Une production d'engrenages de qualité grâce à la numérisation
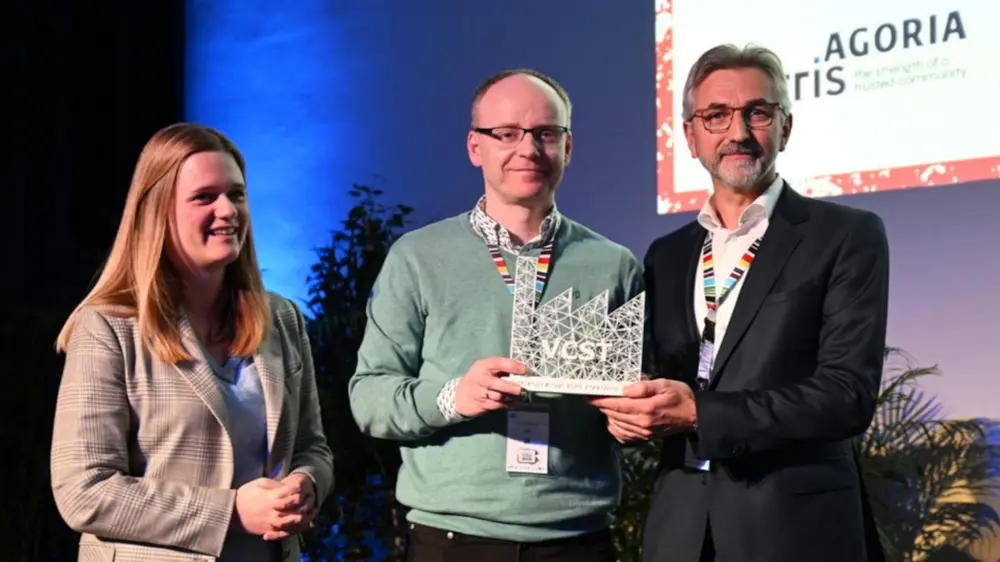
Au début de l'année, VCST a remporté le titre très convoité de Factory of the Future. Il s'agit d'une étape importante pour cette entreprise, qui opère dans le secteur exigeant et en évolution rapide de l'automobile.
Vehicle Components, Systems & Transmissions
Autrefois, VCST signifiait 'Volvo Cars Sint-Truiden'. Aujourd'hui, le lien avec Volvo a disparu et VCST est devenu 'Vehicle Components, Systems & Transmissions'. Entre autres choses, l'entreprise développe et produit des engrenages performants sur mesure pour différents acteurs de l'industrie automobile.
VCST opère sous les ailes du groupe BMT, qui comprend également des entreprises actives dans le développement de systèmes pour l'aérospatiale, le secteur du verre et l'industrie de l'entraînement, entre autres. Le fait que VCST opère sous les ailes de BMT est un point important car l'entreprise fait souvent office d'usine pilote pour le groupe. Les innovations sont d'abord implémentées chez VCST, avant d'être introduites chez les autres membres du groupe.
