Tips en tricks bij het boren van diepe, slanke gaten
Hoe kies je de juiste technologie en gereedschappEN?
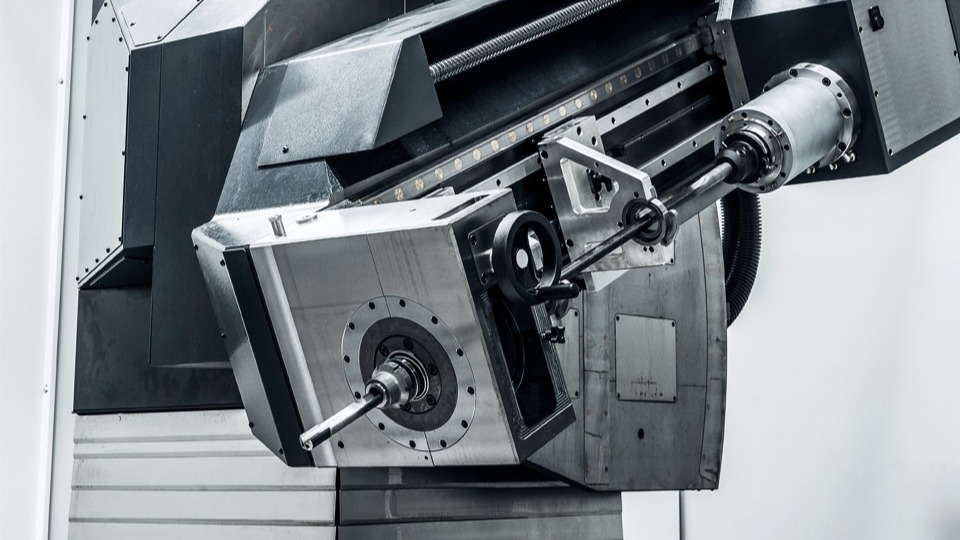
'Diepgatboren' en 'langgatboren' zijn twee begrippen die door elkaar worden gebruikt maar die hetzelfde beogen: diepe gaten maken met gereedschappen met een hoge lengte-diameterratio. Dit is evenwel gemakkelijker gezegd dan gedaan, met het afvoeren van de spanen uit het diepe gat als grootste uitdaging.
Actuele technologie
Vooral in de automobielindustrie wordt deze bewerking vaak gebruikt, onder andere in de productie van motorblokken en cilinderkoppen. Ook bij de elektrische voertuigen zijn er nog steeds toepassingen te vinden, bijvoorbeeld bij de behuizing voor het batterijpakket. En in onderdelen voor de energietransitie, zoals de productie van warmtewisselaars, zijn er eveneens diepe, nauwkeurige gaten nodig. De diepgatboortechnologie zal dus altijd wel een actuele bewerkingstechnologie blijven.
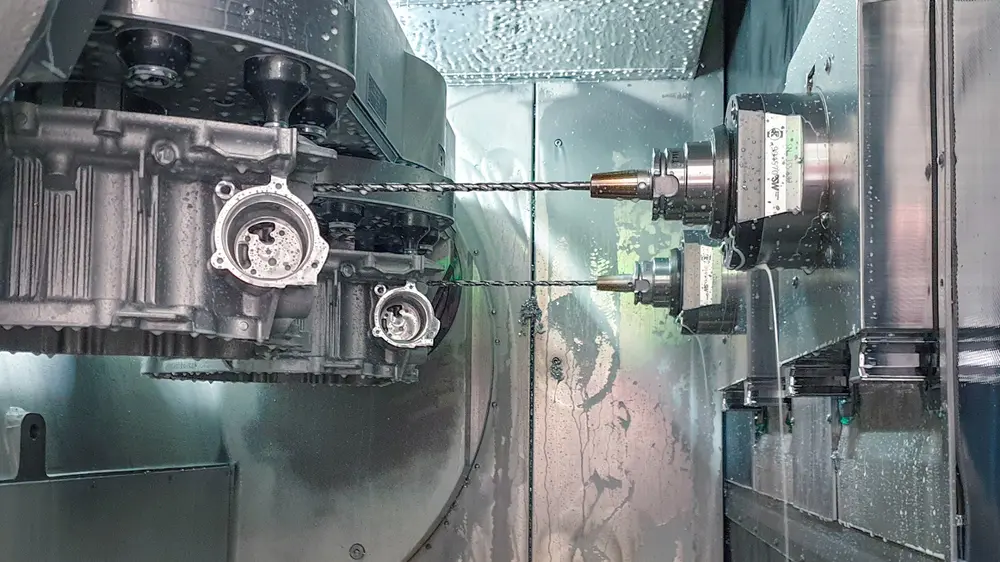
Meerdere begrippen
In de sector wordt er veel gesproken over 'diepgatboren', maar er bestaan ook andere benamingen voor: 'kanonboren', 'gundrills', '1-lippenboren' en 'langgatboren'. Hoewel dit het misschien verwarrend maakt, gaat het telkens om hetzelfde gereedschap. De verschillende namen verwijzen soms naar specifieke toepassingen. Bijvoorbeeld 'gundrillen': de oorsprong van deze bewerking ligt in de wapenindustrie.
