Additive manufacturing van keramische materialen
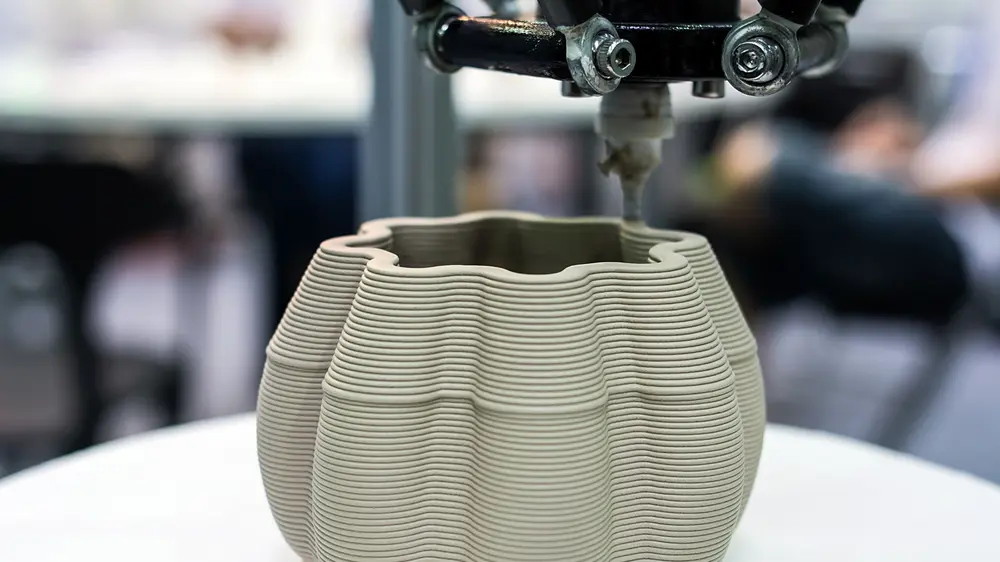
Keramische materialen worden algemeen beschouwd als de beste keuze voor extreme omstandigheden op lange termijn. Ze bieden tal van voordelen ten opzichte van metalen en hun belangrijkste toepassingen zijn precies gelinkt aan één of meer van die pluspunten. Door de hoge hardheid vertoont technisch keramiek echter ook enkele nadelen. Wie de voordelen van additive manufacturing wil koppelen aan die van dit materiaal, stoot bijgevolg op enkele uitdagingen.
Technisch keramiek
Voordelen
Keramisch materiaal is over het algemeen de beste keuze voor extreme gebruiksomstandigheden wat temperatuur, druk, corrosie of een mix van die elementen betreft, en dit over een lange periode.
Ten opzichte van metalen biedt keramisch materiaal meerdere voordelen, waaronder:
- weerstand tegen hoge temperaturen (lage thermische uitzetting) en corrosie;
- hoge hardheid en dus hoge slijtageweerstand;
- hoge druksterkte;
- lagere densiteit;
- specifieke eigenschappen die inherent zijn aan het materiaal zelf: bio-, elektrisch, magnetisch of optisch.