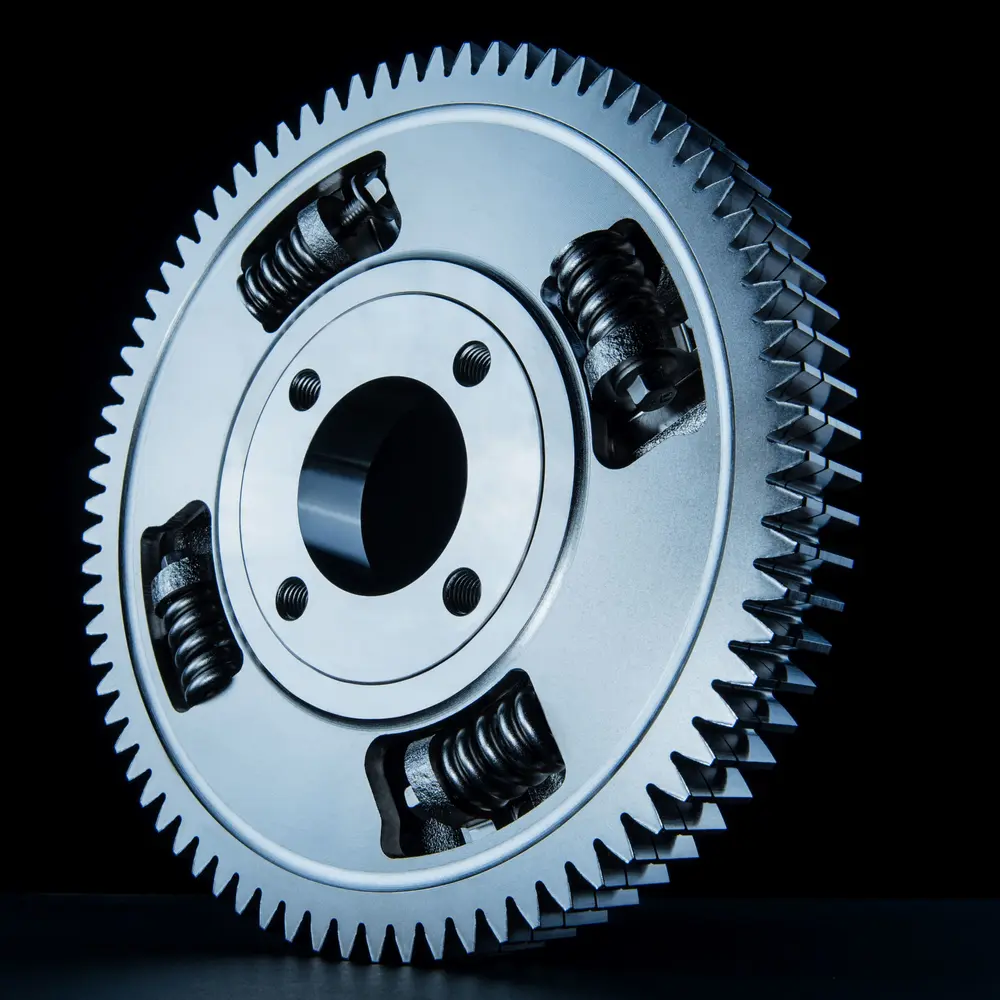
Engrenages haute performance
Le vice-président Eddy Van Steyvoort nous parle des activités et des clients de VCST: "Nous développons et produisons des engrenages pour les fabricants de composants. Ces engrenages finissent par être intégrés dans les moteurs et les boîtes de vitesses des véhicules utilitaires légers et des poids lourds. Il s'agit toujours d'un travail sur mesure, car chaque client a ses propres spécifications pour le moteur qu'il construit. Cela signifie que la R&D et la production de haute qualité sont extrêmement importantes pour nous. C'est pourquoi nous sommes constamment à la recherche d'innovations. En ce sens, le fait de recevoir le titre d'usine du futur est une excellente indication que nous sommes sur la bonne voie."
De solides défis dans le secteur
"Le secteur automobile est confronté à des défis très divers et spécifiques. Certains d'entre eux sont là depuis toujours, comme les normes de qualité élevées, les délais de commercialisation rapides et l'approche très axée sur les prix. Au fil des ans sont venus s'ajouter des exigences telles que la traçabilité et le faible poids. En outre, l'avènement de l'e-mobilité met également l'accent sur la production de bruit, par exemple. Les engrenages utilisés pour les entraînements des véhicules électriques doivent supporter des valeurs de rotation par minute plus élevées."
"Les exigences de qualité plus strictes se reflètent également dans les exigences NVH (Noise, Vibration & Hardness), que nous devons inclure dans le développement et la production de nos composants, mais j'y reviendrai plus tard. En outre, nous adoptons une approche design-for-infinite-life. Cela représente évidemment un certain coût, mais cela nous donne une réputation très solide. En 36 ans, nous n'avons eu que deux 'field issues'. De plus, ici, tout se passe sous le même toit: du développement à la production."
