Slijpen naar hoger niveau getild
Is geautomatiseerd slijpen volgende stap?
Slijpmachinefabrikanten doen nog steeds goede zaken, ondanks dat menigeen jaren geleden voorspelde dat 5-assige freestechniek én het harddraaien het slijpen zouden gaan verdringen. Dat is niet gebeurd, integendeel. Slijptechnologie is op verschillende manieren naar een hoger niveau getild. Niet in de laatste plaats dankzij de geavanceerde besturingstechnologie. Zal automatisering de volgende stap zijn?
Slijpen biedt superieure oppervlaktekwaliteit
Het simpele feit dat machinebouwers slijpspindels integreren in een 5-assig bewerkingscentrum geeft aan dat slijptechnologie in bepaalde toepassingen nog altijd superieur is. Bepaalde oppervlaktekwaliteiten zijn enkel te realiseren met slijpen.
Voor bijvoorbeeld kritische onderdelen en lange, slanke of dunwandige componenten in de medische, luchtvaart- en automobielsector, maar ook in andere sectoren kiezen engineers nog steeds voor de superieure oppervlaktekwaliteit en nauwkeurigheid die de techniek van het slijpen te bieden heeft. Dit is onder meer te danken aan de reproduceerbaarheid van het slijpproces.
Bepaalde oppervlaktekwaliteiten zijn enkel te realiseren door middel van slijpen
Zeker bij het bewerken van harde materialen zoals hardmetaal, keramiek en composieten, zijn het relatief hoge spaanvolume en de beperktere gereedschapsslijtage twee voordelen waarmee slijpen de concurrentiestrijd met andere bewerkingstechnieken in vele gevallen wint.
Vergeleken met harddraaien – voor bepaalde toepassingen zeker een alternatief – levert slijpen als voordeel een betere oppervlaktekwaliteit en een hogere vormnauwkeurigheid.
Wel vereist het slijpen extra machines, extra omspannen en langere cyclustijden. De toepassing én de gestelde kwaliteitseisen zijn hier de bepalende keuzefactoren.
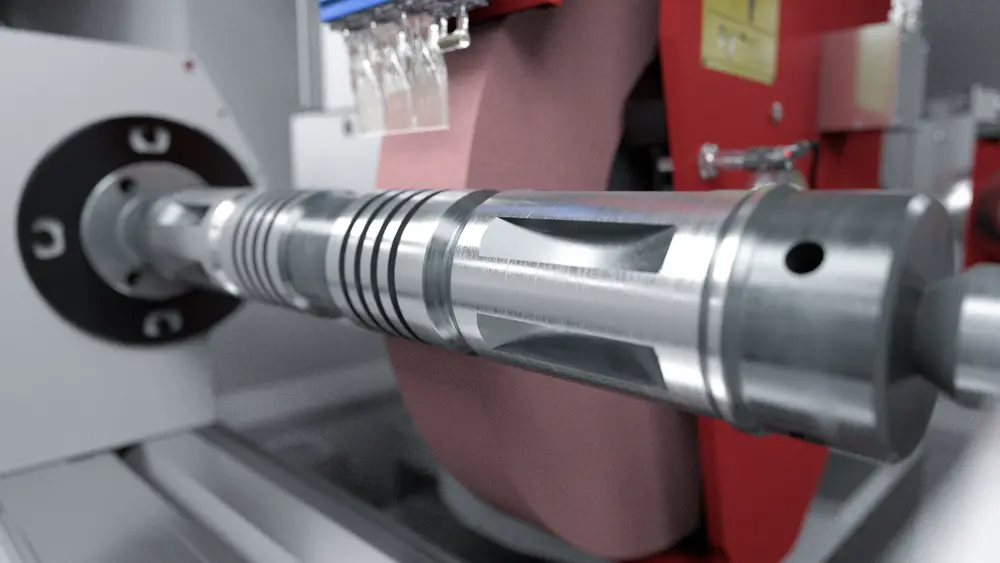
Adaptieve Slijpprocessen
Slijpen blijft nog steeds een vak apart binnen de verspaning. De techniek veronderstelt heel wat kennis en ervaring van een slijpmachineoperator, iets waaraan het tegenwoordig steeds meer ontbreekt. Machinebouwers ontwikkelen daarom adaptieve slijpprocessen en maken de slijpmachinebesturing intuïtiever en gebruiksvriendelijker.
