Trillingsmetingen voor predictief onderhoud
AI legt steeds beter verband tussen procesparameters en trillingdata
Eén van de meest gebruikte methodes om de conditie van machines te monitoren, is het meten van trillingen van roterende delen. Al meer dan tachtig jaar geleden werd hierover reeds geschreven maar waren de mogelijkheden nog beperkt. Door ontwikkelingen op het vlak van sensoren, communicatie, analysesoftware, rekenkracht en AI vormen trillingsmetingen en -analyses inmiddels een betrouwbare manier om onderhoud op basis van conditie uit te voeren en zelfs te voorspellen.
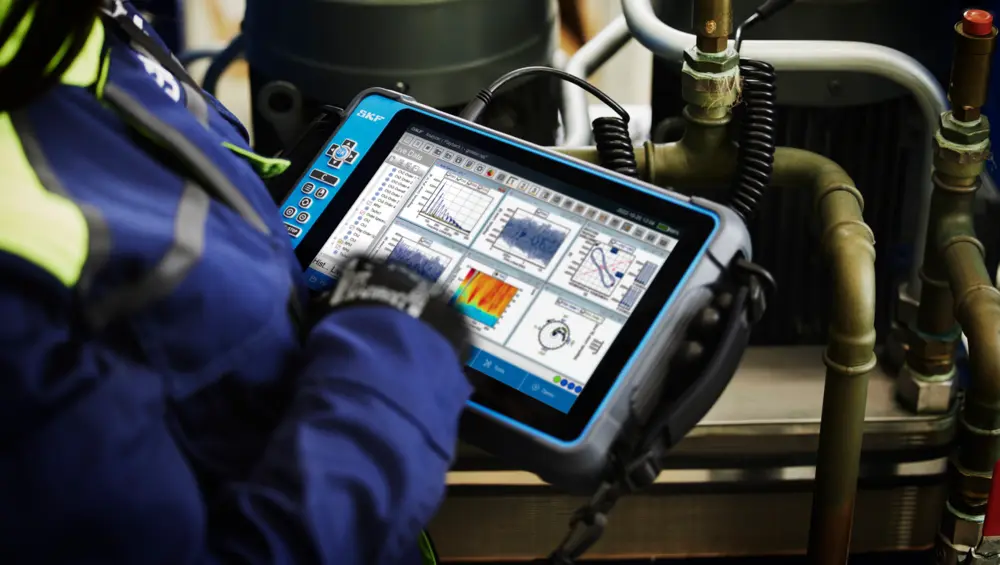
Trillingsanalyse?
Trillingen in machines zijn vaak een betrouwbare indicatie voor problemen zoals uitlijnfouten, onbalans en slijtage. Hierdoor nemen het geluidsniveau en het energieverbruik toe en de productiesnelheid en kwaliteit van de producten af. In het slechtste geval valt de machine volledig uit of wordt er schade berokkend aan mens, milieu of de machine zelf. Met alle kosten en leed van dien.
Anderzijds vormen dezelfde trillingen bij uitstek een waardevolle input voor het bepalen van de conditie van een machine of machineonderdeel. Sterker nog: het zijn trillingen die als eerste signaal optreden wanneer een storing zich ontwikkelt.
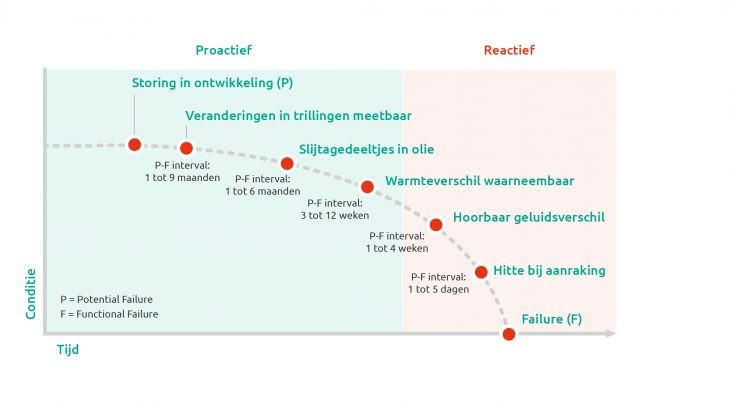
Een en ander is te zien in figuur 1 waar links de conditie van een machine op de verticale as is uitgezet en op de horizontale as de tijd. In het groene deel functioneert de machine goed en is geen onderhoud nodig. Wanneer zich een storing ontwikkelt (eerste rode bolletje), zal er eerst nog praktisch niets te merken zijn aan de machine. Bovendien bedraagt de tijdspanne dat de storing daadwerkelijk zal leiden tot een functionele fout 1 tot 9 maanden.
