les Mesures de vibrations au service de la maintenance prédictive
L'IA établit un lien toujours plus étroit entre les paramètres du processus et les données vibratoires
L'une des méthodes les plus utilisées pour surveiller l'état des machines est la mesure des vibrations des pièces rotatives. Il y a plus de quatre-vingts ans, cette méthode faisait déjà couler beaucoup d'encre, mais les possibilités étaient encore limitées. Les progrès réalisés en matière de capteurs, de communication, de logiciels d'analyse, de puissance de calcul et d'intelligence artificielle font désormais de la mesure et de l'analyse des vibrations un moyen fiable d'effectuer et même de prévoir la maintenance conditionnelle.
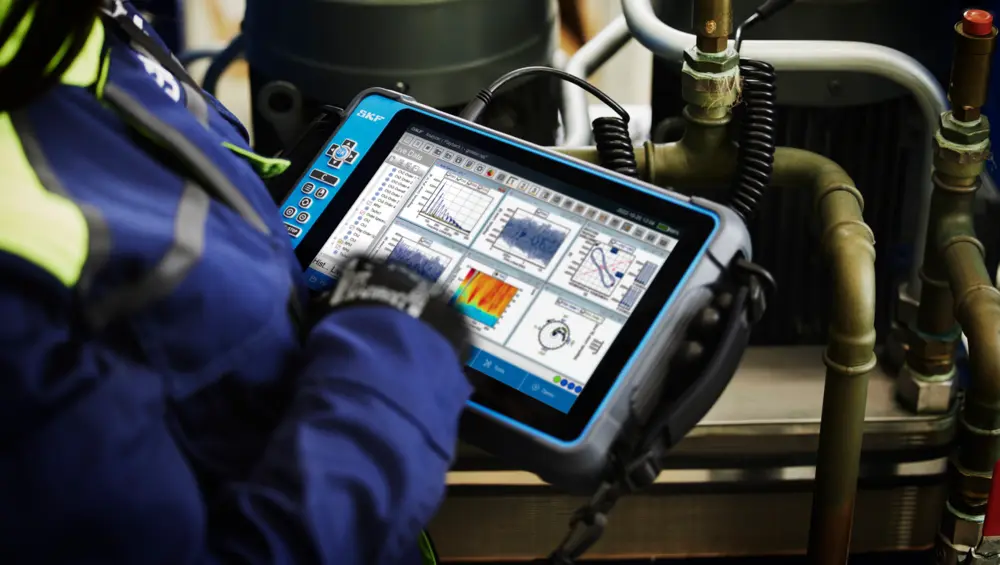
Analyse des vibrations?
Les vibrations dans les machines sont souvent un indicateur fiable de problèmes tels que le désalignement, le déséquilibre et l'usure. En conséquence, les niveaux de bruit et la consommation d'énergie augmentent et la vitesse de production et la qualité des produits diminuent. Dans le pire des cas, la machine tombe complètement en panne ou endommage les personnes, l'environnement ou la machine elle-même. Avec tous les coûts et les souffrances que cela implique.
D'un autre côté, ces mêmes vibrations constituent une donnée éminemment précieuse pour déterminer l'état d'une machine ou d'une pièce de machine. En effet, ce sont les vibrations qui constituent le premier signal de l'apparition d'une défaillance.
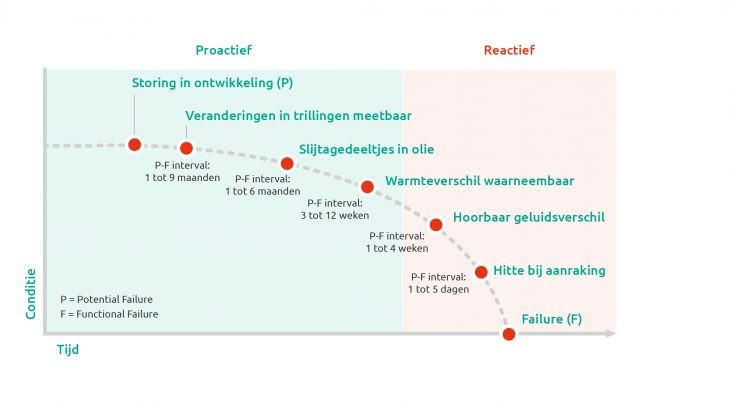
Ceci est illustré dans la Figure 1 où, à gauche, l'état d'une machine est représenté sur l'axe vertical et, sur l'axe horizontal, le temps. Dans la partie verte, la machine fonctionne bien et aucune maintenance n'est nécessaire. Lorsqu'une panne survient (premier point rouge), pratiquement rien n'est visible sur la machine dans un premier temps. De plus, le temps nécessaire pour que la défaillance se traduise par un défaut fonctionnel est de 1 à 9 mois.
