CNC-besturing wordt cybersafe
Data-encryptie, bescherming van datatoegang en gebruikersauthenticatie
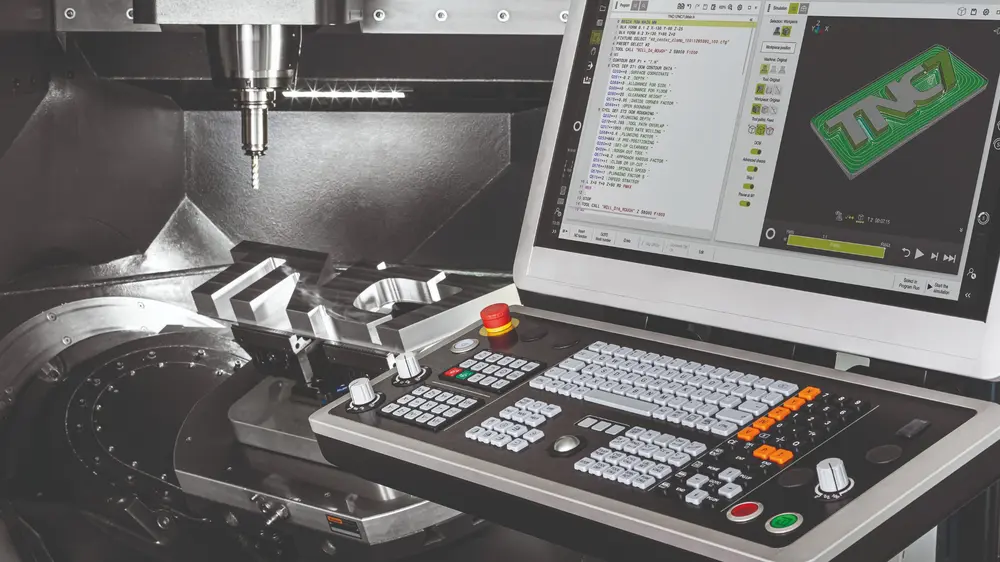
De data die de CNC-besturing genereert, spelen een alsmaar grotere rol. Tegenwoordig zijn CNC-machines vaak verbonden met het web; al dan niet continu. Dat biedt veel mogelijkheden, maar ook bedreigingen. Geen wonder dat de bouwers van de besturingen een belangrijke nieuwe functie toevoegen: cybersecurity. Maar dit is niet de enige evolutie.
Van NC naar CNC
Nadat eind jaren veertig aan universiteiten de eerste tests werden gedaan, kwam de doorbraak eind jaren vijftig in de Verenigde Staten met een Numerical Control die werd ontwikkeld aan het Massachusetts Institute of Technology (MIT). Het was de Amerikaanse machinebouwer Cincinnati Hydrotel die de eerste freesmachine uitrustte met deze NC-besturing.
De echte doorbraak kwam pas later, in de jaren tachtig, toen microprocessors beschikbaar kwamen en de integratie met CAD/CAM tot stand kwam. De eerste besturingen werkten nog met ponskaarten, maar dankzij de microchips kon men beginnen met de echte integratie van 3D-ontwerpen en frezen en draaien. Deze ontwikkeling blijft tot op de dag van vandaag doorgaan. Vanaf dat moment praten we over CNC: Computer Numerical Control.
Hoewel er achter de schermen nog steeds met G-codes wordt gewerkt, lijkt de HMI van tegenwoordig in de verste verte niet meer op die van weleer. Zeker sinds de digitalisering in een stroomversnelling raakt, ligt hier een van de speerpunten waar de ontwikkelaars zich op richten.
Het bedienersscherm wordt zo gebruikersvriendelijk gemaakt, zodat iedereen de informatie ziet die voor hem van belang is. Een van de trends is de mogelijkheid om je eigen schermindeling samen te stellen, bijvoorbeeld in functie van specifieke processen. Dit moet het gebruiksgemak verhogen.
Verbonden met het internet
Tegenwoordig zijn CNC-machines alsmaar vaker verbonden met het internet. Misschien niet permanent, maar er zijn digitale toegangen tot de besturing van de machines. Cybersecurity is daarom een actueel thema in de wereld van de CNC-besturingen. Alle fabrikanten zijn hiermee bezig. De eindgebruiker wil absoluut niet meemaken dat zijn CNC-machine op een ochtend gehackt is.
