La fabrication additive des ceramiques
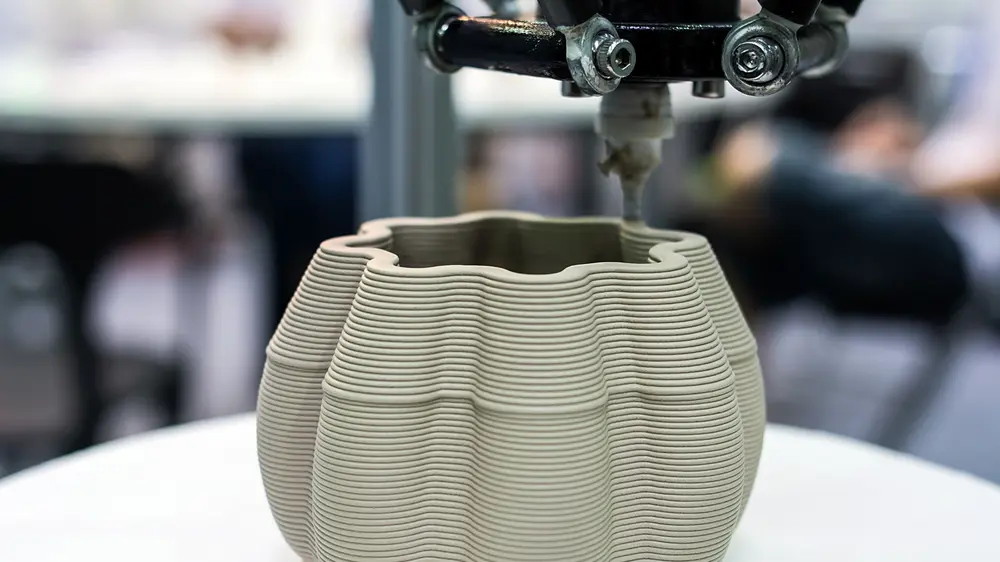
Les matériaux céramiques sont généralement considérés comme le meilleur choix pour les conditions extrêmes à long terme. Ils offrent de nombreux avantages par rapport aux métaux et leurs principales applications sont précisément liées à un ou plusieurs de ces avantages. Toutefois, en raison de leur dureté élevée, les céramiques techniques présentent également certains inconvénients. Lorsqu'on veut combiner les avantages de la fabrication additive avec ceux de ces matériaux, il faut donc relever un certain nombre de défis.
Ceramique technique
Avantages
Le matériau céramique est généralement le meilleur choix lorsqu'on est confronté à des conditions d'utilisation extrêmes en termes de température, pression, corrosion ou mélange de ces éléments sur une longue période.
Par rapport aux métaux, le matériau céramique présente plusieurs avantages, notamment:
- une résistance aux températures élevées • une résistance aux températures élevées (faible dilatation thermique) et à la corrosion;
- une dureté élevée et donc une grande résistance à l'usure;• une grande résistance à la compression;
- une densité plus faible;
- des propriétés spécifiques inhérentes au matériau à différents niveaux: bio, électrique, magnétique ou optique.

Applications
Les principales applications des céramiques techniques sont liées à un ou plusieurs de ces avantages: produits de haute valeur (horlogerie et bijouterie), pièces d'usure pour les rectifieuses et les machines-outils, pièces pour la protection thermique ou revêtements céramiques sur des pièces métalliques, produits chimiquement résistantes pour les secteurs chimique et agroalimentaire, isolants électriques, supraconducteurs, implants biocompatibles et remplacements osseux.
Inconvénients
Toutefois, en raison de sa dureté élevée, le matériau céramique présente plusieurs inconvénients: une faible déformabilité et une grande fragilité, ce qui limite son utilisation dans les applications structurelles. Il est aussi plus difficile à travailler que les autres matériaux.
La fabrication additive est une option à envisager et ses possibilités sont actuellement explorées. Les plus grands défis actuels sont liés à la fiabilité et à la reproductibilité des machines de FA (fabrication additive) existantes.
Potentiel limité
La fabrication additive peut être une option pour le façonnage de pièces en céramique. Cette technologie est déjà utilisée pour des applications dentaires et biomédicales, dans l'automobile et le secteur aérospatial. Toutefois, comme pour d'autres types de matériaux, il n'est pas réaliste de supposer que la FA résoudra tous les problèmes de l'industrie céramique.
