Cobot of robot: waar moet je op letten?
Keuzemenu voor automatisering wordt steeds uitgebreider
Metaalbedrijven kunnen vandaag de dag kiezen uit legio automatiseringsoplossingen. Van geavanceerde cellen met industrierobots voor product- en pallethandling tot CNC-draaimachines met stafaanvoer én geïntegreerde grijpers. Voor bedrijven die voor het eerst instappen in automatisering of die capaciteitsuitbreiding zoeken, zijn er cobots en plug-and-play-systemen op basis van een industrierobot. En de mobiele robots zijn aan een opmars begonnen.
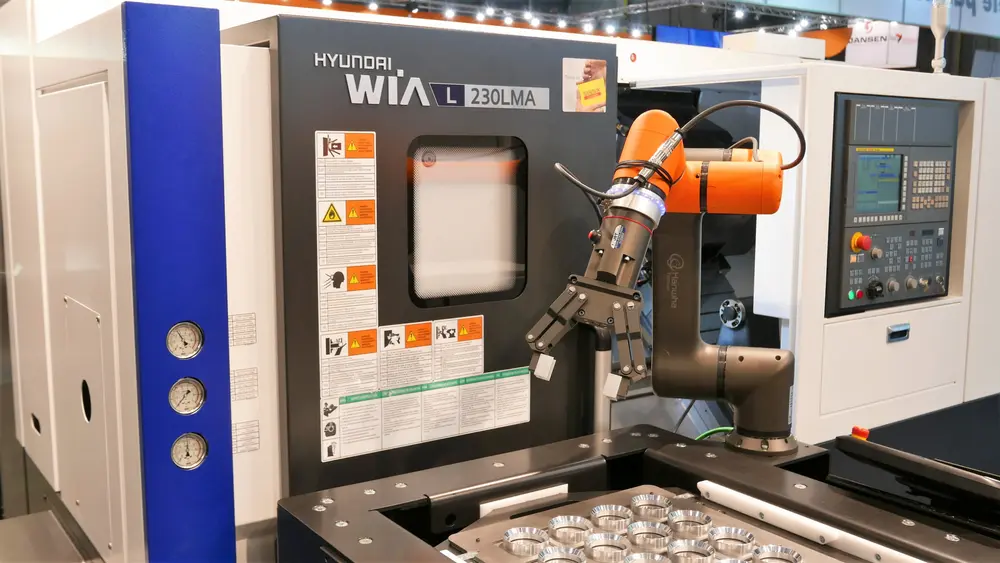
Obstakels
De cobot wint snel aan populariteit, zeker in logistieke omgevingen waarin doorgaans minder zware producten verplaatst moeten worden. Dit geeft eigenlijk al direct de beperking van de cobot in de metaalindustrie aan: het hefgewicht is beperkt. De grens ligt momenteel bij 25 kg (inclusief grijper). In de praktijk zal dit doorgaans lager liggen - denk eerder aan ongeveer 12 kg, met een maximale reikwijdte van zo’n 1.300 mm.
De cobot wint snel aan populariteit, maar heeft ook beperkingen zoals het hefgewicht en de geringe nauwkeurigheid in vergelijking met een industrierobot
Een andere beperking is de geringere nauwkeurigheid dan die van een industrierobot, alhoewel de fabrikanten met de nieuwe generatie cobots de nauwkeurigheid naar een hoger niveau tillen. Positioneernauwkeurigheden van 30 micron zijn bij de kleinste systemen al haalbaar. Dat bereiken de cobotfabrikanten met camera’s waarmee de positie van de grijper ten opzichte van een referentiepunt wordt bepaald, waarna voor de eventuele afwijking wordt gecorrigeerd. Voor assemblagetoepassingen is dit handig, voor het beladen van een CNC-machine is die nauwkeurigheid vaak niet eens nodig.
