Le traitement de surface de l'inox n'est pas du luxe
Restaurer la couche d'oxyde endommagée de l'inox
La couche d'oxyde qui protège 'naturellement' l'acier inoxydable peut être perturbée par des opérations telles que le soudage, le pliage et l'usinage, ainsi que par l'action de certains chlorures; l'ampleur de ces perturbations détermine si une restauration spontanée se produit. Si ce n'est pas le cas, il faut alors prévoir un traitement de surface, ce qui a pour agréable effet secondaire que l'objet traité prend moins facilement la saleté. Il s'agit d'une caractéristique importante lorsqu'une hygiène optimale est requise.
Restauration du film d'oxyde
Si la couche d'oxyde est endommagée, elle se réoxyde en présence d'une quantité suffisante d'oxygène et la situation initiale est rétablie. Si ce mécanisme ne fonctionne pas, trois opérations de restauration sont appropriées: le traitement mécanique (voir encadré), le traitement chimique et le traitement thermochimique de durcissement. Cet article se concentre sur les deux derniers.
Traitements de surface mécaniques
Le sablage avec des billes de verre ou de céramique élimine les oxydes thermiques. Le taux de fracture élevé crée des éclats qui donnent une rugosité de surface élevée. Avec les billes de céramique - moins susceptibles de se briser -, le résultat final est plus lisse mais les contaminants sont (plus) difficiles à éliminer.
Le ponçage, le polissage et le brossage visent à obtenir une certaine finition; celle-ci dépend du type de disque et de la taille des grains. Le brossage convient également pour éliminer les dommages et les défauts de couleur. Le polissage présente la rugosité de surface la plus faible, mais c'est aussi l'opération qui demande le plus de travail.
Le sablage humide avec un abrasif assure une finition hygiénique et esthétique; l'utilisation d'eau déminéralisée ou obtenue par osmose inverse est recommandée. Le traitement répond aux exigences d'hygiène élevées des industries alimentaires et pharmaceutiques.
Traitements de surface chimiques
Décapage et passivation
Lors du décapage, on utilise des acides forts pour éliminer les traces de chaleur et les décolorations. La passivation se concentre sur l'élimination des contaminants et la restauration de la couche protectrice. Comme le décapage peut être effectué par trempage, pulvérisation, circulation et au pinceau, ce traitement est relativement facile à réaliser et donc relativement bon marché.
Le décapage est relativement facile à réaliser et donc relativement bon marché
Cependant, les deux processus doivent être effectués dans un endroit clos et bien ventilé, en portant des équipements de protection individuelle. Pour les petites surfaces et le traitement d'un cordon de soudure par exemple, on utilise généralement une pâte décapante; pour les grandes surfaces, on utilise le décapage par pulvérisation ou en bain.
S'ils sont mal préparés, les bains de décapage peuvent être contaminés par des métaux et/ou causer des dommages irréparables. Pendant la passivation, il peut se produire une inclusion de saletés provenant par exemple de chlorures, ce qui est préjudiciable à la couche d'oxyde de chrome. Pour ces raisons, il faut toujours rincer à l'eau déminéralisée.
