Un troisième Factory oF the future AWARD pour Continental Mechelen
Les ateliers Continental à Malines comptent parmi les quelques rares entreprises récompensées trois fois d'un titre de Factory of the Future. Le responsable du département Industrial Engineering, Marc Moris, nous a parlé des étapes du développement du site de production pour en faire une usine exemplaire au sein du groupe Continental.
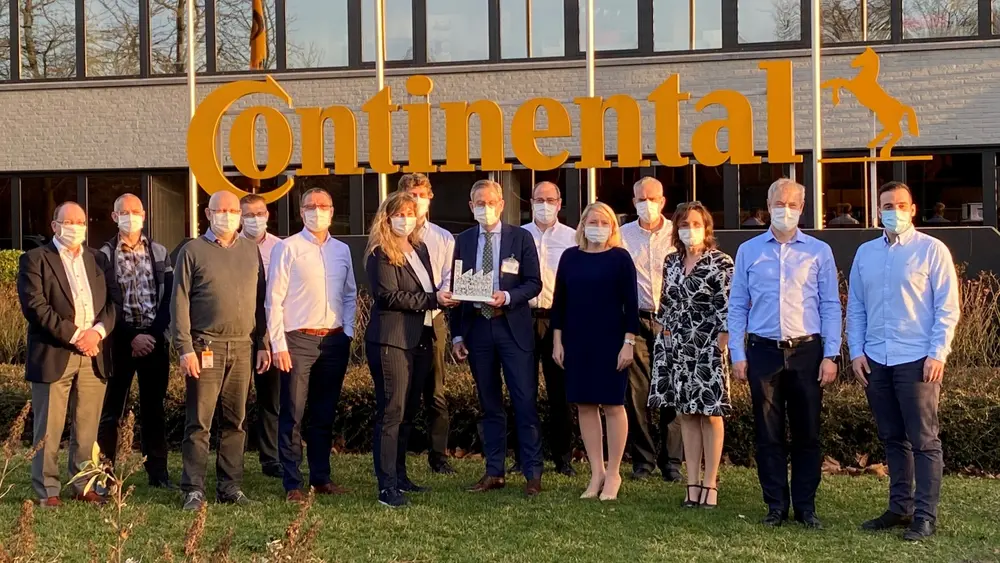
Fournisseur de niveau 1
Continental est un important fournisseur de niveau 1 de l'industrie automobile et se classe au deuxième rang en Europe dans ce domaine, selon le cabinet d'études spécialisé Berylls. Le pilier belge de Malines produit trois grands groupes de produits : des capteurs de roue actifs, des valves hydrauliques et des systèmes de freinage complets.
La production a lieu sur des lignes de production entièrement automatisées utilisant diverses technologies telles que des machines de moulage par injection, des soudures par résistance, des robots, des soudures au laser, des servopresses, des systèmes de caméras, des systèmes d'essais fonctionnels à 100 % et une installation de test capable de développer une pression d'air de plus de 200 bars. La logistique est également fortement automatisée, avec un entrepôt automatique, un e-kanban et des AGV pour la livraison et la collecte des produits. Tous les ingrédients pour parler d'une Factory of the Future, donc.