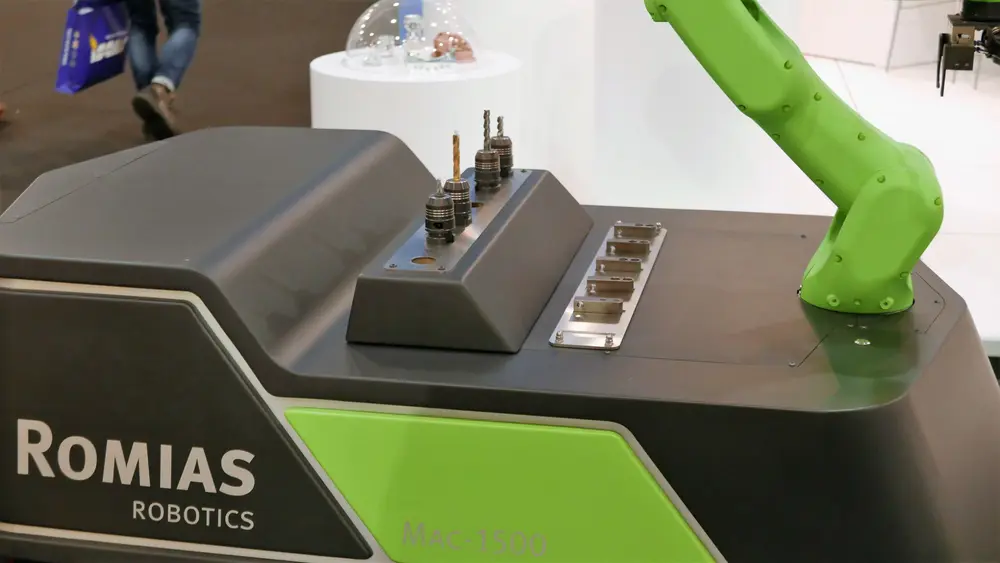
Toch zijn er zeker zinvolle toepassingen te bedenken
Hoeveel flexibiliteit is nodig?
De belangrijkste vraag die men zich in de metaalindustrie rond de cobot moet stellen, is: hoe flexibel moet de automatisering zijn en zal er geen behoefte komen om zwaardere stukken te handlen of over een grotere afstand te verplaatsen? Is dat laatste het geval, dan is een 6-assige industrierobot in combinatie met een gestandaardiseerd laadsysteem een slimmere oplossing.
Waar men zich ook bewust van moet zijn, is dat het niet bij de aanschafprijs van de cobot blijft. Die vergt eigenlijk altijd nog een extra investering in een tafel waarop de producten worden weggelegd of een andere oplossing.
De kracht van dit ‘maatje’ van de operator zit in diens flexibiliteit. Voor veel gangbare cobots zijn er extensies beschikbaar zodat de cobot naast de producthandling-taken bij een machine bijvoorbeeld een werkstuk automatisch kan ontbramen of schuren. Dit zijn zaken die ook een industriële robot kan uitvoeren, zij het dan dit extra programmeerkennis vereist, waardoor de plug-and-play-oplossing een deel van z’n kracht, namelijk snel en heel eenvoudig programmeren, verliest. De cobot kan dikwijls via teach-in geprogrammeerd worden.
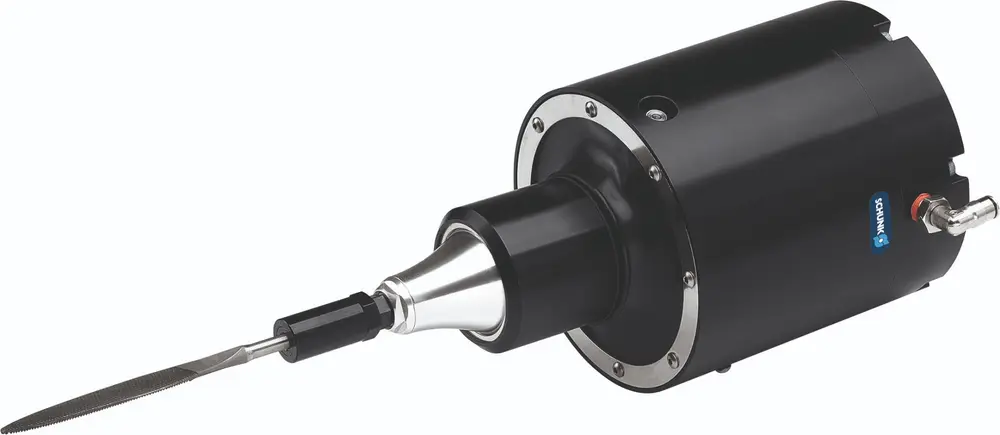
De moraal van het verhaal: besteed bij het investeren in automatisering de nodige aandacht aan het programmeren van het systeem. Snel en eenvoudig programmeren is een belangrijk voordeel van de plug-and-play-systemen; dit is een fundamenteel verschil tussen de robot en cobot. Iedere CNC-operator leert binnen een dag hiermee omgaan.