Veiligheidsrisico's
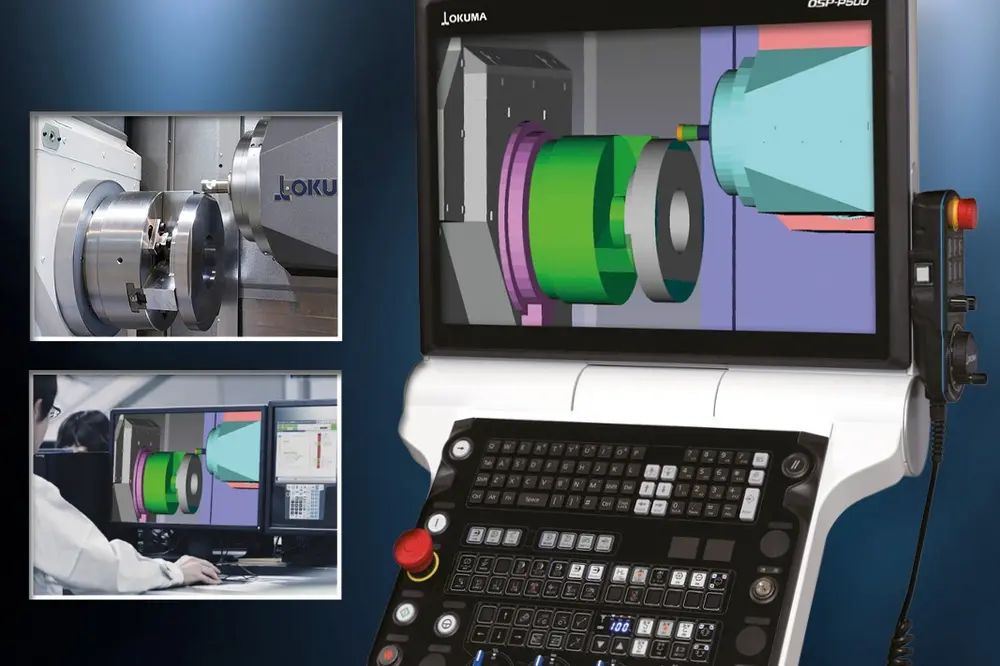
Deze aandacht komt niet te laat. Een Amerikaans onderzoek in 2022 ('The Security Risks Faced by CNC Machines in Industry 4.0') toonde aan dat de gangbare CNC-besturingen niet volledig immuun waren voor cyberaanvallen.
Ransomware is één voorbeeld van zo’n aanval, maar het kan erger. De onderzoekers – gespecialiseerd in cybersecurity – wisten in sommige besturingen de compensatietabellen voor gereedschapsslijtage te bereiken; of ze wisten een vals alarm uit te lokken, met alle ongeplande gevolgen van dien voor de productie. Zelfs het stelen van de programmacode was soms mogelijk.
In het minst erge geval wordt het werkstuk niet of verkeerd bewerkt. In ernstigere gevallen kan de CNC-machine crashen of op een andere manier ernstig beschadigd raken, ofwel gaan de aanvallers er dus met belangrijke informatie vandoor.
Niet alleen de industrie onderkent dit risico, ook de Europese beleidsmakers doen dit. In de nieuwe Machineverordening die in 2027 de huidige Machinerichtlijn zal vervangen, is er veel meer aandacht voor de software. De verordening sluit aan bij de Europese regelgeving omtrent data en cybersecurity.
Verantwoordelijkheden
In de Cyber Resilience Act en de NIS2-richtlijn verplicht de Europese Unie de leveranciers van technologie om software en apparatuur te leveren die veilig is voor cybersecurity. Een van de nieuwe eisen in de Machineverordening is dat wijzigingen traceerbaar moeten zijn. Software en machines moeten gecertificeerd zijn en als er naderhand toch nog kwetsbaarheden blijken te zijn, moet de leverancier deze met een patch dichten.
De verantwoordelijkheid voor cybersecurity ligt zeker ook bij de gebruiker
Gebruikers moeten deze volgens de richtlijnen installeren. Zij moeten ook technische en organisatorische maatregelen nemen om hun netwerk- en informatiesystemen te wapenen tegen cyberaanvallen. De verantwoordelijkheid ligt dus zeker ook bij de gebruiker.
Hoe maak je de besturing cybersafe?