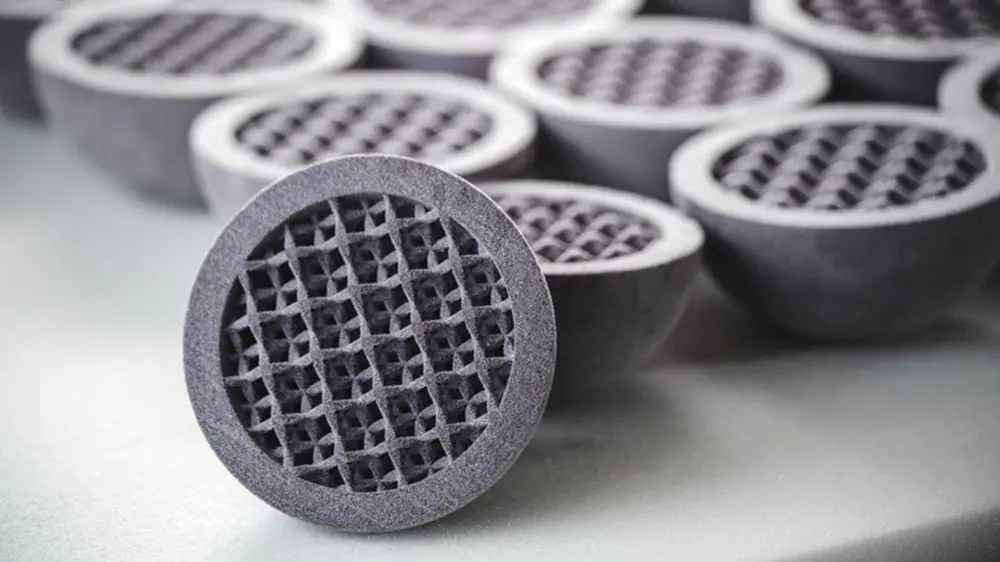
Toepassingen
De belangrijkste toepassingen van technisch keramiek zijn gelinkt aan één of meer van deze voordelen: producten van hoge waarde (bv. horloges en juwelen), slijtageonderdelen zoals voor slijp- en werktuigmachines, onderdelen voor thermische bescherming of keramische coatings op metalen onderdelen, chemisch resistente producten in de chemische en agrovoedingssector, elektrische isolatoren, supergeleiders, biocompatibele implantaten en botvervangers …
Nadelen
Door zijn hoge hardheid vertoont keramisch materiaal echter ook een aantal nadelen: een geringe vervormbaarheid en een hoge brosheid, wat het gebruik ervan in structurele toepassingen beperkt. Keramische materialen zijn ook moeilijker te bewerken dan andere materialen.
Additive manufacturing is één van de te overwegen opties en de opportuniteiten ervan worden momenteel onderzocht. De grootste uitdagingen vandaag zijn gelinkt aan de betrouwbaarheid van en reproduceerbaarheid op bestaande AM-machines.
Beperkt potentieel
Additive manufacturing kan een optie zijn om keramische onderdelen te vervaardigen. De technologie wordt momenteel al gebruikt voor tandheelkundige en biomedische toepassingen, automotive, lucht- en ruimtevaart. Maar net zoals het geval is met andere types van materialen, is het niet realistisch ervan uit te gaan dat AM alle problemen van de keramische industrie zal oplossen.
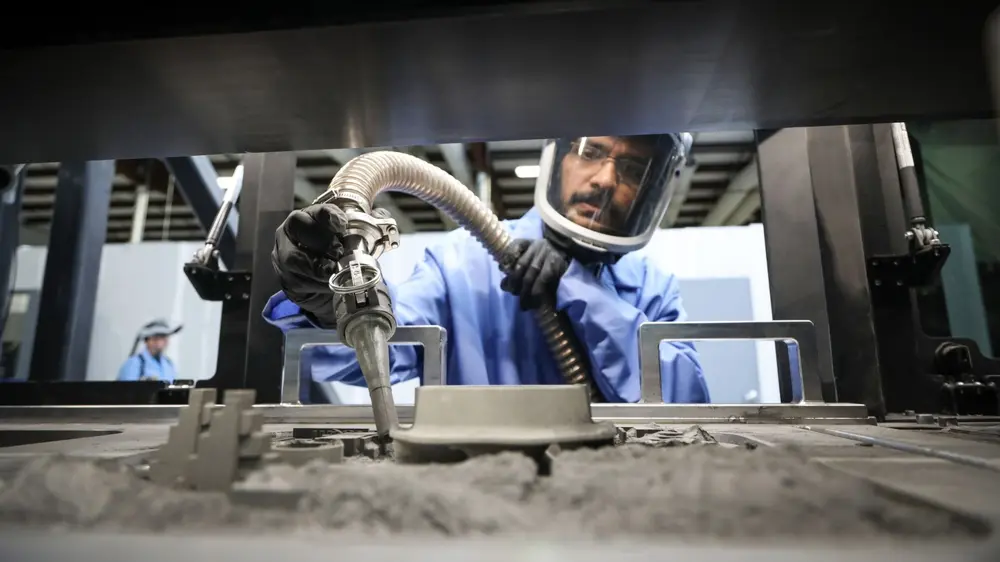
Productie via AM
Het aantal keramische materialen dat momenteel beschikbaar is voor AM-processen is klein en de procedés zijn complex. Ze bestaan uit verschillende stappen (indirecte processen) en er moet rekening gehouden worden met de volledige procesketen voor de ontwikkeling van nieuwe materialen. Daarom is de markt nog altijd in ontwikkeling, gaat het om een niche en vinden we vandaag nog geen grote succesverhalen met keramisch geprinte materialen in de voornaamste sectoren.
