Un procédé d'électroérosion à fil plus intelligent grâce à l'IA
La technologie de contrôle améliore le procédé d'électroérosion à fil
Aujourd'hui, les innovations dans le domaine de l'électroérosion à fil concernent principalement des éléments qui ne sont pas immédiatement visibles, mais qui ont un impact majeur sur le résultat final, le fonctionnement de la machine et les exigences supplémentaires imposées par les entreprises de haute technologie. Et cela va bien au-delà de la technologie des machines.
Intelligence artificielle
Dans la technologie de l'érosion également - ou peut-être justement dans cette technologie - les fabricants commencent de plus en plus à appliquer l'intelligence artificielle (IA). En fait, ils le font depuis un certain temps, mais aujourd'hui, le lien entre certaines nouvelles fonctionnalités et l'intelligence artificielle est plus explicite.
C'est le cas, par exemple, des derniers logiciels qui, associés à des capteurs, permettent de mieux contrôler le processus et de générer des données pour une meilleure compréhension du procédé d'éléctroérosion à fil (de zinc). Tout cela dans le but de rendre le processus plus accessible, même aux ouvriers les moins expérimentés, et de donner à l'utilisateur des outils pour analyser le processus afin d'obtenir de meilleures performances.
Obtenir des résultats optimaux plus rapidement
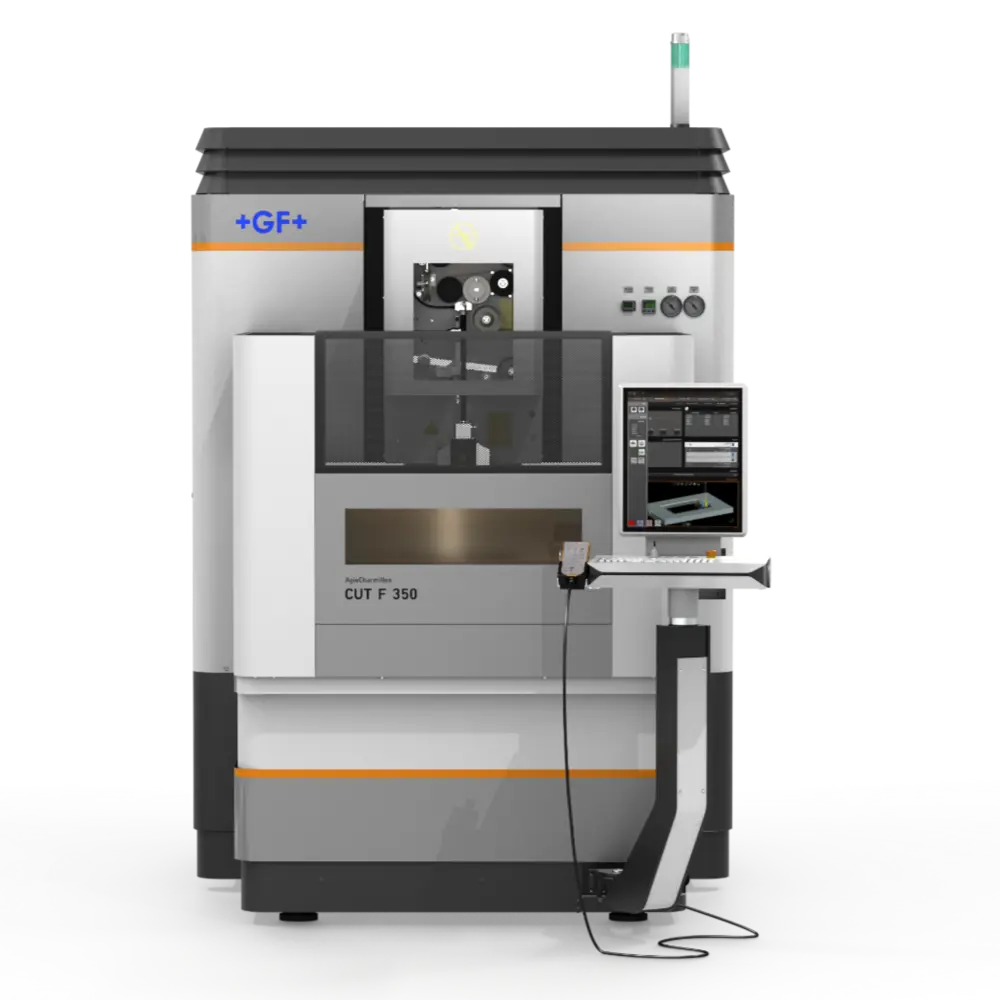
L'intelligence artificielle est également utilisée pour améliorer le procédé d'électroérosion proprement dit, par exemple lors de la coupe avec des fils spéciaux, ou pour ajuster les paramètres de coupe de manière adaptative. On diminue ainsi le risque de rupture du fil; le processus devient plus efficace et on peut réduire la consommation de fil.