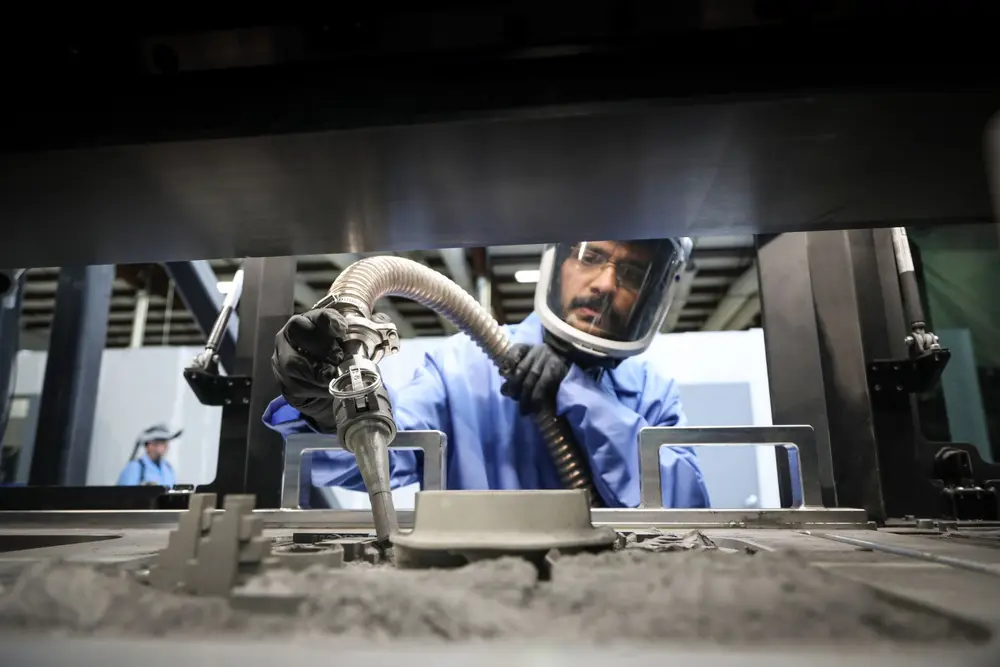
fabrication par FA
Le nombre de matériaux céramiques disponibles pour les procédés de FA est faible et les procédés sont complexes. Ils nécessitent plusieurs étapes et il faut prendre en considération l'ensemble de processus pour le développement de nouveaux matériaux. C'est pour ça que le marché se développe toujours, qu'il s'agit d'une niche et qu'on ne trouve pas encore de grandes réussites avec les matériaux imprimés en céramique dans les principaux secteurs. Les processus de production traditionnels permettent d'obtenir de bonnes performances et fonctionnalités et de produire en grande quantité un même design avec une complexité moyenne. La FA offre une plus grande liberté de conception et donne la possibilité de créer quelque chose de nouveau avec moins de limitations – ou du moins avec des limitations différentes – au niveau du processus.
Opportunités
La FA n'a pas nécessairement d'effet économique par rapport à la production classique mais elle peut ajouter plus de complexité et de fonctionnalité à une pièce.
Il y a deux stratégies possibles:
- Une stratégie purement axée sur la production, où les pièces sont construites par FA uniquement pour des raisons de rentabilité. Cette stratégie n'exploite pas pleinement le potentiel de la FA et n'est certainement pas adaptée à la FA.• Une stratégie purement axée sur la production, où les pièces sont construites par FA uniquement pour des raisons de rentabilité. Cette stratégie n'exploite pas pleinement le potentiel de la FA et n'est certainement pas adaptée à la FA.
- Une stratégie innovante axée sur la conception, où la FA est utilisée pour réaliser des produits très complexes, car elle est le seul moyen de produire de telles pièces, quel que soit le coût de production. Ce qui est intéressant ici, c'est que la conception doit apporter à la pièce une valeur ajoutée en termes de performance et d'efficacité. Cette stratégie exploite tout le potentiel de la FA.