Au fur et à mesure que le temps passe et que la défaillance évolue, les signes d'une défaillance fonctionnelle imminente se multiplient. Comme le montre le graphique, l'un des premiers signes est un changement dans le modèle de vibration.
À un stade encore plus avancé (dans un système hydraulique), par exemple, des particules d'usure seront trouvées dans l'huile et la machine commencera à produire de plus en plus de chaleur et de bruit, jusqu'à ce que le défaut fonctionnel se produise. Bien entendu, cette progression ne s'applique que si aucune mesure n'est prise.
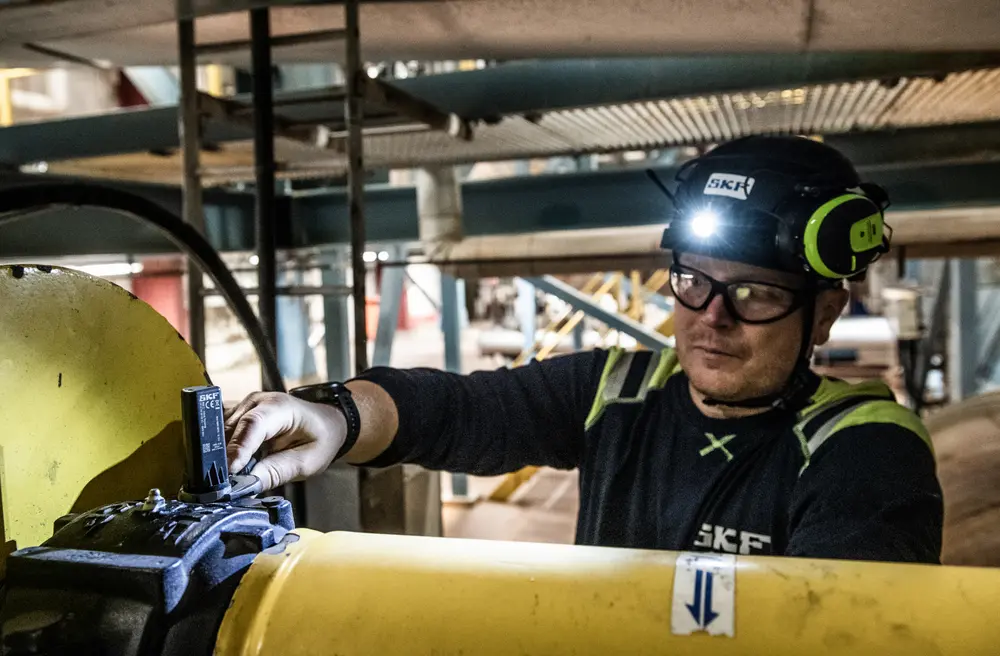
Causes et conséquences des vibrations
Causes
Le graphique ci-dessus indique directement pourquoi la mesure des vibrations est si efficace en matière de maintenance prédictive et conditionnelle: les vibrations sont facilement les premiers signes d'une défaillance à venir. En surveillant les vibrations et en détectant les changements, il reste dans la plupart des cas suffisamment de temps pour identifier la cause et y remédier ou, du moins, pour effectuer une maintenance en temps voulu. Et ce, avant même que la consommation d'énergie et les niveaux de bruit n'augmentent de façon notable ou qu'une détérioration de la qualité du produit ne devienne perceptible.
