Duurzaamheid als aanjager voor innovaties in poedercoating
Als er één woord is dat de markt voor poedercoaten de komende tijd domineert, is het duurzaamheid. De inzet op het verduurzamen raakt de oppervlaktebehandelaars aan veel kanten: van de nieuwe toepassingen voor coatings en het terugdringen van de CO₂-impact van de processen tot het zoeken naar nieuwe, biobased concepten voor de beschermingslaag, die op zichzelf misschien wel de ultieme factor is bij het verduurzamen van producten.
De Europese klimaatplannen hebben flinke gevolgen voor de coatingindustrie. Neem bijvoorbeeld de transitie naar hernieuwbare energie, met over enkele jaren een verplicht afscheid van de verbrandingsmotor. Autofabrikanten lakken bij EV’s meer dan alleen de carrosserie. Zo ontstaan er meer nieuwe markten voor de sector. Tegelijkertijd wil Brussel dat ook de industrie verduurzaamt en minder energie en grondstoffen verbruikt. Poedercoaten is een heel efficiënt proces, omdat tot wel 98% poederrendement wordt gehaald.
Patentaanvragen
Toch neemt de druk op de producenten van poedercoatings toe. Een voorbeeld is de komst van de eerste coatingsystemen gebaseerd op hernieuwbare grondstoffen, vooral als die ook nog eens vanuit de circulaire gedachte zijn ontwikkeld. Het aantal octrooitaanvragen voor zowel biogebaseerde bindmiddelen als vulmiddelen neemt de laatste jaren gestaag toe. Van de 2.800 gepubliceerde octrooien in de laatste 20 jaar, is het merendeel in het laatste decennium gepubliceerd. De octrooien voor biogebaseerde bindmiddelen zijn daarbij ruim in de meerderheid. De belangrijkste bindmiddelen zijn acrylaat, epoxy, PLA en urethaan.

Alternatief voor Chroom 6
Een stof waar de sector een alternatief voor zoekt is chroom 6. Dat werd lange tijd gebruikt in de voorbehandeling van producten waarvan de poedercoatlaag het Qualicoat Seaside-label vereist. Chroom 6 zorgt voor een goede hechting en voorkomt het loslaten van de beschermende laag gevolgd door corrosievorming. Poedercoatbedrijven zijn op zoek naar alternatieven.
De hechting is een essentieel aspect van de kwaliteit van een poederlaklaag
Tijdens de beurs voor oppervlaktetechnologie MES 2021 werd een alternatief gepresenteerd waarbij men pre-anodisatie toepast. Met een elektrochemisch proces worden de metalen onderdelen, nadat ze zijn geborsteld en in een alkalisch en zuur beitsbad zijn geweest, voorzien van een dunne aluminiumoxidelaag. Die laatste wordt in een bad aangebracht en voorzien van een pre-anodiseerlaag van constant 10 µm dik. Die dient als versterker voor de hechting van het poeder. Over de pre-anodisatielaag wordt nog een conversielaag aangebracht om de hechting verder te verbeteren. Daarmee haalt men de eisen van het Qualicoat Seeside-label.
Invloed op de hechting
De hechting is een essentieel aspect van de kwaliteit van een poederlaklaag. Een van de pistes om poedercoaten duurzamer te maken, is het verbeteren van de hechting. Als men erin slaagt om de hechting aan het substraat te verbeteren kan men immers in de toekomst wellicht dunnere coatings toepassen of de levensduur verlengen, wat op lange termijn tot minder grondstoffenverbruik leidt.
Een belangrijke stap in die richting is gezet aan de Vrije Universiteit Brussel, waar een onderzoeksgroep aan de slag is gegaan met het bepalen van de interactie tussen verf en metaal. De onderzoekers onderzochten verschillende vragen. Wat er gebeurt op microscopisch niveau als je een coating aanbrengt op een metaal? En hoe kun je de hechting tussen de twee verbeteren? Welke bindingen kunnen daarvoor zorgen? Dat deden de onderzoekers door met infrarood en röntgenstralen door de lagen heen te kijken. Tegelijkertijd liet men een elektrisch veld door een dunne metaaloxidefilm gaan. Zo was infraroodspectroscopie mogelijk en kon de interactie van de metaaloxidelaag met de coating of verflaag geanalyseerd worden.
Het onderzoek heeft veel informatie opgeleverd, bijvoorbeeld over het effect van de staat van het oppervlak en de verbinding met de polymeer. De onderzoekers verwachten dat in de toekomst de sterkte van de hechting beter afgestemd kan worden op de toepassing. Het grootste rendement zal moeten komen uit de langere levensduur van de coating door de betere hechting, omdat men de coatings vanaf de basis anders gaat ontwikkelen, meer gericht op een specifieke toepassing in bepaalde omstandigheden.
