L’EMBOUTISSAGE FAIT SON GRAND RETOUR
Lignes complètement automatisées; pas une exception
L’emboutissage est une de ces techniques de tôlerie ayant un peu trinqué ces dernières années. Contrairement au poinçonnage, il s’agit ici des pièces coupées dans la tôle, plutôt que de la tôle usinée même. Comme lors du poinçonnage, une (grande) série d’usinages sont exécutés successivement au moyen d’outils spécifiques comme des poinçons et des matrices. Vous avez pu lire récemment dans Métallerie comment des outils spéciaux ont offert une seconde vie au poinçonnage. L’emboutissage semble aussi à présent faire son retour, surtout pour les produits à base de tôle de qualité supérieure.
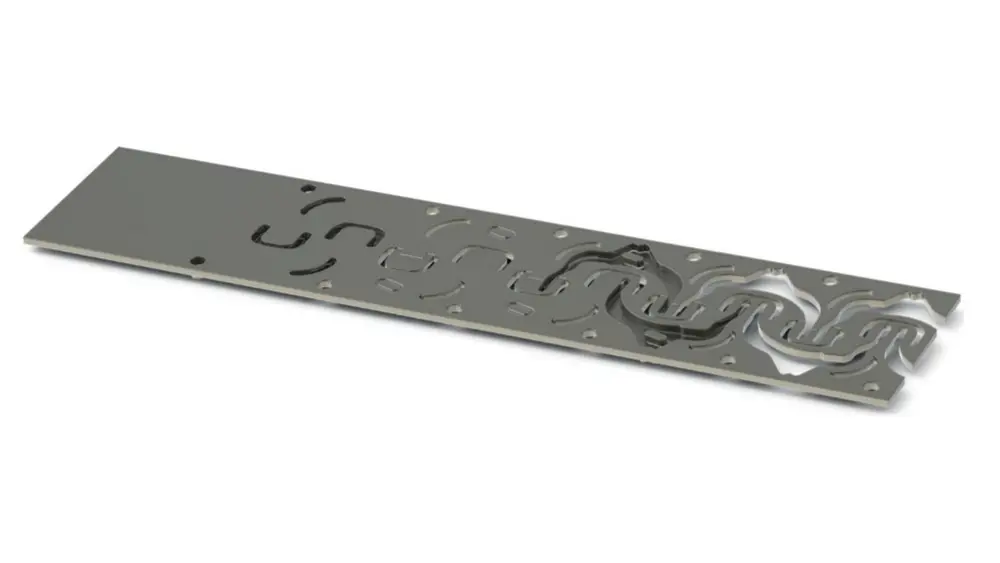
tous ces usinages en un seul mouvement. Le résultat? Un élément découpé, prêt pour l’assemblage. Une finition
est autrement dit superflue et l’emboutissage de précision est plus rapide et plus économique que jamais
QU’EN ETAIT-IL DE L’EMBOUTISSAGE?
La définition décrit l’emboutissage comme une technique mécanique avec des caractéristiques typiques propres, basée sur une machine-outil sous la forme d’une presse commandée par ordinateur, un poinçon ou matrice propre au produit fabriqué au préalable et l’amenée de tôles et l’évacuation des produits découpés. Ces dernières années, la technique conventionnelle très ancienne, qui a même quelque peu disparu dans la formation professionnelle classique, a évolué en une expertise high-end quasiment indispensable suivant les tendances générales actuelles comme le couplage dans la chaîne de production, le monitoring, l’intégration fonctionnelle croissante et l’automatisation dans la périphérie, ainsi que l’économie d’énergie et de matériau.
Une fois réglée correctement, une telle combinaison robuste à rendement élevé produit avec une grande fiabilité et répétabilité des composants, des produits semi-finis et des séries de produits en trois dimensions prêts à l’emploi. Le tout, en outre, avec une grande précision et selon des spécifications définies en termes de mesure et de forme, à partir de tôle, bande ou film relativement fin, sans formation de copeaux.
Avec l’emboutissage, une série d’usinages sont exécutés successivement en différents stades: déformer, rectifier, post-poinçonner, découper, ... Cette déformation et cette séparation peuvent être réalisées au moyen d’un large spectre disponible de processus technologiques. Les usinages cités consistent en un mélange (sous-estimé) d’une sélection généralement cohérente de ces processus. Le produit passe autrement dit par plusieurs étapes différentes dans l’outillage. Si nous considérons l’assortiment total d’outils, nous parlons pour la déformation de conversion, cintrage, dressage, compression et emboutissage profond (pour les produits creux à épaisseur de paroi constante).