Met traditionele productieprocessen kunnen goede prestaties en functionaliteit worden bereikt. Eenzelfde ontwerp kan in hoge volumes worden geproduceerd, met een gemiddelde complexiteit. AM biedt meer ontwerpvrijheid en geeft de kans iets nieuws te creëren met minder – of in elk geval andere – beperkingen aan het procedé.
Opportuniteiten
Anders dan bij klassieke productie leidt schaalvergroting bij AM niet noodzakelijk tot een economisch voordeel, maar kan het wel complexiteit en functionaliteit aan een onderdeel toevoegen.
Er zijn twee mogelijke strategieën:
- Een puur productiegedreven strategie, waarbij onderdelen alleen om kostenefficiënte redenen opgebouwd worden met AM. Deze strategie benut het potentieel van AM niet ten volle en is er niet voor geschikt.
- Een innovatief ontwerpgedreven strategie, waarbij AM gebruikt wordt om zeer complexe producten te vervaardigen, omdat het de enige manier is om zulke complexe ontwerpen te produceren, wat de productiekost ook is. Het interessante is hier dat het ontwerp een toegevoegde waarde aan het stuk moet geven op het vlak van performantie en efficiëntie. Deze strategie benut wél het volledige potentieel van AM.
Vandaag is AM van keramische onderdelen een haalbare optie wanneer de stukken klein, complex en op maat (kleine seriegrootte) zijn. De technologie leidt tot een betere efficiëntie, voornamelijk door het ontwerp. AM kent de voordelen van flexibele productie, zonder dat er extra tools vereist zijn en waarbij er een digitale opslag van de geproduceerde stukken is (geen nood aan een voorraad grote matrijzen per klant).
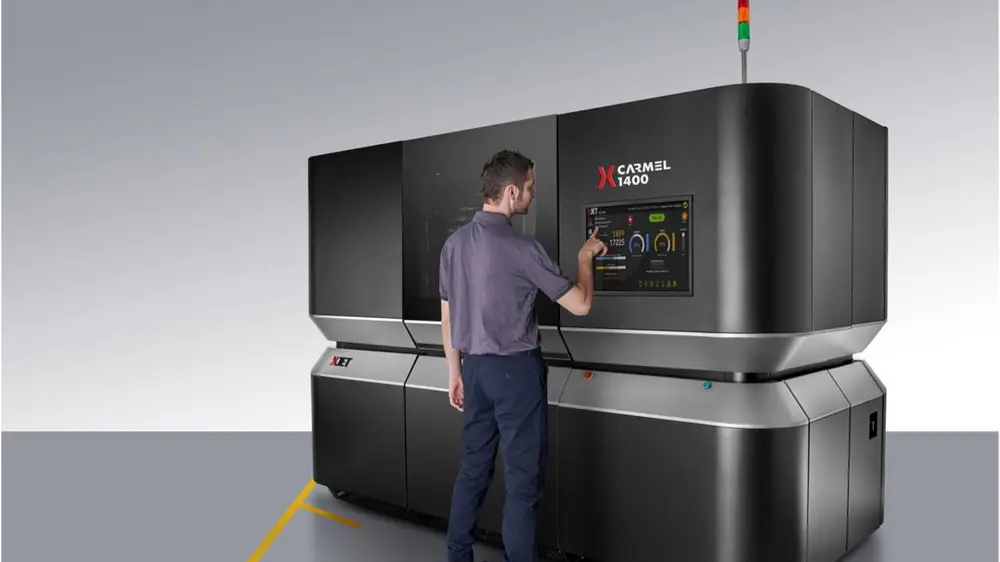
AM-processen voor keramische materialen
Hoewel alle zeven categorieën van AM-processen in theorie kunnen worden aangewend voor keramiek, zijn er slechts enkele daarvan die vandaag al met succes worden ingezet hiervoor. Dat zijn indirecte technologieën: binder jetting, vatpolymerisatie en materiaalextrusie. De onderdelen worden in ‘groene‘ toestand (ongebakken) gevormd via AM met een mengeling van keramisch poeder en organische componenten als bindmiddel. Vervolgens worden deze ontdaan van bindmiddel en gesinterd, zoals bij de klassieke methode.