Aujourd'hui, la FA de pièces en céramique est une option viable lorsque les pièces sont petites, complexes et sur mesure (petite série). La technologie entraîne une meilleure efficacité, principalement grâce à la conception.
La FA connaît les avantages d'une production flexible, sans avoir besoin d'outils supplémentaires et avec un stockage numérique des pièces à produites (plus besoin d’un grand espace de stockage pour les moules des pièces de chaque client).
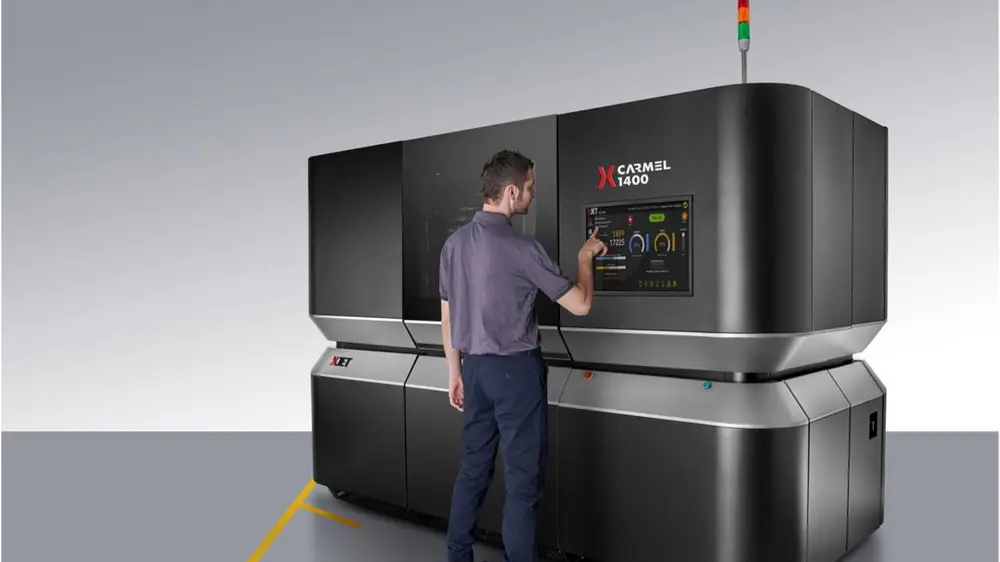
Processus de FA
Théoriquement, les sept catégories de procédés de FA peuvent être utilisées pour les céramiques mais seules trois sont déjà appliquées avec succès aujourd'hui. Il s'agit de technologies indirectes: projection de liant, polymérisation en cuve et extrusion de matériau. Les composants sont formés à l'état 'vert' (non cuit) par FA avec un mélange de poudre céramique et de composants organiques en guise de liant. Ils sont ensuite débarrassés du liant et frittés, comme avec la méthode classique.
Défis
Les principaux défis de la FA des matériaux céramiques sont les mêmes que pour les procédés céramiques classiques:
- Densité de tassement: la densité finale et le retrait par frittage sont liés au tassement de la poudre à l'état vert, qui doit être le plus élevé possible.
- Frittage: divers problèmes et défauts peuvent survenir au cours de ce cycle thermique, qui est responsable de la microstructure finale et donc des propriétés mécaniques et physiques des composants.
- La composition finale (pureté), qui définit également certaines des principales propriétés des céramiques techniques.
Outre ces obstacles, d'autres problèmes spécifiques peuvent surgir dans les technologies de FA avec des matériaux céramiques. Pour produire un objet en céramique très dense, il faut une poudre très fine, qui a souvent une piètre coulabilité et une faible densité de tassement. Cela nécessite une quantité considérable de matière organique, ce qui entraîne une restriction de l'épaisseur des parois et du volume des pièces, afin d'éviter les défauts et une vitesse de chauffage lente pendant l'enlèvement du liant. C'est pourquoi les technologies de FA existantes sont principalement adaptées à la construction de céramiques poreuses, de structures lattices et de pièces à parois minces, qui sont faciles à fritter sans se fissurer, et avec un contrôle précis des dimensions et de la forme finale.