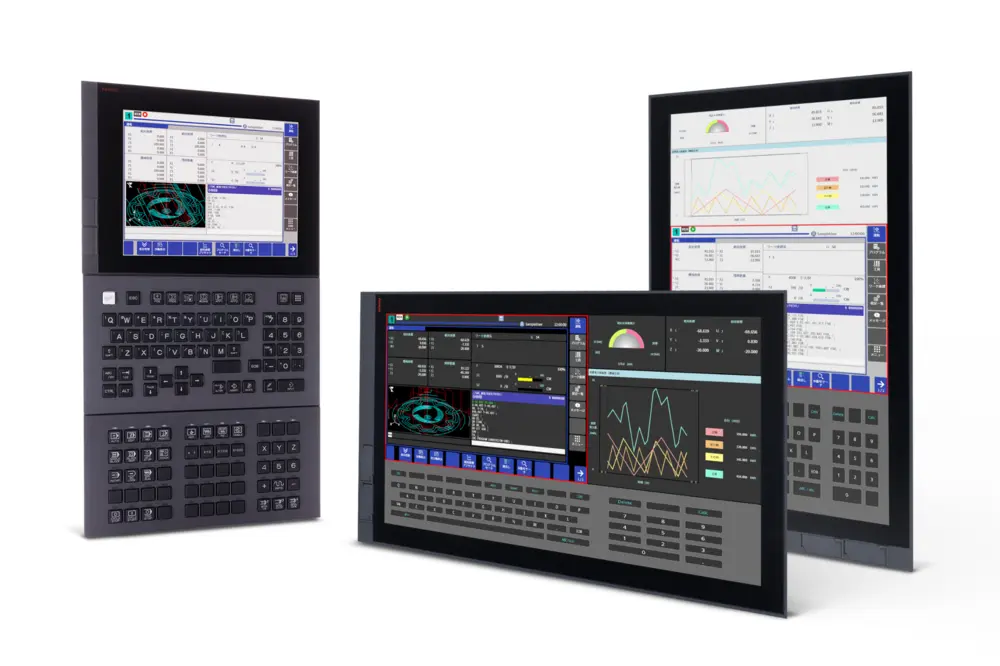
In het eerder genoemde onderzoek werd ook ingegaan op de maatregelen die besturingsfabrikanten kunnen nemen. Encryptie van data is één oplossing; bescherming van datatoegang een andere. De derde is authenticatie door de gebruiker. Denk daarbij aan wachtwoorden en biometrische gegevenscontrole, zoals op een smartphone met je vingerafdruk.
De onderzoekers concluderen in hun studie dat dit de meest afdoende oplossing is, die sommige besturingsontwikkelaars overigens al enkele jaren toepassen. Met zo’n toegangscode voor de besturing kan men brute aanvallen van buitenaf effectief weren.
Uiteindelijk zal het echter vooral gaan om het gedrag van de CNC-operator. Is die bereid om de strikte inlogprotocollen te volgen? Sommige machinebouwers testen al het gebruik van biometrische gegevens, zoals dus een vingerafdruk om toegang te krijgen tot de machine. Men beseft dat eenvoudige protocollen de acceptie ten goede komen.
Digitale tweelingen
Een andere trend wanneer het om besturingen van CNC-machines gaat, is het gebruik van digitale tweelingen. De meeste machinebouwers, zeker die van hoogwaardige machines, bieden een offline kopie van hun besturing aan waarin een digitale tweeling van de CNC-machine is geïntegreerd. Als men hier ook nog de opspanmiddelen en gereedschappen aan toevoegt, kan men voorafgaand aan de fysieke bewerking een betrouwbare simulatie uitvoeren. Ook robots kunnen meegenomen worden in de simulatie.
