STANSEN HELEMAAL TERUG VAN WEGGEWEEST
Compleet geautomatiseerde perslijnen geen uitzondering
Stansen is een van die plaatbewerkingstechnieken die de voorbije jaren wat in het verdomhoekje zijn beland. In tegenstelling tot bij ponsen gaat het bij stansen om de gesneden stukken uit de plaat, eerder dan de bewerkte plaat zelf. Net als bij ponsen wordt een (grote) serie bewerkingen na elkaar uitgevoerd door middel van specifieke gereedschappen zoals stempels en matrijzen. Onlangs kon u in Metallerie lezen hoe speciale gereedschappen ervoor hebben gezorgd dat ponsen een tweede leven heeft gekregen. Ook stansen blijkt nu meer en meer opnieuw aan bod te komen, voornamelijk bij hoogwaardige plaatproducten.
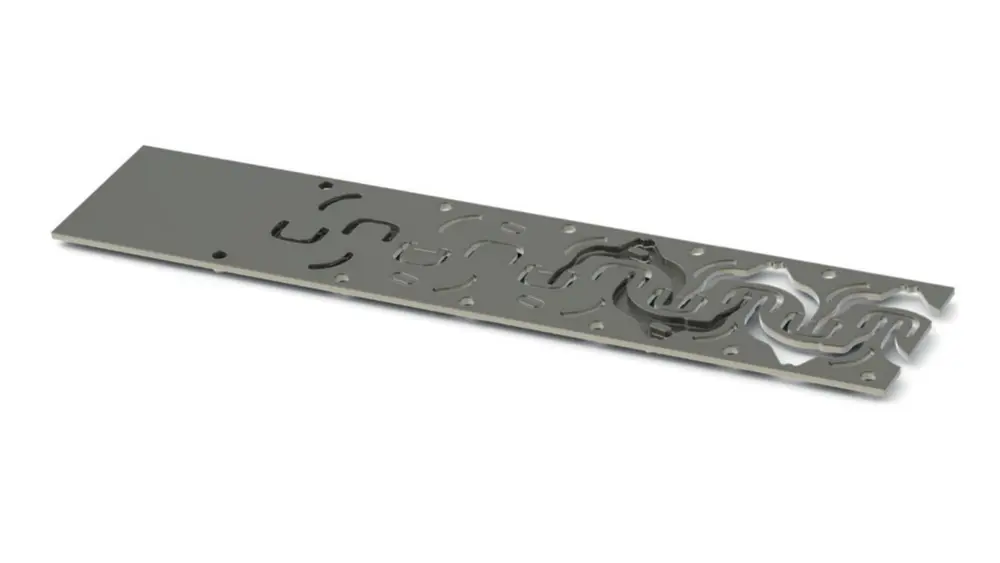
deze bewerkingen in één beweging. Het resultaat is een gestanst onderdeel, klaar voor assemblage.
Nabewerking is met andere woorden overbodig en het fijnstansen verloopt sneller en economischer dan ooit tevoren
STANSEN, HOE ZAT DAT NU WEER?
De definitie omschrijft stansen als een mechanische techniek met typische eigen kenmerken, die opereert door middel van een gereedschapswerktuig in de vorm van een computergestuurde pers, een vooraf gefabriceerde productspecifieke stempel of matrijs en bijhorende aanvoer van platen en afvoer van gesneden producten. De voorbije jaren is de oeroude conventionele techniek, die zelfs in de reguliere vakopleiding zowat is verdwenen, ontwikkeld tot een vrijwel onmisbare high-end expertise die de huidige algemene trends volgt zoals koppeling binnen de productieketen, monitoring, toenemende functionele integratie en automatisering in de periferie, alsmede energie- en materiaalbesparing. Eenmaal vakkundig afgesteld, produceert een dergelijke robuuste combinatie met hoge output bedrijfszeker en hoogrepeterend componenten, halffabricaten en series kant-en-klaar inzetbare driedimensionale producten. Dit alles, bovendien erg nauwkeurig en volgens vastgelegde specificaties wat betreft maat en vorm, uit relatief dunne plaat, band of folie, zonder dat er sprake is van spaanvorming.
