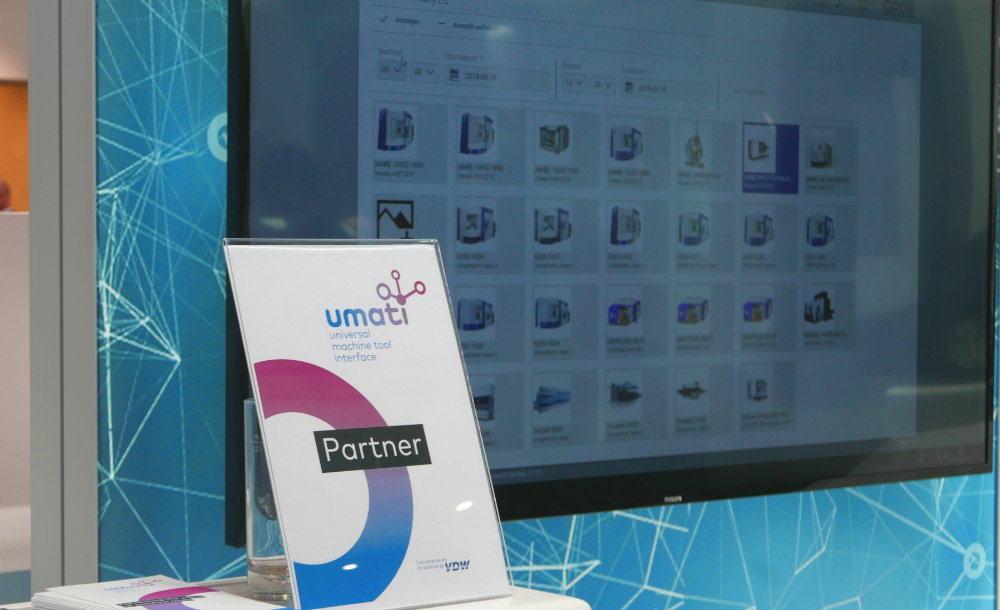
Artificiële intelligentie
Maar waarom is zo’n communicatiestandaard belangrijk? Dat heeft alles te maken met de digitalisering van de maakindustrie. Het monitoren van de machines is slechts de eerste stap. In de toekomst zal dankzij kunstmatige intelligentie nog veel meer mogelijk zijn. Bijvoorbeeld om naar zelflerende processen te gaan. Artificiële Intelligentie maakt het in de toekomst mogelijk dat software aan de hand van gemeten waarden en een model kan voorspellen welke parameters veranderd moeten worden om een kwalitatief goed product te maken. De komst van 5G-netwerken in de fabriek zal daarin een belangrijke rol spelen. Want hoeveel er ook over cloudsystemen wordt gesproken, voor realtimecommunicatie blijft de cloud vooralsnog te traag en zullen in de toekomst lokale, zogenaamde Edge-computers worden ingezet. Via een lokaal 5G-netwerk in de fabriek worden de data razendsnel heen en weer gestuurd tussen machine en server. Dergelijke oplossingen zullen invloed krijgen op hoe de machines door de operatoren bediend worden. Zo zullen zij steeds meer ondersteund worden door digitale assistenten; algoritmes die op basis van ervaringen oplossingen voorstellen.
Een eerste voorzichtig voorbeeld ziet men al in de software voor het programmeren van robotsystemen. Specifieke progammeersoftware is niet meer nodig omdat de software zelf de vertaling maakt tussen een aantal parameters die voor elke verspaner herkenbaar zijn, en de aansturing van de robot. De cloudsystemen zullen dan vooral gebruikt worden voor de analyses op langere termijn. Uiteindelijk zal dit ook leiden tot nieuwe verdienmodellen, waar sommige machinebouwers al mee experimenteren. Bedrijven kopen dan capaciteit bij de fabrikant, die afgerekend wordt per spindeluur. Omgekeerd zullen uitbesteders geen orders meer plaatsen bij hun toeleveranciers, maar blokken productiecapaciteit op specifieke machines kopen.
Het commando 'deur open' kan bij de ene machinebouwer semantisch heel anders omschreven zijn dan bij de andere. Er is nooit een wereldwijde standaard opgesteld
HOE NU VERDER?
De VDW heeft, samen met alle grote besturingsfabrikanten en een aantal machinebouwers, op EMO 2019 de mogelijkheden van umati gedemonstreerd. Enkele besturingsontwikkelaars gaven niet alleen bij hun klanten op de beurs, maar ook op de eigen stand demonstraties van de mogelijkheden van umati.
Tot nog toe zijn er twintig zogenaamde ‘use cases’ uitgewerkt, zoals het overzicht van de productie, de voortgang van een programma, machinestatus, orderafhandeling et cetera. Met ruim 100 gestandaardiseerde parameters worden deze beschreven. Deze parameters zitten in de OPC UA-server die de fabrikanten in de machine inbouwen, willen ze de communicatiestandaard integreren. umati zorgt dat de data eenvoudig uitgelezen worden. Daarna is het aan softwareontwikkelaars om iets met deze data te doen.
Acceptatie
De VDW toonde de eerste concrete producten op EMO in Hannover. Tegelijkertijd is dit echter slechts het begin: umati 1.0, aldus de projectleider bij de VDW. Het aantal toepassingen zal verder uitgebreid worden. Belangrijker is echter de vraag hoe het met de acceptatie uitziet. Willen maakbedrijven deze data wel uitlezen en willen ze daarmee blijven werken in hun fabrieken? Het ligt voor de hand dat met name de grote OEM’ers het voortouw nemen. Of kmo’s snel hierin stappen, valt te bezien.
De tweede vraag is hoe snel aanbieders van meer generieke systemen marktaandeel winnen. En welke ontwikkelingen in de VS met betrekking tot MTConnect de komende tijd aangekondigd zullen worden. De standaardinterface voor de werktuigmachine is in ieder geval nog geen gelopen race.
CNC-besturing in de cloud
MTConnect en umati zijn voor oplossingen die de verdere digitalisering van de productieprocessen, met daarin CNC-machines, vereenvoudigen. De machinebesturing an sich en de HMI (Human Machine Interface) veranderen hierdoor niet wezenlijk. Toch zijn er ook op dit vlak ontwikkelingen gaande.
In Nieuw-Zeeland hebben recent enkele wetenschappers de kaders geschetst voor een CNC-besturing die in de cloud draait. Aan de Universiteit van Auckland in Nieuw-Zeeland is zo’n model ontwikkeld. Men ziet kansen om de CNC-besturing los te koppelen van de hardware en ze aan te bieden als een dienst. Via het internet worden dan de signalen aan de CNC-machine doorgegeven. Een van de belangrijkste voordelen die de Nieuw-Zeelandse wetenschappers zien, is dat er veel meer gebruik kan worden gemaakt van geavanceerde algoritmes om de productiemachines aan te sturen. Men ziet zelfs een koppeling naar VR en AR. Operators zullen de machine bedienen met een AR-bril, en niet meer via de typische HMI op de besturingskast.
Volgens deze onderzoekers functioneert de digitale tweeling van de machine – in de cloud – als de hersenen van de fysieke machine. Door realtimedatacommunicatie denken zij dat het mogelijk wordt om vanuit de cloud het bewerkingsproces te optimaliseren en aan te sturen. Zij constateerden toen eveneens dat een gestandaardiseerde wijze van data-acquisitie wel iets is wat snel opgepakt moet worden. MT Connect is volgens hen snel te implementeren, maar slechts read-only. OPC UA werkt bidirectioneel (dus voor monitoring en besturing), maar de implementatie is complex.