Beide oplossingen zijn mogelijk door de ontwikkelingen op het vlak van digitalisering. Door met sensoren en via de besturing het slijpproces continu te monitoren en op basis van gemeten waarden het proces bij te stellen, wordt het slijpen autonomer. In een adaptief slijpproces gebeurt de aanpassing van de procesparameters (snijsnelheid, voeding, snedediepte) automatisch, en wordt deze continu in een optimale bandbreedte gehouden.
Productiever en consistentere kwaliteit
Dit leidt tot een hogere productiviteit zonder extra inzet van operators met een specifieke kennis. Ook zorgt het voor een consistentere kwaliteit (kleinere kwaliteitsvariaties). Ten slotte bespaart een adaptief proces tijd bij het instellen en optimaliseren van de parameters.
Zo’n adaptief slijpproces vereist geïntegreerde sensoren (akoestische, kracht- en vermogenssensoren, vibratiesensoren, optische en temperatuursensoren) en software om alle gecapteerde sensordata te analyseren. Dankzij 'Machine Learning'-algoritmen wordt het steeds beter mogelijk om al die data (zelfs in real time) te analyseren en beslissingen te nemen over de procesparameters. Met deze algoritmen kan men in de data fouten herkennen en al tijdens het slijpproces ingrijpen.
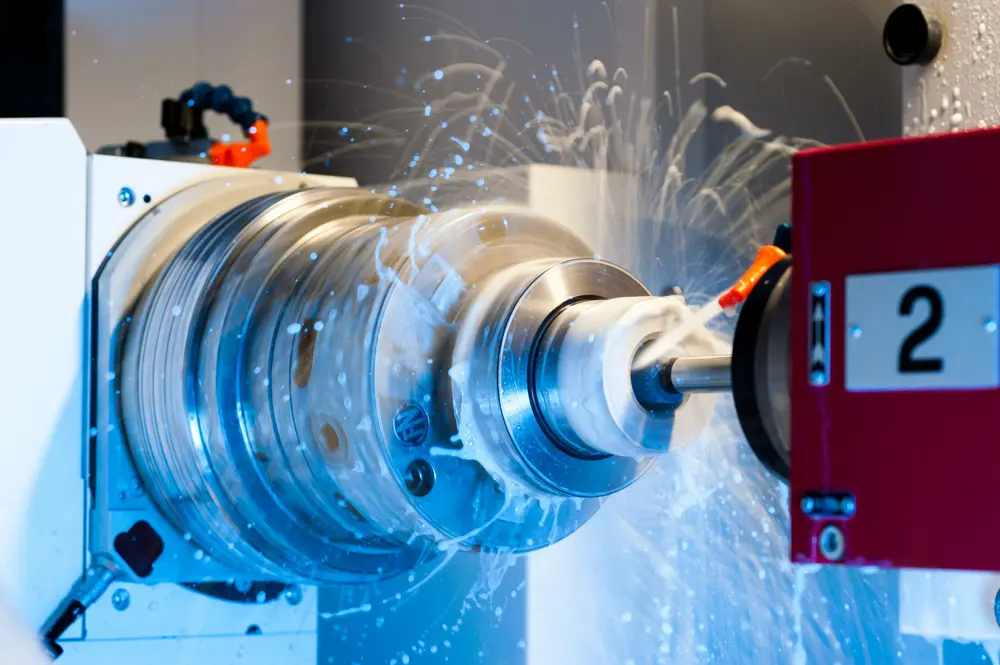
'Closed loop'-proces
De besturing van de CNC-slijpmachine moet in het adaptieve proces onmiddellijk kunnen reageren op de signalen. In de praktijk hebben de fabrikanten daarom een 'closed loop'-proces ontwikkeld, waarbij data-output dient als input voor het (automatisch) instellen van procesparameters.
Een andere ontwikkeling is het gebruik van umati (universal machine technology interface) als interface naar andere machines, randapparatuur en software. Ook bij slijpmachines kiezen machinebouwers voor deze vanuit Duitsland ontwikkelde open, gestandaardiseerde interface om het automatiseren en het uitwisselen van data te vergemakkelijken.
