Découpe au plasma: où en sommes-nous aujourd'hui?
Amélioration systématique de la qualité de coupe
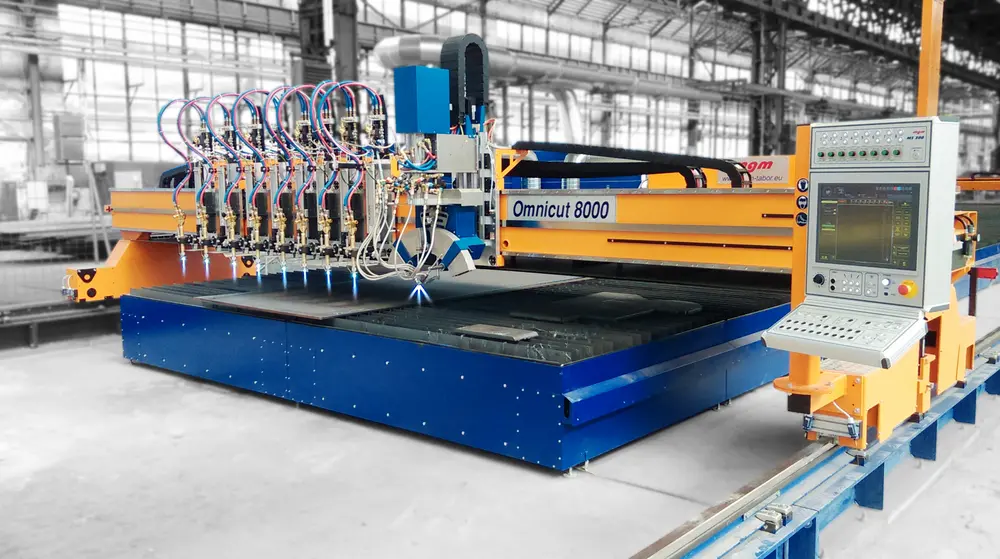
En termes de précision, la découpe au plasma a déjà parcouru un long chemin. Alors qu'à l'origine, le diamètre minimal des trous devait être égal à deux fois l'épaisseur de la tôle, ce rapport est aujourd'hui de 1 à 1, voire légèrement inférieur (0,8) dans la fourchette moyenne. En ce sens, la forte augmentation de la qualité des trous est symbolique de l'amélioration générale de la qualité de la découpe au plasma. Nous passons en revue les développements qui sont à la base de cette évolution afin de donner une image précise de la situation actuelle. Et il s'avère que c'est très proche du laser.
Fusion ou combustion
Lorsque vous chauffez un gaz par l'ajout d'énergie jusqu'au point où les atomes perdent leurs électrons, il devient conducteur. Les découpeurs au plasma utilisent ce principe pour faire fondre le matériau. C'est la principale différence avec la découpe au gaz, qui brûle le matériau.
Lors de la découpe au plasma, la source d'énergie crée un arc entre la torche de coupe (la cathode) et la pièce (l'anode). L'arc est tiré sous un nuage de gaz inerte ou d'air comprimé, qui est forcé sous haute pression à travers la buse. L'arc électrique fait monter la température du gaz à 30.000 °C, une température suffisante pour transformer une partie du gaz en plasma et faire fondre le matériau. Le reste du gaz fait disparaître la fonte.