De groep diepgatboorgereedschappen kan je in vier typen verdelen: de boren met een gesoldeerde hardmetalen kop (vanaf 1,9 mm doorsnede en tot 6.000 mm lengte); de volhardmetalen gereedschappen die onder de 1 mm doorsnede beginnen en oplopen tot 50 mm (maximaal 100xD). De maximale diepte van het gat bedraagt voor deze volhardmetalen gereedschappen rond de 600 mm. De wisselplaatboor – oftewel de boorbaren – zijn er vanaf zo'n 12 tot ongeveer 30 mm doorsnede en kunnen een lengte hebben van 3.000 mm. Voor hetzelfde bereik kan men ook een 2-lippenboor kiezen, met een gesoldeerde hardmetalen kop op de schacht.
Spiraalboren en BTA
Er bestaat ook een variant op diepgatboren: 'BTA', 'trepanning', ontwikkeld in Japan. Dit is een bewerkingstechnologie voor grotere diameters (vanaf 20 mm) en aspectratio's tot meer dan 400xD. De speciale boorkop wordt op de boorbaar geplaatst. Het grote verschil met de andere gereedschappen is dat de snijkop meerdere snijkanten bevat, waardoor dus de productiviteit omhoog gaat. Dat is een van de belangrijkste voordelen van deze BTA-bewerking.
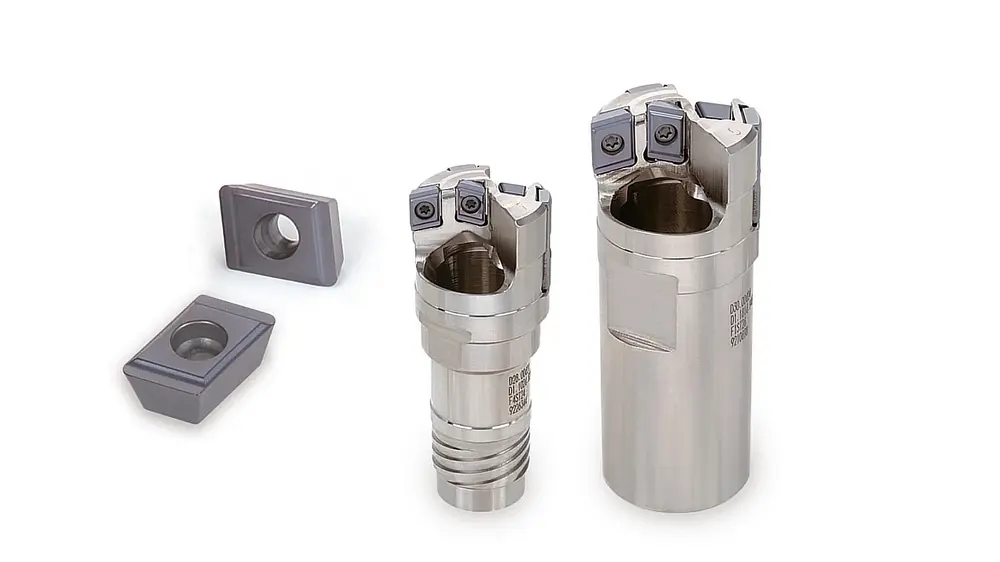
Men kan 5 tot 7 maal hogere voedingen gebruiken in vergelijking met een 1-lippenspiraalboor met dezelfde diameter. Het ideale inzetgebied zijn boorgaten van 8 tot 114 mm diameter. Het bereik van de diepgatspiraalboren loopt van onder de 1 mm tot ongeveer 50 mm. Hierboven kan men een spiraalboor gebruiken, maar de BTA-technologie biedt dan duidelijk voordelen.