Met stansen is in verschillende stadia een serie bewerkingen achter elkaar uit te voeren, zoals omvormen, trimmen, naponsen en lossnijden. Dat omvormen en scheiden kan door een ruim beschikbaar spectrum aan technologieprocessen. De genoemde bewerkingen bestaan uit een (ondergewaardeerde) mix van een meestal op elkaar aansluitende selectie van die processen. Het product doorloopt met andere woorden meerdere verschillende stappen binnen in het gereedschap. Beschouwen we het totale assortiment aan gereedschappen, dan spreken we bij het vervormen over door- of omzetten, buigen, kanten of zetten, nadrukken en dieptrekken (voor holle producten met constante wanddikte).
Bij het scheiden of lossnijden hebben we het over ponsen (uitsnijden van een volledig gesloten vorm) en kappen (om van het overgebleven rastervormige plaatskelet of restmateriaal makkelijker uit te nemen afvalstukken te maken), trekken, strekken en veelvuldig richten. Ook meer gebruikelijke (na)bewerkingen als ontbramen, reinigen, wassen en drogen, testen, corrigeren, sorteren en verpakken komen aan bod. Tijdens deze handelingen verandert het uitgangsmateriaal, los van menselijke invloed, blijvend plastisch van vorm. Dit op volledig gecontroleerde wijze.
MARKTSITUATIE
Vandaag is er bij technische onderdelen sprake van efficiënte productie. Dit onder meer van serie- en massawerk, maar ook testruns, voorseries in grote en kleinere aantallen of batches bestaande uit losse onderdelen en geassembleerde componenten. Het seriewerk is sterk uiteenlopend en onderscheidt zich in een hoogwaardige productrange in zowat alle maten en soorten. Denk aan press-fit connectorpennen, lichte contactstrips, kleine bladveren, stansgrids voor geleidende controle- en schakelelementen, scheermesjes, slanke lead frames of stabiele behuizingen voor smartphones e.d.
Trends vandaag zijn de steeds krapper wordende toleranties en de stijgende kwaliteitseisen.
Klanten verwachten bovendien een korte reactietijd, terwijl die flexibiliteit niet vanzelfsprekend is bij conventioneel perswerk, waar de seriegrootte vanouds relatief klein is. Klantspecifieke, gepersonaliseerde producten leiden bovendien tot nog kleinere series, die wel vaak lang blijven lopen in de vorm van ‘repeatorders’. Die specials zijn vaak een deel van de service en een aanvulling op de eigen producten. Heel wat bedrijven met als specialisme stansen kennen immers het voordeel van meerdere, complementaire expertises in eigen huis, bijvoorbeeld een eigen gereedschapsmakerij en een engineeringsafdeling. Ze dienen als middel om de flexibiliteit, functie-integratie en productiviteit van de stamperij omhoog te brengen en om de productietijd en stilstand te verminderen.