Pour la séparation ou découpe, nous parlons de poinçonnage (découpe d’une forme complètement fermée) et taille (pour faire des déchets se retirant plus facilement de la carcasse de tôle ou du matériau résiduel restant), étirage et dressage multiple. Sans oublier des usinages (de finition) plus usuels comme l’ébavurage, le nettoyage, le lavage et le séchage, le test, la correction, le tri et l’emballage. Pendant ces opérations, le matériau de départ change, indépendamment de toute influence humaine, durablement et plastiquement de forme. Ce, de manière complètement contrôlée.
SITUATION SUR LE MARCHE
Aujourd’hui, on parle pour les éléments techniques de production efficace. Ce, notamment de travail de série et de masse, mais aussi de tests, préséries en grands et plus petits nombres ou batchs composés d’éléments distincts et de composants assemblés. Le travail en série est très divers et se distingue dans une plage de produits de qualité de quasiment tous les types et mesures: broches de connecteur press-fit, bandes de contact légères, petits ressorts à lames, grids pour éléments de contrôle et commutation de guidage, lames de rasoir, lead frames fins, boîtiers stables pour smartphones, ...
Les tendances actuelles sont les tolérances de plus en plus justes et les exigences de qualité croissantes. Les clients s’attendent, en outre, à un temps de réaction court, alors que cette flexibilité n’est pas évidente lors du pressage conventionnel, où la taille de série est depuis toujours relativement petite. Les produits personnalisés propres au client donnent, de plus, lieu à des séries encore plus petites, toutefois appliquées souvent longtemps sous la forme de ‘repeat orders’.
Ces ‘specials’ font souvent partie du service et complètent les propres produits. De nombreuses entreprises spécialisées dans l’emboutissage ont, en effet, l’avantage d’abriter en leur sein plusieurs expertises complémentaires, p.ex. une propre fabrique d’outils et une division d’ingénierie. Cela permet d’augmenter la flexibilité, l’intégration de fonction et la productivité de l’installation d’emboutissage, et de réduire le temps de production et les arrêts.
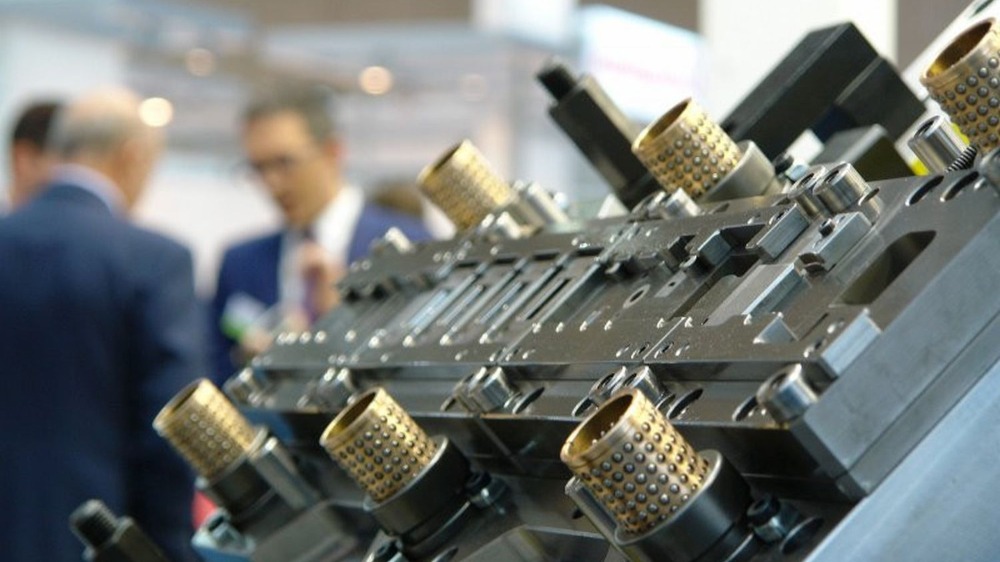
Formation et perfectionnement
Lorsque quelques grosses entreprises ont décidé d’arrêter leur production et de la confier à des sous-traitants, cela a tout d’abord impliqué une diffusion de l’expertise avancée et de l’équipement de production pour l’emboutissage. Au fil des ans, ces connaissances et cette expérience technologiques se sont, surtout pour l’emboutissage, raréfiées. Dans la formation professionnelle classique aussi, la technologie est passée à l’arrière-plan. Conséquence: il y a une pénurie de professionnels qualifiés et expérimentés.