Spaanafvoer
De grootste uitdaging van diepgatboren ligt voor de hand: het afvoeren van de spanen uit het diepe gat. Gebeurt dit niet op de juiste manier, dan kunnen de achterblijvende spanen het werkstuk beschadigen, ofwel breekt het gereedschap af. Beide problemen zorgen voor een behoorlijke verstoring van het productieproces, dus wil men dit voorkomen. Daarnaast is het belangrijk om trillen van het lange gereedschap te voorkomen als men echt diepe gaten boort.
De eerste stap richting een stabiel proces is de selectie van het juiste gereedschap
Gereedschapsselectie
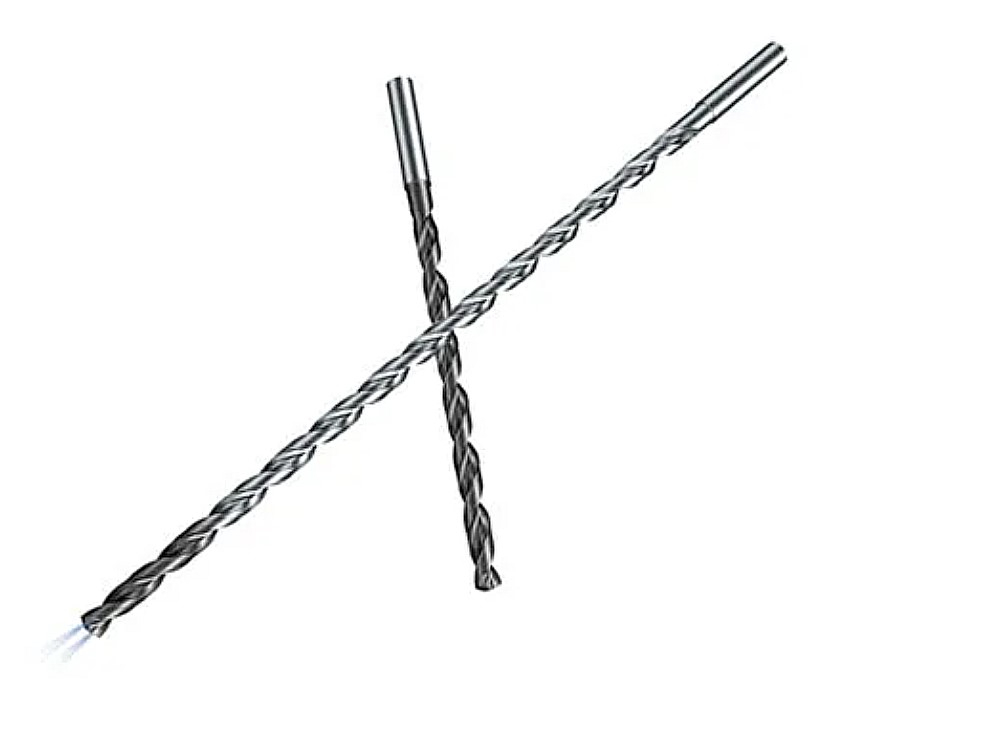
De eerste stap richting een stabiel proces is de selectie van het juiste gereedschap. Het gaat erom dat de nauwkeurige gaten op een herhaalbare manier worden geboord in een zo kort mogelijke cyclustijd en met liefst een lange standtijd van het gereedschap. Afhankelijk van de diameter van het gat zal men een keuze maken. Hoe groter de gatdiameter, des te meer keuze er is.