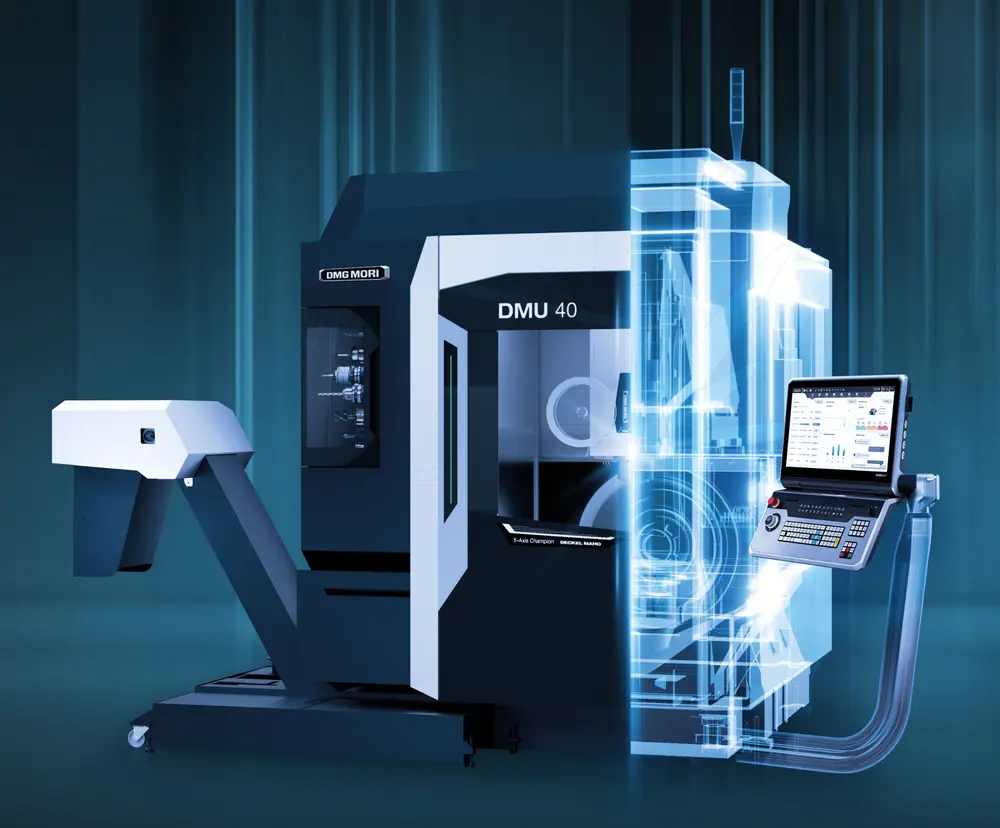
Met sommige besturingen kunnen deze simulaties direct aan de machine worden uitgevoerd, ongeacht de complexiteit van de opspanning. Het ligt evenwel voor de hand om dit extern te doen. Hierdoor neemt de betrouwbaarheid van het (onbemande) proces toe en verkort men de insteltijd, omdat men virtueel al kan testen.
Tijdsbesparing
Besturingsfabrikanten spreken over tijdsbesparingen van tientallen procenten bij het instellen van de machine, als men zowel een digitale tweeling heeft van de machine, de besturing, het werkstuk en de opspanning en gereedschappen. Het testen van programma’s verschuift immers van de machine naar de virtuele omgeving, waar niet alleen de risico’s kleiner zijn (een virtuele crash kost geen geld) maar de productie op de fysieke machine ondertussen doorloopt.
Digitale tweelingen kunnen leiden tot aanzienlijke tijdsbesparingen bij het instellen van de machine
Het gevolg is wel dat de besturingen complexer worden. Door kunstmatige intelligentie in te zetten, proberen de ontwikkelaars de bediening te vereenvoudigen of repeterende taken te automatiseren.
Eigenlijk kun je deze stap samenvatten onder het kopje digitalisering. Sommige besturingsfabrikanten zetten de ontwikkeling van hun huidige besturingen stop en gaan alleen nog verder met de nieuwste, vaak op digitale fundamenten gebouwde versies. De dwang van de Europese Unie om datasecurity onderdeel te maken van de CE-markering zal deze ontwikkeling waarschijnlijk nog versnellen.
Betere hardware
Een ander gevolg van de digitalisering en de grotere hoeveelheid informatie die een besturing moet verwerken, is dat de eisen aan de hardware toenemen.
Rekenkracht en snelheid
Onder de motorkap komt men daarom steeds krachtigere CPU’s tegen, die voldoende rekenkracht moeten bieden. Een belangrijke KPI is op dit vlak het aantal blokken dat de besturing vooruit kan kijken. Immers, hoe meer blokken de besturing vooruit kijkt, hoe meer rekening kan worden gehouden met de volgende bewerkingstappen.
De bedieningsschermen worden groter, omdat men hierop veel meer gegevens wil kunnen zien
Rekensnelheid speelt eveneens een rol bij de manier waarop het programma de geprogrammeerde freesbanen interpreteert. In het CAD-model ziet de lijn er altijd vloeiend uit. Voor de besturing worden echter een aantal punten geprogrammeerd waarlangs de frees zal bewegen. Hoe dichter deze punten bij elkaar liggen, des te nauwkeuriger de beweging de getekende lijn volgt. Dit is met name bij 5-assig simultaan frezen van belang, om hoge (oppervlakte)nauwkeurigheid te behalen.
