Precisiebewerken: meerdere wegen leiden naar Rome
Precisiebewerken is niet langer het exclusieve domein van de halfgeleiderindustrie. Ook in de medische sector en de lucht- en ruimtevaartindustrie worden er tegenwoordig nauwkeurigheden gevraagd die enkele decennia geleden het werk waren voor specialisten. Het grote verschil tussen toen en nu is wel dat er vandaag meer technieken beschikbaar zijn.

Veel meer mogelijk met frezen en draaien
Als het om precisie gaat, wordt in de metaalbewerking al snel gedacht aan slijpen of EDM (draad- en zinkvonken). Dat zijn van oudsher de technieken waar men op teruggreep als het echt om de micrometers maatnauwkeurigheid ging.
De nieuwe generatie CNC-machines en gereedschappen halen echter dergelijke nauwkeurigheden zonder dat men meteen naar deze gespecialiseerde bewerkingstechnieken moet grijpen. De fabrikanten van CNC- machines zijn erin geslaagd om hun precisiemachines zowel in alle opzichten stabieler te maken, alsook om met de nieuwste besturingssystemen en sensortechnologie de nauwkeurigheidsgrenzen te verschuiven.
Minder onvolkomenheden in constructiefase machine
In de constructiefase van een CNC-machine speelt de opmars van simulatietechnieken (zoals FEM, de eindige-elementenmethode) een rol. Hiermee kunnen de machinebouwers hun machines virtueel onder belasting testen om onvolkomenheden in het ontwerp op te lossen en het thermodynamisch gedrag te optimaliseren.
Meer compensatiemogelijkheden in de praktijk
In de praktijk is het met name de verbeterde sensortechnologie (bv. temperatuurmetingen) in combinatie met compensatiemogelijkheden via de besturing die de nauwkeurigheid verhoogt. De machine compenseert nu zelfs voor een eventuele temperatuurstijging in de fabriekshal. Dat gebeurt met een optimaal machinemanagement koelsysteem en rekenkundige modellen om de CNC-machine binnen een positioneernauwkeurigheid van 1 µm in elke as te laten bewegen.
Snellere besturingen
De derde factor die bijdraagt aan de hogere nauwkeurigheid van CNC-bewerkingscentra is de veel snellere besturingen. Hierdoor kan men veel eerder ingrijpen als de gemeten positie afwijkt van de geprogrammeerde positie. Hoe sneller de besturing en hoe vaker de feitelijke freesbaan wordt bijgestuurd, des te vloeiender is de beweging en des te hoger de nauwkeurigheid waarmee er gefreesd wordt. Sommige besturingen meten elke 0,03 ms de positie van de punt van het gereedschap en sturen hierop bij, wat uiteraard lineaire aandrijvingen vereist.
Het voordeel van deze ultranauwkeurige CNC-machines is dat ze speciale bewerkingen soms kunnen vervangen. Om oppervlakteruwheden van 8 nm te halen, waren er vroeger bewerkingen zoals leppen of slijpen nodig. Ook rondheidsnauwkeurigheden van 2 µm in glas of keramiek waren vroeger het domein van de speciale verspanende technieken; tegenwoordig zijn er CNC-freesmachines die met deze precisie bewerken.
De nieuwe generatie CNC-machines en gereedschappen halen strenge nauwkeurigheden zonder dat men meteen naar gespecialiseerde bewerkingstechnieken zoals slijpen of EDM moet grijpen.
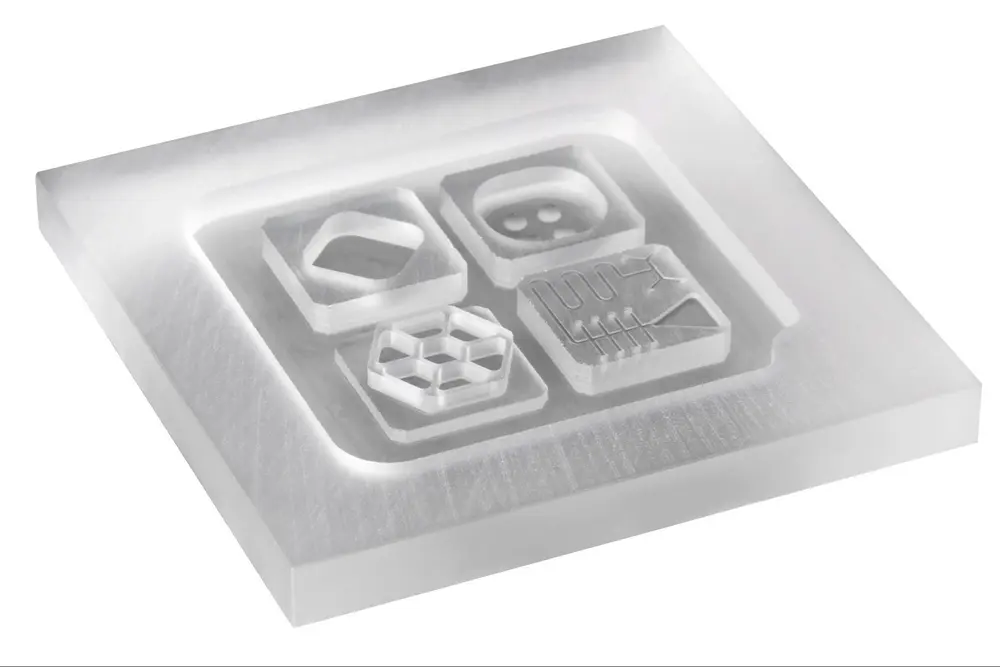
GEREEDSCHAPSBANEN HERBEREKENEN
Software speelt een beslissende rol in het zeer precies verspanen. Eén van de opties is om op de machine na het voorfrezen het werkstuk te meten en het programma aan te passen voor de overmaat die men meet. Tot nog toe gebeurt dit door de offset van het gereedschap aan te passen, ofwel in de lengte of in de diameter. Een nog vrij zelden gebruikte optie is om daadwerkelijk de bewegingen aan te passen.