Les causes des défaillances entraînant une modification du modèle vibratoire sont généralement le désalignement, le déséquilibre (statique ou dynamique), la résonance, les pièces desserrées, la corrosion, l'endommagement des roulements et l'usure. Les vrais désalignements se produisent principalement lors de l'installation de nouvelles machines ou à la suite de catastrophes.
L'interprétation des mesures des vibrations doit toujours être confiée à un expert
D'autres problèmes sont souvent dus à l'usure, qui elle-même est souvent liée à un mauvais entretien. Par exemple, une grande partie des défaillances de roulements est liée à l'absence de lubrification ou à une lubrification inadéquate. Inversement, une bonne maintenance (lubrification) prévient les vibrations et, en fin de compte, les défaillances.
Conséquences
Les conséquences des vibrations sont diverses et ont déjà été brièvement évoquées au début de cet article. Les conséquences auxquelles il convient d'accorder la plus grande attention sont les questions de sécurité. Par exemple, de fortes vibrations peuvent entraîner des blessures humaines, des dommages à la machine ou à l'environnement.
Les dommages causés à la machine elle-même peuvent entraîner non seulement des temps d'arrêt imprévus, voire des pannes complètes, mais aussi une baisse de la disponibilité, une baisse de la qualité du produit ou une augmentation des temps d'arrêt. Dans pratiquement tous les cas, les problèmes entraîneront une augmentation des coûts en raison des heures de maintenance nécessaires, du remplacement des pièces ou de la perte de production due aux temps d'arrêt non planifiés.
capteurs et dispositifs
Maintenant que l'on sait que les vibrations sont un paramètre important pour déterminer l'état d'une machine, il est logique de s'organiser pour les mesurer et les surveiller. Il existe plusieurs capteurs et systèmes sur le marché. Si vous décidez de commencer à mesurer les vibrations dans le cadre de la maintenance conditionnelle ou de la maintenance prédictive, mieux vaut vous faire conseiller sur le choix du bon capteur. En effet, tous les capteurs ne conviennent pas à toutes les machines, à tous les composants ou encore à tous les environnements.
Les capteurs les plus courants dans le contexte de la mesure des vibrations sont les capteurs de proximité (déplacement), les capteurs de vitesse et les accéléromètres (capteurs d'accélération). Les capteurs d'accélération sont les plus couramment utilisés et sont disponibles en version piézoélectrique et MEMS (système microélectromécanique). Le premier est une variante fiable et polyvalente pour mesurer les fréquences et les amplitudes. Un capteur MEMS est moins précis en termes de fréquence et d'amplitude, mais il peut mesurer les accélérations statiques et dynamiques tout en consommant moins d'énergie.
Les capteurs de vitesse mesurent les vibrations dans une gamme de fréquences de 1 à 1.000 Hz et sont particulièrement adaptés à la mesure des vibrations dans les équipements rotatifs tels que les ventilateurs, les roulements et les pompes. Ces capteurs sont moins sensibles aux vibrations à haute fréquence que les capteurs d'accélération et sont donc moins sujets aux surcharges.
Les capteurs de déplacement – également connus sous le nom de capteurs de proximité sans contact – sont utilisés pour mesurer la position ou le mouvement de l'arbre sans contact physique afin de déterminer le mouvement interne des roulements. Ils mesurent les fréquences dans un intervalle de 1 à 5.000 Hz et sont généralement utilisés pour mesurer les paliers lisses.