Uitdagingen
De voornaamste procesuitdagingen met AM van keramische materialen zijn dezelfde als die bij klassieke keramische processen:
- Depositiedichtheid: de finale dichtheid en krimp door sintering zijn gelinkt aan de pakking van het poeder in de groene toestand, die zo hoog mogelijk moet zijn.
- Het sinteren: verschillende problemen en fouten kunnen opduiken tijdens deze thermische cyclus, die verantwoordelijk is voor de finale microstructuur en zo voor de mechanische en fysische eigenschappen van de componenten.
- De finale samenstelling (zuiverheid), die ook enkele van de belangrijkste eigenschappen van technisch keramiek definieert.
Naast deze hindernissen kunnen nog andere specifieke problemen opduiken bij AM-technologieën met keramische materialen. Om een heel dicht keramisch object te genereren, is er heel fijn poeder vereist, wat vaak een heel lage vloei en een lage depositiedichtheid heeft. Dat vraagt om een aanzienlijke hoeveelheid aan organisch materiaal, wat op zijn beurt leidt tot beperkingen in de wanddikte en het volume van de onderdelen, om defecten en een trage opwarmsnelheid tijdens het verwijderen van het bindmiddel te vermijden. Dat is waarom bestaande AM-technologieën voornamelijk geschikt zijn om poreus keramiek, roosterstructuren en stukken met dunne wanden te bouwen, die makkelijk te sinteren zijn zonder barsten, en met een nauwkeurige controle van de finale afmetingen en vorm.
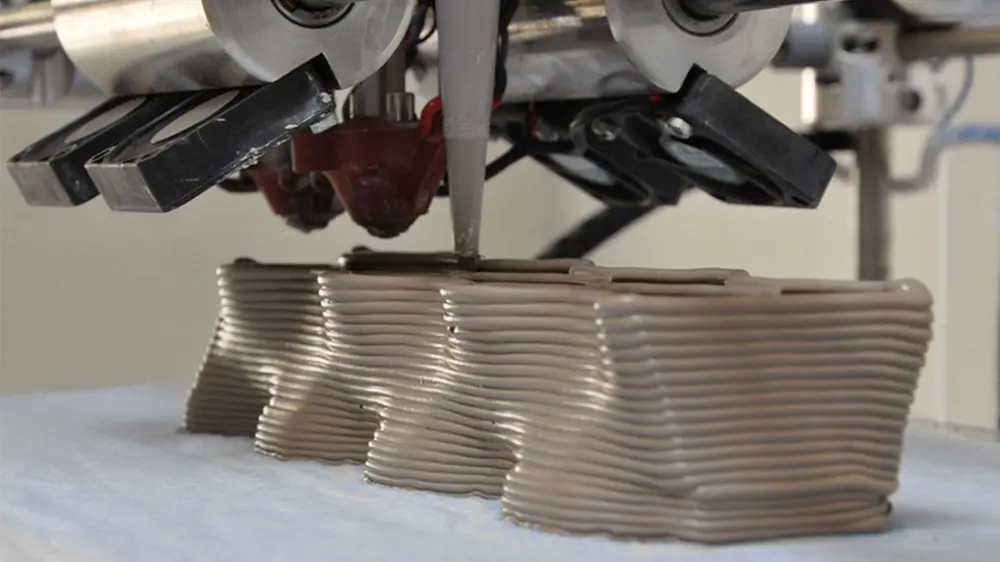
Binder jetting
Binder jetting is een eenvoudige manier om keramische materialen vorm te geven met AM. Lagen poeder worden hierbij uitgespreid en plaatselijk geprint met een organisch bindmiddel dat uitgehard wordt. De geprinte groene stukken moeten vervolgens worden ontdaan van het bindmiddel. Dat gebeurt door alle organische lijm uit te branden en het stuk te sinteren, om zo al het poedermateriaal te densifiëren.
