Big data en micro spanen bij het slijpen
Procesbeheersing en digitalisering: dat zijn de twee sleutelwoorden in de verdere ontwikkeling van slijptechnologie. Big data krijgen dus vat op de slijpmachines om verder te komen dan de laatste micrometers. Of gaat de laser nog een rol spelen?
Digitalisering in het slijpproces
Aan de Duitse technische universiteiten is er het jongste decennium veel onderzoek verricht onder de noemer van 'Industrie 4.0'. Ook als het om slijpen gaat. De digitalisering heeft al greep op deze precisietechnologie gekregen, doordat het programmeren eenvoudiger wordt. De komende jaren zal dit ook een steeds grotere rol krijgen waar het gaat over het slijpproces zelf.
Modelgebaseerde regelkringen
Door extra sensoren in de machines te bouwen, kunnen meer data van het slijpproces gegenereerd worden. Denk bijvoorbeeld aan de temperatuur aan het werkstuk of de slijpkrachten hierop, of de temperatuur van het koelsmeermiddel.
Extra sensoren leveren meer data van het slijpproces op
Bij het 'Werkzeugmaschinenlabor' van de RWTH Aachen voorziet men een verschuiving van het gebruik van modellen. Dankzij de nieuwe meetdata kan men de slijpbewerking namelijk veel nauwkeuriger plannen en krijgt men data om modelgebaseerde regelkringen te bouwen. Een factor die zich moeilijk laat bepalen in een slijpmachine, is de oppervlaktekwaliteit. Met virtuele sensoren - of opnieuw modellen - zou dit in de toekomst wel mogelijk moeten zijn. Door data tijdens het proces te verzamelen en te analyseren, zal het in de toekomst steeds beter mogelijk zijn om al na afloop van het proces een goed beeld te hebben van de kwaliteit. Hiermee wil men de noodzaak verkleinen voor metingen, die vaak meer tijd kosten dan de slijpbewerking zelf. Een voorwaarde hiervoor is wel een realtime verwerking van data. Het is niet voor niets dat men in Aken volop inzet op de toepassing van 5G in de industrie.
Toestand slijpschijf analyseren
Een ander voorbeeld hoe data het slijpen verandert, toont onderzoeksinstituut IFW in Hannover. Een lasermeetsysteem, opgeslagen in het gereedschapsmagazijn van de machine, meet in luttele seconden de topografie van het oppervlak van de slijpschijf. Vervolgens zetten de onderzoekers Artificiële Intelligentie in om het resultaat te analyseren.
Hiertoe wordt het meetresultaat vergeleken met het oppervlak van een niet-gebruikte slijpschijf. Algoritmen bepalen vervolgens volstrekt autonoom wanneer het tijd is om de schijf te dressen. In het model wordt exact bepaald hoeveel materiaal daarbij moet worden afgenomen. Op termijn levert deze aanpak dus, naast een onbemand slijpproces, een langere levensduur op.
Beeldverwerkingstechnologie
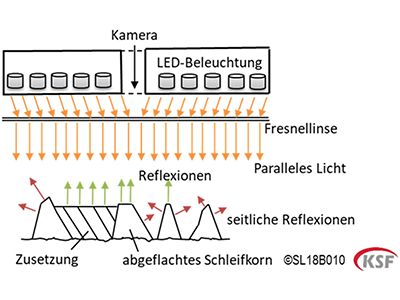
Aan meerdere Duitse onderzoeksinstituten doet men onderzoek in deze richting. Het Kompetenzzentrum für Spanende Fertigung (KFS) bij de hogeschool in Tuttlingen gebruikt beeldverwerkingstechnologie voor het in ontwikkeling zijnde Grainvision-meetsysteem voor de controle van een slijpschijf. Met de combinatie van hoge resolutie beeldopnamen van het oppervlak én algoritmen, lukt het om uitspraken te doen over de toestand van de slijpkorrels aan het oppervlak van het gereedschap.
Het principe van deze oplossing is dat je met de juiste belichting en camera’s de slijtage aan de slijpkorrels herkent, doordat deze licht reflecteren. Naarmate de snijvolumes toenemen, treedt slijtage op van het gebruikte slijpgereedschap. Het KSF-analysesysteem extraheert dan de door slijtage veroorzaakte reflecties uit de hogeresolutiebeelden van het oppervlak.