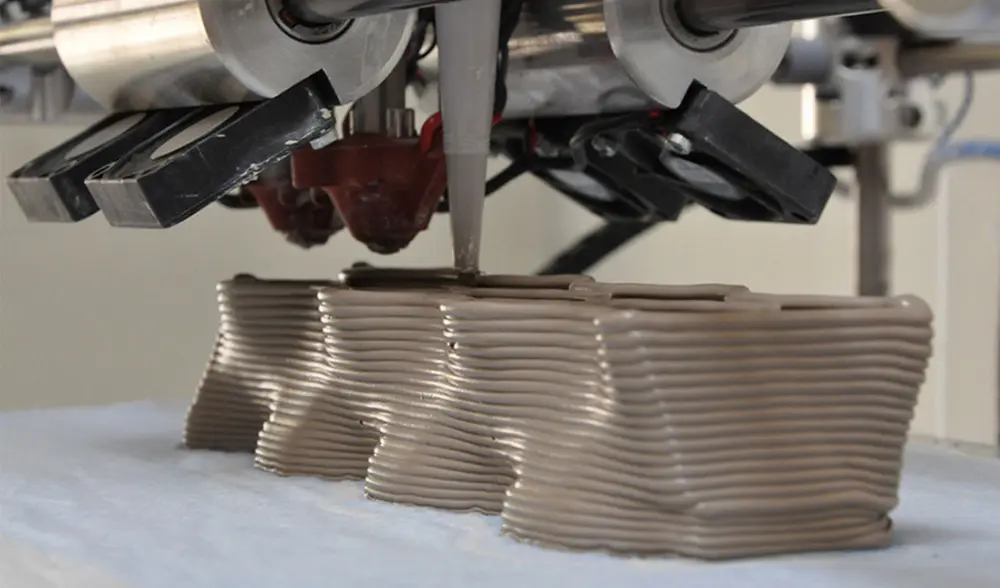
PROJECTION DE LIANT
La projection de liant est un moyen facile de façonner des matériaux céramiques avec la FA. Les couches de poudre sont étalées et imprimées localement avec un liant organique qui durcit. Les pièces vertes imprimées doivent ensuite être débarrassées du liant. Pour ce faire, on brûle toute la colle organique et on fritte la pièce afin de densifier tout le matériau poudreux.
Le processus est rapide, simple (aucune structure de support n'est nécessaire) et peut théoriquement être appliqué avec n'importe quel matériau disponible sous forme de poudre. La restriction la plus critique est que l'impression fonctionne mieux avec des poudres à gros grains, ce qui permet aux particules d'être facilement étalées en couches et au liant liquide de pénétrer rapidement à travers le lit de poudre, afin de coller les particules de la couche imprimée et les couches entre elles. Malheureusement, celles-ci sont plus difficiles à fritter par la suite, de sorte que les applications possibles avec ces poudres sont souvent limitées aux pièces poreuses et aux structures infiltrées. En général, cette technologie est utilisée pour créer des pièces légères et complexes à haute performance.
Les plateaux de fabrication des différents types de machines disponibles vont de quelques centimètres à plusieurs mètres. La résolution d'impression est comprise entre 50 et 150 µm. La précision dimensionnelle de la chaîne complète de fabrication ne dépasse pas 0,2 mm.
Les principaux defis de la FA des materiaux ceramiques sont les memes que pour les procedes ceramiques classiques
Les fabricants de machines de projection de liant compatibles avec les poudres céramiques sont Voxeljet, Exone, 3DSystems, Desamanera et XJet (machine Carmel). Les fournisseurs de matériaux céramiques pour ces machines sont Tethon 3D et Additive Elements..
extrusion de materiau
L'extrusion de matériau permet de mettre en forme des matériaux céramiques de manière grossière. Les pièces sont fabriquées en déposant couche par couche un matériau plastique ou pâteux, qui est extrudé par une buse. Les pièces sont ensuite séchées, et le liant brûlé et fritté, comme dans les procédés classiques de production de céramique.
Ce processus est rapide mais pas aussi simple que la projection de liant car il nécessite des structures de soutien sous les parties en surplomb lors du façonnage. De plus, en raison du dépôt en couches du matériau extrudé, les pièces sont anisotropes en Z (sens vertical), la surface a une structure en escalier et les détails fins ne peuvent pas être réalisés. Cette technologie présente davantage de limites de conception, en particulier pour les pièces complexes.