Daarnaast zijn fabrikanten de afgelopen jaren bezig geweest om kennis van slijptechnologie te integreren in besturingstechnologie, om het hele proces minder afhankelijk te maken van de machineoperator.
Tegelijkertijd moet dit slijptechnologie toegankelijker maken voor een bredere doelgroep, zodat medewerkers sneller inzetbaar zijn. Digitalisering en de directe koppeling naar Internet of Things worden hiervoor ingezet. Zo kunnen gebruikers hun eigen scherm op de bedieningsterminal opvragen, afgestemd op hun eigen niveau.
Bij sommige fabrikanten kan men de slijpmachine inmiddels programmeren via apps op tablet of smartphone. Daarbij schakelt de gebruiker naadloos van data in de cloud naar data op het eigen servernetwerk.
Door met templates te werken, probeert men het programmeren verder te vereenvoudigen en quasi te parametriseren. Door een 3D-model van het werkstuk in te lezen en de verschillende vlakken die men wil slijpen te koppelen aan een specifieke slijp- en africhttechnologie, wordt het programmeren deels geautomatiseerd. Zo kan men ook via een muisklik posities aangeven die in de machine gemeten moeten worden, waarna deze programmaregels automatisch aan het slijpprogramma worden toegevoegd.
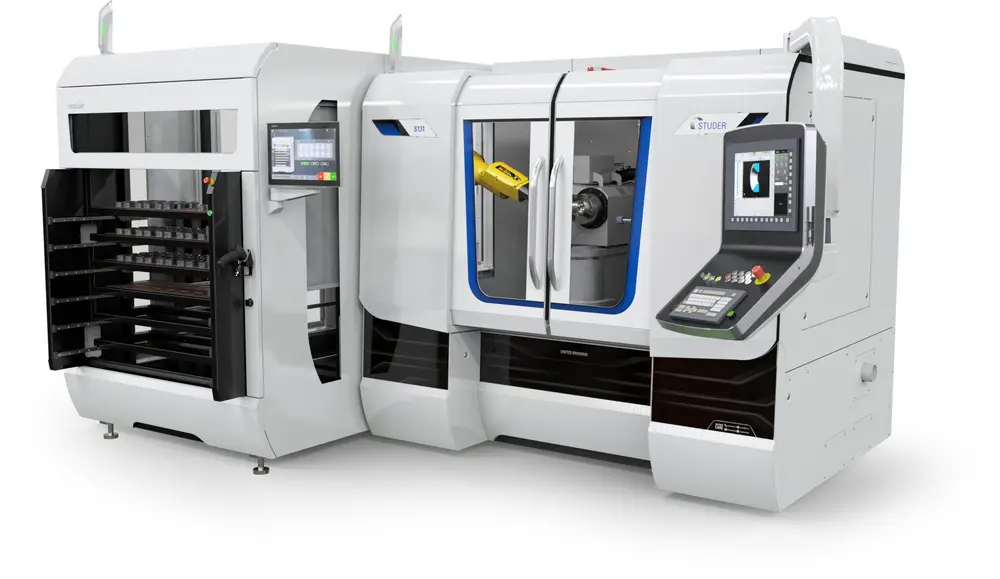
Geautomatiseerd slijpen
Automatisering is in de slijpwereld nog niet zover doorgebroken als bij het frezen of draaien. Dit verandert stilaan, niet alleen om economische redenen maar ook vanwege het gebrek aan vakmensen.
Een slijpmachine automatiseren behelst meer dan enkel het automatisch beladen
Automatiseren van een slijpmachine vraagt echter om een andere oplossing dan enkel het automatisch beladen van een freesmachine. Dit heeft vooral te maken met de nauwkeurigheid. Werkstukken moeten immers in micrometerbereik nauwkeurig worden opgespannen.
Hier komen eigenlijk alle ontwikkelingen samen, zoals de nieuwe besturingstechnologie, connectiviteit en data-uitwisseling en adaptieve procescontrole.
In een geautomatiseerd slijpproces gaat het om meer dan alleen het automatisch beladen van de machine. Waar dit concept als eerste doorbreekt, is in het slijpen van gereedschappen. Hiervoor zijn op internationale beurzen het afgelopen jaar concepten gedemonstreerd waarmee een frees vanaf een onbewerkt halffabricaat volledig geautomatiseerd wordt geslepen en gemeten.
