Bramen veelal door versleten ponsgereedschap
Hoe weet je dat een gereedschap aan herslijpen toe is?
Bij elke scheidingstechniek hoort een bepaalde afwerkingskwaliteit die inherent is aan het proces. Hetzelfde kan gezegd worden van een machine. Maar soms schort er wat en merk je dat je veel meer bramen hebt dan gewoonlijk, zonder dat je iets aan de parameters hebt veranderd. In het geval van ponsen moet je dan in de eerste plaats naar de staat van je gereedschappen kijken. Wellicht kunnen ze een herslijpbeurt gebruiken. Een tweede mogelijke oorzaak van een inferieure kwaliteit is een slechte uitlijning van het gereedschapsstation. Ook dat is te verhelpen.
Hoe ontstaan bramen?
Helemaal braamloos ponsen? Moeilijk. Door de mechanische manier waarop een ponsgereedschap door het materiaal snijdt, zal er zich op het onderoppervlak altijd een kleine braam vormen. Om te begrijpen hoe dat komt, moeten we wat dieper ingaan op wat er gebeurt tijdens de ponsslag.
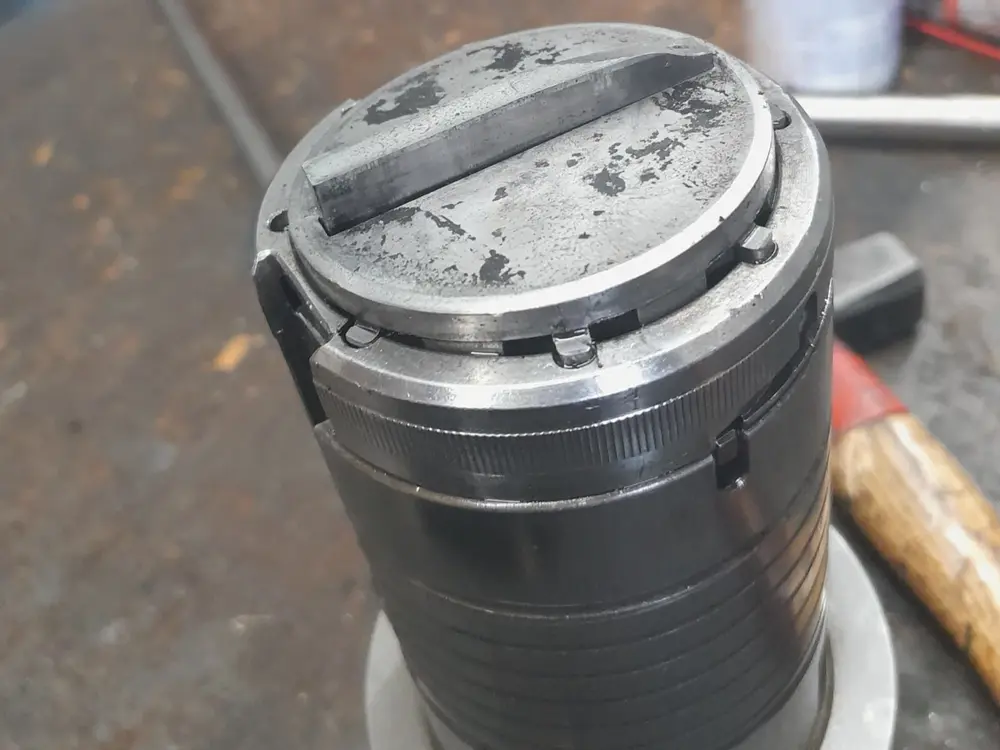
Plooimoment
Alvorens het stuk uit de plaat word gesneden en afgebroken, vindt er eerst een plooimoment plaats. De stempel maakt namelijk contact met het materiaal terwijl de contour van die stempel kleiner is dan die van de matrijsopening. Hoe groot dat plooimoment is, hangt dus af van de snijspeling tussen stempel en matrijs, maar net zo goed van de verhouding tussen de plaatdikte en de grootte van het te ponsen gat. Ook het type materiaal speelt daarin een rol.