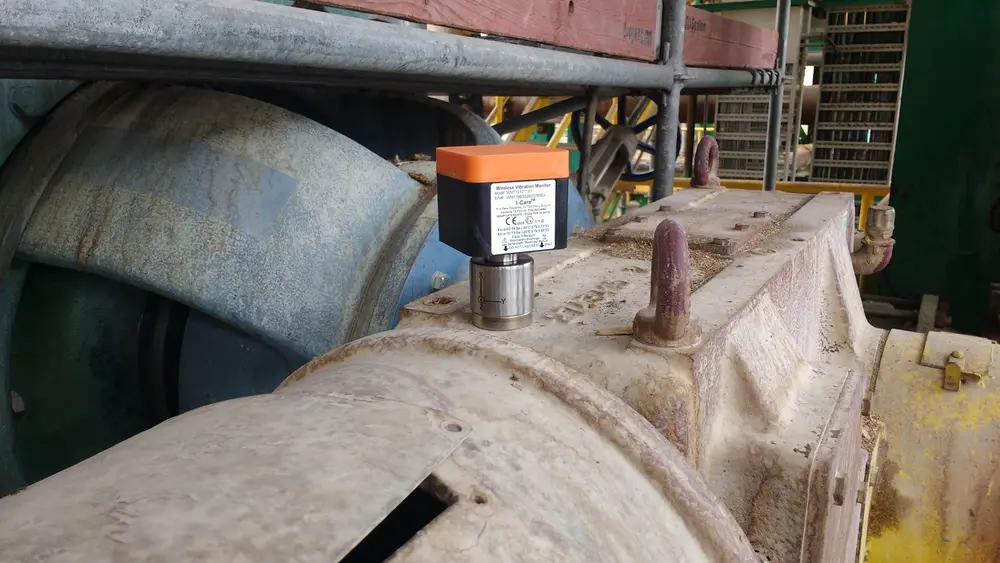
Développements
Les développements importants dans le domaine des capteurs résident dans les versions sans fil qui transmettent leurs données via, par exemple, Bluetooth. Il est possible de choisir des capteurs qui transmettent toutes leurs données, mais il existe également des capteurs intelligents. Ceux-ci ne transmettent une mesure à un point central (souvent le cloud) que lorsqu'une certaine valeur – prédéfinie – est dépassée. Si la valeur se situe dans les limites normales, elle est rejetée. De cette manière, seules les données relatives aux défaillances sont collectées.
La pratique montre que cette approche permet d'économiser beaucoup d'énergie et d'éviter de surcharger les systèmes qui collectent et analysent les données. L'inconvénient de cette approche est qu'il n'est pas possible d'analyser les tendances, car une grande partie des données est manquante.
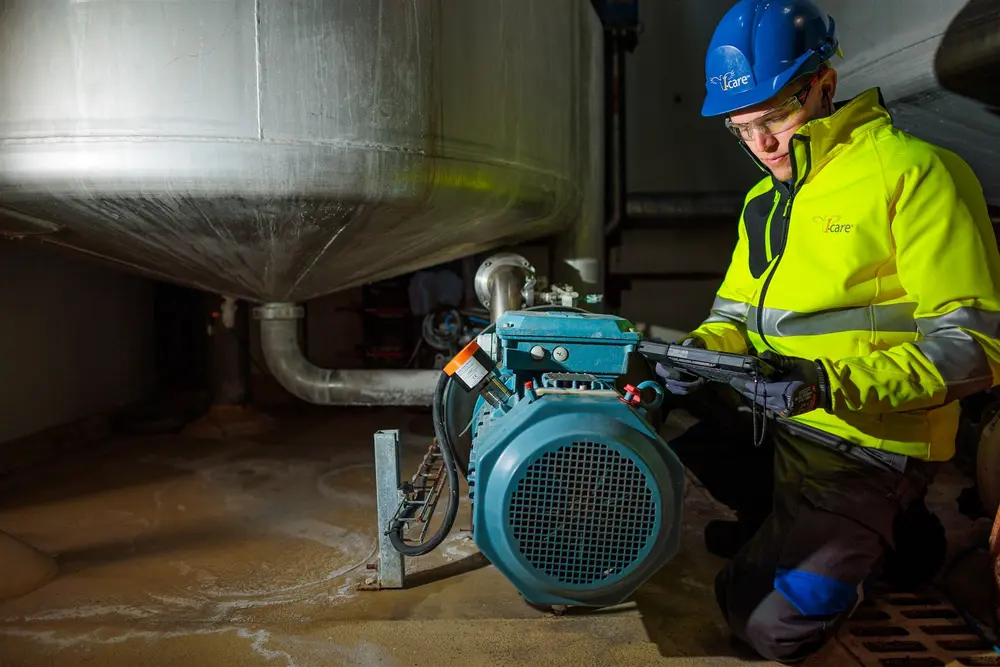
analyse
Mesurer les vibrations et collecter toutes les mesures est une chose. Les analyser est une profession à part entière pour laquelle – à juste titre – on fait souvent appel à un spécialiste. Les mesures typiques pour les données de tendance sont les mesures entre 10 et 1.000 Hz, où chaque composant ou combinaison de composants a ses propres caractéristiques. En enregistrant ces caractéristiques dans une mesure dite de base, il est relativement facile d'identifier les écarts éventuels. Toutefois, cela ne permet pas toujours de déterminer la cause des vibrations déviantes.