De eerste testen tonen aan dat het meetsysteem reproduceerbare resultaten oplevert. De conclusie is dan ook dat dergelijke meetsystemen bijdragen aan een efficiënter slijpproces, dat met meer zekerheid een bepaalde kwaliteit oplevert. De Duitse onderzoekers denken dat deze aanpak een robuuster systeem oplevert dan gebruik te maken van bijvoorbeeld akoestische signalen of het meten van krachten op het slijpwerkstuk, omdat die resultaten afhankelijk zijn van externe factoren. In Aken denken de wetenschappers zelfs dat het straks nog allemaal veel verder gaat. In het onderzoeksproject GrainVision heeft het KSF in Tuttlingen hogeresolutiecamera’s ingezet om de slijtage aan een slijpschijf automatisch te detecteren.
Operator ondersteunen
Al deze datasystemen zullen ook de slijper zelf gaan ondersteunen. Deels zullen er volledig autonome processen komen, voor een ander deel gaan de data en de daarop gebaseerde informatie de slijper helpen om het proces te optimaliseren.
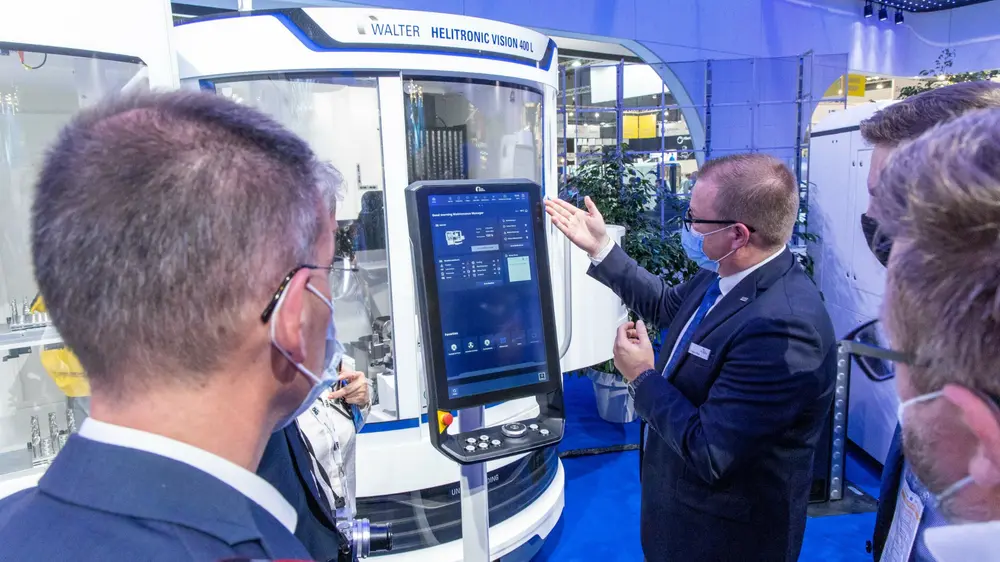
Vroeger was de basis van een goede slijper vooral specifieke kennis, aangevuld met ervaring. Tegenwoordig spelen de assistentiesystemen in toenemende mate een rol, met name bij het verbeteren van processen. Fabrikanten van slijpmachines passen daarom hun besturingen aan. Enerzijds worden operators intuïtiever door de programmeerstappen geleid en zien zij alleen de voor hen relevante informatie. Anderzijds wordt de verbinding met de buitenwereld - lees: de databanken - verbeterd.
Bedreigt de laser het slijpen?
De jongste jaren komt laserpolijsten regelmatig aan de orde. Met de ultrakorte pulslasers kunnen oppervlakken in zeer korte tijd nauwkeurig worden nabewerkt. Toch ziet de Duitse hoogleraar professor Dirk Biermann van de TU Dortmund dit eerder als een aanvullende technologie dan als een concurrerende voor het slijpen. Volgens hem zijn er wel enkele interessante nichetoepassingen, onder andere in de medische industrie, maar is de technologie niet geschikt voor alle applicaties en ligt de investeringsdrempel hoog.