Voorbij de plastische vloeigrens
Het plooimoment zorgt ervoor dat het materiaal eerst elastisch en daarna plastisch zal vloeien. De indrukradius zichtbaar op zowel het geponste gat als de ponsafvaldop is trouwens het gevolg van de plastische vervorming. Naarmate de stempel dieper in het materiaal drukt, zal de plastische vervorming groter en groter worden tot de vloeigrens is bereikt. Op dat moment begint het ponsgereedschap door het materiaal te snijden. Zo ontstaat een glad glimmend oppervlak (= de burnish zone) met dezelfde afmetingen als de omtrek van de stempel.
Finale stadium: breuk
In een laatste fase breekt het materiaal onder een hoek die loopt van de stempel- naar de grotere matrijsdoorsnede. Het is aan die rand op het onderoppervlak van het materiaal dat er zich een minimale braamvorming voordoet als gevolg van het mechanische scheidingsproces.
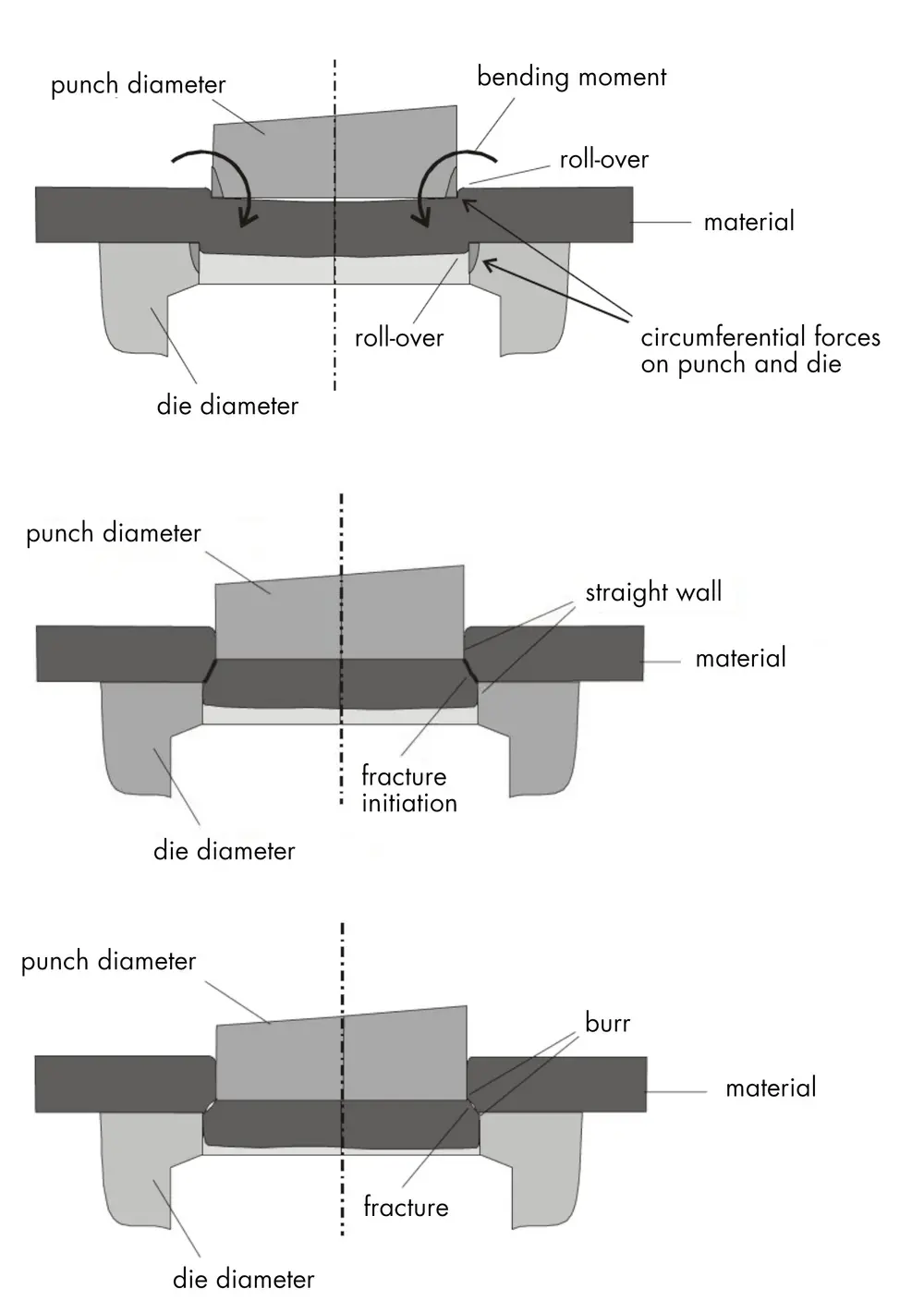
Oorzaken inferieure randkwaliteit
Een beetje braamvorming is eigen aan het proces en dus volstrekt normaal, zolang die minimaal is weliswaar. In die zin kan je de mate van braamvorming zelfs gebruiken als waardemeter voor de kwaliteit van je ponsproces. Als de randafwerking slechter is dan wat je van een standaard ponsproces mag verwachten, kan dat slechts aan een paar dingen liggen. Specifiek focussend op braamvorming heeft het bijna altijd te maken met een van de volgende drie oorzaken: een verkeerde snijspeling tussen stempel en matrijs, stompe ponsgereedschappen of een slechte uitlijning.