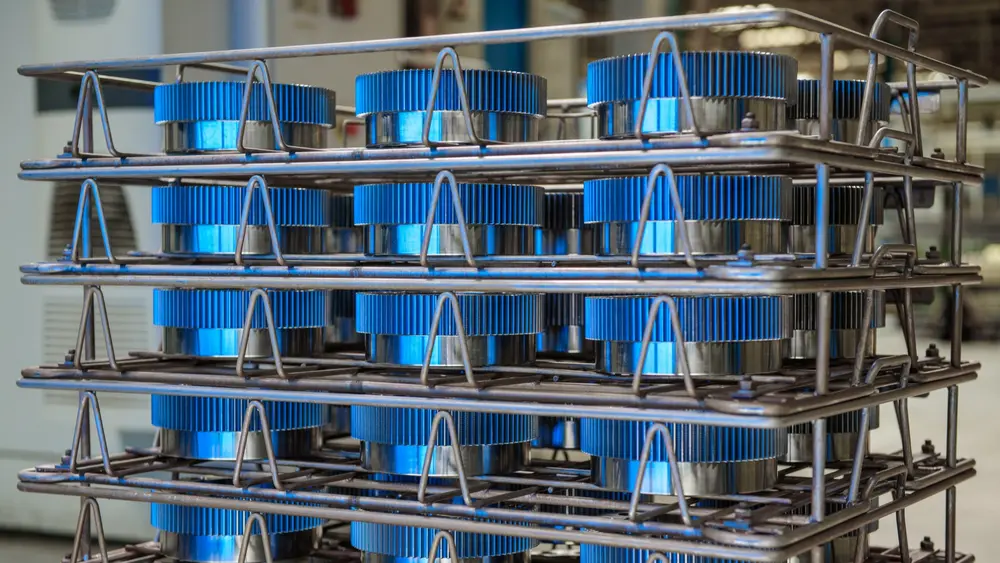
Les données de mesure jouent un rôle central
"La qualité et la fiabilité sont évidemment importantes, mais dans ce secteur en particulier, la stagnation est synonyme de régression. Nous avons ressenti le besoin d'un délai de commercialisation plus court et d'une plus grande flexibilité. Bref, de plus d'efficacité. Nous voulions également créer une grande transparence pour nos clients. Aujourd'hui, on voit apparaître une plus grande ouverture partout dans le processus logistique, les clients pouvant par exemple suivre l'état de leurs commandes en temps réel. Nous voulions qu'il en soit de même pour l'approche de la qualité. Une transparence totale pour les clients en ce qui concerne les données relatives à la qualité: tel était notre objectif."
"D'ailleurs, il n'y a pas que de notre part que cela demande une certaine ouverture. En effet, le feed-back des clients est également très important pour ce type de produits. Par exemple, ils effectuent des tests de fin de ligne sur leurs groupes motopropulseurs. Ces informations sont très précieuses pour nous, car elles nous permettent d'améliorer encore notre système et notre produit. En d'autres termes, c'est une situation où tout le monde est gagnant. La question était de savoir comment implémenter cela au mieux. Nous avons opté pour une vision à long terme; la crise du corona, par exemple, n'a pas eu d'impact sur nos actions."