Des trajets d’apprentissage et de travail sur mesure sont proposés depuis peu au secteur en collaboration avec quelques entreprises spécialisées et centres de connaissance et instituts de formation indépendants. Les professionnels orientés pratique sont ainsi formés en opérateurs diplômés ‘nouveau style’. Aujourd’hui, les professionnels ayant suivi un perfectionnement théorique et pratique peuvent faire une différence avec cette expertise, ces compétences et ces connaissances supplémentaires. Ce n’est pas un luxe superflu pour une réaction rapide aux exigences actuelles des clients dans le secteur.
UN BON OUTILLAGE EST DEJA LA MOITIE DU TRAVAIL
Le poinçon constitue le cœur battant de l’emboutissage. Le terme poinçon désigne l’ensemble comme la partie inférieure de l’outil serré en mode stationnaire (= plaque de coupe). L’‘emporte-pièce’ (= découpoir) est la partie supérieure plus légère de l’outil, se déplaçant à une vitesse de production élevée et exécutant les actions de déformation et de coupe. L’emporte-pièce est couplé de manière rigide au poussoir de la presse.
Les poinçons utilisés pour l’emboutissage sont onéreux en raison de leur complexité, mais ont une construction extrêmement durable et peuvent être utilisés à n’importe quel moment sous la presse, avec une sécurité intégrée. Chaque outil d’emboutissage correct contient au moins un dévêtisseur, vu qu’il y a une tendance à l’adhésion par rapport au découpoir, inhérente au processus d’emboutissage. Une tendance, en outre, encore renforcée par les bavures, un agent de lubrification visqueux et une mauvaise amenée.
Dans chaque poinçon complexe, il y a, de plus, une plaque de guidage pour le découpoir, avec des éléments normalisés comme un palier lisse ou des roulements à billes ou à rouleaux précontraints pour les versions plus lourdes en cas de longue tenue d’outil. Dans la pratique, les poinçons sont subdivisés pour divers usinages en un type simple, un poinçon complet et dans la forme la plus complexe, en poinçon progressif avec les variantes poinçon progressif d’étirement, de cintrage ou de dressage, selon la configuration de l’outillage.
Emboutissage de précision
Une technique à part digne d’être mentionnée pour les nombres de production plus conséquents (> 10.000 pièces) est l’emboutissage de précision. Différents fabricants fournissent pour cela des presses triples, avec outillage de façonnage spécial, notamment caractérisées par une rondelle de pression à bord crénelé et un décolleur. Des produits high-end prêts à l’emploi à arêtes lisses sortent ici à la fin du cycle de la matrice spéciale de la machine de production. D’un point de vue économique, il ne faut pas oublier lors de cette phase d’inclure la possibilité de rectification, et d’éviter les bavures et d’éliminer les fissures et les plis.
Conditions essentielles
L’exécution du processus d’emboutissage implique notamment une arête régulière sur toute la géométrie, ainsi que la rectitude d’outils de poinçonnage plus longs, un bon état de surface (Ra) du tranchant, la précision de pas la plus élevée de la plaquette de coupe et du porte-poinçon, et un jeu le plus petit possible, dépendant du type et de l’épaisseur du matériau. La règle de base: 5% de base, pour un travail plus précis ou moins précis, respectivement en-deçà ou au-delà de cette limite. Pour les éléments emboutis les plus courants, un traitement thermique est superflu.
LA SECURITE DANS LA PRATIQUE
Pour les collaborateurs et les opérateurs, notamment à la presse, il est crucial de surveiller dès le début la sécurité. Quelques rappels peuvent être utiles.
- Ayez au préalable une bonne vision des travaux, avant le démarrage.
- Portez, selon les conditions de travail, des équipements de protection individuelle: lunettes de sécurité, gants et chaussures de travail corrects, bouchons d’oreille/casque, masque, ...
- Veillez à ce que les sécurités soient activées et fonctionnent.
- Utilisez uniquement un outillage professionnel et adéquat, et utilisez-le correctement.
- Ne laissez pas traîner d’objets (outils, boulons, écrous, matériau, …), surtout pas lorsque la presse fonctionne.
- Veillez également à garder le sol propre, sec et libre, avec un passage sûr.
(Source: Mikrocentrum)
DEVELOPPEMENTS
Les configurations de presses en partie automatisées depuis toujours ont aussi connu ces dernières années une forte évolution, sur le plan du hardware comme du logiciel. Le contrôle de processus et le contrôle de qualité sont ainsi devenus plus adultes grâce à des systèmes de mesure intégrés, en ligne avec des caméras, des capteurs, le traitement d’images, l’enregistrement de données et l’inspection de bande. Ce dernier point est particulièrement important, lorsque le produit est coupé, avant ou à la fin du cycle. Il y a aussi la sécurisation de plaque de guidage avancée sur la base de la pression, de la force, de la course et du bruit.