Naarmate de tijd verstrijkt en de storing zich verder ontwikkelt, zullen er steeds meer tekenen komen die duiden op een aankomende functionele fout. Zoals de grafiek laat zien is een van de eerste tekenen het veranderen van het trillingspatroon.
In een nog later stadium zullen (bij een hydraulische installatie) bijvoorbeeld slijtagedeeltjes in de olie zijn te vinden en zal de machine steeds meer warmte en geluid gaan ontwikkelen tot uiteindelijk de functionele fout optreedt. Dit verloop geldt uiteraard alleen wanneer er niet wordt ingegrepen.
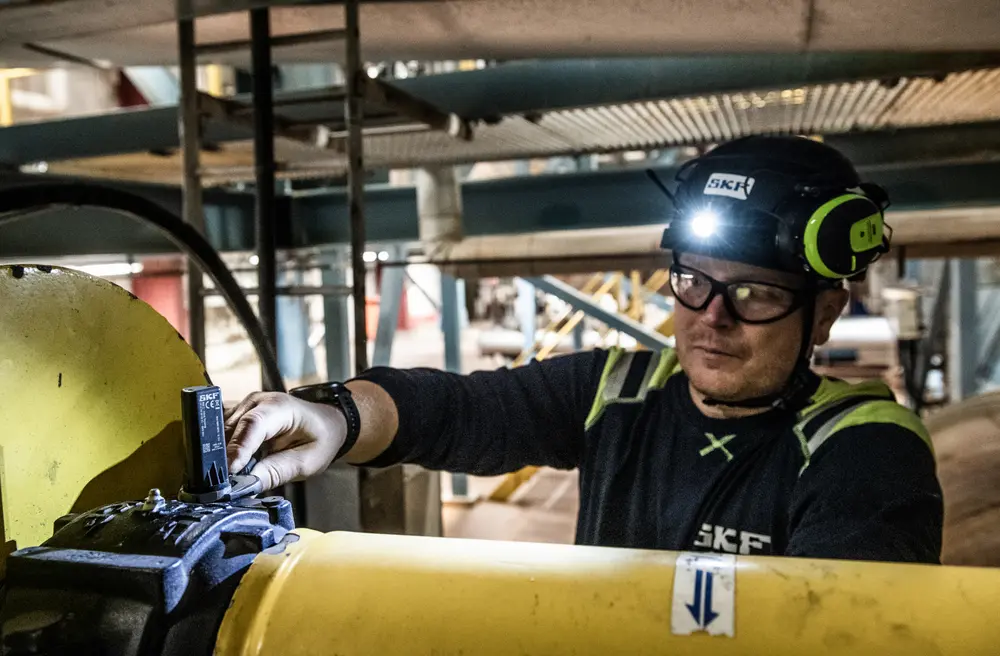
Oorzaken en gevolgen trillingen
Oorzaken
Bovenstaande grafiek geeft direct aan waarom het meten van trillingen zo effectief is wanneer het om voorspellend en condition based onderhoud gaat: Trillingen zijn eenvoudig de eerste tekenen van een aankomende storing. Door trillingen te monitoren en veranderingen te detecteren, is er in de meeste gevallen nog alle tijd om de oorzaak te achterhalen en deze op te lossen of in elk geval tijdig onderhoud uit te voeren. Dus nog voordat het energieverbruik en het geluidsniveau merkbaar stijgen of een achteruitgang van de kwaliteit van producten merkbaar wordt.