La littérature fournit des mesures de référence variables d'un grand nombre d'éléments dans différentes conditions. Même dans ce cas, la tâche n'est pas aisée, car les données mesurées dans la pratique ne sont pas totalement propres, mais contiennent une quantité plus ou moins importante de bruit. Par exemple, en raison du bruit ambiant, des vibrations d'autres composants, des interférences, etc.
Là encore, il faut un expert capable de démêler les différentes influences et de faire une déclaration fiable sur la cause sous-jacente que les analyses de vibrations pourraient indiquer. Par exemple, un problème de lubrification, des erreurs d'alignement ou l'usure d'un composant.
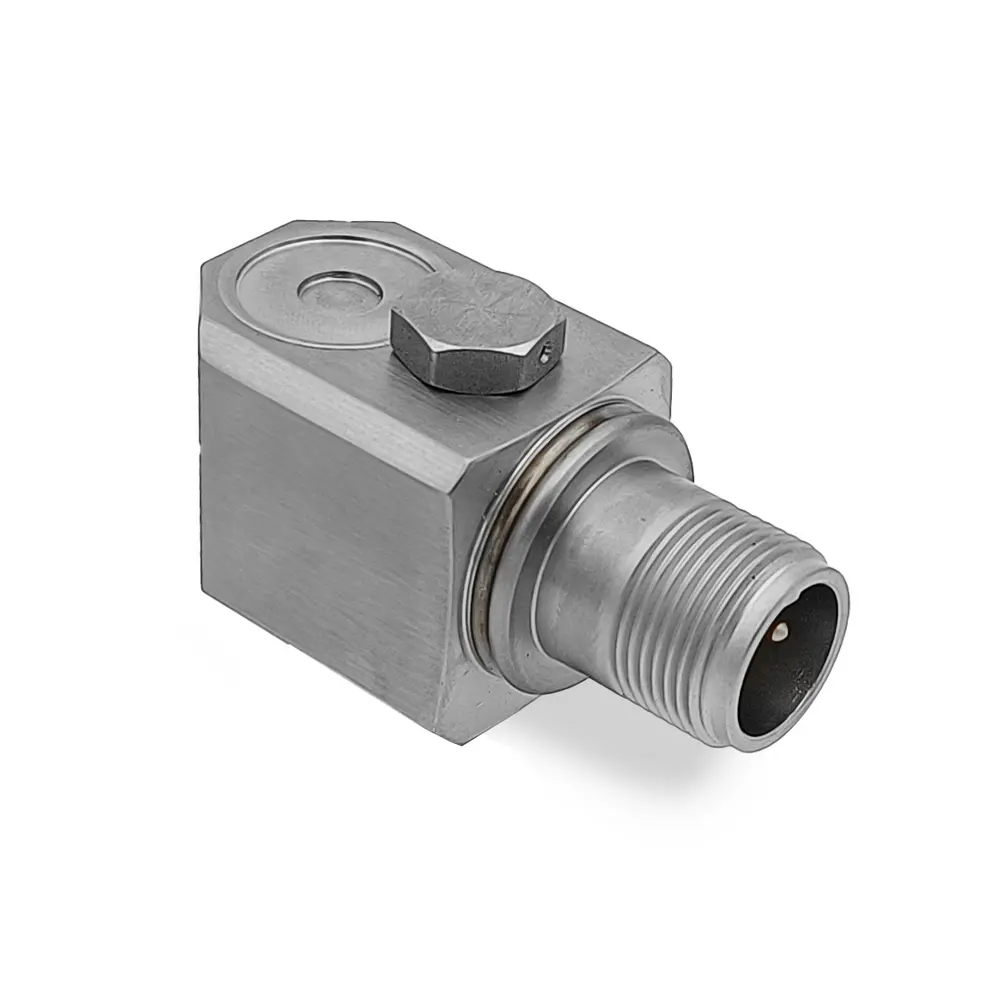
Incidentelles ou continues?