Het proces is snel, eenvoudig (geen steunstructuren nodig) en kan in theorie toegepast worden met elk als poeder beschikbaar materiaal. De meest kritische beperking is dat het printen beter werkt met grove poeders, wat toelaat de deeltjes makkelijk te verspreiden en het vloeibare bindmiddel snel doorheen het poederbed te laten vloeien, om zo de partikels van de geprinte laag en de lagen onderling te verlijmen. Helaas zijn deze dan weer moeilijker te sinteren achteraf, waardoor de mogelijke toepassingen met deze grove poeders vaak beperkt worden tot poreuze onderdelen en geïnfiltreerde structuren. Typisch worden met deze technologie lichtgewicht en complexe onderdelen met hoge performantie gerealiseerd.
De bouwplaten van de verschillende soorten beschikbare machines gaan van een paar centimeters tot verscheidene meters. De printresolutie ligt in het bereik van 50-150 µm. Dimensionele nauwkeurigheid van de volledige korrel overschrijdt 0,2 mm niet.
De voornaamste procesuitdagingen met AM van keramische materialen zijn dezelfde als die bij klassieke keramische processen
Fabrikanten van binder jettingmachines die compatibel zijn met keramische poeders, zijn Voxeljet, Exone, 3DSystems, Desamanera en XJet (Carmel-machine). Leveranciers van keramische materialen voor binder jettingmachines zijn Tethon 3D en Additive Elements.
Materiaalextrusie
Met materiaalextrusie kunnen keramische materialen ruw gevormd worden. Onderdelen worden opgebouwd door laag per laag een kunststof of pastavormig materiaal af te zetten, dat door een spuitkop (nozzle) wordt geëxtrudeerd. Daarna worden de stukken gedroogd, en het bindmiddel uitgebrand en gesinterd, zoals bij klassieke keramische productieprocessen.
Dit proces is snel, maar niet zo eenvoudig als binder jetting, want steunstructuren zijn vereist onder de overhangende delen tijdens het vormgeven. Bovendien zijn door de laagsgewijze depositie van ruw geëxtrudeerd materiaal de onderdelen effectief anistroop in de Z-richting (verticale richting), heeft het oppervlak een trapstructuur en kunnen fijne details hiermee niet worden verwezenlijkt. Deze technologie heeft wel meer ontwerpbeperkingen, zeker voor complexe onderdelen.
Net zoals bij binder jetting-machines liggen de afmetingen van de bouwplaat tussen enkele centimeters en verscheidene meters. De printresolutie hangt af van de afmeting van de geëxtrudeerde draad; meestal in de ordegrootte van een millimeter of meer. De precisie is daarom behoorlijk laag, vergeleken met andere technologieën. Fabrikanten van industriële machines zijn 3D- Potter, 3D-Fugo, Vorm Vrij en WASP (alleen de extrusiekop).