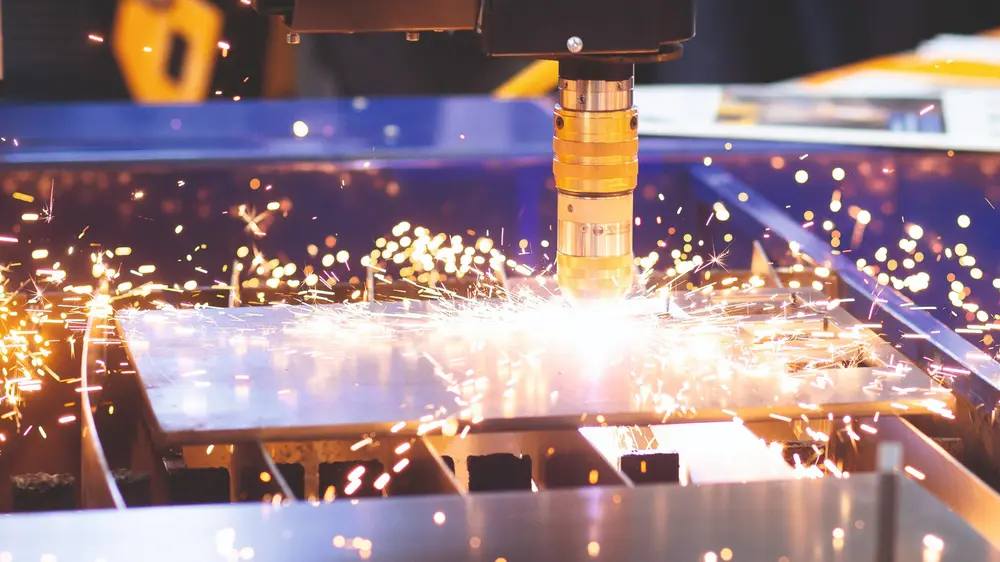
Diverses évolutions
Une machine de découpe laser reste plus chère qu'une machine de découpe au plasma, et cette dernière présente également l'avantage de pouvoir traiter des tôles d'une épaisseur allant jusqu'à plus de 60 mm. Mais cette technologie a aussi ses inconvénients, comme le manque d'équerrage de la coupe et les problèmes de tolérance avec les petits détails et les contours intérieurs aigus.
Néanmoins, nous avons parcouru un long chemin dans ces domaines. N'oubliez pas que les premières sources de plasma étaient des transformateurs à échelons qui ne produisaient pas un courant de coupe très stable et qu'au départ, un seul gaz de coupe était utilisé, ce qui entraînait un désalignement angulaire des deux côtés de la coupe. L'époque du plasma conventionnel est révolue depuis longtemps, grâce aux diverses évolutions technologiques qui ont permis d'augmenter chaque fois la précision de manière significative.
Diverses avancées technologiques ont considérablement amélioré la précision des coupes
Plasma HD
Le premier grand pas en avant a été fait avec la variante haute définition du plasma conventionnel. Ainsi, une couche de gaz à rotation rapide (gaz protecteur) autour de l'arc plasma proprement dit assure une forte focalisation ou constriction.
Cette forme d'atmosphère supplémentaire autour de l'arc de coupe a tout d'abord mis fin à l'obliquité typique associée à la coupe au plasma. En d'autres termes, la qualité et l'équerrage de la coupe se sont nettement améliorés.
En outre, elle a permis d'allonger la durée de vie des pièces de coupe. Cet aspect ne doit pas non plus être sous-estimé, car par rapport au laser, la découpe au plasma présente encore une consommation assez élevée de pièces d'usure dans la torche à plasma. En prolongeant la durée de vie, ces coûts pourraient être quelque peu réduits.
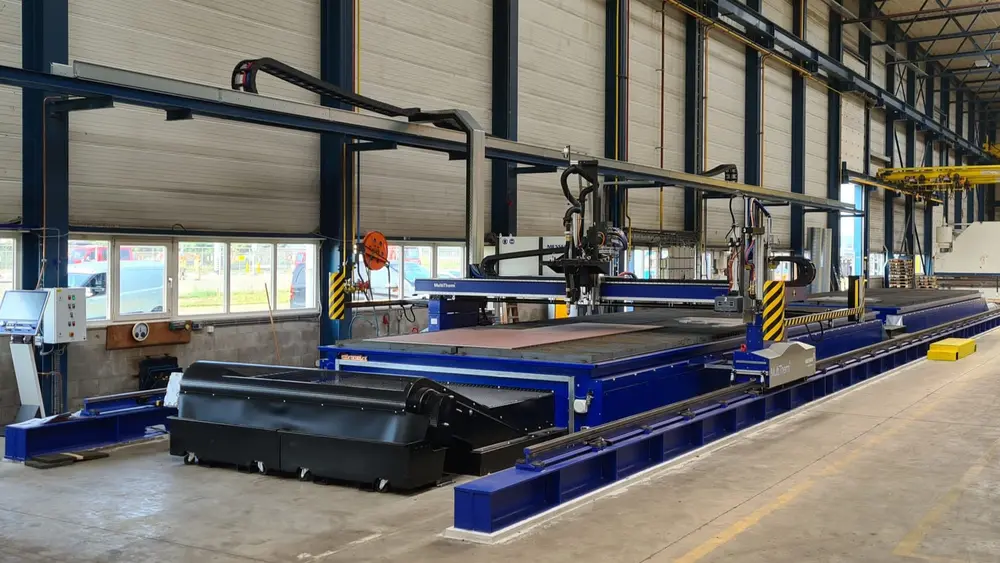
Meilleure qualité des trous
Un deuxième problème auquel la découpe au plasma était confrontée était la conicité des trous: le fond du trou s'écartait tellement du diamètre fixé qu'un boulon ne pouvait pas y entrer. Entre-temps, presque tous les fabricants ont développé une technologie à cet effet.