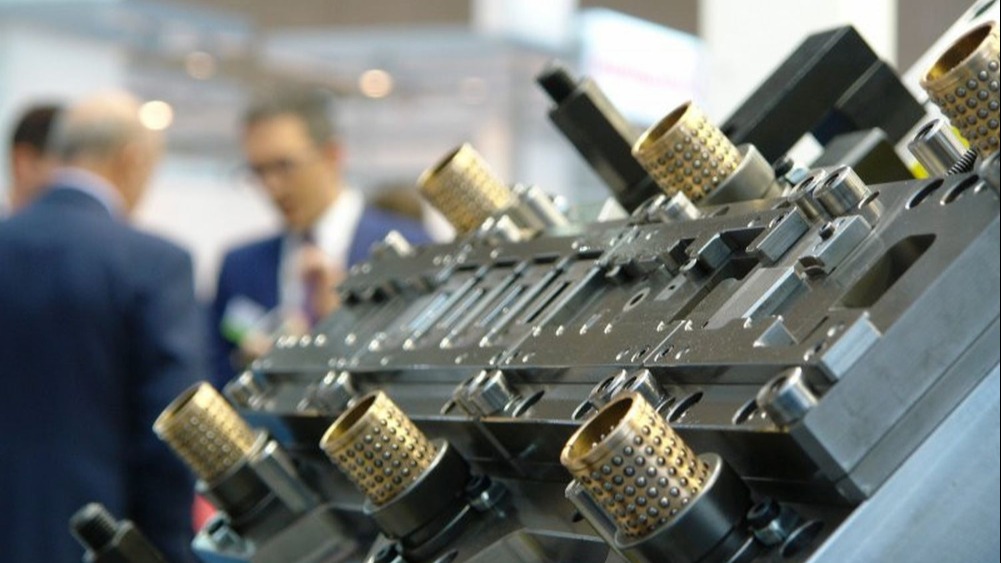
Opleiding en bijscholing
Toen enkele grote bedrijven ervoor kozen om hun productie stop te zetten en te vertrouwen op toeleveranciers, betekende dat in eerste instantie een verspreiding van de geavanceerde expertise en bijhorende productieapparatuur voor het stansen. Door de jaren heen zijn die technologische kennis en ervaring, zeker wat betreft stansen, geleidelijk verdund. Ook in de reguliere vakopleiding verdween de technologie naar de achtergrond. Dat alles heeft ertoe geleid dat er vandaag een tekort is aan geschoolde en getrainde vaklieden.
In samenwerking met enkele gespecialiseerde bedrijven en onafhankelijke kenniscentra en opleidingsinstituten worden daarom sinds kort leer- en werktrajecten op maat aangeboden aan de sector. Dat leidt praktijkgeoriënteerde vaklieden verder op tot gediplomeerde stellers en operators ‘nieuwe stijl’. Theoretisch en praktisch bijgeschoolde vaklui bewijzen vandaag met die extra expertise, handvaardigheid en opgedane kennis een verschil te kunnen maken. Geen overbodige luxe voor een snelle reactie op de actuele eisen van klanten in de sector.
EEN GOED GEREEDSCHAP IS AL HET HALVE WERK
Bij stansen is de stempel het kloppend hart van de bewerking. De term stempel slaat zowel op het geheel als op het onderste deel van het stationair opgespannen gereedschap (= de snijplaat). De ‘pons’ (= de snijder) is het lichtere deel boven in het gereedschap, dat op hoge productiesnelheid meeloopt en de omvorm- en snijacties uitvoert. De pons is star gekoppeld aan de stoter van de pers. De stempels die bij het stansen gebruikt worden, zijn prijzig vanwege hun complexiteit, maar wel uitermate duurzaam van constructie en op elk willekeurig moment in te zetten onder de pers, met ingebouwde beveiliging.
In elk serieus stansgereedschap zit minimaal een afstroper, aangezien er adhesieneiging bestaat ten opzichte van de snijder, inherent aan het stansproces. Die neiging wordt bovendien nog versterkt door braamvorming, plakkerig smeermedium en foute aanvoer. Bovendien zit er in elke complexe stempel een leiplaat voor de snijder opgenomen, met genormaliseerde elementen als glijlagering of voorgespannen kogel- of rollagers voor de zwaardere versies bij een lange standtijd. Stempels laten zich in de praktijk voor diverse bewerkingen onderverdelen in een enkelvoudig type, een compleetstempel en in de meest complexe vorm als volgstempel met als varianten volgsnijtrek-, volgsnijbuig- of volgsnijzetstempel, al naargelang van de configuratie van het gereedschap.
Fijnstansen
Een aparte noemenswaardige techniek voor grotere productieaantallen (> 10.000 stuks) is het fijnstansen. Verschillende fabrikanten leveren daarvoor drievoudig werkende persen, met speciaal vormgevend gereedschap, onder meer gekenmerkt door een drukring met een kerfrand en een tegenhouder. Kant-en-klare high-end producten met gladde snijkanten komen hierbij op het einde van de cyclus uit de speciale matrijs van de productiemachine. Vanuit economisch standpunt mag in deze fase niet vergeten worden om de mogelijkheid tot naslijpen in te bouwen, evenals het vermijden van braamvorming en het elimineren van scheuren en vouwen.