Polissage électrolytique ou électrochimique (PE)
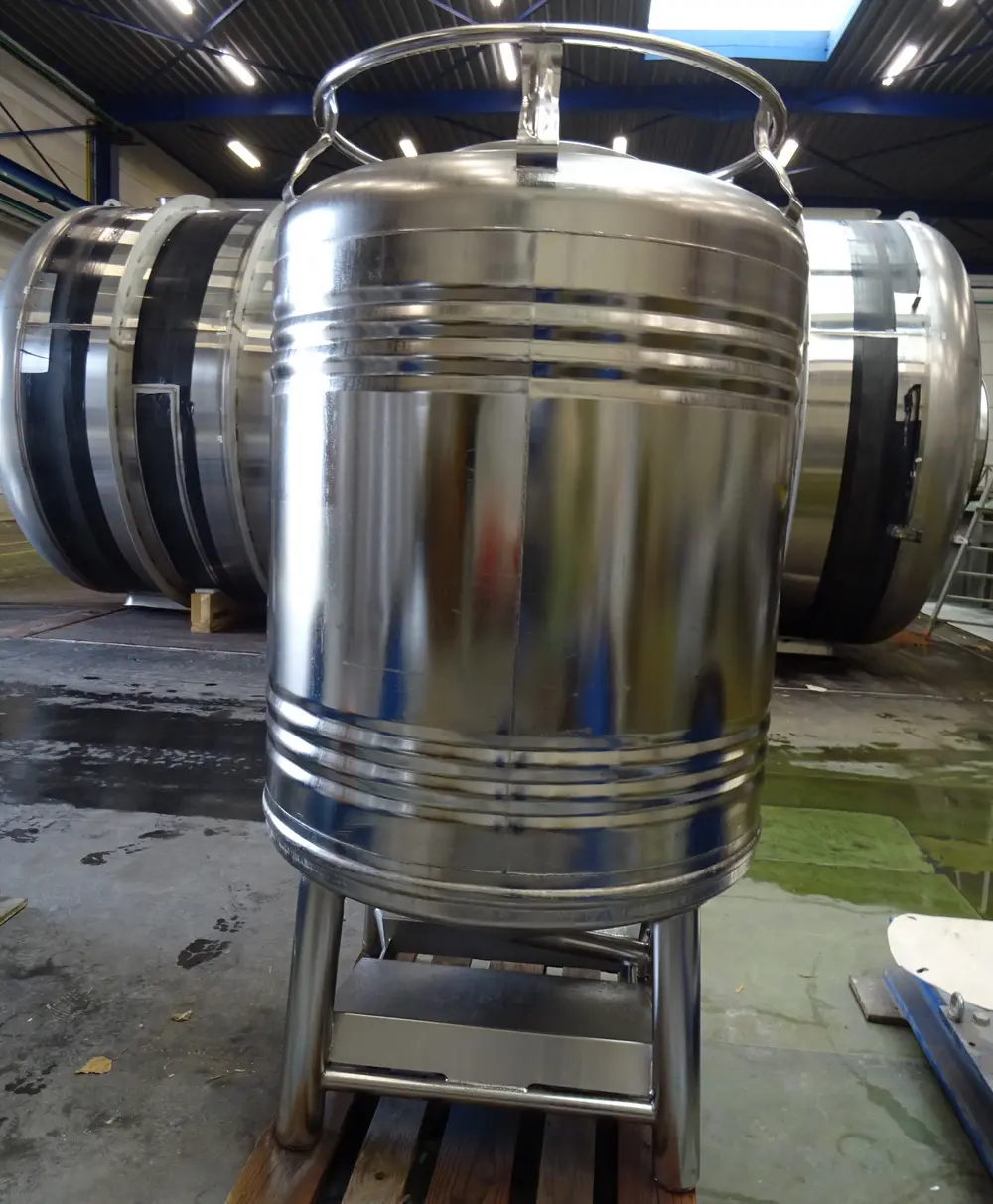
Le PE permet d'enlever de la matière d'une surface métallique, ce qui donne une finition très brillante. La faible rugosité de la surface réduit également de manière significative l'adhérence du produit, de la saleté et des micro-organismes.
L'objet à traiter est suspendu dans une cuve contenant des produits chimiques. Il peut s'agir, par exemple, d'un mélange de différents acides (acide sulfurique, acide chromique, acide citrique et/ou acide phosphorique) qui n'est généralement dilué dans l'eau que de manière limitée, ou de composants organiques tels que de la glycérine ou de l'éther monobutylique du diéthylèneglycol.
Sous l'influence du courant électrique et des produits chimiques du bain, les couches superficielles endommagées et contaminées se dissolvent. Comme le chrome se dissout moins rapidement que les autres métaux au cours du processus d'électrolyse, il en reste proportionnellement plus, ce qui permet d'obtenir une résistance à la corrosion (encore) meilleure.
En raison de sa nature inerte après traitement, le PE est fréquemment utilisé lorsqu'une bonne nettoyabilité est requise, comme pour les équipements et les canalisations dans les industries pharmaceutiques et alimentaires. Le PE est comparativement coûteux, non seulement en raison des cathodes généralement complexes, mais aussi parce que les électrolytes utilisés doivent être traités et éliminés comme des déchets dangereux. En revanche, ce procédé consomme relativement peu d'énergie.