Een te kleine snijspeling veroorzaakt een snellere slijtage van het ponsgereedschap.
Correcte snijspeling
De snijspeling tussen stempel en matrijs hangt zowel af van de plaatdikte als van het type materiaal. Ze bepaalt in grote mate het plooimoment en op die manier ook het verloop van het ponsproces. Bovendien zorgt een te kleine snijspeling voor een snellere slijtage van het ponsgereedschap. Maar hoe kom je tot een correcte snijspeling? Daarvoor bestaat een eenvoudige formule, die rekening houdt met de twee eerder genoemde variabelen: d = p + (k*t), met d diameter matrijs (of zijde), p diameter stempel (of zijde), t plaatdikte en k-factor (afhankelijk van het materiaal).
Staat van het gereedschap
Wellicht de meest voorkomende oorzaak van excessieve braamvorming zijn stompe ponsgereedschappen. Die ontstaat doordat het vooral de omtrekranden van de stempel en de matrijs zijn die contact maken met het materiaal en zo de meeste ponskracht opnemen. Door de stompe snijkanten start de breuk en braamvorming al voor de radius van die snijkanten, wat dus aanleiding geeft tot meer bramen. Maar naast meer bramen zorgen stompe gereedschappen er ook voor dat de machine meer kracht moet gebruiken bij elke ponsslag. Dat kan je trouwens ook goed horen. Met andere woorden, niet alleen de afwerkingskwaliteit maar ook de machine zelf heeft eronder te lijden. Nog een ander kwalijk gevolg van versleten ponsgereedschappen is dat de plaat slechter van de stempel wordt afgestroopt. Op tijd je ponsgereedschappen laten herslijpen is dus de boodschap.
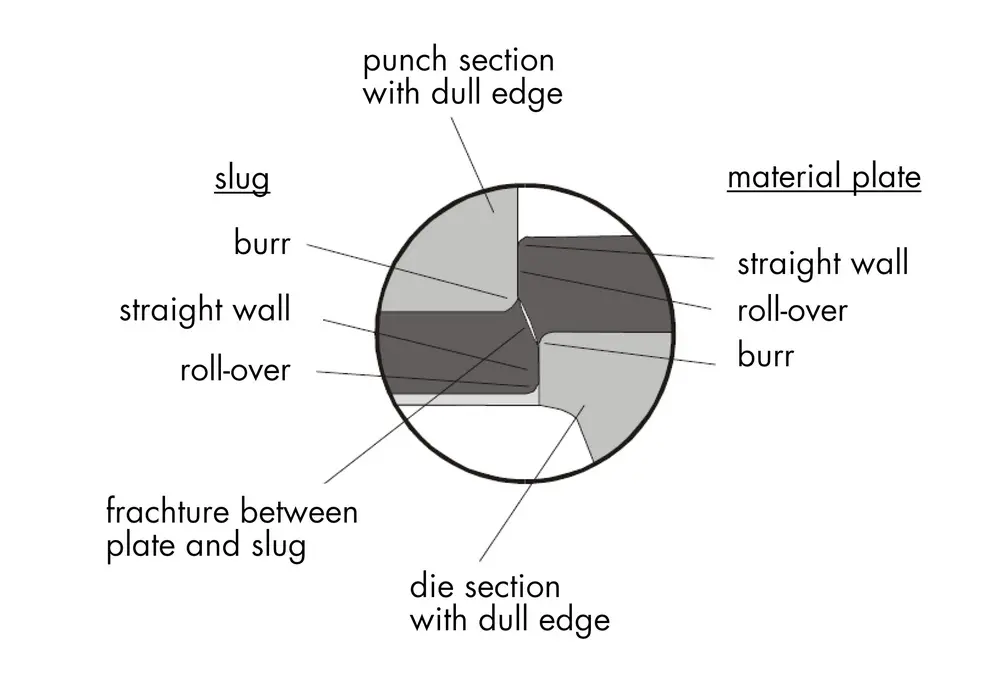
Bij een stompe ponstool heeft de ponsmachine meer kracht nodig bij elke ponsslag, wat ook goed hoorbaar is
