Poedercoaten… Een bijzondere manier van metaalconservering
Voorbehandeling essentieel voor het eindresultaat
Poedercoaten is een elektrostatisch proces, waarbij elektriciteit wordt gebruikt om de poedercoating op het object aan te brengen. De voorbehandeling is daarbij essentieel voor het eindresultaat, en gaandeweg kunnen zaken als kleur- en materiaalkeuze, het Faraday-effect, het applicatie- en het moffelproces het eindresultaat in positieve of negatieve zin beïnvloeden. Wanneer met deze factoren voldoende rekening wordt gehouden, is men verzekerd van een stevige en fraai ogende barrière tussen de buitenlucht en het gecoate voorwerp.
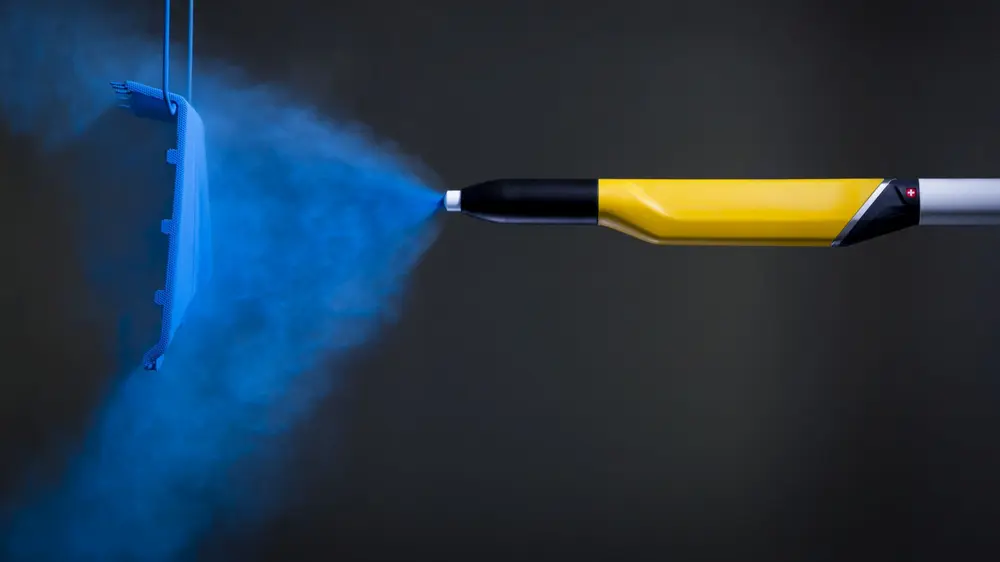
Wat is poedercoaten?
Poedercoaten ‒ ook wel poederlakken of poederverven genoemd ‒ is een efficiënte, duurzame en milieuvriendelijke vorm van metaalconservering, geschikt voor (thermisch verzinkt of gemetalliseerd) staal, RVS en aluminium. Het behandelen van andere materialen kan, maar die moeten dan wel geleidend zijn en in staat zijn de moffeltemperatuur – 180 à 200 °C − te weerstaan.
Een belangrijk doel van poedercoating is het beschermen van producten tegen invloeden van buitenaf door een stevige, fraai ogende barrière aan te brengen tussen de buitenlucht en het voorwerp dat is gecoat. Die barrière biedt bescherming tegen water, zuurstof en weersinvloeden. De levensduur wordt hierdoor aanmerkelijk verlengd doordat corrosie (roestvorming) wordt voorkomen en doordat krassen bijvoorbeeld minder permanente schade aanrichten.
Poedercoaten is een bijzondere en volgens deskundigen ook een van de beste manieren om deze barrière aan te brengen. Het toepassingsgebied varieert van staalconstructies, aluminium kozijnen, ramen, deuren en kantoormeubilair tot auto-onderdelen, landbouwmachines en radiatoren.
“Het periodiek reinigen van de laklaag en een tijdige reparatie van beschadigingen dragen bij tot een langere levensduur”
Hoe verloopt poedercoaten?
Bij poedercoaten wordt een poeder langs elektrostatische weg aangebracht op een object. Het verschil met het aanbrengen van een normale coating of van verf is dat elektrostatisch poeder geen oplosmiddel bevat. Het hechtingsproces komt tot stand door de aantrekkende werking tussen de positief of negatief geladen poederdeeltjes en het geaarde object (neutraal). Door het ladingsverschil blijft het poeder tijdelijk aan het metaal ‘plakken’ (het kan zijn lading niet kwijt), waarna het in een oven wordt uitgehard.