GROEIMARKT ELEKTRISCHE AUTO'S
Een van de beloftevolle markten voor poedercoating is de automobielmarkt, dankzij het elektrificeren van de auto. Autofabrikanten zien poedercoating als een goede oppervlaktebehandeling voor uiteenlopende onderdelen van de elektrische auto, uiteenlopend van stator en rotor tot en met batterijbehuizingen. Dat is met name een interessante ontwikkeling voor de producenten van de poedercoatings.
Onderzoekers verwachten dat de komende jaren de markt voor het coaten van onderdelen in de aandrijflijn net zo groot zal worden als die voor de carrosserie. De markt zou tot 2026 in omvang vervijfvoudigen wereldwijd.
Plasmabehandeling
Een technologie die de laatste tijd vaker wordt toegepast om kunststof- en composietdelen voor te behandelen, is koude plasma. Deze materialen hebben dikwijls van zichzelf slechte hechtingseigenschappen door hun laag-energetische oppervlakken. Tot nog toe worden voor het verbeteren vaak middelen met VOC’s ingezet. Die staan echter onder druk uit milieuoverwegingen. 80% van de emissie van VOC’s wordt veroorzaakt door het middel dat de adhesie verbetert. Een alternatief is het gebruik van plasma in de voorbehandeling. De deeltjes die het plasma genereert, reinigen door hun hoge snelheid het oppervlak zeer effectief en activeren het tegelijk. Dat zorgt ervoor dat de poedercoating beter kan vloeien en zich beter aan het oppervlak hecht.
Op lagere temperatuur werken levert niet alleen 50% energiebesparing op, het zorgt ook voor een compacter proces
Lagetemperatuurpoeders
Om het energieverbruik bij poedercoaten te verminderen, ontwikkelen de coatingfabrikanten poeders die bij een lagere temperatuur uitharden. Normaal gebeurt dat bij 200 °C. In Europa is dat al verschoven naar 180 °C en tegenwoordig zelfs naar 160 °C. De nieuwe generatie poederlakken kan bij temperaturen tussen 80 en 100 °C uitharden. Die laatste stap is een lastige geweest. Met elektrostatische energie en hitte kan men nu temperatuurgevoelige oppervlakken poederlakken. De moeilijkheid is het waarborgen van de kwaliteit, zoals de kleurstabiliteit.
De uv-uithardende coatings die oorspronkelijk voor het uitharden van coatings op hittegevoelige materialen ontwikkeld werden, verlagen de temperatuur nog verder. Deze laagtemperatuurcoatings zijn vooral goed voor toepassingen waarbij dubbele lagen coating aangebracht moeten worden. Door de dikte van de laag duurt het doorgaans lang voordat ze is uitgehard. Door op een veel lagere temperatuur te werken, hardt de laag sneller uit en kan men de tweede laag in dezelfde processtap aanbrengen. Naast 50% energiebesparing levert het dus ook nog eens een compacter proces op.
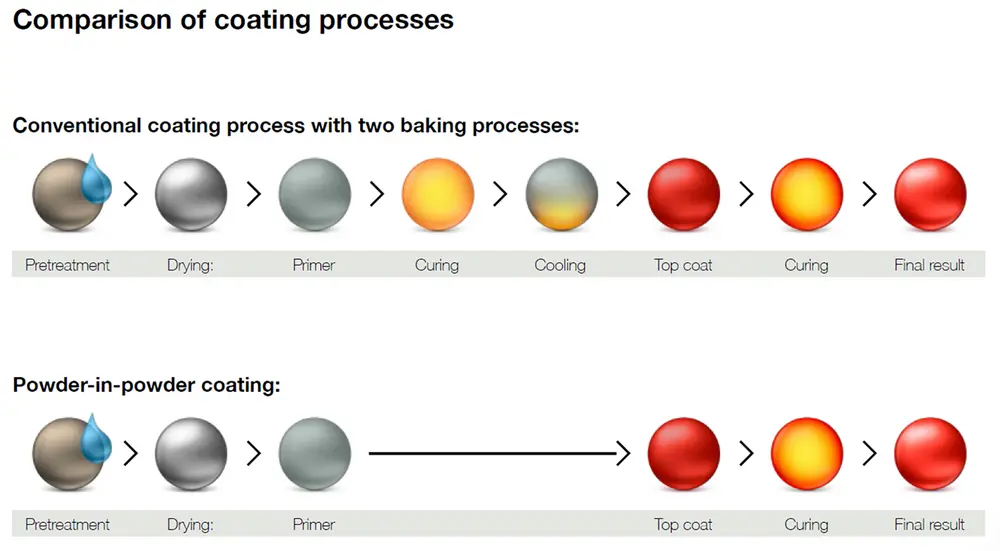