Il s'agit toujours d'une interaction complexe d'interventions, à commencer par la méthode de rodage, qui affecte principalement la qualité du trou à cet endroit. Au lieu de travailler en ligne droite du centre vers le bord, on travaille maintenant en arc de cercle.
Un élément supplémentaire est la vitesse de coupe, qui est différente pour les trous et pour les autres contours. En effet, la machine utilise non pas un mais deux paramètres dans le programme: un pour les contours et un pour les trous. Un chapitre récent de cette histoire prévoit même une accélération toujours plus grande lors de la coupe, afin d'obtenir des résultats encore meilleurs.
Troisièmement, le gaz protecteur est utilisé avec une forte teneur en oxygène, afin qu'il puisse jouer un rôle actif dans le processus de coupe.
Enfin, sur la base de différents paramètres (par exemple, l'épaisseur de la tôle, la vitesse de coupe...), le contrôle calcule le point exact auquel il doit arrêter l'arc, de sorte qu'aucun point de déformation ne soit visible à la fin du cercle. Ce point ne coïncide donc pas avec le moment où le 360° complet a été couvert; il y a une phase de basculement. Le contrôle accru du processus rend cela possible.
Paramétrage et contrôle du processus
En général, la découpe au plasma nécessite un grand nombre de paramètres qui doivent être parfaitement réglés afin de fonctionner de manière qualitative, productive et rentable. Par exemple, la qualité de la coupe dépend de la vitesse du mouvement horizontal de la torche et de sa hauteur; le plasma et le gaz protecteur utilisés dépendent du matériau de la tôle et, bien sûr, la tension de l'arc fournie (ampérage et pression du gaz) doit être adaptée à l'épaisseur de la tôle.
Ces connaissances, qui devaient auparavant être obtenues auprès de l'opérateur, sont désormais stockées dans de vastes bases de données qui répertorient les combinaisons optimales pour des applications spécifiques. Cela rend l'opérateur beaucoup moins dépendant. Outre l'intégration complète de la base de données dans la source plasma, le contrôle offre de plus en plus d'outils pour surveiller la machine et la rendre plus intelligente dans sa façon de traiter les données recueillies pendant la découpe. Cela se traduit, entre autres, par un meilleur logiciel d'imbrication et un retour d'information en temps réel pour l'opérateur.
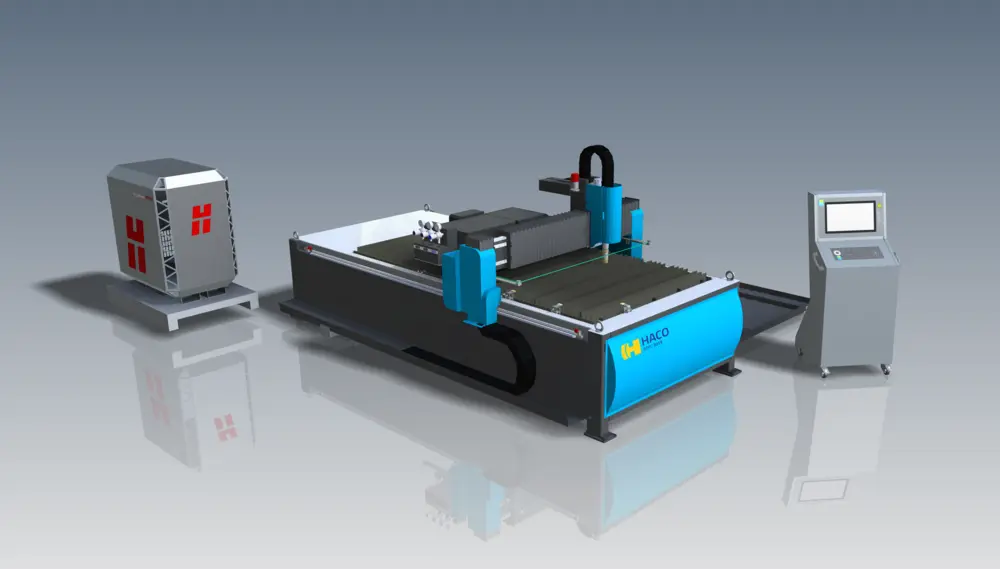
Multi-talent
Les machines de découpe au plasma sont de plus en plus souvent équipées d'outils supplémentaires. Pour des raisons de traçabilité, de nombreux utilisateurs souhaitent marquer leurs pièces, par exemple (à l'argon). Les programmes de commande et d'imbrication des machines de découpe au plasma sont conçus à cet effet. Grâce à la possibilité de réglage du courant, la profondeur et la largeur du trait de gravure peuvent également être ajustées de plus en plus finement, ce qui permet d'obtenir une qualité de gravure allant de très fine à extrêmement grossière. En alternative à la source de plasma, une machine de découpe au plasma peut aussi être facilement combinée à un jet d'encre, mais cela n'est pas nécessaire. Le marquage, d'ailleurs, n'est qu'une des nombreuses combinaisons possibles. Il s'agit tout autant de l'abattage de gaz, du forage, du taraudage ou de la coupe de tuyaux. Bien plus que le laser, la machine de découpe plasma est donc un multi-talent qui permet à l'utilisateur de proposer des pièces plus complexes.