Uitlijning tussen stempel en matrijs
Een onregelmatig slijtagebeeld en met name braamvorming kunnen ook wijzen op een foutieve verticale uitlijning van het gereedschapsstation. De stempel moet samen met het materiaal namelijk op een heel specifieke en precieze manier door de matrijsopening geduwd worden, dat wil zeggen met evenveel speling rondom het ponspunt. Daarvoor is de verticale uitlijning verantwoordelijk. Radiaal gaat het over de rechtheid en de uniformiteit van de ponsgaten, eerder dan over braamvorming. Hoe dan ook, als operator moet je sowieso een toolset bij de hand hebben om dit soort van fouten op te lossen.
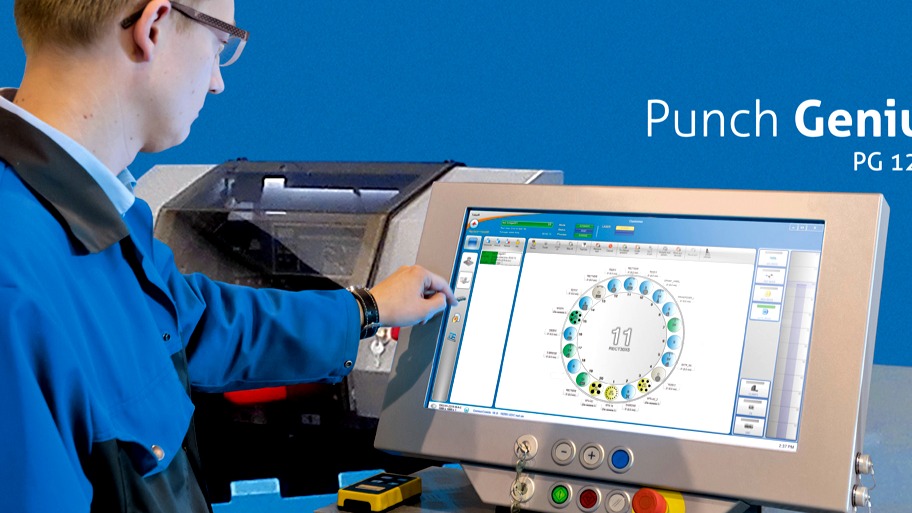
Wanneer is het tijd om te herslijpen?
Om tal van redenen (zie eerder) moeten ponsgereedschappen dus scherp blijven. Maar hoe weet je dat het tijd is om ze te herslijpen? Het is bijzonder moeilijk om daar een exact aantal ponsslagen op te kleven. Dat hangt namelijk van te veel factoren af: het materiaaltype dat geponst wordt, de kwaliteit waaruit het ponsgereedschap is gemaakt (zie kaderstuk), de mate waarin de correcte snijspeling wordt toegepast, het gebruik van gepaste smering …
Gelukkig bestaan er wel een aantal signalen om slijtage tijdig te herkennen. Ervaren operatoren zien aan de braamvorming op de ponsslak (slug) of het gereedschap aan herslijpen toe is. Roll-over op het bovenvlak is een duidelijke indicatie, net als overmatige braam aan de onderkant. Je kan ook de rand van je ponsstuk tegen het licht houden en visueel inspecteren: het licht moet mooi weerkaatsen van de radius van de rand. Daarnaast heb je nog de nageltest. Daarbij controleer je of het ponsgereedschap nog scherp genoeg is om je nagel lichtjes te vijlen.