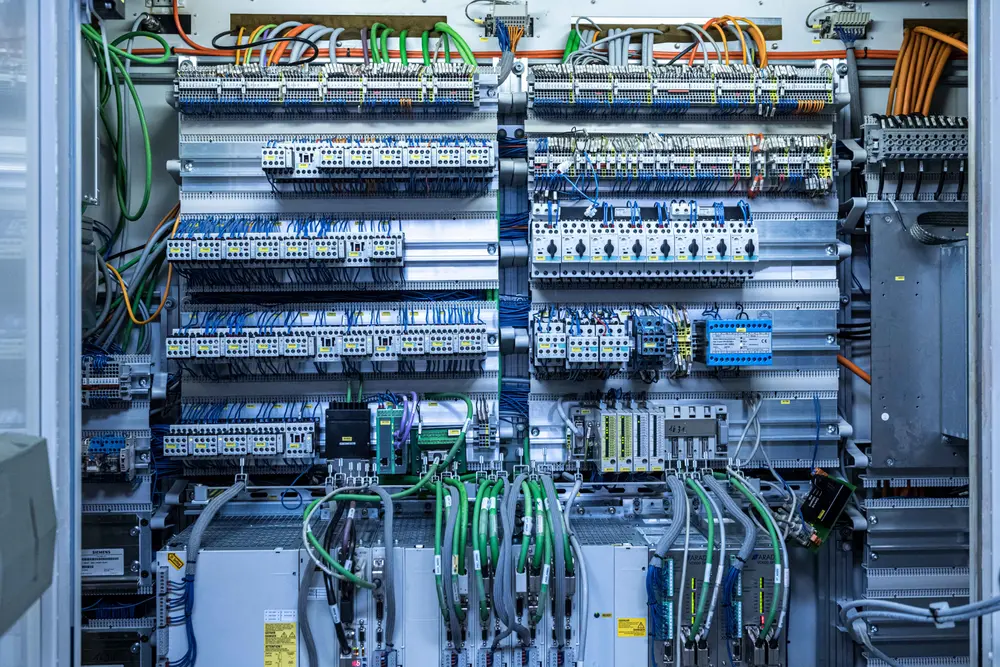
Tim Polleunis, Manager Business Transformation, explique comment cette approche a été mise en œuvre sur le terrain: "Comme nous l'avons dit, éviter les vibrations – et donc le bruit – est l'une des exigences les plus importantes pour les engrenages. Mais la qualité est également un facteur très important de manière générale. Dans l'industrie automobile, les pièces de mauvaise qualité ne sont tout simplement pas envisageables. En cas de réclamation d'un client, une inspection complète peut être demandée. Cela entraîne des temps d'arrêt qui peuvent avoir un impact significatif sur les marges. Sans parler du coût d'un éventuel rappel."
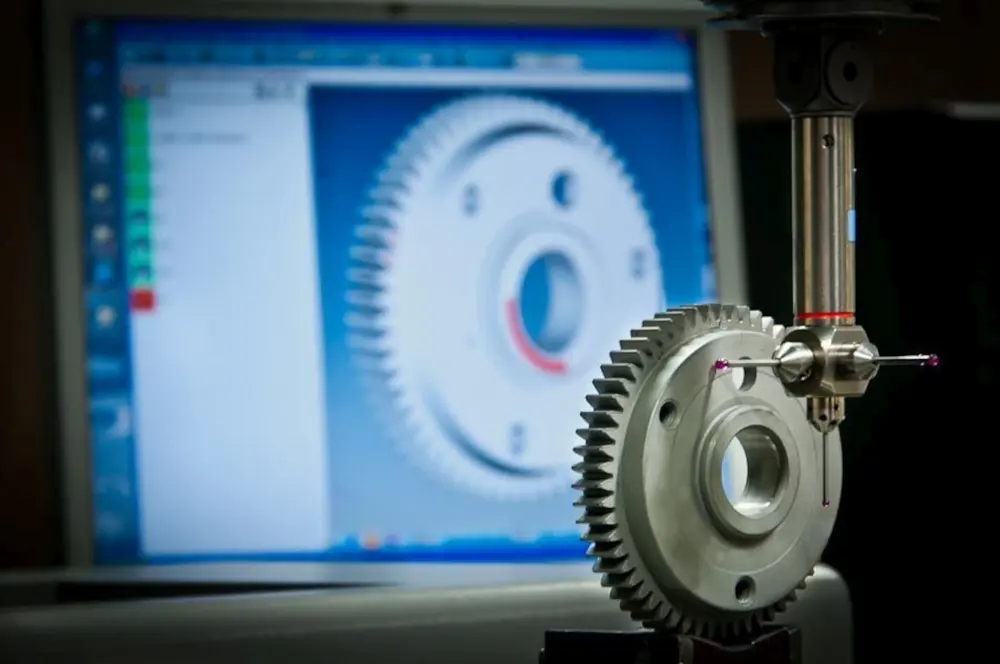
"Notre site de production est déjà hautement automatisé et d'un niveau élevé mais en ce qui concerne la qualité, par exemple, nous travaillions encore principalement avec des processus papier et des systèmes distincts, qui fonctionnaient en silos pour ainsi dire. L'automatisation et la numérisation de ces flux de travail et de ces processus étaient donc des approches évidentes pour accroître l'efficacité, réduire les coûts dans l'atelier et améliorer encore la qualité. Le lien entre la numérisation et la qualité n'est peut-être pas évident à première vue, mais il existe bel et bien: les processus sur papier prennent du temps et créent donc plus de pression. En outre, les processus numériques permettent d'éviter certaines erreurs humaines."