De oorzaken van storingen die leiden tot een verandering van het trillingspatroon zijn meestal te vinden in uitlijnfouten, onbalans (statisch of dynamisch), resonantie, losse onderdelen, corrosie, lagerschade en slijtage. Echte uitlijnfouten ontstaan vooral bij de installatie van nieuwe machines of door calamiteiten.
Het interpreteren van trillingsmetingen moet altijd door een expert gebeuren
Overige problemen zijn vaak het gevolg van slijtage die uiteindelijk weer vaak in verband is te brengen met gebrekkig onderhoud. Zo hangt een belangrijk deel van lagerfalen samen met niet of onjuist smeren. Andersom geldt dat goed (smeertechnisch) onderhoud het ontstaan van trillingen en uiteindelijk storingen tegengaat.
Gevolgen
De gevolgen van trillingen zijn divers en al kort in het begin van dit artikel genoemd. Het gevolg dat de eerste aandacht zou moeten hebben zijn de veiligheidsissues. Zo kunnen sterke trillingen leiden tot menselijk letsel, schade aan de machine of het milieu.
De schade aan de machine zelf kan niet alleen leiden tot ongeplande stilstand of zelfs volledige uitval, maar ook tot een lagere beschikbaarheid, een slechtere kwaliteit van de producten of meer uitval. In praktisch alle gevallen zullen problemen leiden tot hogere kosten door benodigde onderhoudsuren, het vervangen van onderdelen of gederfde productie door ongeplande stilstand.
Sensoren
Nu bekend is dat trillingen een belangrijke parameter vormen voor het bepalen van de conditie van een machine, is het een logische volgende stap om deze trillingen daadwerkelijk te gaan meten en te monitoren. Hiervoor zijn diverse sensoren en systemen in de markt beschikbaar. Wie start met trillingsmetingen in het kader van condition based onderhoud of voorspellend onderhoud, doet er verstandig aan zich te laten adviseren met betrekking tot de juiste sensor. Niet iedere sensor is geschikt voor elke machine, alle onderdelen of iedere omgeving.
Gangbare sensoren in het kader van trillingsmetingen zijn proximity (verplaatsings)sensoren, velocity (snelheids)sensoren en accelerometers (versnellingssensoren). De versnellingssensoren worden het meest toegepast en zijn beschikbaar in een piëzoelektrische en MEMS (micro-electromechanisch systeem) uitvoering. De eerste is een betrouwbare en veelzijdige variant voor het meten van frequenties en amplitudes. Een MEMS-sensor heeft een lagere nauwkeurigheid op frequentie en amplitude maar kan wel statische en dynamische versnellingen meten bij een lager energieverbruik.
Snelheidssensoren meten trillingen in een frequentiebereik van 1-1.000 Hz en zijn vooral geschikt voor het meten van trillingen in rotating equipment zoals ventilatoren, lagers en pompen. Deze sensoren zijn minder gevoelig voor trillingen met een hoge frequentie dan versnellingssensoren en hiermee minder gevoelig voor overbelasting.
Verplaatsingssensoren – ook bekend als contactloze naderingsensoren – worden gebruikt voor het meten van de aspositie of -beweging zonder fysiek contact te maken om zo de interne beweging van lagers te bepalen. Ze meten frequenties in een interval van 1-5.000 Hz en worden typisch gebruikt voor het meten aan glijlagers.