Comme pour les machines à projection de liant, les dimensions du plateau de fabrication sont comprises entre quelques centimètres et plusieurs mètres. La résolution d'impression dépend de la taille du filament extrudé, généralement de l'ordre du millimètre ou plus. La précision est donc assez faible par rapport à d'autres technologies.
Les fabricants de machines industrielles sont 3D Potter, 3D-Fugo, Shape Free et WASP (uniquement la tête d'extrusion).
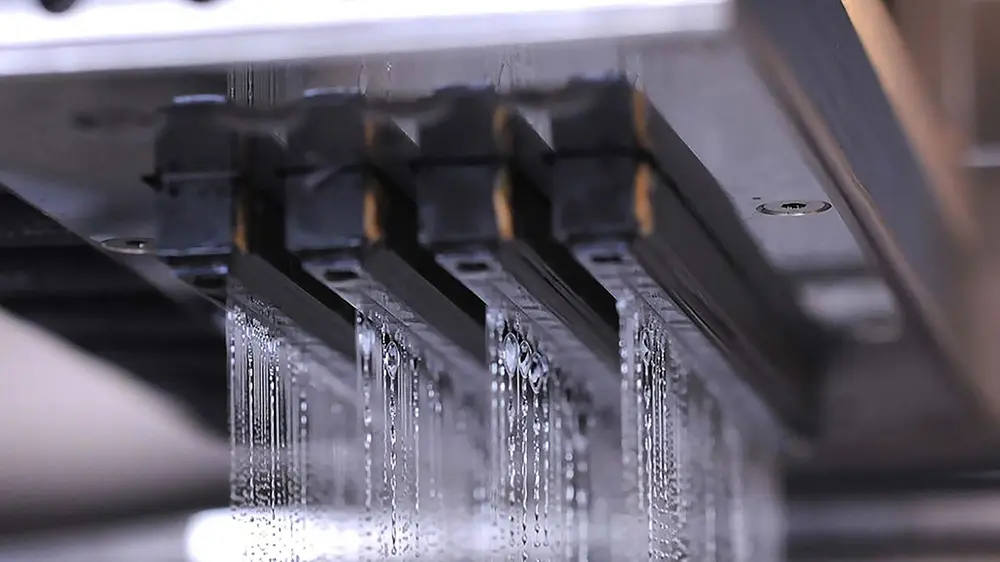
Polymerisation en cuve
La stéréolithographie est peut-être le procédé de FA le plus mature sur le plan technologique en ce qui concerne les matériaux céramiques. Ce procédé est basé sur la stéréolithographie classique: un laser ou un DLP durcit un polymère liquide couche par couche dans une cuve. Une poudre céramique est ajoutée sous forme de charge solide à la résine liquide avant le traitement, ce qui lui donne un aspect pâteux. La viscosité de la matière pâteuse nécessite certains réglages de la machine mais le principe général reste le même: la pâte est étalée en couches exposée localement à de la lumière UV pour solidifier le polymère. Les pièces sont ensuite déliantées pour enlever le liant. Ensuite, elles sont frittées. Comme on utilise un matériau semi-liquide, des supports sont nécessaires sous toutes les parties en surplomb et faites du même matériau.
Les avantages de cette technique sont qu'elle peut être utilisée avec des poudres fines (facile à fritter), ce qui est intéressant pour la production de pièces avec des petits détails, une grande précision et un bon état de surface. Il existe pour ce procédé un éventail assez large de matériaux céramiques. Les principaux inconvénients sont la stabilité à long terme du photopolymère (en raison de la date d'expiration) pour le processus d'impression, la suppression du support pour les structures complexes et la difficulté de développer de nouveaux matériaux liée à divers facteurs inhérents à cette technologie.
Les dimensions de la plate-forme de construction varient de 50 à 500 mm. La précision dimensionnelle peut être inférieure à 0,1 mm pour un processus complet et contrôlé (impression + suppression du liant-frittage).
Les fabricants des machines existantes sont Lithoz, 3DCeram, Prodways, Admatec et DDM Systems. Tethon 3D et Cerhum sont des fournisseurs de matériaux céramiques, spécifiquement pour les processus SLA.