Grotere schermen
Daarnaast groeien de bedieningsschermen sterk. Waar een jaar of tien geleden 15 inch al een royaal formaat was, zijn beeldschermformaten van 23 en zelfs 27 inch tegenwoordig geen unicum meer. Dit heeft te maken met het bedieningsgemak en het feit dat men veel meer gegevens op het scherm wil zien.
Ook het gebruik van twee schermen ziet men daarom bij sommige machinebouwers. Zij leggen vaak hun eigen schil over de HMI van de besturingsfabrikant heen, waarin ze nieuwe functies makkelijk toegankelijk maken met apps. Zo’n app kan een specifieke frees- of testcyclus zijn die daarmee makkelijk bruikbaar wordt, maar kan ook te maken hebben met data over bijvoorbeeld het energieverbruik van de machine.
Android voor CNC-machines
De markt voor CNC-besturingen wordt al jarenlang gedomineerd door enkele grote partijen, waarbij de verschillende regio’s in de wereld hun duidelijke voorkeur hebben. Sommige machinefabrikanten kiezen er echter voor om hun eigen besturing te ontwikkelen. Met de opmars van Industrie 4.0 komt er misschien meer beweging in deze markt.
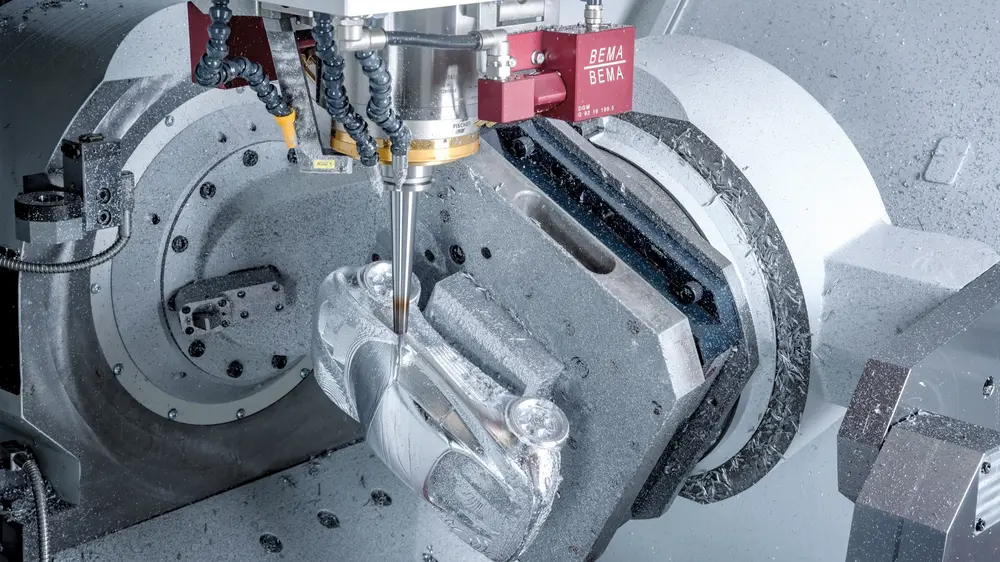
Open-source software
Zo werkt Autodesk al enkele jaren samen met andere partijen aan de Autodesk Machine Control (AMC). Het softwarebedrijf omschrijft deze software zelf als een soort 'Android voor de CNC-industrie'. Het is namelijk open software, waarmee ontwikkelaars en machinebouwers hun eigen CAD/CAM-software kunnen integreren met de besturing van de machine.
AMC overbrugt de kloof tussen CAD/CAM-software en machinehardware met een moderne, browsergebaseerde Human Machine Interface, configureerbare Open API's en functies zoals over-the-airupdates en het loggen van zaken die gedaan worden. Het besturen van de machine gebeurt vanuit de basis van het AMC-framework. Ontwikkelaars en machinebouwers kunnen zich dus volledig focussen op de toepassingen.
Doordat AMC niet alleen signalen naar de aandrijvingen in de machine kan sturen, maar eveneens data kan terugontvangen, kan men tijdens een bewerking een digitale tweeling van het feitelijke proces opbouwen. Dit kan men weer gebruiken om met behulp van CAD/CAM-inspecties virtueel uit te voeren en eventueel closed loop-processen te bouwen.
Met medewerking van Fanuc