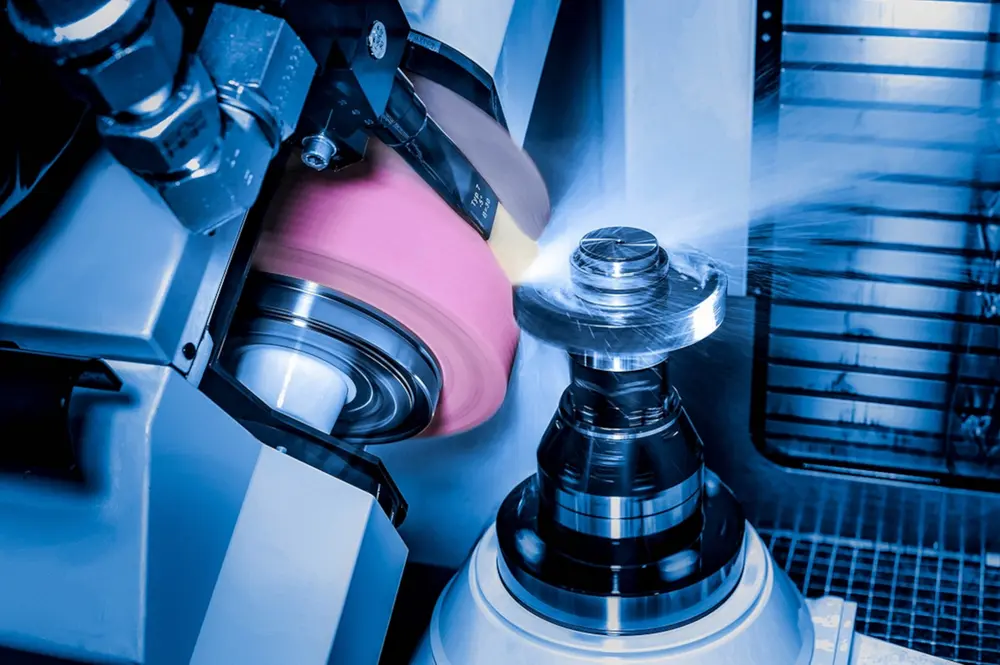
De la preuve de concept à l'implémentation
"En juillet 2018, nous avons commencé à mettre en place une preuve de concept sur une ligne, en optant pour ThingWorx comme plateforme. En avril 2019, le projet a pris de l'ampleur avec l'achat de téléphones portables pour les opérateurs, et un peu plus tard, nous avons également pu connecter nos machines CNC à la plateforme. Ce dernier point nous a permis d'extraire facilement des données de l'automate pour les traiter et les analyser; les informations provenant de la CN (commande numérique) étaient un peu plus complexes, mais nous avons trouvé une solution pour ça avec Siemens."
DEUX TYPES DE BRUIT
Les causes de la production de bruit indésirable peuvent être très diverses. Il existe même de multiples manifestations du bruit. Chez VCST, on se concentre sur deux types de bruits: le 'rattle noise' et le 'whine noise'. Le premier est un bruit de tic-tac répétitif, dû au contact entre deux pièces mobiles d'une boîte de vitesses. Le second, de nature sifflante et continue, se produit autour d'une fréquence particulière. Il est plus difficile à éliminer et il est propre à une pièce, ce qui devient de plus en plus un défi pour les constructeurs automobiles. Avec un moteur à combustion interne traditionnel, la présence d'un 'whine noise' était moins problématique car le niveau de bruit inhérent à ce type d'entraînement était élevé. Avec le passage aux moteurs électriques, le 'whine noise' ne gagne pas en intensité mais il devient plus audible en raison du fonctionnement plus silencieux du moteur.