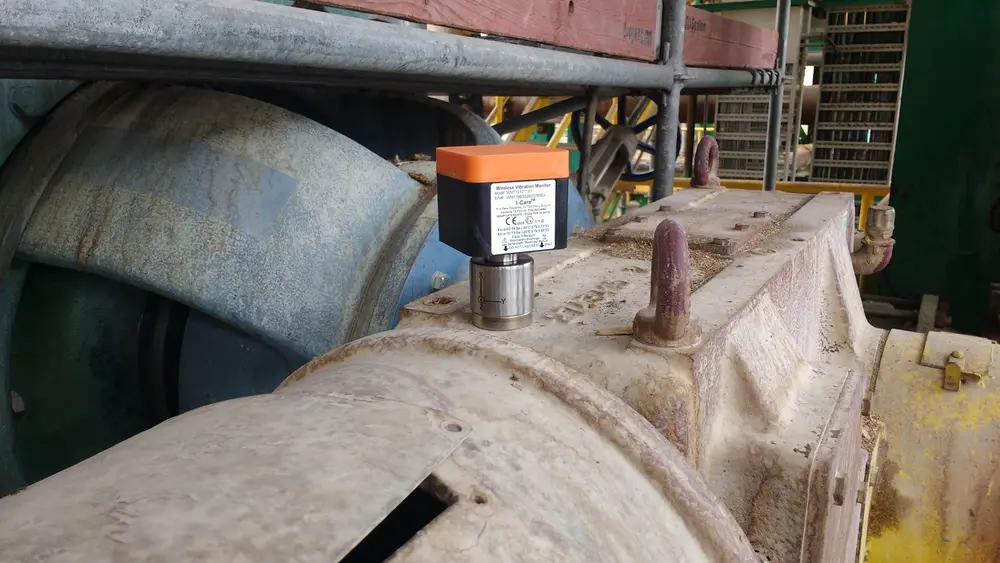
Ontwikkelingen
Belangrijke ontwikkelingen op het gebied van sensoren liggen in de draadloze uitvoeringen die hun gegevens via bijvoorbeeld bluetooth overdragen. Hierbij is te kiezen voor sensoren die al hun data doorsturen maar er zijn ook intelligente sensoren. Deze sturen een meting pas door naar een centraal punt (vaak de cloud) wanneer een bepaalde – vooraf ingestelde – waarde wordt overschreden. Is de waarde binnen de 'normale' grenzen, dan wordt hij weggegooid. Op deze manier worden uitsluitend faaldata verzameld.
De praktijk leert dat deze aanpak véél energie bespaart en overbelasting van systemen die data verzamelen en analyseren voorkomt. Een nadeel van de aanpak is dat er geen trendanalyse kan plaatsvinden omdat een groot deel van de data zal ontbreken.
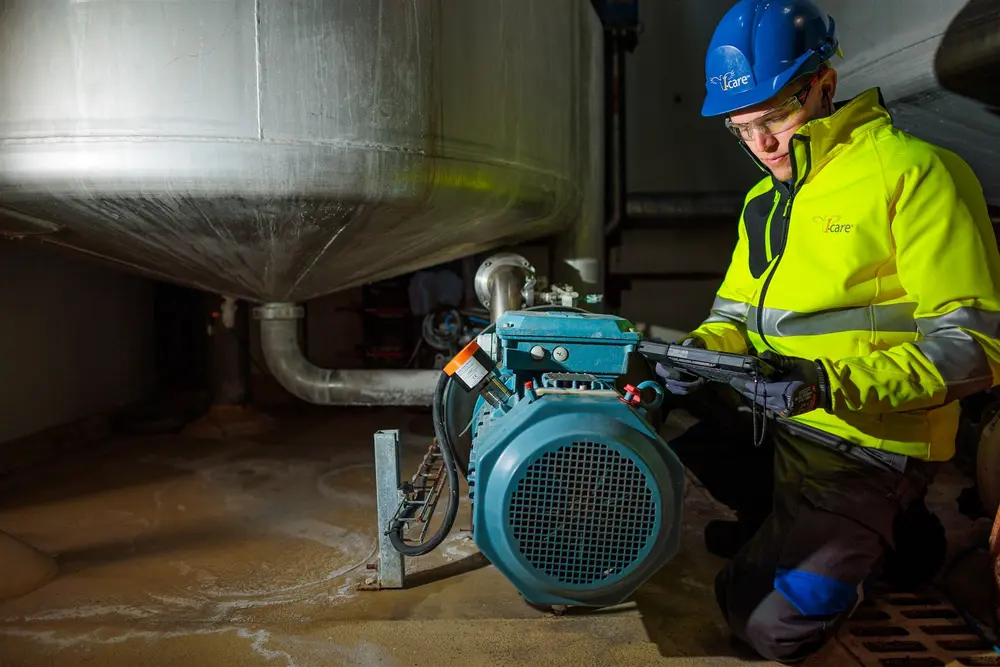
Analyse
Het meten van trillingen en het verzamelen van alle metingen is één. Het analyseren ervan is een vak apart waarvoor – terecht – in veel gevallen een specialist in de arm wordt genomen. Typische metingen voor trenddata zijn metingen tussen de 10-1.000 Hz waarbij iedere component of samenstel van componenten hun eigen karakteristieken hebben. Door deze vast te leggen in een zogenaamde nulmeting, zijn eventuele afwijkingen daarna relatief eenvoudig vast te stellen. Daarmee is echter nog niet altijd de oorzaak van afwijkende trillingen bekend.