Bijzonder bij één van de machinebouwers die dit doen, is dat het gereedschap in de machine gemeten wordt, terwijl de spindel het toerental draait dat geprogrammeerd is. Hiermee meet men ook het effect van de centrifugaalkrachten op het gereedschap. Dit vervangt het compenseren aan de hand van tabellen, wat in feite een aanname is tegenover de feitelijke meting van het gereedschap.
Harddraaien...
Een voorbeeld van een nieuwe precisietechnologie is het harddraaien. Staal met een hardheid van 55-65 HRC werd voor precisie-onderdelen vroeger altijd bewerkt op een slijpbank. Tegenwoordig gebeurt dat steeds vaker op een CNC-draaimachine die gebouwd is voor harddraaien, eventueel met hydrostatische lagers voor een nog hogere nauwkeurigheid.
De geoptimaliseerde CBN-gereedschappen (Cubic Boron Nitride) spelen bij harddraaien een grote rol. CBN-gereedschappen met een wiper verhogen de productiviteit van harddraaien sterk, vergeleken met een standaard wissenplaat. Harddraaien is daardoor een echte productietechniek: de productiviteit ligt hoger dan bij het slijpen.
De jongste jaren gaat in veel bedrijven het precisiewerk met toleranties van 3 µm en die in batches worden geproduceerd, richting het harddraaien. Maatnauwkeurigheden onder de 2 µm worden op de slijpmachines gerealiseerd.
... en slijpen
Bij die slijpmachines zien we de trend dat de machines veelzijdiger worden. Men kan ze sneller ombouwen naar een ander type product of een andere slijptechnologie. Meerdere slijpspindels die automatisch wisselen alsook het meten in de machine zelf, maken het slijpproces robuust en onbemand.
De belangrijkste vernieuwing in de slijptechnologie zit in de software van de machines. De fabrikanten doen er alles aan om zoveel mogelijk technologiekennis in de software onder te brengen, zodat er minder specifieke expertise van de operator nodig is. Dit kan een intuïtieve bediening zijn, maar net zo goed speciale technologiecycli, zoals het slijpen van vertandingen. Door enkele maten in te geven, kan de besturing al een geavanceerd slijpprogramma voor vertandingen genereren.
Nog een heel nieuwe (hardware) ontwikkeling die eerder op de slijpbeurs GrindingHub in Stuttgart gedemonstreerd werd, is het gebruik van synchroonmotoren in de slijpspindels. Hiermee haalt men 120.000 toeren per minuut en 32 kW vermogen. Omdat het koppel van zo’n synchroonmotor hoger ligt dan dat van een asynchroon motor, kan men volstaan met een derde minder geïnstalleerd vermogen om toch dezelfde productiviteit te halen.
Laser

De traditionele precisiebewerkingstechnieken zoals CNC-slijpen zijn opgeschoven in de richting van nog hogere nauwkeurigheden. Ze concurreren daar echter ook met nieuwere technieken, zoals laserbewerken. Dankzij de komst van femto- en picoseconden lasers, die een extreem korte pulsduur kennen (10 à 15 bij een femtoseconde laser), kan men niet alleen oppervlaktestructuren aanbrengen, maar ook daadwerkelijk materiaal afnemen van een werkstuk.