In combinatie met een verzinkte ondergrond of staal voorzien van een KTL-lak ‒ KTL staat voor Kathodische Tauch Lackierung, een elektrostatisch verfproces waarbij het te verven deel wordt ondergedompeld in een verfbad ‒ biedt poederlakken een duurzame bescherming tegen corrosie en uitstekende bestendigheid tegen (extreme) weersinvloeden. Het proces kent vaste stappen die elkaar doorgaans ononderbroken en veelal volledig geautomatiseerd opvolgen. Elke stap wordt gekenmerkt door specifieke procesparameters die nauwgezet worden gemonitord aan de hand van permanente kwaliteitscontroles.

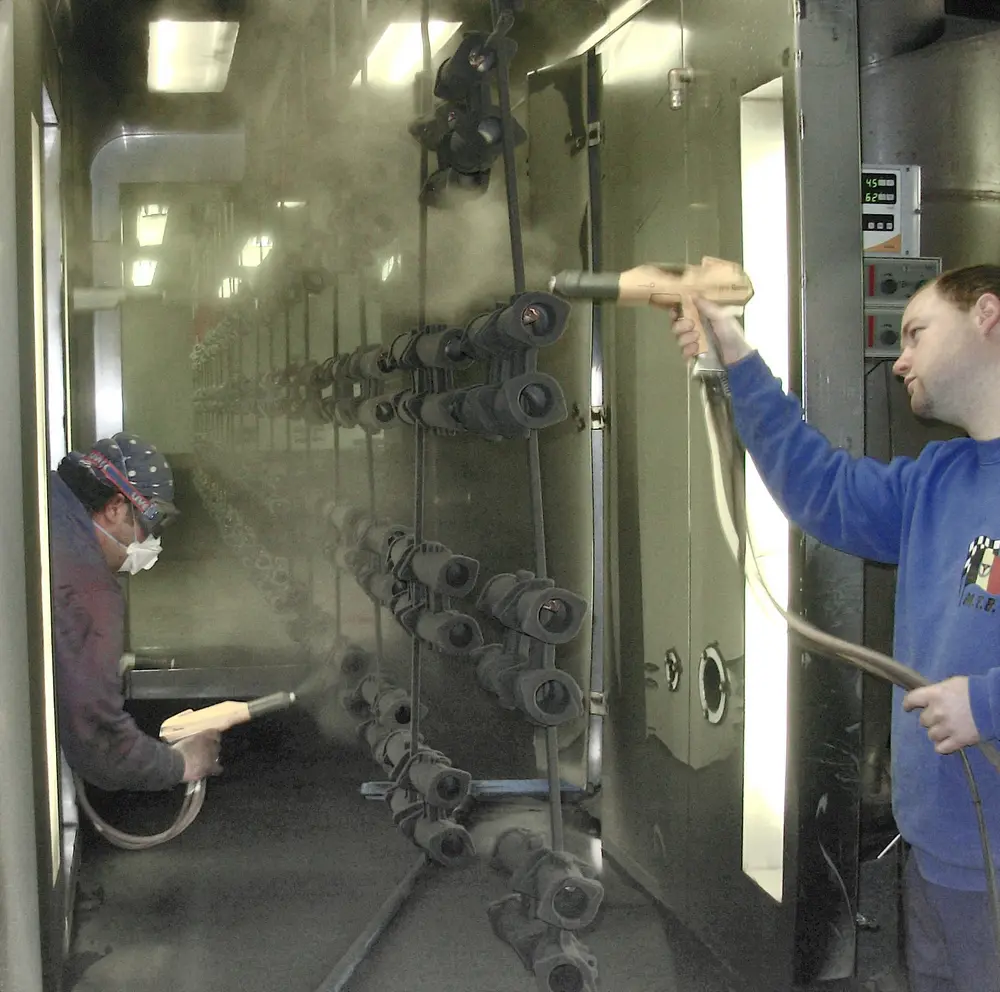
Soorten poedercoatings
Men onderscheidt twee hoofdcategorieën: thermoharders en thermoplasten. Thermoharders (90%) bevatten een zogeheten crosslinker; een verbinding die in staat is twee polymeerketens aan elkaar te koppelen. Thermoplasten (10%) worden niet gemoffeld; ze smelten en vloeien uit op het verwarmde werkstuk, en vormen aldus bij afkoeling de uiteindelijke coating. Poedercoatings worden doorgaans ingedeeld op basis van het gebruikte bindmiddel.