Daar staat tegenover dat de taakuitbreiding van een cobot een aantrekkelijke optie kan zijn. Maar is de besturing zo gebruiksvriendelijk dat een operator zo’n extra taak zelf kan programmeren? En hoe eenvoudig is het om plug ins, al dan niet aangeleverd door de system integrator, in te lezen?
Overigens is de algemene trend dat het programmeren van een robot steeds gemakkelijker zal worden. Ook voor de industrierobot zijn er nieuwe besturingsplatformen in ontwikkeling om met eenvoudige programmering de inzet van een robot laagdrempeliger te maken.
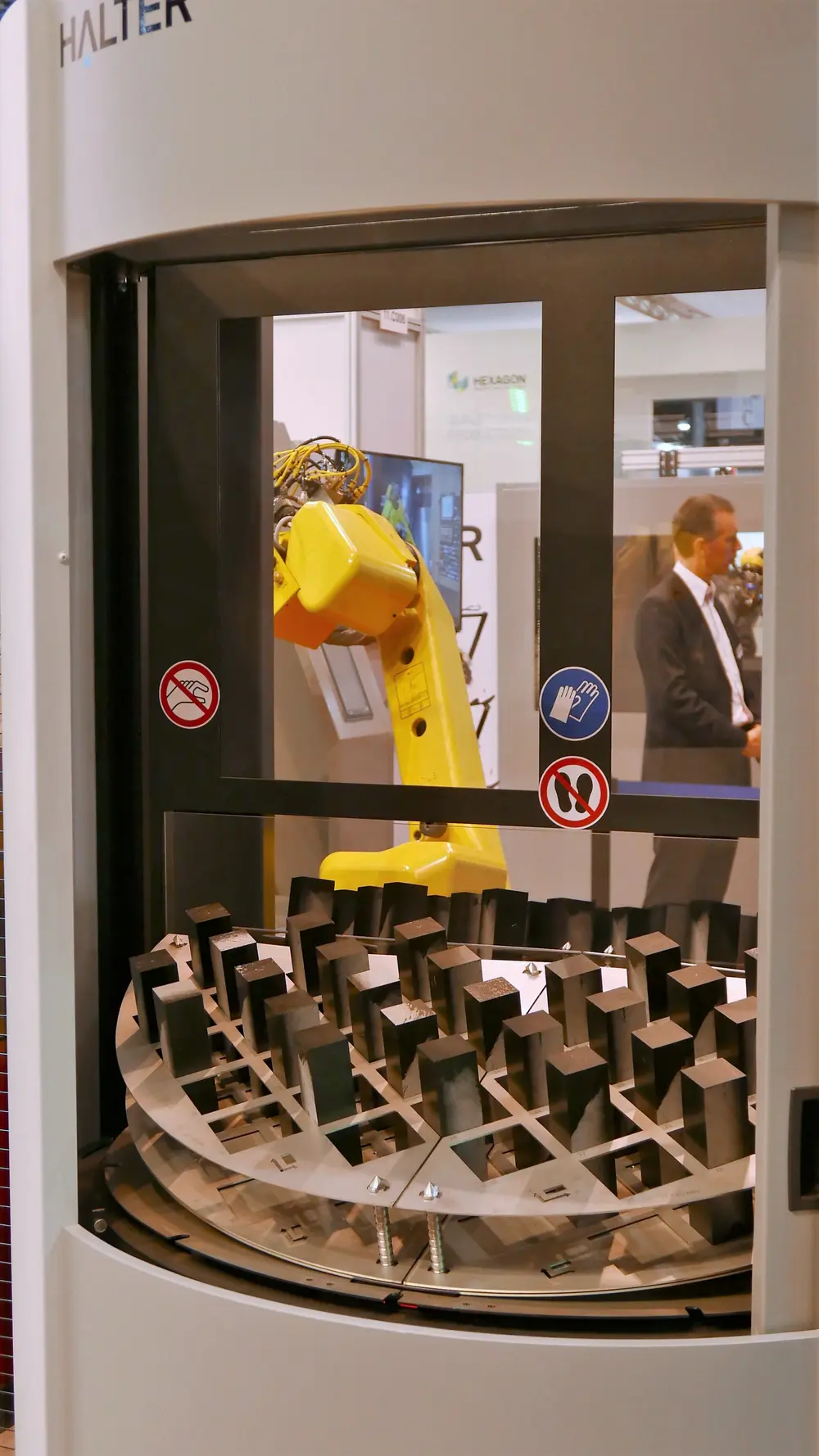
Veiligheid
Veiligheid is een punt waar soms wel eens te gemakkelijk overheen wordt gestapt bij automatisering. Bij plug-and-play-cellen, die door de leverancier aan de CNC-machine worden gekoppeld, hoeft de gebruiker zich hier niet druk over te maken. De leverancier neemt dit mee in zijn aanbieding. Dat is zo geregeld in Europese Machinerichtlijn, die de verantwoordelijkheid voor de veiligheid neerlegt bij de partij die de systemen aan elkaar koppelt.