De literatuur geeft uiteenlopende referentiemetingen van een groot aantal elementen onder verschillende omstandigheden. Dan nog is het niet eenvoudig omdat gemeten data in de praktijk niet helemaal 'schoon' zijn maar een kleinere of grotere 'ruis' bevatten. Bijvoorbeeld door omgevingsgeluiden, trillingen van andere componenten, interferentie enzovoort.
Ook hier is dan een expert nodig die de diverse invloeden kan ontrafelen en een betrouwbare uitspraak kan doen over de achterliggende oorzaak die de trillingsanalyses mogelijk aangeeft. Bijvoorbeeld een smeerprobleem, uitlijnfouten of slijtage aan componenten.
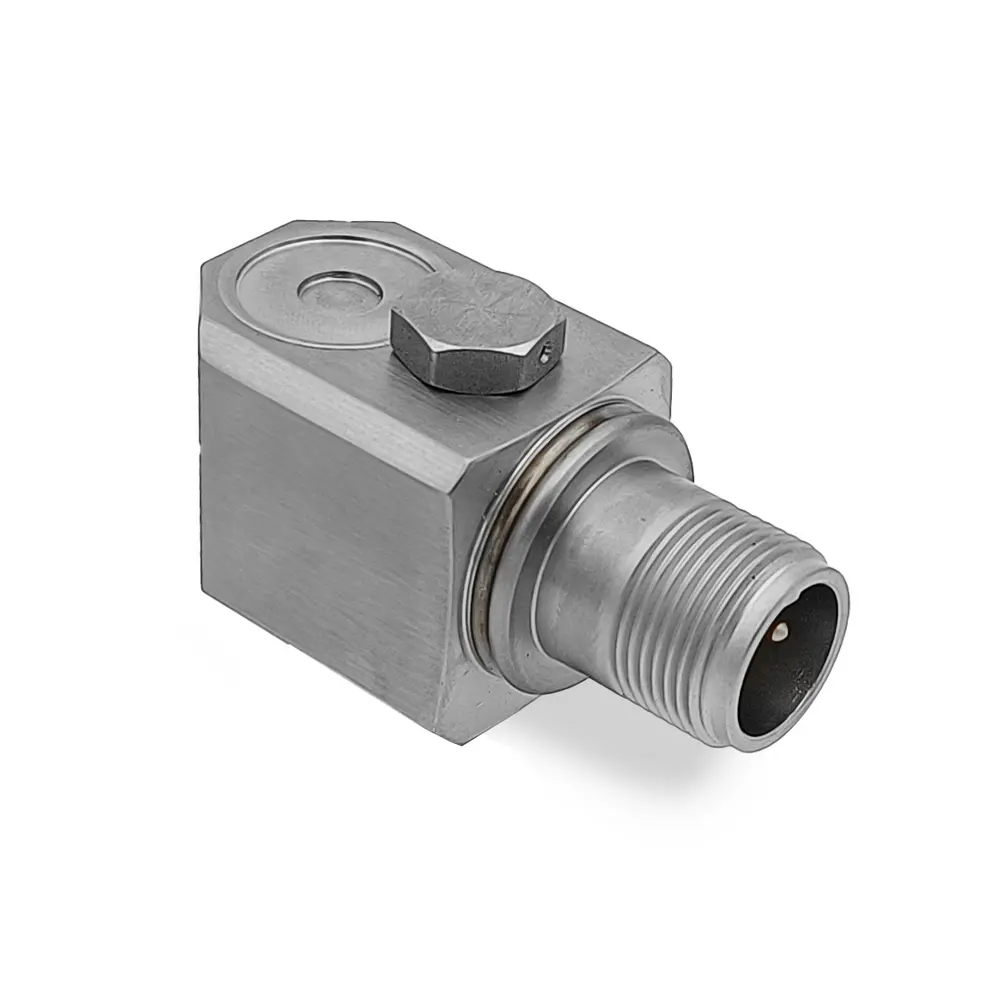
Incidenteel of continu?