Het grote voordeel is dat het hier om een contactloze bewerking gaat, die vermijdt dat er spanningen in het materiaal ontstaan. Daarvoor is de pulsduur – de tijd dat extreem veel energie wordt ingebracht – immers te kort. Hoewel het om zeer nauwkeurige bewerkingen gaat, betekent dit niet dat laserbewerken zich beperkt tot microcomponenten. Ook grotere werkstukken kunnen met de energie van een laser bewerkt worden. Deze toepassing ziet men steeds vaker in de productie van matrijzen.
De verwachting is dat AI (Artificiële Intelligentie) een stempel op deze lasertechnologie zal gaan drukken. En dit niet alleen bij het monitoren van het proces, maar ook bij het programmeren van de laserbewerking, waardoor first time right productie van zeer complexe onderdelen mogelijk zou kunnen worden.
Laser- en microverspanen zullen naast elkaar blijven bestaan en elkaar aanvullen en versterken. Wat onder invloed van duurzaamheidsregels wel een rol kan gaan spelen, is het energieverbruik. Mechanisch bewerken kost meer energie per kubieke cm materiaal dat men weghaalt dan contactloze processen, zoals EDM en laserbewerken.
Laser- en microverspanen zullen naast elkaar blijven bestaan en elkaar aanvullen en versterken. Wat onder invloed van duurzaamheidsregels wel een rol kan gaan spelen, is het energieverbruik.
PECM: contactloos voor serieproductie
Een in de Benelux relatief nieuwe technologie voor seriematig precisiebewerken, is Precision Electrochemical Machining (PECM). Met deze technologie kan men zowel voor-, tussen- als finishbewerkingen doen.
PECM is een doorontwikkeling van elektrochemisch verspanen. Beide technieken gebruiken een anode (het werkstuk) en een kathode (het gereedschap) om het materiaal dat zich in een geleidend medium bevindt, contactloos te bewerken.
Bij ECM wordt deze elektrode tot 80 à 800 µm van het werkstuk gebracht. Door de stroomimpuls wordt van het werkstuk materiaal afgenomen in de vorm van het gereedschap (de kathode). Bij PECM wordt de spleet tussen werkstuk en gereedschap teruggebracht tot 10 µm. In tegenstelling tot bij EDM springt er geen vonk over, omdat de afstand telkens direct na de stroomimpuls vergroot wordt en er vers elektrolyt tussen de anode en kathode stroomt. Dit proces herhaalt zich met een frequentie van 100 Hz.
Voordelen
De technologie heeft twee belangrijke voordelen. De eerste is dat de materiaaleigenschappen van het werkstuk niet worden aangetast, omdat er geen warmte-inbreng plaatsvindt. Er kan dus geen witte rand ontstaan, een dunne laag die jarenlang de acceptatie van EDM in de luchtvaartindustrie afremde.
Het tweede voordeel is dat het gereedschap absoluut niet slijt, in tegenstelling tot de elektrode die men voor zinkvonken nodig heeft. Deze laatste moet regelmatig vervangen worden, maar het PECM-gereedschap kan in principe voor een oneindig aantal producten worden gebruikt.
Met name hierdoor leent de technologie zich voor serieproductie van heel nauwkeurige onderdelen. Oppervlakteruwheden van Ra 0,05 µm zijn haalbaar, net als een hoge maatnauwkeurigheid. De bewerkingstijd is bovendien relatief kort. En deze blijft gelijk, bij het eerste en het laatste werkstuk. Daarnaast zijn de werkstukken absoluut braamvrij. In de Nederlandse precisie-industrie zijn er inmiddels enkele bedrijven die meerdere machines van dit type in huis hebben, als aanvulling op draad- en zinkvonken.

Draadvonken anno 2024
Een interessante ontwikkeling bij draadvonken – een nog steeds veelgebruikte precisietechnologie – is de komst van een nieuw type draad voor het bewerken van onderdelen die aan de hoogste reinheidseisen moeten voldoen. Als men deze bewerkt met koperhoudende draad, slaan deeltjes van de draad neer op het oppervlak, wat moeilijk tot niet te reinigen valt. Tot nog toe gold als alternatief het gebruik van wolfraamdraad, wat echter aanzienlijk duurder is. In Nederland hebben partijen een nieuw type gecoate draad ontwikkeld die geen verontreiniging achterlaat.
Een andere oplossing is het gebruik van A.I. om snel te leren wat het ideale moment is om de vonkpuls af te breken, voor er draadbreuk optreedt. Hierdoor kan men makkelijker met kopervrije draad vonken; iets dat anders veel testen vereist.
Een derde innovatie op EDM-vlak is het vonken met een roterende draad. De draad roteert licht gekanteld om de eigen as heen. Deze rotatie zorgt ervoor dat men steeds met een verse draad snijdt. Dit zorgt voor een hogere vormnauwkeurigheid, lagere oppervlakteruwheid en tegelijkertijd voor 30 % minder draadverbruik.