Koeling door het gereedschap (spiraalboor) spreekt duidelijk in het voordeel; simpelweg noodzakelijk. Ook langgatboren van een millimeter diameter zijn tegenwoordig verkrijgbaar met inwendige koeling. Met de unieke geometrie van de kop onderscheidt een langboorspiraalgereedschap zich van gewone boren.
De enkelvoudige snijkant zorgt voor een goede afvoer van de spanen. In combinatie met de juiste snijgeometrie en coating worden de spanen uit het diepe gat weggevoerd. Dit zorgt er tevens voor dat de spanen niet aan de boor gaan plakken, wat anders onherroepelijk tot beschadigingen aan de wand zou leiden.
Ook de boorstrategie is van invloed, met name voor de manier waarop het gereedschap weer uit het werkstuk komt. De moderne CAM-programma's hebben hiervoor ingebouwde features en macro's die het programmeren van de diepgatbewerking vereenvoudigen. Een voordeel van CAM-programmeren is dat men vooraf een botsingdetectie kan uitvoeren, wat zeker in een manloze of manarme productie cruciaal kan zijn.
Diepgatboren op CNC-bewerkingscentrum
Nog altijd zijn er speciale diepgatboormachines op de markt, die dus specifiek voor deze bewerking ontwikkeld zijn. Deze machines zijn vooral ontwikkeld voor serieproductie: diepe gaten boren in grote aantallen werkstukken, doordat de machines vaak met drie of vier spindels zijn uitgerust. Ook robotisering heeft hier al zijn intrede gedaan.
Daarnaast gaan deze speciaalmachines qua aspectratio verder dan bewerkingscentra waarmee ook langgatgeboord wordt. Deze aspectratio (lengte maal diameter) kan oplopen tot meer dan 400; een veelvoud van wat mogelijk is op bewerkingscentra. Toch is de opmars van diepgatboren op een bewerkingscentrum een interessante ontwikkeling, omdat dit toeleveranciers de kans biedt de onderdelen op minder machines af te werken en daarmee doorlooptijd te besparen.
Een voordeel van CAM-programmeren is dat men vooraf een botsingdetectie kan uitvoeren
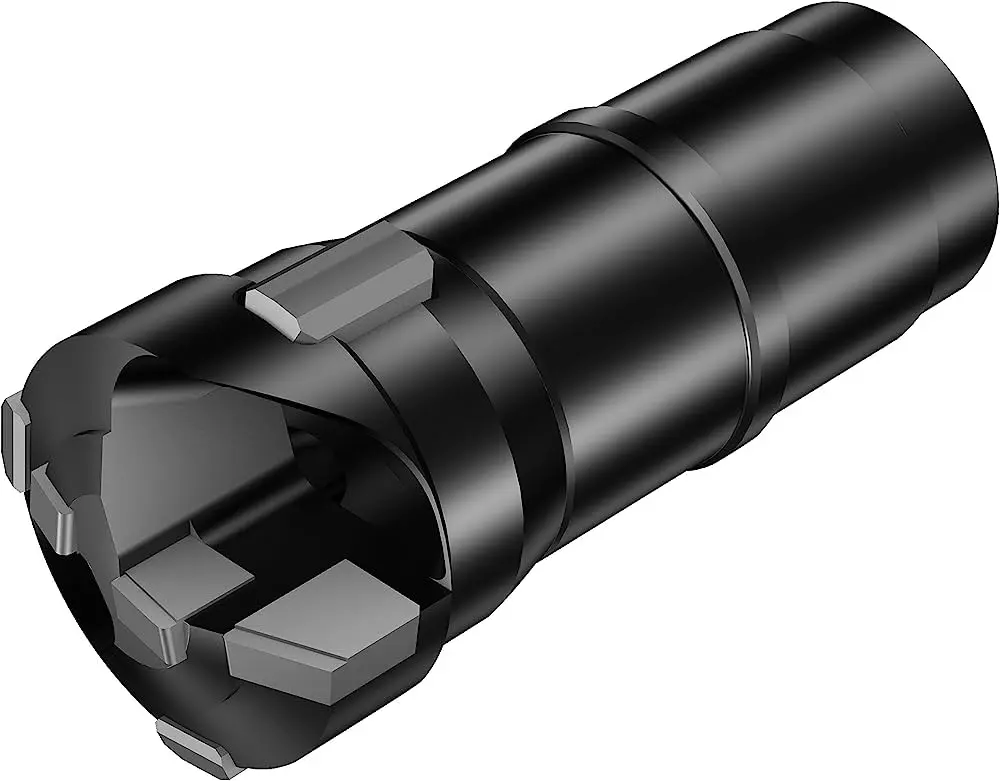
Als reactie op deze trend zijn fabrikanten van diepgatboormachines dan weer extra functionaliteiten aan hun machines gaan toevoegen, zoals freesmogelijkheden en tappen. De machinekeuze wordt vooral bepaald door de aard van het werk: seriewerk kan nog altijd het beste op de diepgatboormachines gebeuren.