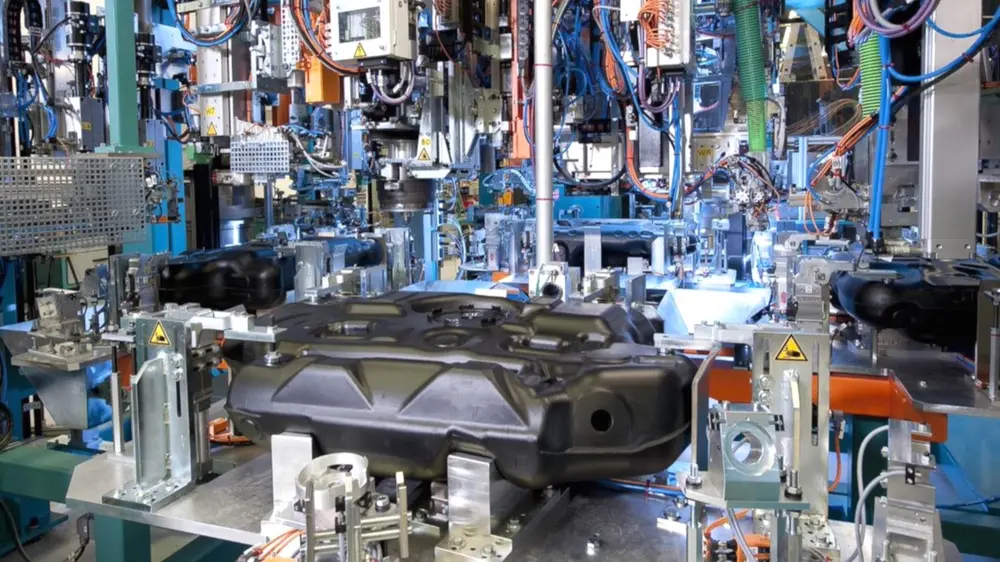
évolutions et impact
Le secteur automobile connaît actuellement plusieurs évolutions passionnantes. Notamment la transition vers les véhicules électriques, mais aussi les conséquences du scandale du diesel et le fait que les constructeurs chinois entrent progressivement sur le marché européen. Enfin, la pandémie de Covid-19 a également eu un impact important.
Motion Control : Comment a-t-on géré ces situations chez Continental ...
Marc Moris "C'est certain, la pandémie de Covid-19 a eu un effet significatif sur notre situation de marché, ce que nous n'avions jamais connu auparavant puisque nous fabriquons des systèmes de freinage électroniques. L'arrivée des constructeurs automobiles chinois aura peu d'impact sur le groupe Continental, par exemple, car les autres usines Continental qui fabriquent des systèmes de freinage font déjà partie de ces chaînes d'approvisionnement locales."
"La transition électrique a en soi peu d'impact sur la production des systèmes de freinage actuels. Dans un système de freinage hydraulique, il y a à la fois un moteur à combustion interne et un moteur électrique, et cela restera le cas pour l'instant pour des raisons de sécurité. Je voudrais également mentionner la tendance importante à la conduite autonome, qui exige encore plus de soupapes dans un système de freinage. Toutefois, des développements sont déjà en cours pour pouvoir proposer des systèmes de freinage 'secs' d'ici 2030.
Factory of the future
"Depuis 2010, nous sommes confrontés à la vague d'Industrie 4.0 et cela vaut vraiment la peine d'utiliser l'évaluation comme un outil à part entière
Qu'est-ce qui a poussé Continental Mechelen à rejoindre le concept de Factory of the Future en 2014 ?
Marc Moris : "Notre directeur d'usine de l'époque, Stefaan Van Thielen, était membre du conseil d'administration d'Agoria. C'est là, avec Sirris, que tout a été mis en place pour aider l'industrie manufacturière flamande à progresser, avec l'intention de ramener les volumes de production en Flandre et de les ancrer ici. Cette approche a conduit au développement de critères d'évaluation ciblés Factory of the Future. Et c'était une étape parfaitement logique pour notre propre retour d'expérience à 360°. Tout d'abord, il s'agissait d'un bon exercice pour réfléchir de manière structurée à ce que nous avions réalisé au cours des dernières années, mais cela nous a aussi permis de nous conforter dans nos choix. Depuis 2010, nous sommes confrontés à la vague d'Industrie 4.0 et cela vaut vraiment la peine d'utiliser les critères d'évaluation comme outil à part entière."
"Via Agoria, nous avons reçu une liste d'opportunités lors de notre première participation pour poursuivre sur la voie du 'Cyber Physical Production System' dans un environnement réel 4.0. Quelques points ont ainsi été mis en avant :
• intégration des éléments physiques sans fil dans le réseau d'information ;
• transformation des systèmes de production en systèmes de production intelligents extrêmement flexibles, auto-apprenants et adaptatifs ;
• maintenance conditionnelle ;
• et enfin, l'utilisation de l'usine en tant qu'outil marketing."
"Nous avons ensuite pris très au sérieux les recommandations. Pour la maintenance conditionnelle, par exemple, de nouvelles idées ont vu le jour et ont été traduites en belles applications. Nous avons également consacré beaucoup d'efforts à notre transformation en ECO Factory, ce qui nous a permis d'obtenir entre-temps les reconnaissances nécessaires. Par exemple, nous avons été la première entreprise du groupe Continental à utiliser 100 % d'énergie verte. Nous nous engageons également à atteindre certains objectifs, comme la charte RSE de VOKA. Cela nous a permis de remporter le prix Continental Green Label."