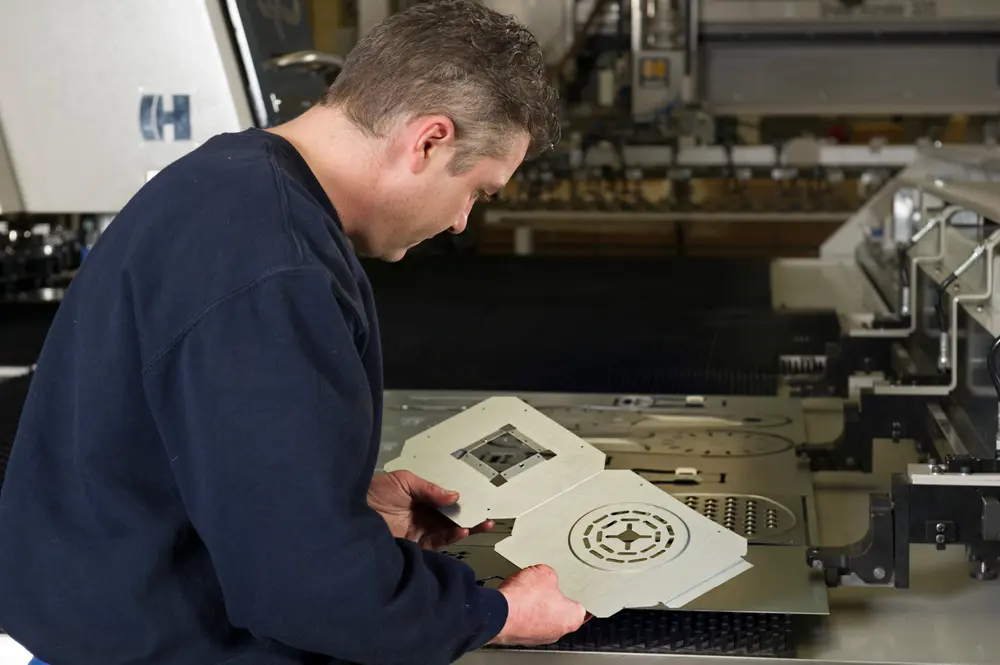
Hoe vaak kan je herslijpen?
Herslijpen gebeurt geleidelijk: ongeveer 0,01 tot 0,02 mm per stap. En dat in een koelend oliebad om de ongewenste neveneffecten van oververhitting te vermijden. Per herslijpbeurt neemt men tussen de 0,1 en 0,2 mm aan materiaal weg. Volstaat dat niet, dan is dit een teken dat er te lang is gewacht met herslijpen en het ponsgereedschap dus eigenlijk al te bot was voor een optimaal ponsproces.
Hoe vaak je de stempels kan herslijpen hangt onder meer af van de gereedschapsfabrikant, het tooltype en het station. Bij sommige tools kan je bijvoorbeeld de lengte aanpassen om het verlies van materiaal te compenseren. Zo kom je tot een totale levensduur die schommelt tussen 1,5 en 13 mm. Als de gereedschappen op een correcte manier zijn geslepen, is er geen impact op het aantal slagen noch op de kwaliteit van de gaten. Wel is het belangrijk om de scherpe kanten na herslijpen te breken. Bijvoorbeeld met een stukje schuurpapier. Vergeet ook niet het gereedschap te demagnetiseren (als het magnetisch is opgespannen in de slijpmachine). Anders zal de ponsafvaldop gaan kleven aan de stempel of matrijs, wat tot braamvorming leidt.
Materiaal gereedschappen
Ponsgereedschappen heb je in allerlei soorten en kwaliteiten van staal, gaande van poederstaal, standaard gereedschapsstaal tot hogesterktestaal. Hoe hoger de kwaliteit, hoe meer slagen je kan ponsen vooraleer de stempel en matrijzen herslepen moeten worden. Fabrikanten komen ook met steeds betere coatings, vaak op basis van titaniumnitride (TiN) of titaniumcarbonitride (TiCN), om de levensduur nog serieus te verlengen door de slijtageweerstand van de stempelflanken te verhogen. Want zeker bij het ponsen van roestvaststaal, aluminium en andere abrasieve staalsoorten heeft het plaatmateriaal de neiging om rond de stempel te gaan kleven, met een zogenaamde koudlas tot gevolg. En die zorgt dus voor een snelle flankslijtage van de stempel (en grote afstroopkrachten).