Une analyse porte toujours sur le spectre et la tendance. Le spectre indique les fréquences présentes et est facile à comparer avec le spectre de la mesure de référence. Cela signifie qu'une mesure de référence et une mesure unique peuvent déjà fournir beaucoup d'informations.
En effectuant des mesures régulières, il est possible d'identifier d'éventuelles tendances. Plus le nombre de données collectées est important, plus les petits changements peuvent être identifiés rapidement. Dans les installations stables, les mesures sont normalement effectuées tous les 1 à 3 mois, ce qui donne en pratique un bon rapport entre les coûts et les résultats des mesures.
L'IA permet d'établir des liens entre les paramètres du processus et les données vibratoires
Les mesures en continu – c'est-à-dire non pas une fois tous les trois mois, mais en permanence – et la surveillance en ligne sont principalement effectuées sur les machines critiques. Cela implique des mesures continues et la collecte des données dans un environnement cloud, par exemple. La personne responsable peut se connecter à cet environnement et consulter les données. Si certaines limites sont dépassées, une alarme est déclenchée.
Si la mesure continue envoie beaucoup plus que les données brutes (divers paramètres et/ou des spectres complets), cela devient un outil très puissant, mais aussi coûteux. La question est alors de savoir si les coûts de mesure et de surveillance l'emportent sur la réduction des coûts de maintenance et la plus grande disponibilité de la machine. L'investissement peut être réduit en confiant les mesures périodiques à un tiers et c'est aussi une bonne solution pour voir si elle s'intègre dans les opérations d'une entreprise et dans sa stratégie de maintenance globale.
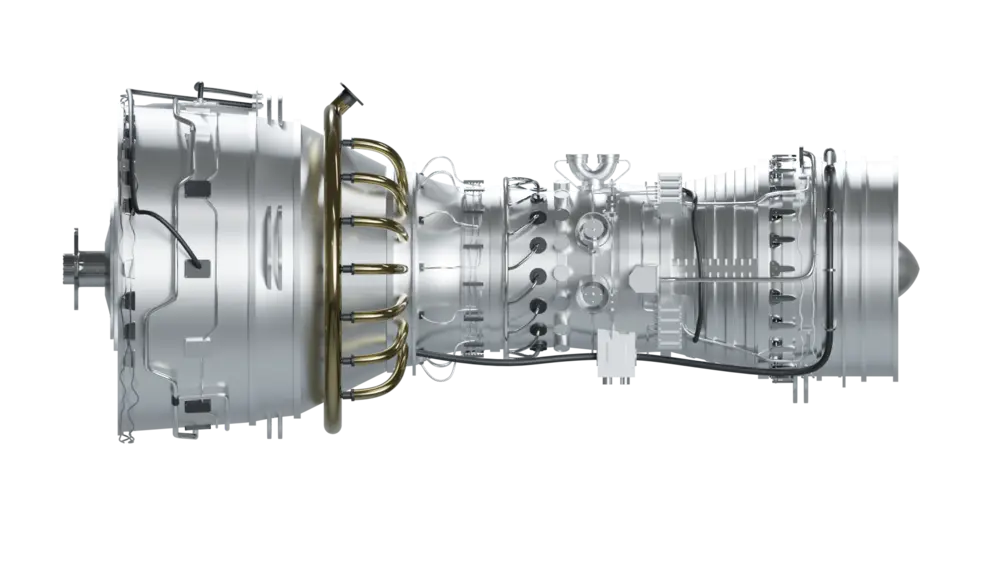
trouver La meilleure solution
La meilleure solution pour une entreprise ou une machine dépend de nombreux facteurs. La criticité des machines et des installations, le budget disponible et la volonté d'investir dans le matériel, les logiciels et le savoir-faire nécessaires.