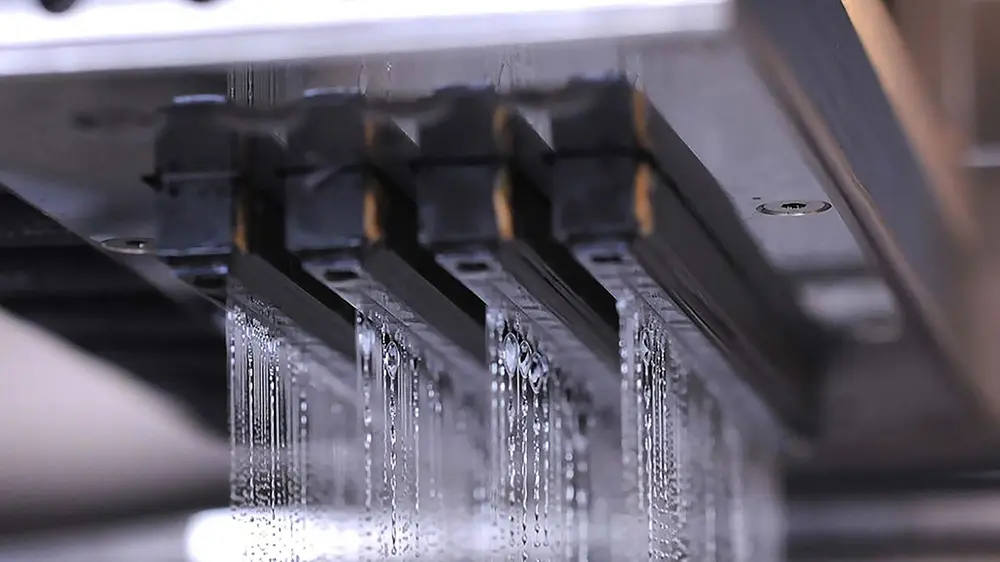
Vatpolymerisatie
Stereolithografie is misschien het meest technologisch mature AM-proces als het om keramische materialen gaat. Het proces is gebaseerd op klassieke stereolithografie: een laser of DLP hardt een vloeibaar polymeer laagsgewijs in een vat uit. In dat geval wordt voor de verwerking een keramisch poeder toegevoegd als vaste lading aan het vloeibare hars, wat het een pasta-achtig aspect geeft. De viscositeit van het pasta-achtige materiaal vraagt om de nodige aanpassingen aan de machine, maar het algemene principe blijft hetzelfde: de pasta wordt in lagen uitgespreid en lokaal verwarmd gecured om het polymeer te doen solidifiëren. Daarna worden de stukken uitgebrand om het bindmiddel te verwijderen en verder gesinterd. Omdat er met een halfvloeibaar materiaal gewerkt wordt, zijn steunstructuren vereist onder alle overhangende delen uit hetzelfde materiaal.
Voordelen van de techniek zijn dat ze kan worden gebruikt met fijne(re) poederkorrels (makkelijk te sinteren), wat interessant is voor de productie van werkstukken met kleine(re) details, een hoge(re) precisie en oppervlakteafwerking. Er is voor dit proces een behoorlijk brede range van beschikbare keramische materialen. De voornaamste nadelen zijn de stabiliteit van het fotopolymeer op lange termijn (omwille van de vervaldatum) voor het printproces, het weghalen van de ondersteuning bij complexe structuren en de moeilijkheid om nieuwe materialen te ontwikkelen die gelinkt zijn aan verschillende factoren inherent aan deze technologie.
De afmetingen van het bouwplatform gaan van 50 tot 500 mm. Dimensionele precisie kan onder 0,1 mm liggen voor een compleet, gecontroleerd proces (printen + debinding-sintering).
Fabrikanten van bestaande machines zijn Lithoz, 3DCeram, Prodways, Admatec en DDM Systems. Tethon 3D en Cerhum zijn leveranciers van keramische materialen, specifiek voor SLA-processen.