La commande apprend de chaque coupe, pour ainsi dire, et est donc beaucoup mieux à même de déterminer où se situent les limites du procédé. En d'autres termes, à partir de quels réglages la probabilité de rupture du fil devient-elle si élevée qu'elle constitue un risque réel?
En appliquant l'apprentissage automatique et les algorithmes associés, la commande apprend des opérations effectuées sur la machine, dans différents matériaux. Au fil du temps, les algorithmes deviendront de plus en plus performants pour choisir les réglages optimaux dès le début.
On obtient ainsi un bon résultat final plus rapidement, sans trop de d'essais-erreurs. Des précisions de formage plus élevées et des rugosités de surface plus faibles peuvent être obtenues plus rapidement, avec moins d'expérience. Outre l'amélioration de l'efficacité et de la qualité, ces solutions permettent aux fabricants de rendre l'électroérosion à fil plus accessible.
Matériaux difficiles et support ultrasonique
L'électroérosion à fil a mis longtemps à s'imposer comme technologie de fabrication de pièces critiques dans l'industrie aéronautique. Ceci à cause de la couche blanche qui se forme sur la pièce en raison du réchauffement et du refroidissement rapides. Avec leur nouvelle génération de générateurs, les fabricants ont maîtrisé ce problème, mais les scientifiques du monde entier poursuivent leurs recherches pour améliorer l'usinage des matériaux difficiles.
L'un de ces matériaux est le carbure de tungstène (carbure). Certaines études ont montré que l'assistance ultrasonique peut avoir un effet positif sur le Material Removal Rate (MRR) ainsi que sur la qualité de la surface. Lorsque la vibration est appliquée au processus de micro-WEDM(Wire Electrical Discharge Machining), les décharges sont plus efficaces et il y a moins de courts-circuits. En outre, la vitesse d'avance peut rester constante.
Les vibrations ultrasoniques peuvent avoir un effet positif sur le taux d'enlèvement de matière et la qualité de la surface lors de l'usinage de matériaux difficiles tels que le carbure
Certains chercheurs font vibrer la pièce par ultrasons, tandis que d'autres le font avec le fil (l'outil). Ceci a également été effectué par des chercheurs d'une université thaïlandaise. Ils ont récemment publié des résultats sur l'électroérosion avec un fil de laiton zingué, avec un support ultrasonique. L'unité ultrasonique fonctionne à une fréquence de 40 kHz. La quantité de matière (carbure de tungstène) qui a pu être enlevée avec cette unité était de 18 mm3/min, contre 14 mm3/min sans le support ultrasonique.
Les chercheurs attribuent cette amélioration de la productivité à deux facteurs. Les vibrations ultrasoniques brisent la surface de la pièce, ce qui permet à la décharge électrique d'enlever le matériau plus facilement. La seconde raison est que les vibrations ultrasoniques augmentent la vitesse d'enlèvement thermique de la couche externe.
Une couche blanche plus fine
Un autre avantage important est que la couche blanche qui se forme normalement en raison du refroidissement rapide de la surface est nettement plus fine lorsque l'électroérosion à fil est soutenue par des ultrasons. La pièce subit donc moins de dommages thermiques.
Les chercheurs précisent toutefois que des fissures peuvent se former sous la couche blanche à la suite d'un choc thermique. Ils indiquent qu'il faudra de nouveaux capteurs et algorithmes de contrôle pour rendre le processus combiné stable.