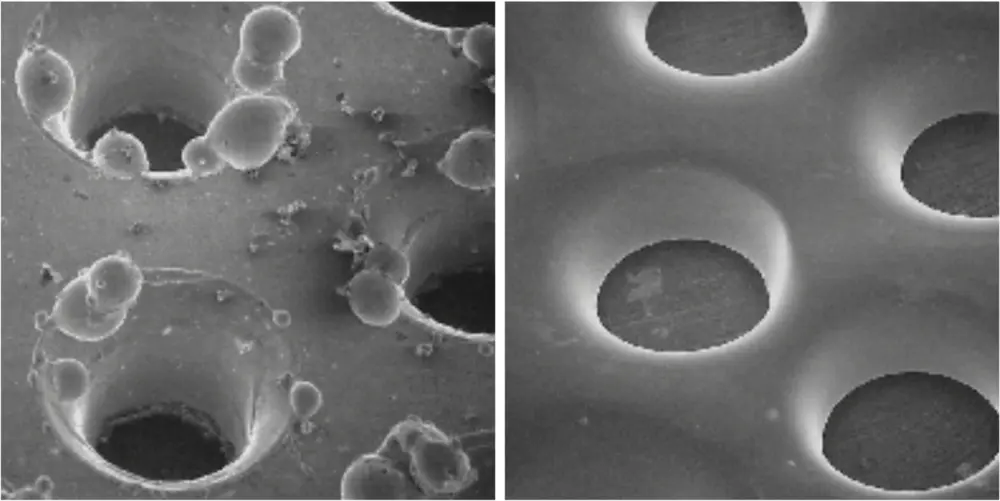
Une variante spéciale du PE, encore en cours de développement, est le polissage au plasma. Il s'agit de polir sous l'influence d'une haute tension électrique générée par un plasma. Les produits chimiques utilisés sont nettement moins acides. La consommation d'énergie élevée reste un inconvénient.
Nettoyage mécano-chimique
Cette méthode est particulièrement adaptée aux petites pièces de masse qui sont mélangées dans un tambour à de la masse abrasive roulante et à des produits chimiques. Ce dernier doit absorber la saleté - généralement des graisses et des huiles -, éliminer les oxydes et la rouille, et créer un effet de brillance ou de polissage. Le fluide de tambourinage est rendu apte à la réutilisation par centrifugation ou (ultra)filtration, entre autres. Les résidus sont éliminés comme des déchets (dangereux) (petites quantités, difficiles à traiter).
Traitements thermochimique de durcissement
Inchromisation ou chromage dur
L'inchromisation est également connue sous le nom de chromage résistant à la chaleur et à la corrosion. Elle confère aux aciers moins chers les propriétés des aciers résistants à la chaleur - y compris une longue durée de vie - tout en leur permettant d'être facilement formés, étirés, assemblés ou soudés.
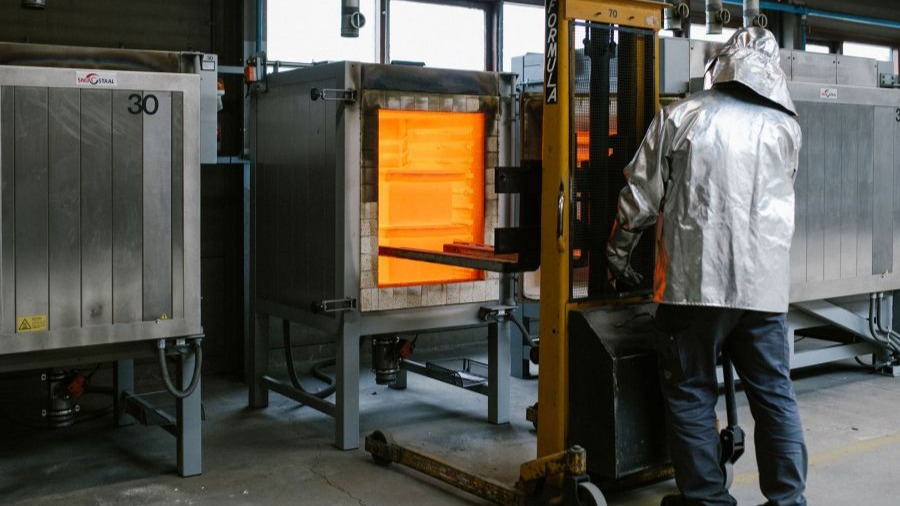
Le chromage dur s'effectue à des températures relativement élevées dans un four spécial. Le chrome se diffuse dans le matériau, les carbures de chrome (CrxCy) formés donnant à la surface la dureté céramique souhaitée, jusqu'à environ 2 000 HV0,025, tout en offrant une résistance chimique accrue. Grâce à l'accumulation uniforme de la couche, la déformation du produit est minime. En outre, aucun problème d'adhérence ne peut survenir entre le matériau de base et la couche d'inchromisation.