Coupe de biais
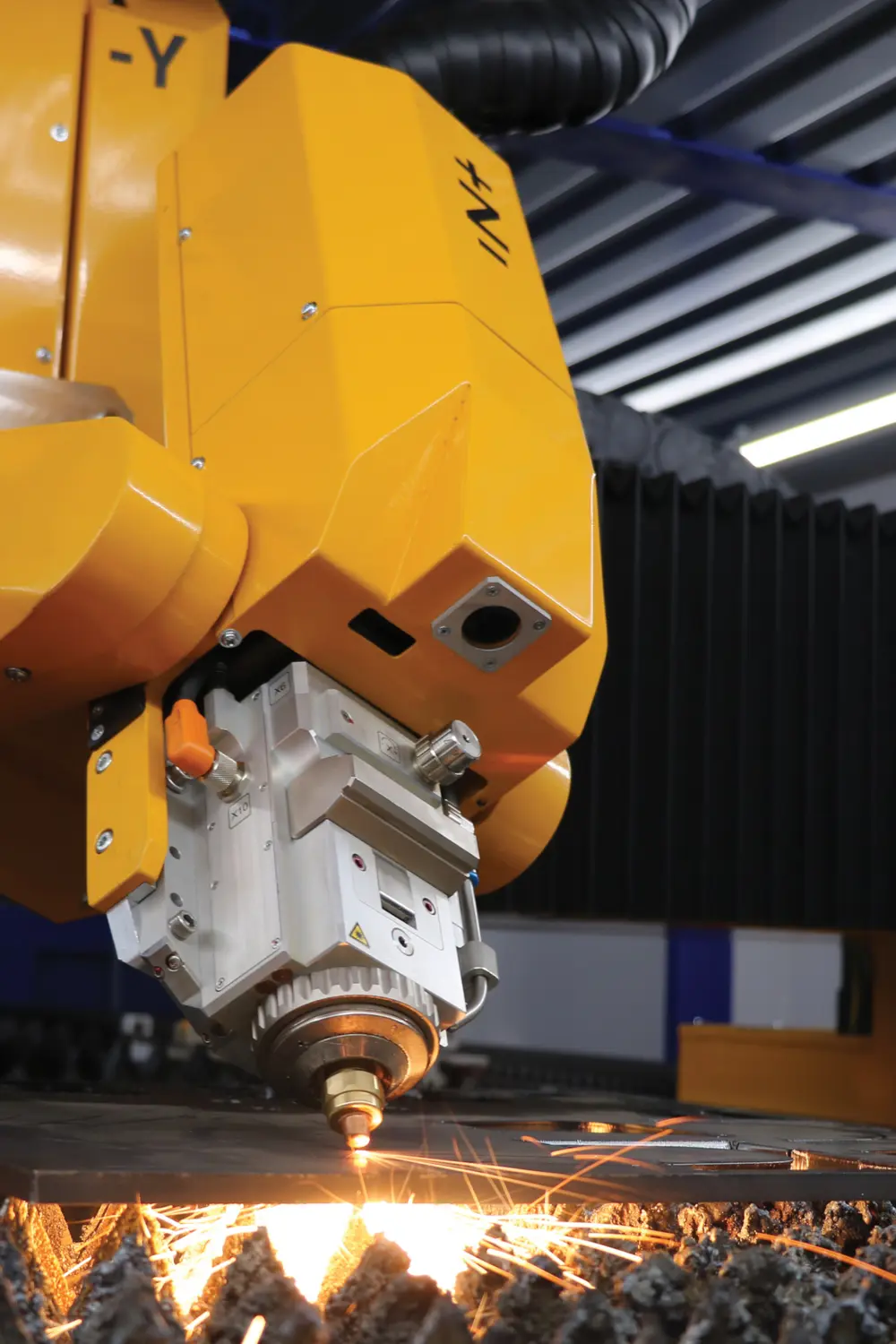
En tant que méthode de préparation des soudures, le biseautage est une option populaire parmi les utilisateurs de machines de découpe au plasma. Cependant, cela ajoute à la complexité, la compensation logicielle de l'angle et le contrôle correct de la hauteur de coupe constituant les deux plus grands défis.