Voor het transport tussen de verschillende machines zet men AGV’s in. Ook hier speelt data-uitwisseling tussen machines van verschillende fabrikanten een sleutelrol, omdat meetdata teruggevoerd worden naar het slijpprogramma om de bewerking van het volgende gereedschap direct te corrigeren.
Ook bij vlak- en rondslijpen zal de robot de komende jaren steeds vaker gezien worden.
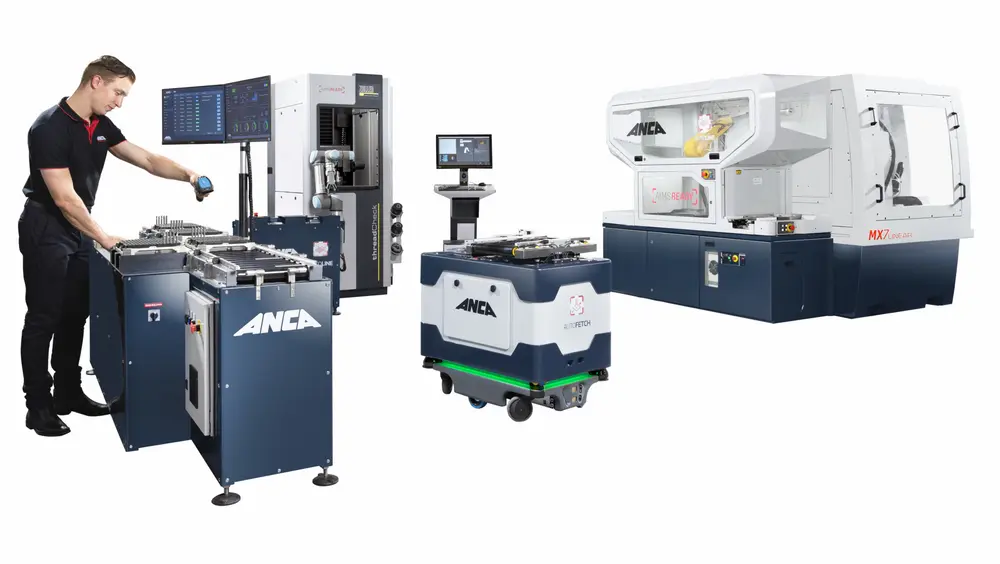
Jongste ontwikkelingen op het Slijpvlak
Dressen van slijpschijven
Qua technologie zijn er nog meer ontwikkelingen. Een hiervan is het dressen van hybride- en metaalgebonden slijpschijven. Deze technologie is oorspronkelijk ontwikkeld in Zwitserland omdat de hoge slijtvastheid van CBN- of diamantschijven het dressen ervan bemoeilijkt.
Doordat in de schijf zowel metaaldeeltjes als diamant zitten, ontstaan er tijdens het dressen microkorrels en blijft de diamantstructuur onaangetast, Door de slijpschijven met vonkerosie opnieuw af te richten, kan men zonder dat er krachten op de slijpschijf komen zeer nauwkeurig complexe geometrieën aanbrengen.
Uiteraard kan dit alleen met metaalgebonden slijpschijven, omdat het echt om vonkeroderen gaat dat geïntegreerd is in de slijpmachine. Met deze technologie kan men de productiviteit van de slijpmachine verbeteren en voor een constante vormnauwkeurigheid van het slijpproces zorgen.