Bij een analyse wordt steeds gekeken naar zowel het spectrum als de trend. Het spectrum geeft aan welke frequenties er aanwezig zijn en is eenvoudig te vergelijken met het spectrum uit de nulmeting. Dit betekent dat één nulmeting en vervolgens een losse meting al veel informatie kunnen opleveren.
Door regelmatig metingen te doen, zijn vervolgens eventuele trends vast te stellen. Daarbij geldt: hoe meer data wordt verzameld, hoe sneller kleine wijzigingen zijn vast te stellen. Bij stabiel draaiende installaties worden er normaal elke 1 tot 3 maanden metingen uitgevoerd wat in de praktijk een goede verhouding oplevert tussen de kosten en hetgeen de metingen opleveren.
AI ondersteunt het leggen van verbanden tussen procesparameters en trillingsdata
Continu meten – dus niet één keer in de drie maanden maar voortdurend – en online monitoren gebeurt veelal bij kritische machines. Hierbij wordt continu gemeten en de data verzameld in bijvoorbeeld een cloudomgeving. De betreffende verantwoordelijke kan inloggen in deze omgeving en de data bekijken. Bij het overschrijden van bepaalde grenzen wordt een alarm gegeven.
Wanneer de continumeting veel meer doorstuurt dan alleen de ruwe data (verschillende parameters en/of volledige spectra), wordt dit een zeer krachtige tool waaraan echter ook een kostenplaatje hangt. De vraag is dan of de kosten voor meten en monitoren opwegen tegen de verlaging van de onderhoudskosten en de hogere beschikbaarheid van de machine. Investeringen zijn mogelijk te verlagen door periodieke metingen uit te besteden aan een derde partij en het is ook een goede oplossing om te kijken of het past binnen de bedrijfsvoering en algehele onderhoudsstrategie van een bedrijf.
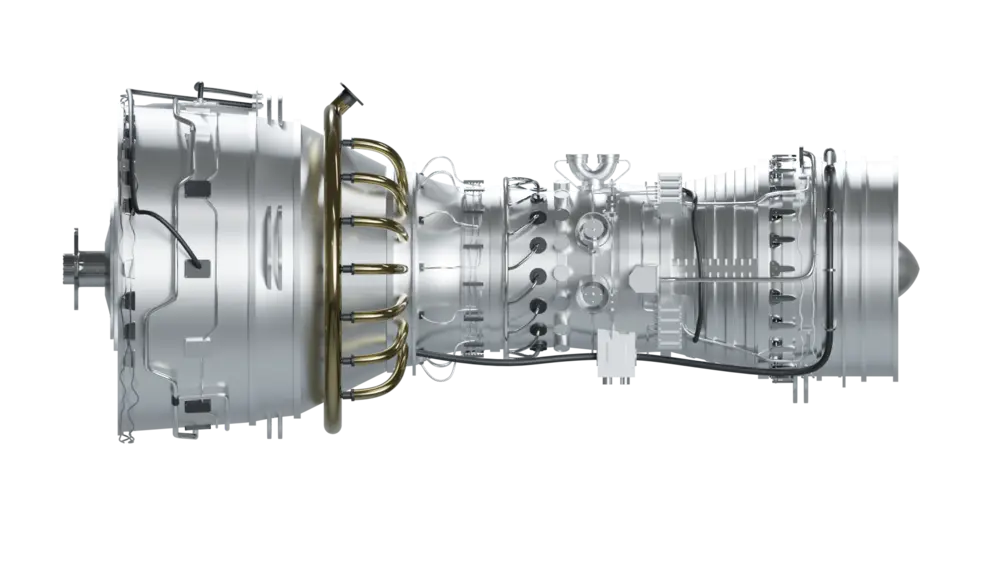
Beste oplossing
Wat uiteindelijk de beste oplossing is voor een bedrijf of machine hangt af van vele factoren. De kriticiteit van machines en installaties, het beschikbare budget en de bereidheid om te investeren in de benodigde hard- en software én de kennis.