Hauteur de coupe
À un angle de 45°, un écart de hauteur de 1 mm se traduira par un écart dimensionnel de 1 mm sur la pièce. Dans le cas d'un angle constant, ce problème peut être résolu: les fabricants utilisent la tension de l'arc pour calculer la distance entre la torche et le matériau. Mais avec un angle variable, la tension de l'arc n'est plus constante, ce qui rend beaucoup plus difficile, mais pas impossible, son utilisation comme point de référence.
Les logiciels de certains fabricants sont maintenant si avancés qu'ils peuvent également compenser un angle variable dans la commande, en fonction de la tension de l'arc. D'autres optent pour une mesure indépendante de la hauteur avec des capteurs laser dans le cas d'un angle variable. Ces appareils de mesure doivent être capables de traiter les différentes fréquences lumineuses et les perturbations que l'arc plasma émet.
Bien que difficile, de plus en plus de cas de coupe en biais à angle variable sont rencontrés dans la pratique.
Angle de coupe
Outre la hauteur de coupe, il faut également considérer l'angle et la stabilité dimensionnelle, en tenant compte des propriétés physiques du matériau. On utilise ici des valeurs de compensation qui dépendent, entre autres, de l'épaisseur de coupe et du matériau. Un autre facteur important ici est la détermination du point central de l'outil: le point autour duquel la torche peut tourner. Après une collision, des déviations mécaniques peuvent bien sûr se produire. La tête de biseau doit alors être recalibrée, soit manuellement, soit automatiquement via une station de calibrage.
Découpe de l'aluminium
L'aluminium (et dans une moindre mesure l'acier inoxydable) est un autre cas particulier. Avec l'aluminium, l'arc plasma traîne fortement, ce qui rend le contrôle du processus de coupe plus difficile. En outre, son point de fusion est inférieur à celui des autres types de métaux. Afin de minimiser la zone affectée par la chaleur, vous pouvez utiliser un jet d'eau au lieu d'un gaz protecteur. Cela resserre également l'arc et le jet a l'avantage supplémentaire de mieux évacuer la chaleur. L'utilisation d'un brouillard d'eau peut être particulièrement utile dans la gamme moyenne. Cependant, l'eau doit être très pure, avec une teneur spécifique en calcaire et en fer, et vous aurez également besoin d'autres cartouches filtrantes - lisez: plus chères. Par ailleurs, pour éliminer complètement l'influence de la chaleur, vous avez toujours la possibilité de couper sous l'eau, bien sûr.
Conclusion
Tous les développements décrits ci-dessus ont permis à la découpe plasma d'atteindre aujourd'hui une qualité de coupe conforme à la norme ISO 2 pour les tôles fines et à la norme ISO 3 pour les tôles plus épaisses. Un niveau comparable donc à la découpe laser, ce qui est assez impressionnant compte tenu de l'origine de cette technologie. En outre, des progrès sont également réalisés dans des domaines très spécifiques, tels que la découpe sur commande et la découpe de l'aluminium. Mais ce processus connaît encore des limites. Les finitions nettes et les petits détails possibles avec un laser ne sont pas encore à la portée du plasma. Par contre, le laser atteint ses limites lorsqu'il s'agit de couper des épaisseurs à partir d'environ 15 mm. Bref, pour l'instant, les deux technologies se valent pour leurs qualités et avantages respectifs.
En collaboration avec De Tollenaere, Haco, Hypertherm, Messer Cutting Systems, Plasma Solutions et Wouters Cutting & Welding