"Nous avons un responsable interne de l'énergie qui dirige notre équipe ECOS. C'est l'acronyme de Energy COst Saving, cette équipe est active depuis les années 1990. Nos initiatives y sont très diverses : refroidissement central, récupération de la chaleur des compresseurs d'air, arrêt automatique des lignes et des générateurs hydrauliques, éclairage à faible consommation d'énergie, etc. Nous étudions même la façon de récupérer et d'économise l'eau et l'énergie avec nos nouvelles machines à laver industrielles."
Traçabilité au niveau des composants
"Les constructeurs automobiles veulent éviter à tout prix les rappels coûteux. C'est pourquoi la traçabilité est aujourd'hui essentielle dans notre secteur. Grâce à l'utilisation précoce des techniques numériques dans la production, c'est l'un des points forts de notre entreprise. Les ateliers de Malines permettent une traçabilité complète en boucle fermée, du composant au produit fini. En d'autres termes, il est possible d'assurer la traçabilité non seulement au niveau du produit final, mais aussi au niveau des composants. Nous suivons plusieurs facteurs : les numéros de lot des fournisseurs, le moment où les pièces sont sorties de l'entrepôt, le moment où elles sont conditionnées, les machines sur lesquelles elles sont usinées, le moment où elles sont intégrées dans les sous-ensembles et enfin les ensembles finaux dans lesquels elles sont assemblées. Tout cela avec les lieux et les horaires correspondants. Cela nous permet de répondre très précisément aux éventuelles plaintes et de limiter les coûts."
Source d'inspiration et image
Certaines de vos idées ont-elles inspiré des collègues Factory of the Future ?
Marc Moris : "Oui, l'approche allégée de notre flux de matériaux à l'aide d'AGV a été reprise par quelques entreprises. Notre organisation centrée sur l'homme a également fait l'objet d'une grande attention, ce qui a donné lieu à un échange avec d'autres entreprises. Agoria a organisé un événement avec nous sur ce thème. Continental Mechelen a une organisation matricielle et à un certain niveau, nos équipes dans certains départements travaillent en autogestion."
"Une confirmation et une certification supplémentaires de notre position de référence au sein du groupe, via une expertise externe"
Que signifie ce prix pour la position de Continental Mechelen dans le groupe mondial ?
Marc Moris : " Grâce au Factory of the Future Award, nous avons pu faire un travail d'image au sein du groupe, notamment auprès de la direction allemande. Il s'agissait d'une nouvelle confirmation et certification de notre position de référence au sein du groupe, cette fois par le biais d'une expertise externe."
Vous aviez été à nouveau certifié Factory of the Future en 2018. Cela avait-il demandé plus ou moins d'efforts ?
Moris : "Gagner un Factory of the Future Award, cela ne se fait pas du jour au lendemain, c'est un travail de longue haleine qui consiste à s'améliorer et à reprérer les opportunités de manière continue. Cela vaut également pour l'utilisation des nouvelles technologies. La barre est placée chaque année plus haut dans les évaluations, il faut donc faire des efforts constants pour suivre - et devancer - la concurrence."
PRojets
Y a-t-il des projets particuliers qui vous ont marqué ?
Smart Toolshop
Marc Moris : "Le Smart Toolshop de l'évaluation précédente était un projet merveilleux. Nous y avons développé une plate-forme en ligne pour la production des outils que nous fabriquons nous-mêmes, ce qui est le cas pour environ la moitié de nos pièces détachées et de nos outils. Dans le passé, cela impliquait des appels téléphoniques et des échanges de courriels constants entre le planificateur du travail et les responsables de l'atelier d'outillage pour connaître le statut d'une commande. Pour éviter cette perte de temps, nous avons développé une plate-forme dans laquelle les planificateurs peuvent suivre en permanence le statut de leurs pièces. Comme les pièces sont placées dans des conteneurs munis d'une étiquette qui indique la géolocalisation par WiFi, ils savent immédiatement où se trouvent les pièces. Les planificateurs du travail reçoivent également un message texte lorsque la pièce est terminée. Cette méthode de travail a été largement approuvée et permet de gagner énormément de temps. La nouvelle méthode de travail nous a également permis de passer à une équipe autogérée dans l'atelier d'outillage intelligent, alors que deux chefs d'équipe étaient auparavant nécessaires."