Polyesterpoedercoating wordt meestal toegepast als monolaag of als deklaag in een tweelagensysteem, en geeft zowel kleur als bescherming. Polyesterpoeder wordt specifiek ingezet voor buitentoepassing, maar is ook geschikt voor binnentoepassingen. Polyurethaan is gemakkelijk te reinigen en wordt mede daardoor voornamelijk toegepast om graffiti tegen te gaan. Het is als het ware de ‘antivandalismecoating’.
Epoxy-polyester poedercoatings zijn alleen geschikt voor toepassingen binnen (niet uv-bestendig), bijvoorbeeld voor huishoudelijke apparatuur en CV-radiatoren. Metallics en structuurpoeders kunnen aanleiding geven tot een wolkvormig effect en tintverschillen. Dit is onvermijdelijk en eigen aan deze poeders omwille van de reflectie van de metallieke deeltjes in de poedercoating bij verschillende lichtinval.
Voorbehandeling
Bij poedercoaten is het van belang de op het object aanwezige onzuiverheden te verwijderen. Het kan daarbij gaan om stof, vuil afkomstig uit de werkplaats, vingerafdrukken, smeermiddelen en/of oliën, maar ook om conserveringsmiddelen ‒ gebruikt tijdens het transport en de opslag ‒ en/of restanten van mechanische bewerkingen. Er zijn twee mogelijkheden: mechanische of chemische voorbehandeling.
Mechanische voorbehandeling
Van de mechanische toepassingen wordt stralen het meest toegepast, en dan met name bij het poedercoaten van zwaardere materialen: dikke(re) platen, buizen of gietwerk. Gewoonlijk gebeurt dit met behulp van hoekige/kantige staalgrit. Dit wordt onder hoge druk naar het werkstuk geblazen (de klassieke methode), dan wel geworpen (straalwerpmachine). Het resultaat is een zuiver licht geruwd, egaal en schoon oppervlak dat een goede hechting van de poedercoating mogelijk maakt; een te glad oppervlak kan namelijk hechtingsproblemen veroorzaken.
Chemische voorbehandeling
Bij een chemische voorbehandeling is een belangrijke stap het (alkalisch) ontvetten. Vet en eventueel achtergebleven stof worden daarbij verwijderd zonder dat het metaaloppervlak daarbij wordt aangetast. Beitsen is een reinigingsmethode waarbij roest en ook de gloeihuid worden weggenomen en waarbij het oppervlak in zeer lichte mate wordt geruwd. Voor beide methoden kunnen dompelbaden of sproeitunnels worden gebruikt. Na het ontvetten en/of beitsen brengt men, voordat de poedercoating zelf wordt aangebracht, doorgaans een zogeheten conversielaag aan; een goed hechtende laag die wordt verkregen door het metaaloppervlak chemisch te laten reageren met actieve elementen in een vloeibare fase. Een dergelijke conversielaag zorgt voor een verbetering van zowel de hechting als de corrosiewerende eigenschappen.

Waar poedercoaten?
Het poedercoaten zelf vindt plaats in een poedercabine. Poeder bestaat uit bindmiddel, pigment, vulstof, verharder en additieven, en wordt door een venturi-luchtstroom (perslucht) getransporteerd naar het pistool. Door de poederdeeltjes met een elektrode een negatieve lading te geven, ontstaat tussen het pistool en het product een elektrisch veld. Dit gebeurt door het creëren van een spanningsveld (corona-oplading = negatieve oplading) dan wel door wrijving in het pistool (tribo-oplading = positieve oplading). Vanuit het pistool bewegen de poederdeeltjes zich richting het geaarde werkstuk volgens vaste lijnen, de zogeheten veldlijnen. Na het doorlopen van het elektrisch veld komen ze op het product terecht en hechten ze zich waar de (denkbeeldige) veldlijn eindigt. Door deze ‘lijnenverdeling’ komt op de buitenste hoeken het meeste poeder terecht, en is het vaak moeilijk om in holle ruimtes en hoeken te spuiten. Dit natuurlijke verschijnsel wordt het Faraday-effect genoemd. De poederdeeltjes hechten zich aan het geaarde voorwerp doordat ze als gevolg van de hoeveelheid poederdeeltjes die het object bereiken hun lading niet langer kwijt kunnen. Ook de achterzijde van het voorwerp wordt deels met poeder bedekt, poeder dat bij het conventionele verfspuitproces als overspray verloren zou zijn gegaan. De overspray kan worden teruggewonnen en hergebruikt middels een cycloon. Poederdeeltjes < 10 micron worden afgevoerd naar een afvalfilter, de deeltjes ≥ 10 micron kunnen opnieuw worden gebruikt.