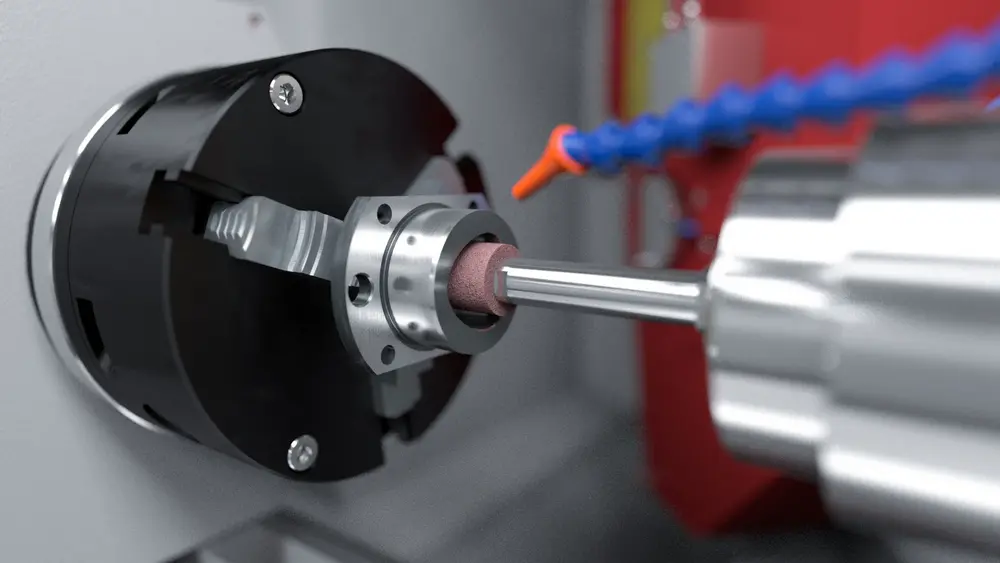
Verlaagd koelmiddel en energieverbruik
Een ander recente ontwikkeling is het reduceren van het gebruik van koelsmeermiddel en energie om het slijpproces te koelen. Om milieu- en energieredenen wil men dit verbruik gaan reduceren. Een oplossing hiervoor is het gerichter doseren van de vloeistoffen op het slijpvlak, wat tot 40% reductie van het vloeistofverbruik en zelfs een halvering van het energieverbruik leidt.
Additive manufacturing biedt een deel van de oplossing hiervoor. Door de nozzle waardoor het koelsmeermiddel komt te 3D-printen, kan men het design optimaliseren qua stroming. Door de verschillende kanalen die naast elkaar liggen, wordt het koelsmeermiddel beter verdeeld. Doordat het koelsmeermiddel precies op de juiste plek terechtkomt, wordt het effectiever benut.
Tegelijkertijd sturen signalen van sensoren de druk en het volume van deze vloeistofstroom, wat direct tot een lager energieverbruik leidt. Dit komt onder andere doordat de technologie continu monitort welke druk en volume nodig zijn, iets dat een slijper nooit zal doen. Ook hier speelt digitalisering een sleutelrol.
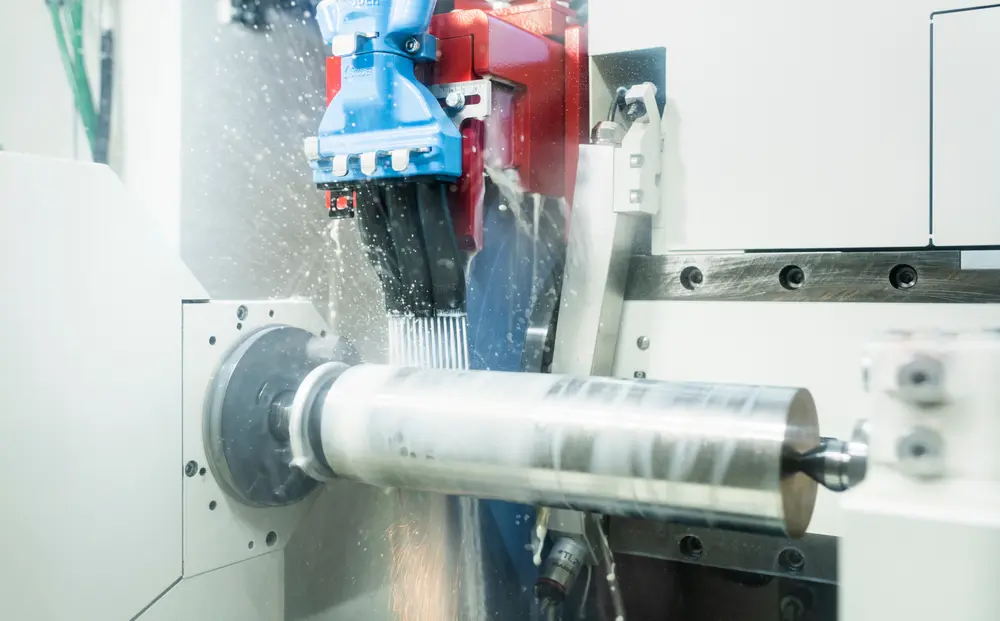
Sommige experts wijzen erop dat slijpen niet langer een eindbewerking hoeft te zijn. Het spaanvolume kan voldoende zijn om het hele proces op de slijpmachine te doen.