Lancement des capteurs de roues
"Une autre étape importante de notre histoire récente est le lancement de la production des capteurs de roues Next-Gen à Malines. La production de ces capteurs a été ramenée dans notre pays depuis des pays à bas salaires. Les capteurs sont un produit typique à faible coût, l'un des nombreux composants qui ont quitté l'Europe pour les pays à bas salaires dans les années 90. Grâce à notre automatisation poussée, nous parvenons aujourd'hui à produire à moindre coût et avec une meilleure qualité que les pays à bas salaires. Le résultat est que nous produisons les capteurs de roue Next-Gen ici depuis un an maintenant, et nous comptons développer cela. Je pense que plus d'entreprises devraient procéder ainsi. Avec un bon niveau d'automatisation, un rendement suffisant et une qualité optimale, beaucoup de choses sont possibles."
une ligne de production entièrement remaniée
"Un troisième projet que je voudrais mentionner est le remaniement d'une ancienne ligne de production. Cette ligne assemblait des systèmes de freinage MK70 depuis 2001, mais ce produit avait été progressivement abandonné. Nous avons converti cette ligne pour fabriquer les systèmes de freinage EBS pour les motos. Certaines parties de la ligne ont été renvoyées à un constructeur de machines pour être modifiées, de nouvelles machines ont été installées et nous avons reconstruit certaines machines nous-mêmes, comme les palettiseurs. Il a fallu environ un an pour mener à bien l'ensemble du projet. Grâce aux faibles coûts d'investissement, nous avons également réussi à amener cette production à Malines."
La feuille de route n'est pas une science exacte
Certaines technologies ont-elles été essayées ces dernières années sans succès ?
Marc Moris : Notre feuille de route technologique ne dépend pas que de nous, mais est réalisée avec nos collègues du monde entier. D'une part, cela se fait par le biais de groupes de travail d'ingénierie simultanés et, d'autre part, au sein du réseau d'expertise mondial du groupe Continental. Mais définir une feuille de route n'est pas une science exacte. Une idée soutenue peut aboutir à un prototype ou à un essai à petite échelle, mais d'autres ne mènent à rien, ou n'ont pas le succès escompté par la suite. CCela été le cas avec Vuzix ou Google Glass, un système qui a connu le succès dans une autre entreprise du groupe Usine du futur. Nous avons pensé que le système pouvait apporter une valeur ajoutée, et nous avions en tête une application dans laquelle le système permettrait aux employés d'effectuer moins de mouvements de balayage manuel. Mais dans notre domaine de travail, nous avons rencontré des lacunes techniques et les utilisateurs ne l'ont pas validé parce que l'ergonomie ne leur convenait pas. Nous avons également écarté un système de suivi avec une Smartwatch. Cela permettait aux employés de recevoir des messages d'erreur, mais au final, le système ne convenait pas vraiment à cause de la taille des appareils et de la nécessité de charger constamment la batterie."
Bonnes pièces et numérisation
Quels sont les projets récemment achevés ?
Marc Moris : "Le but ultime est de ne plus produire une seule mauvaise pièce. L'une des voies que nous suivons est la mise en œuvre du logiciel Space. Cela nous permet d'analyser et de surveiller les tendances de notre processus de manière tellement pointue que nous pouvons intervenir bien avant qu'une mauvaise pièce ne soit effectivement produite. Nous nous concentrons également encore plus fortement sur notre transformation numérique. Un coordinateur I4.0 a été nommé en 2020 pour apporter un soutien encore plus fort à cette transition dans toute l'entreprise. La situation difficile en 2020 a également contribué à accélérer certaines choses. Vous pouvez donc également vous attendre à de nouvelles initiatives dans le domaine de l'organisation centrée sur l'homme. Avec la nouvelle directrice de l'usine, Alexandra Bornemann, forte d'une solide expérience dans la gestion du changement, nous n'avons aucun doute sur le fait que nous viserons une nouvelle récompense d'ici 2024."