Moffelen
De gecoate materialen gaan vervolgens in de oven waar het poeder smelt en vervolgens uithardt. Dit zogeheten moffelproces vindt plaats in speciale ovens bij temperaturen variërend tussen de 160 en de 210 °C; een en ander is afhankelijk van de uithardingstemperatuur van het object, de dikte van het metaal en het type thermohardend poeder dat wordt gebruikt. Tijdens de opwarmfase transformeren de vaste poederlakdeeltjes eerst naar een vloeibare (verf)vorm, waarbij de substantie als het ware uitvloeit over het product en zich hecht aan het oppervlak. Tijdens het verhittingsproces reageren de verschillende poedercomponenten met elkaar tot een polymeer (polymerisatie): kleine moleculen worden door middel van covalente bindingen samengevoegd tot een lange, stevige keten. Naarmate de temperatuur verder stijgt, wordt de substantie stroperig, een proces dat (aan)geleren wordt genoemd, om ten slotte uit te harden tot een vaste verffilm. Na afloop van het moffelproces vindt doorgaans een kwaliteitscontrole plaats. Er wordt gekeken naar eventuele vervuilingen die onder meer het gevolg kunnen zijn van omgevingsvervuiling, een vuile ondergrond, een slechte poederkwaliteit en/of verontreiniging van de moffeloven.
Na metaalbewerking en op geëxtrudeerde profielen kunnen scherpe randen achterblijven waar het poeder na het smelten vaak wegtrekt. Het resultaat is een onvoldoende kantendekking en een verhoogde kans op corrosie. Is de vereiste afrondingstraal niet haalbaar, dan verdienen grotere laagdikten de voorkeur en dient te worden overgestapt naar een tweelagensysteem. Een minimale afrondingsstraal van 2 mm is daarbij wenselijk, zodat lakopbouw kan plaatsvinden.
Wanneer (niet) kiezen voor poedercoating?
Voordelen
- poederverf bevat geen oplos- en/of verdunningsmiddelen of zware metalen;
- het niet-gehechte poeder (de overspray) kan worden hergebruikt aangezien het onveranderd blijft tijdens het verstuiven;
- verlenging van de levensduur van het object door een goede uv-, weers- en krasbestendigheid;
- relatief eenvoudig aan te brengen (beheerst proces);
- opbouw van voldoende laagdikte, doorgaans 60 à 80 µm per laag.
Nadelen
- moffelen is een energie-intensief proces;
- het te behandelen object dient geleidend te zijn en moet bestand zijn tegen hoge moffeltemperaturen, omdat anders vervorming optreedt;
- er is een intensieve voorbehandeling noodzakelijk (het oppervlak dient 100 procent schoon te zijn);
- vanwege het moffelproces is de techniek uitsluitend toepasbaar in een industriële omgeving.
Eventuele overspray kan worden teruggewonnen en herbruikt middels een cycloon. Poederdeeltjes < 10 micron worden afgevoerd naar ene afvalfilter, de deeltjes > 10 micron kunnen opnieuw worden gebruikt (Foto: Kluthe Benelux)
Onderhoud
Poedercoatings hebben onderhoud nodig: het periodiek reinigen van de laklaag en het tijdig repareren van beschadigingen zal de duurzaamheid verlengen. Factoren die van invloed zijn op de frequentie zijn:
- de situering: bij constructies ‘op het zuiden’ is er sprake van een hogere uv-belasting;
- de warmteabsorptiecoëfficiënt: donkere kleuren absorberen meer warmte en worden derhalve meer belast;
- de luchtverontreiniging in de directe omgeving.
Wanneer de laklaag van het behandelde productfrequent genoeg wordt onderhouden, is men verzekerd van een stevige en fraai ogende barrière tussen de buitenlucht en het gecoate voorwerp, dat hierdoor bestand is tegen invloeden van buiten waaronder hoge temperatuurschommelingen, de inwerking van bepaalde verbindingen (bijvoorbeeld zeezout), weersinvloeden en/of vandalisme (‘hufterproof’).
Met dank aan: Fédération Metalliseurs de Belgique, Inplasco, Kluthe Benelux, Reiter, Straaltechniek en VOM.