L'inchromisation (dure) est adaptée à une utilisation en contact direct avec les denrées alimentaires
L'inchromisation (dure) est adaptée à une utilisation en contact direct avec les denrées alimentaires, conformément à la directive EC1935/2004. Pour cette raison, cette technique est largement utilisée dans l'industrie alimentaire, notamment pour la préparation des tuyaux de transport et des systèmes de dosage.
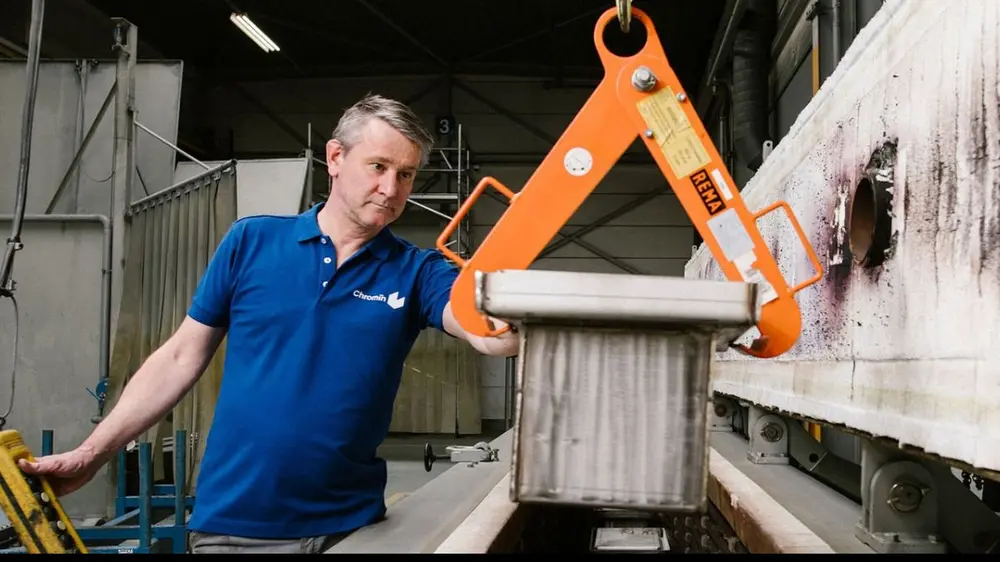
Kolstérisation
Au cours de ce traitement, les atomes de carbone diffusent de l'acier (apport interstitiel) à basse température dans la structure réticulaire existante. Cela crée une contrainte de compression qui induit un fort durcissement de la surface jusqu'à environ 1.000 HV0,025. Aucun changement significatif de taille, de forme ou de couleur ne se produit et la résistance à la corrosion est maintenue. Comme la couche de diffusion se trouve entièrement en surface et qu'il n'y a pas d'accumulation de couches, le produit ne devient pas cassant.
Ce procédé convient parfaitement aux composants en acier inoxydable duplex austénitique qui sont soumis à l'usure et/ou à la corrosion tout en devant répondre à des exigences strictes en matière de stabilité dimensionnelle et de forme. Comme le procédé évite la soudure à froid, il constitue une alternative à la galvanisation.
Nitruration / nitrocarburation
La nitruration implique la diffusion d'azote dans la surface de l'acier, tandis que la nitrocarburation implique une combinaison d'azote et de carbone. Comme cela se fait à une température relativement basse, la déformation est minimale et le post-traitement peut généralement être omis. Le noyau reste résistant, tandis que la surface devient dure et résistante à l'usure. Cependant, la résistance à la corrosion diminue généralement.