Essentiële voorwaarden
Om het stansproces te kunnen uitvoeren, is onder meer een over de hele geometrie gelijkmatige snijkant vereist, evenals de rechtheid van langere ponsgereedschappen, de hoge oppervlaktegesteldheid (Ra) van het snijvlak, de hoogste steeknauwkeurigheid van de snijplaat en ponsopname, alsmede een zo klein mogelijke speling of snijspleet, die afhankelijk is van de soort en de dikte van het materiaal. Als vuistregel geldt: standaard 5%, voor nauwkeuriger of minder precies werk, respectievelijk onder of boven die grens. Voor de meest gangbare stansdelen is een warmtebehandeling overbodig.
VEILIGHEID IN DE PRAKTIJK
Voor medewerkers en operators, onder andere aan de pers, is het cruciaal om vanaf het begin de veiligheid in de gaten te houden. Enkele geheugensteuntjes kunnen daarbij helpen.
- Zorg vooraf al dat je een goed inzicht hebt in de werkzaamheden, voor de opstart.
- Draag, afhankelijk van de werkomstandigheden, persoonlijke beschermingsmiddelen als veiligheidsbril, correcte hand- en werkschoenen, oordoppen/kappen en mondkapje.
- Let erop dat de beveiligingen ingeschakeld zijn én werken.
- Gebruik alleen professioneel en passend gereedschap. Doe dit enkel op correcte wijze.
- Laat geen losse spullen liggen (gereedschap, bouten, moeren, materiaal …), zeker niet wanneer de persopstelling in bedrijf is.
- Hou ook de vloer proper, droog en vrij, met een veilige doorgang.
(Bron: Mikrocentrum)
ONTWIKKELINGEN
Van oudsher deels geautomatiseerde persopstellingen hebben ook de laatste jaren een sterke evolutie gekend, zowel wat betreft hardware als software. Zo zijn procescontrole en kwaliteitsbewaking volwassener geworden door ingebouwde en geïntegreerde meetsystemen, inline met camera’s, sensoren, beeldverwerking, dataregistratie en stansstrookinspectie. Dat laatste is vooral van belang wanneer het product wordt losgeknipt, voor of op het eind van de cyclus. Verder is ook geavanceerde leiplaatbeveiliging in trek gekomen op druk, kracht, slag en geluid. Er werden ook numerieke modellen opgesteld van de machine, het materiaal, de applicatie en het proces, voornamelijk om de werkvoorbereiding completer te laten verlopen.
Simuleren van de bewerking is op weg om de try-out te vervangen, waarmee de hele keten tegenwoordig nagenoeg digitaal is. Ontwerp en fabricage van moderne producten verlopen vandaag niet alleen transparanter, maar zijn ook beter te voorspellen. Denk aan het inschatten waar lastige losse stukjes en ponsdoppen vrij liggen of naar boven komen of kantelen. Een verdere integratie van bewerkingen is mogelijk door het simultaan uitvoeren van verschillende extra stappen op de machine, al of niet met apparaten in de periferie om bijvoorbeeld blanks of halffabricaten manueel los in te leggen, of met een robot materiaal op een strook, band of coil aan te voeren met een afspoel- en oprolhaspel. Een veelvoorkomende ingebouwde optie vormt het tegelijk aanbrengen van een markering, om zo gedurende de levensduur een optimale traceability te realiseren in het product.