Des modèles numériques ont aussi été réalisés de la machine, du matériau, de l’application et du processus, principalement en vue d’une préparation du travail plus complète. La simulation de l’usinage est en passe de remplacer le try-out. Toute la chaîne est ainsi à présent quasiment numérique. La conception et la fabrication de produits modernes sont aujourd’hui non seulement plus transparentes, mais aussi plus prévisibles. Nous pensons à l’estimation de l’emplacement et du comportement d’éléments détachés difficiles.
L’intégration plus poussée des usinages est possible grâce à l’exécution simultanée de différentes étapes supplémentaires sur la machine, avec ou sans appareils en périphérie pour, par exemple, déposer des tôles ou produits semi-finis manuellement, ou amener avec un robot du matériau en bande ou bobine avec un dévidoir et un bobinoir. Une option intégrée courante est la réalisation simultanée d’un marquage, afin de garantir une traçabilité dans le produit pendant la durée de vie.
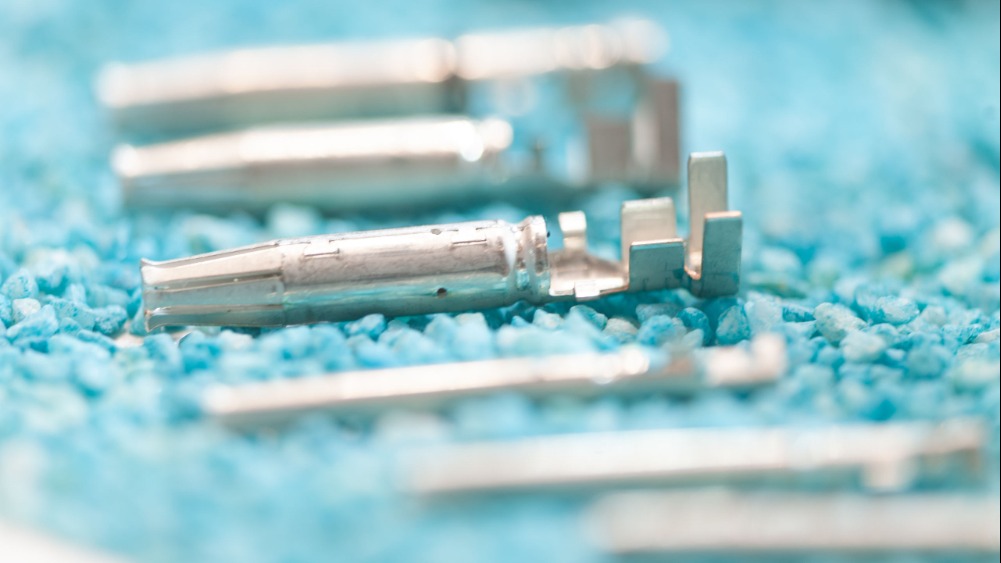
ont montré ces broches de connecteur revêtues embouties
IMPORTANCE DE LA TOLE
Pour être certain que la même qualité puisse être garantie dans une série suivante, une qualité de tôle bien définie et stable est une condition cruciale. Il faut ainsi surveiller que la tôle soit anisotrope. Cela signifie une certaine dépendance de la direction dans laquelle la pièce est chargée, d’assez bien de types de matériau (revêtu ou non): ferreux et non-ferreux, acier, inox et métal résultant de la métallurgie des poudres, cuivre, aluminium et alliages (laiton et bronze (phosphoreux)).
Des matériaux et alliages alternatifs et hybrides sont aussi en pleine progression. Il est donc essentiel de pouvoir distinguer directement le matériau à usiner dans des conditions pratiques et de connaître ainsi les principales propriétés mécaniques, physiques et chimiques. L’opérateur et le programmeur doivent par conséquent posséder un niveau supérieur à la moyenne de connaissances de base liées à la métallurgie, surtout pour les matériaux propres au produit dans le spectre de l’entreprise. Ce, y compris les traitements thermiques et les connaissances et compétences en matière de mesures de dureté, du côté du matériau de départ comme de l’outillage.
Un opérateur peut ainsi analyser la cause d’un problème et le résoudre efficacement et rapidement. Dans la plupart des cas, on utilise une lubrification à base d’eau en guise de lubrifiant, avec ou sans l’ajout de réfrigérants miscibles à l’eau, l’amenée de lessive de savon ou de graisse minérale, toujours dans le but de réduire le frottement et d’éviter le rongement éventuel entre les éléments du poinçon et le produit. La pose d’un film sur le matériau de départ peut aider à obtenir un produit sans traces ou rayures.