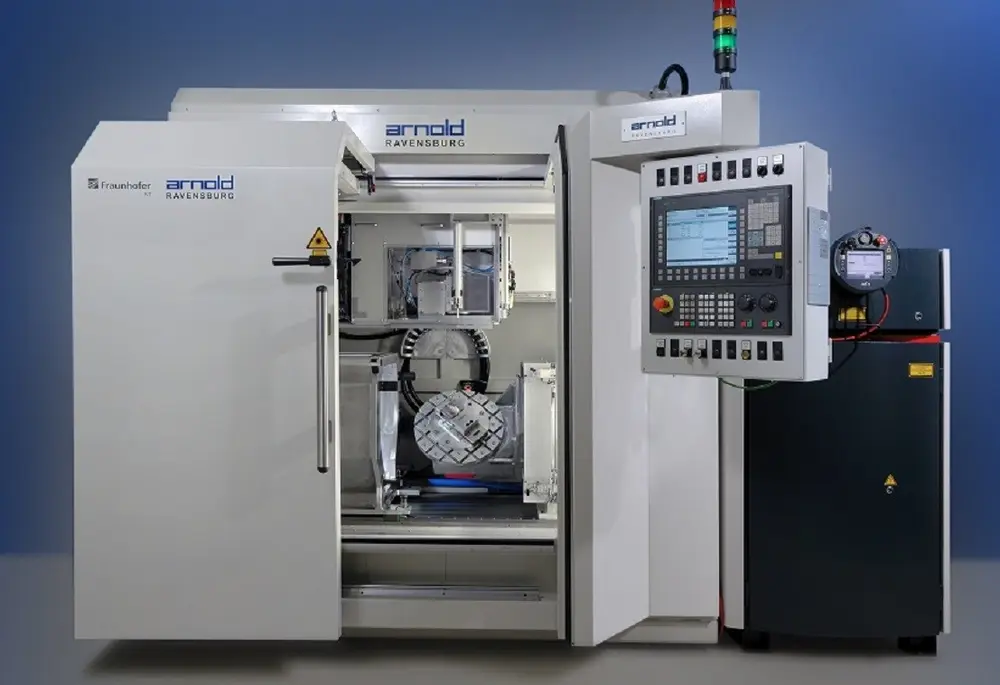
Bij het gereedschapslijpen komt de laser wel vaker in beeld, met name als het gaat om het aanbrengen van spaanbrekers. Bij bepaalde gereedschappen is dat met de laser sneller en eenvoudiger te doen dan bij traditioneel gereedschapslijpen. Tijdens de Laser Polishing-conferentie bij het Fraunhofer ILT in Aken werden vorig jaar resultaten gepresenteerd van het bewerken van matrijzen voor het spuitgieten van een kunststof koplamp. Door het oppervlak met een 100W Nd:YAG laser (1064 nm, pulsduur 7 nanoseconde) te bewerken, realiseerden de onderzoekers een oppervlakteruwheid van 40 nm.
Procesintegratie
De slijpbewerking wordt soms geïntegreerd in een CNC-bewerkingscentrum, omdat doorlooptijden korter moeten en maakbedrijven een all-in-one oplossing zoeken. Omgekeerd zijn er ook fabrikanten die andere verspanende technologieën integreren in een slijpmachine. Voor specifieke toepassingen is dit een zinvolle toepassing, maar uiteindelijk gaat het er wel om hoeveel van de beschikbare productie-uren de andere technologie niet gebruikt wordt. Bepalend is dus of er slechts een beperkte slijpbewerking plaatsvindt (als men deze technologie integreert in een bewerkingscentrum) of slechts een beperkte freesbewerking (als men frezen integreert in een slijpmachine). Sommige machinebouwers hanteren hiervoor als vuistregel 20% van de totale bewerkingstijd.
Recente innovaties hebben de efficiency van kruipslijpen naar een hoger niveau getild
Een recente ontwikkeling is nog de opmars van het zogenaamde creep feed grinding proces, oftewel kruipgangslijpen. Het concept bestaat al langer: door met een zeer langzame voeding te slijpen, kan men méér materiaal in korte tijd weghalen. Vooral bij materialen zoals Inconel en titanium heeft het als voordeel dat een deel van de warmte geabsorbeerd wordt door de bewerking. Door de slijpschijf continu te dressen, blijft deze tijdens de hele cyclus scherp. De voeding ligt bij dit proces een factor 10 tot 100 lager dan bij gewoon slijpen, maar wel met een hoge snedediepte. Daar komt de productiviteit vandaan, die bij sommige toepassingen aanzienlijk hoger ligt dan bij het frezen van complexe vormen.
Innovaties op het vlak van slijpkorrels en het bindmiddel voor de slijpschijven hebben recent de efficiency van kruipslijpen naar een hoger niveau getild. Keramische slijpkorrels hebben een langere standtijd en de nieuwe generatie bindmiddelen gecombineerd met een hogere porositeit verlengen de standtijd van de schijf. De vorm bepaalt mee de capaciteiten van de schijf om de spanen af te voeren, wat zowel op de standtijd als de warmte-opbouw een positief effect heeft. Bij het bewerken van turbineschoepen kan men met deze technologie de bewerking in één opspanning doen.