Daarbij is de kriticiteit van machines afhankelijk van verschillende factoren. Een onderdeel kan kritisch zijn omdat zijn functie bij uitvallen niet kan worden overgenomen door een ander (redundant) onderdeel. Bij het uitvallen van deze ene component zal dan ook de volledige machine komen stil te liggen. Kritisch kan ook betekenen dat er veel problemen ontstaan met bijbehorende kosten (claims) wanneer een machine niet 24/7 kan draaien of wanneer een machine in storing gevaar oplevert voor mens of milieu.
In alle gevallen is het verstandig om met het spreekwoordelijke laaghangende fruit te beginnen. Meet op een beperkt aantal punten en toon aan dat het nut heeft. Hiermee wordt draagvlak gecreëerd in een bedrijf of een specifieke afdeling wat een goede basis biedt voor eventuele uitbreiding. In de toekomst zal daar steeds vaker artificial intelligence bij aan te pas komen waarmee onder meer eenvoudiger het verband is te leggen tussen procesparameters en trillingsdata.
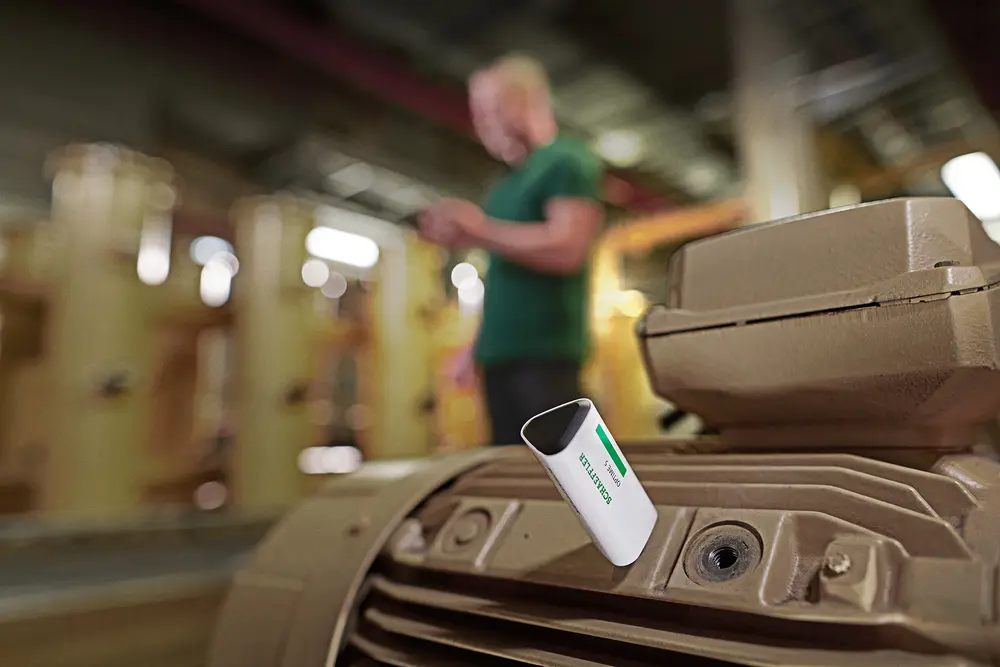
Samenvattend
Trillingsmetingen zijn door het grootste deel van de industrie geaccepteerd als strategie voor condition based en voorspellend onderhoud. De technieken worden steeds vaker en breder toegepast omdat onder meer de prijzen van de sensoren en software dalen en het eenvoudiger wordt om te beschikken over een grote opslag in een cloudomgeving en een hoge rekenkracht.
Voorspellend onderhoud op basis van trillingsmetingen vraagt echter wel voldoende kennis en expertise om de juiste hard- en software aan te schaffen en de data te interpreteren. Mogelijk dat ontwikkelingen op het vlak van AI en analysesoftware dit in de toekomst nog zullen vereenvoudigen en er meer in eigen beheer mogelijk wordt.
Met medewerking van ACD, Bemas, I-care, Istec, Schaeffler en SKF