kRUIPVOERSLIJPEN IS WEER HOT
Ze doelen dan met name op creep-feed grinding (CFG) oftewel kruipvoerslijpen. Deze gespecialiseerde vorm van vlakslijpen is al eind de jaren vijftig ontwikkeld, maar het is vooral te danken aan de ontwikkeling van abrassief materiaal en slijpschijven dat de technologie nu in de belangstelling staat.
Bij kruipvoerslijpen is de diepte waarin men slijpt groot (meerdere millimeters) en de voeding laag. Via deze methode zijn grote hoeveelheden materiaal in één keer te verwijderen, wat ze efficiënt maakt voor slijptoepassingen waar conventionele slijptechnieken tijdrovend of minder effectief zijn.
Bij het slijpen met kruipvoeding wordt een slijpschijf met een zeer poreuze structuur gebruikt, in de meeste gevallen samengesteld uit slijpkorrels die aan elkaar gebonden zijn in een hars of verglaasde matrix. De koelvloeistof of snijvloeistof die in dit proces wordt gebruikt, wordt meestal in grote volumes gebruikt om het werkstuk te koelen en de slijpschilfers weg te spoelen. Qua spaanvolume komt men hiermee in de buurt van frezen.
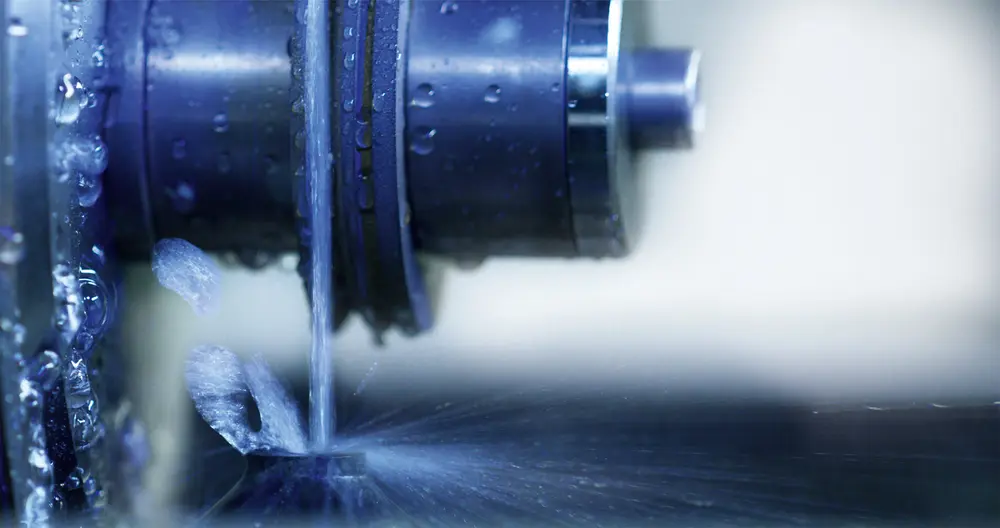
3D-geprinte Slijpschijven
Naast de ontwikkelingen aan de hardwarekant van slijptechnologie, is er ook nieuws aan de kant van slijpgereedschappen, zoals het 3D-printen van slijpschijven. Onderzoek aan universiteiten heeft uitgewezen dat dankzij de printtechnologie de morfologie en de eigenschappen van poreuze structuur van de slijpschijf heel precies gestuurd kunnen worden.
3D-geprinte slijptools leveren tot 40% betere prestaties
Dit maakt in principe maatwerkoplossingen voor bepaalde toepassingen mogelijk. Poreuze metaalgebonden slijpschrijven zijn moeilijk te maken via de traditionele technieken. Met 3D-printen kan men de matrixstructuur ontwerpen en precies produceren. Ook kan men speciale koelgaten en kanalen integreren, en nieuwe geometrieën printen, passend bij heel nieuwe vormen van producten die geslepen moeten worden. Testen tonen dat dergelijke slijptools tot 40% betere prestaties leveren.