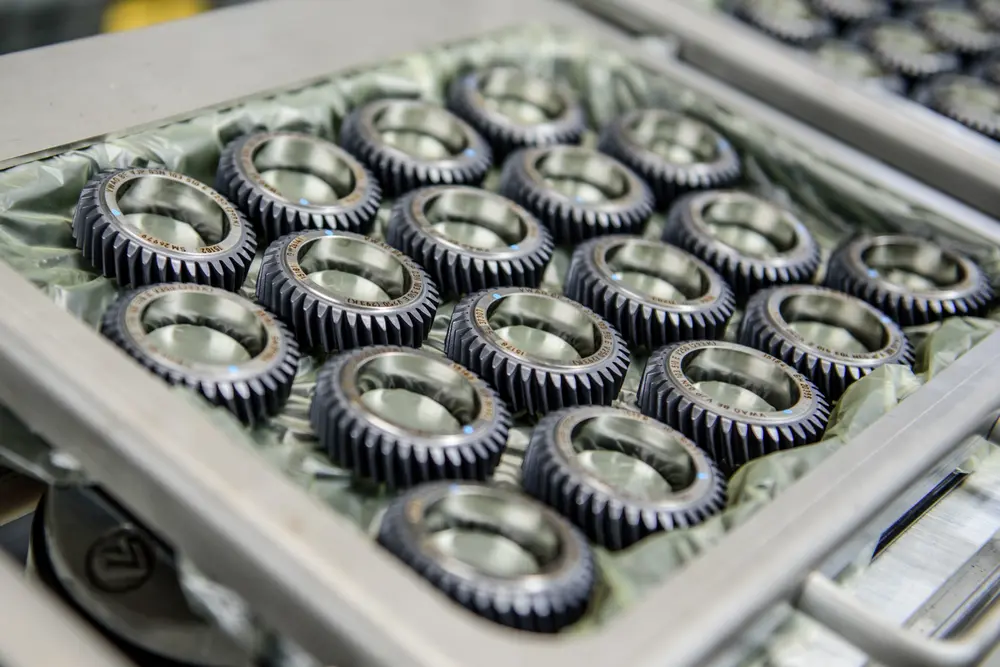
Mesures de qualité NVH
"Si nous prenons l'exemple des mesures NVH importantes, nous voyons quatre facteurs clés dans le processus de production: la machine, les facteurs environnementaux, les pièces proprement dites et l'outillage. Pour la machine, par exemple, il s'agit de rectifier les engrenages sur une Reishauer Argus. Cette machine peut elle-même être équipée de capteurs pour suivre la machine et ses composants. A cela s'ajoute la couche d'informations des automates et de la commande numérique, tandis que les mesures de vibrations peuvent également fournir des données intéressantes."
"Pour les conditions environnementales, nous faisons appel aux opérateurs qui peuvent enregistrer des événements au cours du processus de production. Cela nous permet de vérifier dans quelles conditions une commande a été produite. Les pièces nous fournissent également des informations par le biais de mesures approfondies dans des salles de mesure numériques où sont effectuées et enregistrées toutes les mesures et analyses possibles. Cela se fait avec une fréquence déterminée par pièce, par exemple deux pièces par équipe de 8 heures, selon un schéma défini."
"Cela nous permet de suivre les indicateurs de risque qui font qu'un engrenage fait du bruit. Nous fournissons ces données dans le code matriciel de données (DMC) par engrenage. Nous savons exactement, pour chaque moteur, quelles sont les valeurs des engrenages. Nous garantissons donc à nos clients qu'ils n'auront aucun problème. Et sur base des données de mesure, nous continuons à optimiser nos propres processus à chaque fois."
"Enfin, chaque outil a un numéro de série unique, ce qui nous permet de relier chaque pièce fabriquée à l'outil utilisé."