La criticité des machines dépend de plusieurs facteurs. Un composant peut être critique parce que sa fonction ne peut pas être reprise par un autre composant (redondant) en cas de défaillance. Si ce composant tombe en panne, c'est toute la machine qui s'arrête. Critique peut également signifier que de nombreux problèmes surviennent, avec les coûts associés (réclamations), lorsqu'une machine ne peut pas fonctionner 24 heures sur 24, 7 jours sur 7, ou lorsqu'une machine en panne met en danger les personnes ou l'environnement.
Dans tous les cas, on commencera toujours par ce qu'il y a de plus simple. Prenez des mesures sur un nombre limité de points et démontrez que c'est utile. Cela va encourager les travailleurs ou un département spécifique à aller dans votre sens, ce qui constitue une bonne base pour une éventuelle expansion. À l'avenir, cela impliquera de plus en plus l'intelligence artificielle qui, entre autres, permettra de faire plus facilement le lien entre les paramètres du processus et les données vibratoires.
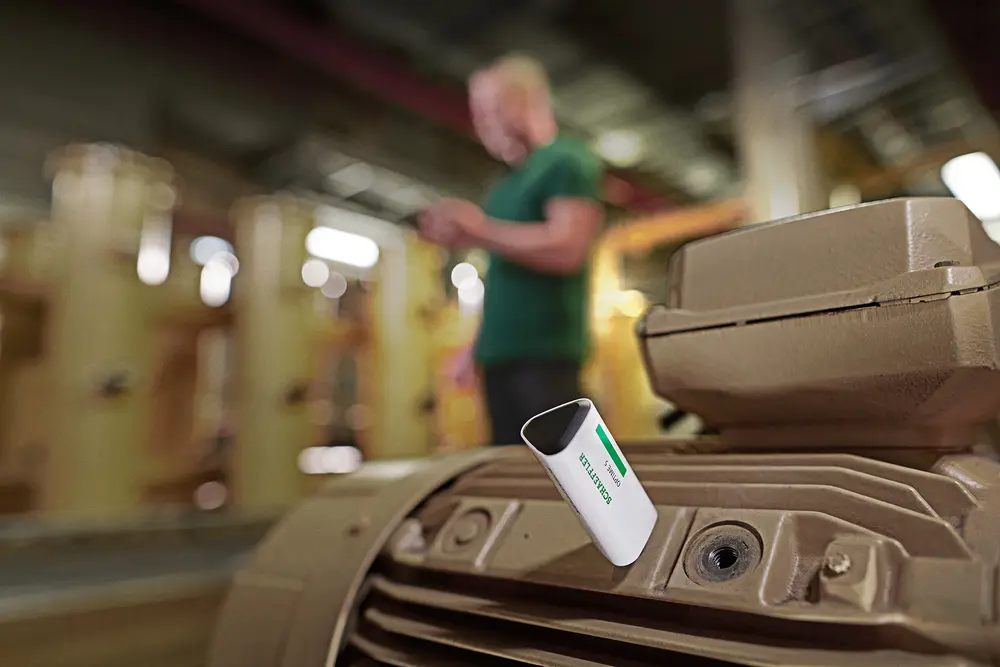
En résumé
La mesure des vibrations a été acceptée par la majeure partie de l'industrie comme stratégie de maintenance conditionnelle et prédictive. Ces techniques sont de plus en plus utilisées, notamment parce que les prix des capteurs et des logiciels baissent et qu'il est de plus en plus facile de disposer d'une grande capacité de stockage dans le cloud et d'une puissance de calcul élevée.
Cependant, la maintenance prédictive basée sur les mesures de vibrations nécessite des connaissances et une expertise suffisantes pour acheter le matériel et les logiciels adéquats et interpréter les données. Il est possible que les développements dans le domaine de l'IA et des logiciels d'analyse simplifient encore cette tâche à l'avenir, rendant possible une maintenance plus interne.
En collaboration avec ACD, Bemas, I-care, Istec, Schaeffler et SKF