Hierbij zijn er drie veiligheidsniveaus die niet direct zichtbaar zijn (bijvoorbeeld de elektrische componenten) en één die in het oog springt: de integratie van de veiligheid van de cel in die van de CNC-machine.
Bij zwaardere industrierobots is een lichtscherm of zelfs een hekwerk verplicht. Bij kleinere robots en bij cobots zijn andere veiligheidssystemen toegestaan, zoals een vloerscanner die de omgeving aftast.
Het thema safety krijgt een andere dimensie zodra een bedrijf een eigen automatiseringsoplossing gaat samenstellen of flexibel wil inzetten en een cobot afwisselend aan verschillende machines plaatst. Dan ligt juridisch de verantwoordelijkheid voor de veiligheid van het totale systeem bij het bedrijf zelf. Hoewel een cobot strikt volgens de betekenis van het woord (collaborative robot) ontwikkeld is om samen te werken met de mens en via druk- en krachtsensoren voelt als er een aanraking is met de mens, mag het aspect veiligheid niet onderschat worden. Hoe traag een cobot ook beweegt, een werkstuk met een scherpe kant in een grijper kan bij een onbedoelde botsing voor letsel zorgen. Een relatief laag gewicht van 10 kg kan bij een snelle beweging toch een behoorlijke impact hebben.
Dat realiseren verschillende fabrikanten van cobots zich terdege en daarom integreren ze geavanceerde safety-oplossingen in de cobot. Denk maar aan 3D-camerasystemen die de omgeving scannen. Zodra die een voorwerp te dichtbij zien komen, vertragen ze automatisch de beweging of laten ze de cobot zelfs helemaal stoppen.
Die technologie is qua effectiviteit vergelijkbaar met de scanners in de voet van veel compacte plug-and-play-oplossingen. Die oplossing om de cobot veilig in te zetten, houdt het systeem flexibel, zonder dat operators iedere keer geconfronteerd worden met een veiligheidshekwerk of een lichtscherm dat de robot of cobot direct volledig stopt.
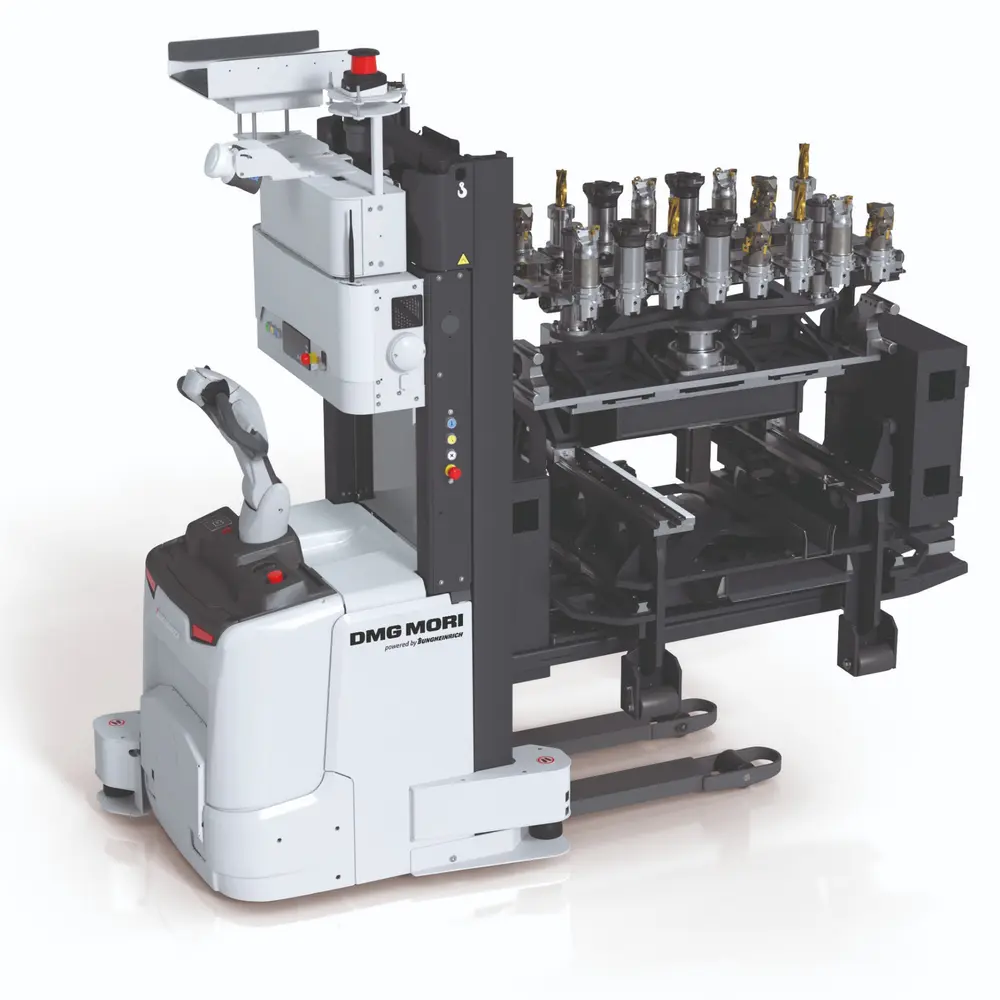
Autonome logistiek
Een vorm van automatisering in die productie, die qua toepassing nog in de kinderschoenen staat in de metaalindustrie, is de mobiele robot, ook wel AGV genoemd (Automated Guided Vehicle) of AMR (Automated Mobile Robot). Deze termen worden nogal eens door elkaar gebruikt, hoewel ze strikt genomen voor verschillende systemen staan.