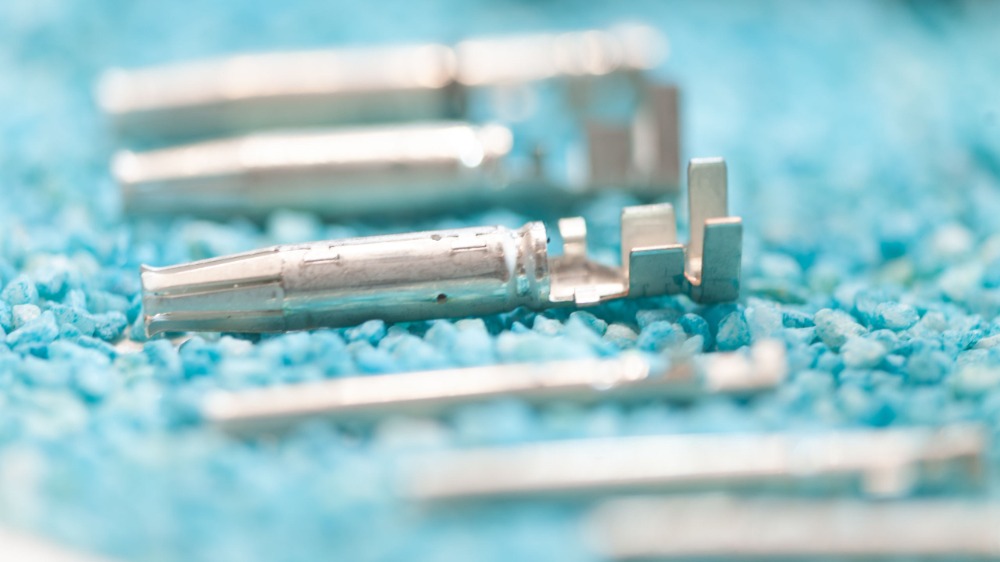
BELANG VAN HET PLAATMATERIAAL
Om zekerheid te hebben dat in een volgende serie dezelfde kwaliteit kan worden gegarandeerd, is eenduidig gedefinieerde en consistente plaatkwaliteit een cruciale voorwaarde. Zo moet in de gaten worden gehouden dat de plaat anisotroop is. Dat betekent een zekere afhankelijkheid van de richting waarin het werkstuk wordt belast, van nogal wat soorten (al dan niet gecoat) materiaal: ferro en non-ferro, staal, rvs en poedermetallurgisch metaal, koper, aluminium en legeringen (messing en (fosfor)brons). Daarnaast zijn ook alternatieve en hybride materialen en legeringen aan een opmars bezig. Daarom is het essentieel om onder praktijkcondities het te bewerken materiaal direct te kunnen onderscheiden en zo de belangrijkste mechanische, fysische en chemische eigenschappen te kennen.
Bijgevolg dient bij de operator en de programmeur een bovengemiddeld niveau aan basiskennis op gebied van metallurgie beschikbaar te zijn, vooral van productspecifiek materiaal binnen het bedrijfsspectrum. Dit, inclusief aansluitende warmtebehandelingen en kennis en kunde over hardheidsmetingen, zowel aan de kant van het uitgangsmateriaal als van het gereedschap. Zodoende kan een operator bij storing de oorzaak analyseren en deze deskundig en snel verhelpen. In de meeste gevallen wordt gebruikgemaakt van smering met behulp van water als smeermiddel, met al dan niet toevoeging van watermengbare koelvloeistoffen, toevoer van zeeploog of mineraal vet, steeds met het doel om de wrijving te verlagen en eventueel vreten tussen stempeldelen en product te voorkomen. Het aanbrengen van een folie op het uitgangsmateriaal kan helpen om een product zonder aftekening of krassen te produceren.
CONFIGURATIE VAN DE PERS
Als werktuigmachines komen persen in sterk verschillende uitvoeringen, afmetingen en tonnages (tot 400 à 500 ton) voor. In vrijwel elke werkplaats vindt men een losse excenterpers, handbediend of al dubbel tegengesteld aangedreven. Voor veel klussen een handige oplossing. In de productie staan daarnaast vanuit het bedrijfseigen netwerk gestuurde hydraulische en servogestuurde versies in heuse persstraten. Dergelijke robuuste apparatuur valt in het algemeen te onderscheiden in een aantal categorieën: energie- of kracht- en snelheidsgestuurd (hydraulisch), weg- of slaggebonden (excenter) of op tijd of arbeid (slaghamer).