Le processus de nitruration et de nitrocarburation peut essentiellement être réalisé dans trois environnements:
- dans un gaz - nitruration gazeuse -, les pièces étant dans un four étanche aux gaz - températures entre 480 et 580 ⁰C - en présence d'azote et de carbone en quantité suffisante. Les atomes respectifs diffusent dans la surface de l'acier pendant une à quatre périodes de 24 heures ; la durée est déterminée par la qualité de l'acier et la profondeur de nitruration souhaitée.
- dans un bain de sel - nitrocarburation en bain de sel -, les pièces étant d'abord préchauffées à l'air à environ 350 °C afin de dissiper les contraintes d'usinage. Le processus lui-même se déroule dans un bain de sel contenant de l'azote et du carbone, dont la température varie entre 480 et 630 °C. Le métal finit par acquérir une surface fine, noire et brillante, assez résistante à la corrosion.
- dans un plasma - nitruration au plasma -, les pièces étant à basse pression dans une atmosphère de gaz ionisé; un mélange d'azote, d'hydrogène et éventuellement d'un gaz émetteur de carbone. Au cours du processus, les ions chargés positivement de l'anode (la paroi du four) se déposent sur la cathode (l'objet) par phases à une vitesse d'impact très élevée. Dans la phase 1, la surface de l'objet est nettoyée, dans la phase 2, elle est chauffée et dans la phase 3 a lieu le processus de nitruration proprement dit. En ajustant le mélange gazeux, il est possible de réaliser des couches et des profils de dureté spécifiques au client.
Aspect financier
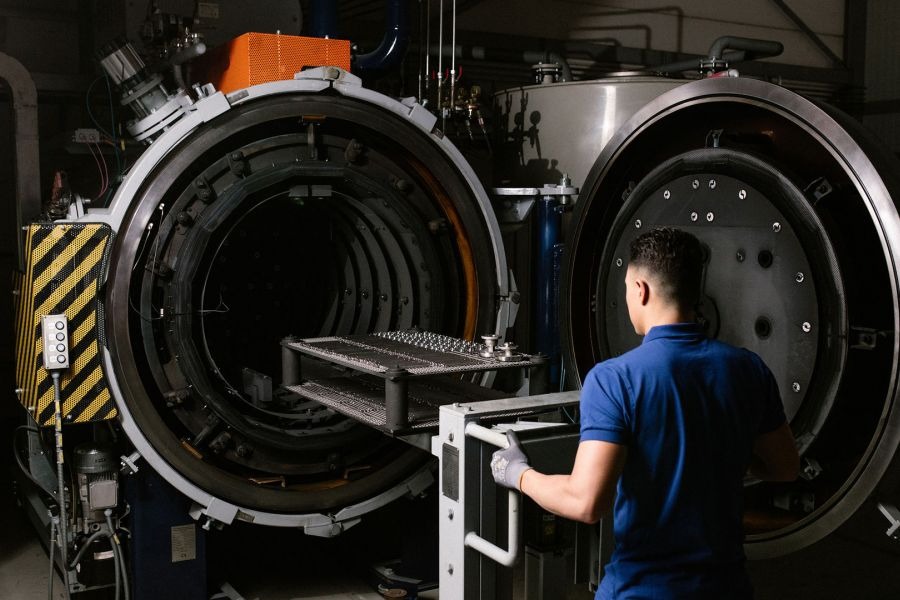
Le coût d'une méthode de traitement de surface est largement déterminé par l'équipement requis, les ressources et les coûts associés au traitement des déchets. En général, le coût des traitements mécaniques est relativement élevé, en raison de leur forte intensité de main-d'œuvre. Les traitements thermiques nécessitent beaucoup d'énergie, notamment pour chauffer le four et le chargement, et pour maintenir la température constante pendant la phase de traitement.
Les procédés de diffusion avec des gaz sont énergivores en raison de la longue phase de traitement - jusqu'à 50 heures - mais grâce à des optimisations toujours plus poussées, cela ne se fait pas au détriment de la valeur ajoutée.
En collaboration avec Chromin Maastricht et Packo Innox