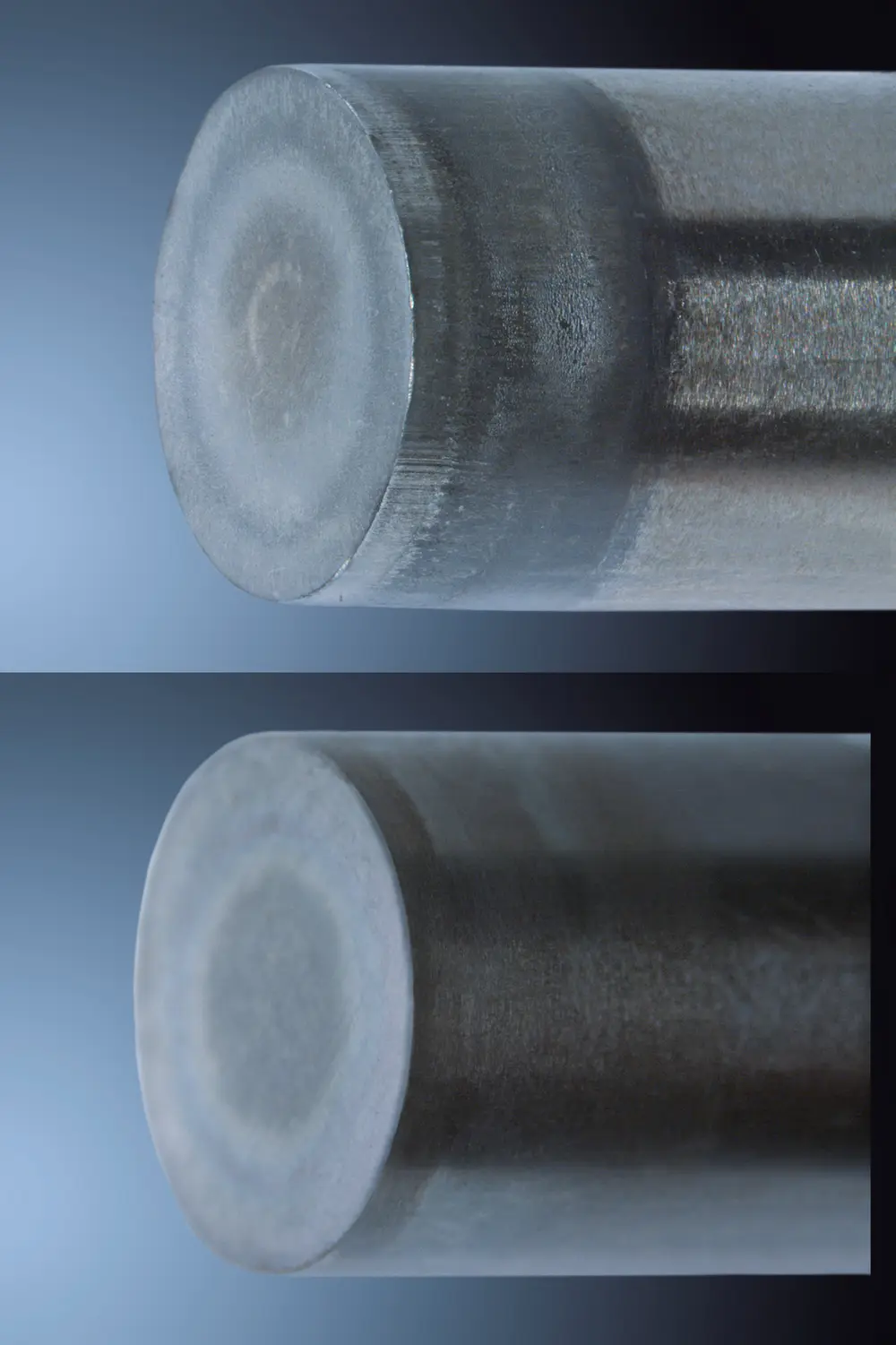
Met medewerking van Euromac, Haco, Prima Power en VAC Machines