De meest recente ontwikkeling is diepgatfrezen op een multitaskingmachine. Met name vanuit de olie- en gasindustrie komt de vraag naar deze bewerking, om de doorlooptijd te verkorten. Daarnaast is de betere kwaliteit doorslaggevend.
Door de hele bewerking op één machine te doen, vermijdt men het transport van de kostbare werkstukken naar de andere machines en het opnieuw opspannen. Gaten tot 1.100 mm diep kan je op deze manier bewerken. De belangrijkste voorwaarde is dat de machine over een hoog koppel beschikt.
Pilootboring maken
Zeker bij het diepgatboren op een bewerkingscentrum is het noodzakelijk eerst een pilootboring te maken. Dit gebeurt met een boor die een iets grotere diameter heeft (0,01 tot 0,03 mm) dan de diepgatboor zelf. De pilootboring wordt met een laag toerental gemaakt en zonder koelsmeermiddel. Daarna voert men de diepgatboor in het gat, nog steeds zonder koeling, totdat men enkele mm voor de bodem van de pilootboring is.
Dan schakelt men het koelsmeersysteem in en wacht men tot de aanbevolen druk wordt bereikt. Pas daarna boort men op de gewenste diepte. Het uitlopen van de boring gebeurt met het traploos verlagen van het toerental en een hoge voeding. Het koelsmeermiddel, met een olieaandeel van 12 tot 15%, moet met zowel voldoende druk als volume toegevoegd worden. En dit liefst dóór het gereedschap, zodat het echt onderin komt.
Het minimaliseren van gereedschapswisselingen is een van de succesfactoren voor langgatboren. Een lange standtijd van het gereedschap is essentieel, omdat er maar weinig machines zijn waarin een langgatboor automatisch gewisseld kan worden. Met CAM-software kan men de bewerking vooraf al virtueel optimaliseren.
Counter draaien
Op een multitaskingmachine of een CNC-draaibank kan men de nauwkeurigheid van diepgatboren verhogen door het werkstuk tegenovergesteld aan het gereedschap te roteren. Hiermee verhoogt de concentriciteit van de boring. Omdat het koelsmeermiddel zo'n grote rol speelt, is het aan te raden het volume en de druk hiervan heel precies te programmeren en aan te sturen.
Reinigen
Een belangrijke laatste stap in het proces is het verwijderen van overtollig koelsmeermiddel van de bodem van het gat. Zeker bij blinde gaten kunnen resten later in het proces tot problemen leiden.
Perslucht is hiervoor de meest gangbare en makkelijkste oplossing, maar daarmee kan men wellicht niet alle koelsmeeremulsie verwijderen. Bovendien moet men oppassen voor eventuele kleine spanen die nog meekomen. Een andere manier is met vacuüm werken. Dit is omslachtiger, maar kan bij diepe boringen soms effectiever zijn.