AGV’s zijn ontworpen om een vooraf gedefinieerde route af te leggen, langs vaste herkenbare punten. Mobiele robots zijn intelligenter. Ze maken gebruik van LIDAR radars (dezelfde als in auto’s) of 3D-camera’s waarmee ze hun omgeving in kaart brengen. Omdat er ook vaste makeringen zijn, weet de mobiele robot elk moment exact de positie en kan veel vrijer de route bepalen door de fabriek.
Het verschil komt het beste tot uiting als er een obstakel op het pad zit: de AGV zal stoppen en wachten, de mobiele robot zoekt een omweg. Hiermee kan men dus het interne transport automatiseren. Omdat die mobiele robots gebruik maken van markeringspunten in de fabriek én uitgerust zijn met sensoren, kunnen ze vrij door de hele fabriek bewegen. De mobiele robots kunnen zo een deel van het interne transport overnemen.
Dit klinkt alsof het iets is dat enkel en alleen voor grote bedrijven een interessante optie is, maar dit is niet correct. In elk metaalverwerkend bedrijf verliezen medewerkers dagelijks tijd met het ophalen van bijvoorbeeld gereedschappen in een centraal magazijn om ze naar de machine te brengen. Of materialen op te halen die ze moeten bewerken. Of halffabricaten. Voor een deel zijn dit taken die een mobiele robot al kan uitvoeren, zonder dat men meteen diep in de technologie duikt en bijvoorbeeld systemen installeert die producten uit magazijnstellingen kunnen halen.
Naarmate maakbedrijven hun productie verder automatiseren en technische medewerkers schaars blijven, zal de vraag naar cobots en robots toenemen
Zodra men in de verspaning gereedschappen centraal voorinstelt, kan een mobiele robot de correcte gereedschapset naar de machine transporteren. Met een zwaarder uitgevoerd systeem kan men eventueel een pallet met producten die bewerkt zijn autonoom naar een magazijn afvoeren. Hiervoor kan men een autonome heftruck inzetten, waarmee men voorkomt dat de ochtendploeg elke dag eerst een tijd bezig is om de bewerkte producten bij de machine weg te halen.
Technisch kan het allemaal, de vraag is of de investering op dit moment al loont en of de inrichting van de productieomgeving voldoende ruimte biedt voor een dergelijke vorm van automatisering. Zeker is wel dat naarmate maakbedrijven hun productie verder automatiseren en technische medewerkers schaars blijven, de vraag naar dergelijke oplossingen zal toenemen.