CONFIGURATION DE LA PRESSE
En tant que machines-outils, les presses se déclinent en modèles, dimensions et tonnages (jusqu’à 400 à 500 tonnes) très différents. Dans quasiment chaque atelier, on trouve une presse excentrique seule, à commande manuelle ou à double entraînement opposé. Une solution pratique pour de nombreuses tâches. Dans la production, il y a aussi des versions hydrauliques et à servo-commande commandées depuis le réseau propre à l’entreprise en de vraies lignes de presses. Un tel équipement robuste est en général subdivisé en un certain nombre de catégories: commande basée sur l’énergie ou la force et la vitesse (hydraulique), sur la course (excentrique) ou sur le temps ou le travail (marteau à percussion).
Les variantes fournies par un grand nombre de fabricants sont principalement caractérisées par le principe de fonctionnement, la course et la force du poussoir, l’espace de travail de processus, la puissance de raccordement et les dimensions extérieures. Le poids de la machine est important aussi, par rapport à la fondation. Aujourd’hui, un tôlier sélectionne souvent le nouvel équipement d’emboutissage sur la base de grandeurs comme l’énergie, la force, le temps et la précision. Ce, en toute logique selon l’ensemble de commandes actuel et estimé pour le futur.
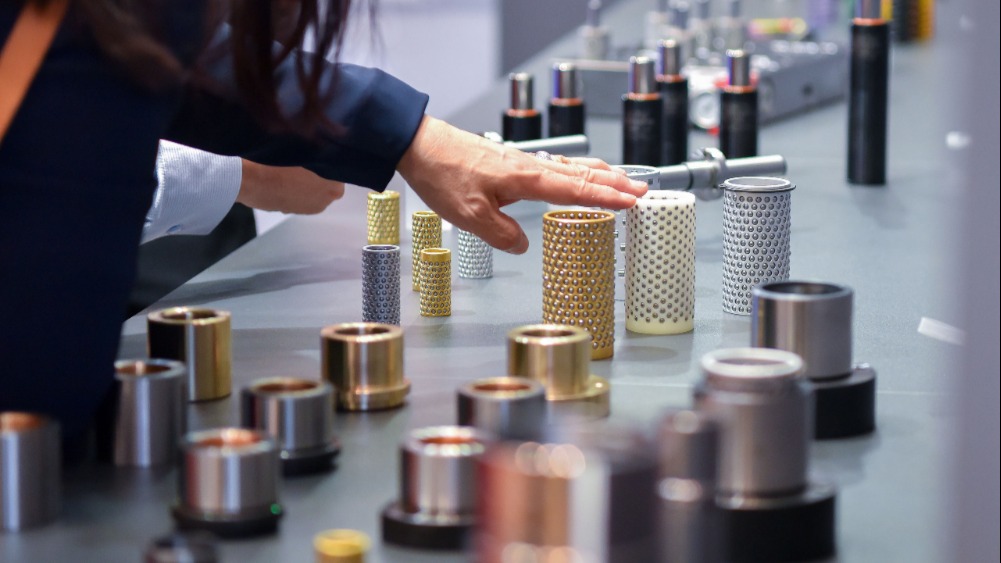
une qualité de tôle bien définie et stable est une condition cruciale
La tâche principale de la presse consiste avant tout à positionner la tôle ou la bande et l’outil d’emboutissage l’un par rapport à l’autre, à garantir la stabilité par la conduction et à transmettre la force ou le couple sur la tôle. La construction détermine directement la conduction, p.ex. du poussoir même ou via les roulements des deux à quatre colonnes robustes de la presse. A l’aide de la machine-outil à commande numérique, la force de presse nécessaire est transférée de manière bien dosée via le poussoir sur le poinçon, générant un fort jeu de forces.
Un réglage correct de la presse et du serrage du poinçon est crucial pour la qualité des produits finaux, la productivité et la durée de vie. Il est essentiel ici que la charge soit aussi centrale que possible, avec la force par le centre du serrage de la table. Selon la construction, il peut y avoir plus ou moins de suspension dans le bâti en C ou le portique fermé pouvant supporter une plus lourde charge pendant la déformation et la séparation. Si ce point est connu, à la suite de tests ou par expérience, cela peut être intégré dans le réglage de la machine, afin de compenser le rebondissement du produit pendant l’usinage.