Varianten, geleverd door een groot aantal fabrikanten, kenmerken zich in hoofdzaak op werkingsprincipe, slag en kracht van de stoter, proceswerkruimte, aansluitvermogen en buitenafmetingen. Bovendien is ook het machinegewicht van belang, in verband met de fundering. Een plaatbewerker selecteert vandaag de nieuwe stansapparatuur vaak op grootheden als energie, kracht, tijd en nauwkeurigheid. Dit, logischerwijs uitgaande van het huidige en voor de toekomst ingeschatte orderpakket.
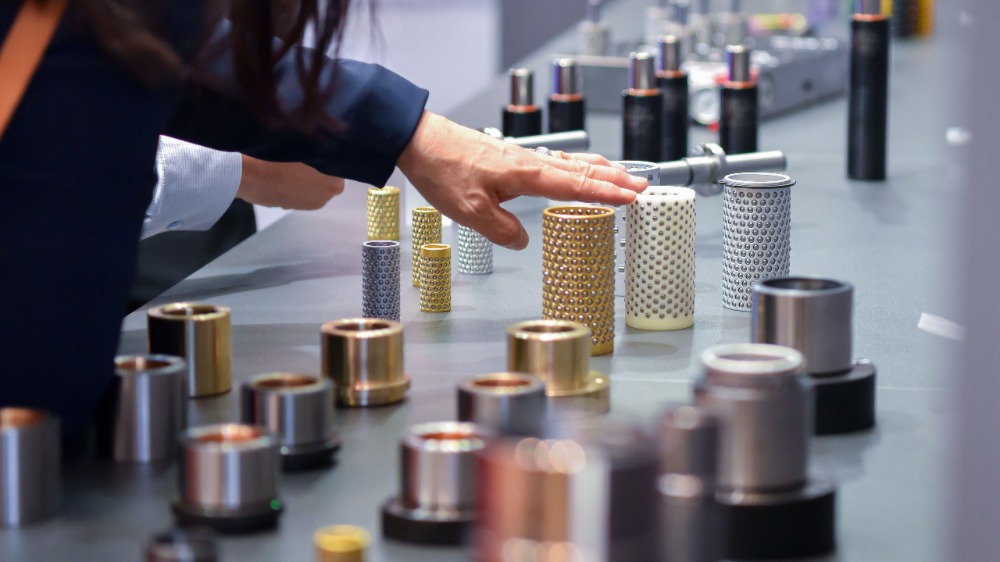
In eerste instantie is het de hoofdtaak van de pers om blenk, strook of strip en stansgereedschap relatief ten opzichte van elkaar in positie te brengen, de stabiliteit te garanderen door de geleiding en om de nodige kracht of momentum over te brengen op plaatmateriaal. De opbouw bepaalt rechtstreeks de geleiding, bijvoorbeeld van de stoter zelf of via de lagering van de twee tot vier robuuste kolommen van de pers. Met behulp van het numeriek bestuurde gereedschapswerktuig wordt de benodigde perskracht via de stoter strak gedoseerd op de stempel overgebracht, waarbij zich in bedrijf een fors krachtenspel afspeelt.
Een juiste afstelling van de pers en opspanning van de stempel zijn van cruciaal belang voor de kwaliteit van de eindproducten, de productiviteit en de levensduur. Essentieel is daarbij om de belasting zo goed mogelijk centraal te laten verlopen, met de kracht door het center van de tafelopspanning. Afhankelijk van de bouw kan er meer of minder vering in het C-vormige frame of de hoger belastbare gesloten portaalconstructie optreden tijdens het omvormen en scheiden. Is dit bekend, uit proefopstelling of door ervaring, dan kan dit meegenomen worden bij de instelling van de machine, om terugvering van het product tijdens de bewerking te compenseren.