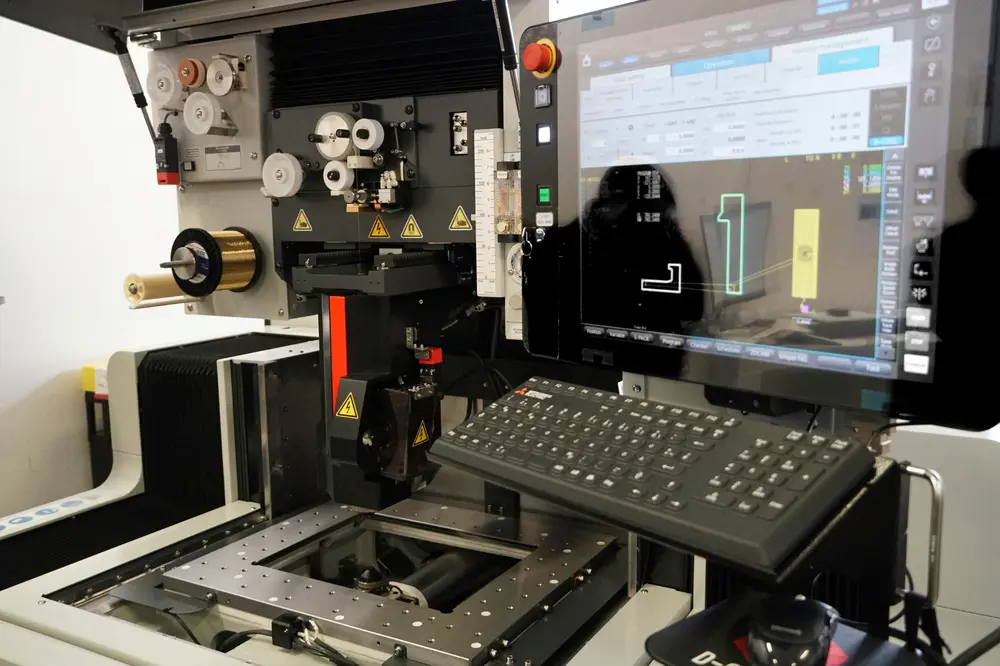
Mitsubishi Electric déploie également l'IA. Cette technologie 'Maisart' est notamment utilisée pour l'électroérosion avec un fil sans cuivre, tel que le fil en molybdène. La manière dont Mitsubishi applique l'intelligence artificielle garantit que les réglages du générateur sont continuellement ajustés. L'une des applications est l'électroérosion de composants de précision avec des exigences élevées en matière de propreté, par exemple l'absence totale de cuivre de le procédé d'électroérosion
Nouveaux types de fils
Il n'y a pas que du côté des machines que l'électroérosion à fil continue à se développer. La composition des fils fait également l'objet d'innovations. L'une d'entre elles vient des Pays-Bas et est fortement motivée par la chaîne d'approvisionnement de haute technologie dans l'industrie des semi-conducteurs.
Les particules de zinc et de cuivre contenues dans les fils de laiton revêtus ne sont pas souhaitées dans toutes les industries. Dans l'industrie des semi-conducteurs, cela peut poser un problème avec les composants sous vide poussé, qui doivent répondre aux exigences les plus élevées en matière de propreté. Elles peuvent également poser des problèmes dans les applications médicales. Ces particules restent dans la surface et peuvent causer des problèmes dans l'application finale.
L'électroérosion stable avec des fils de molybdène ou de tungstène est une solution, mais elle a un prix. Ces fils sont chers (jusqu'à 20 fois plus chers qu'un fil de laiton revêtu), cassent rapidement et coupent lentement. La productivité s'en ressent.
L'utilisation d'un nouveau type de fil avec une âme en laiton, une couche de cuivre-zinc par-dessus et une couche protectrice de nickel permet de répondre aux exigences de propreté les plus élevées sur le marché des composants de haute performance
En collaboration avec le fabricant allemand de fils Berkenhoff, Sommen EDM et De Ridder ont mis au point un nouveau type de fil de laiton, le confreecut One. Il s'agit d'une alternative pour les applications où il ne doit rester aucune trace de zinc ou de cuivre sur la pièce à usiner. Ce fil a été testé à grande échelle dans la chaîne d'approvisionnement de l'industrie des semi-conducteurs
Une nouvelle solution mise au point par des parties néerlandaises en collaboration avec un fabricant de fils allemand consiste à couper un nouveau type de fil avec une âme en laiton, entourée d'une couche de cuivre-zinc et d'une couche protectrice de nickel.
La part de cuivre et de zinc restant après la coupe (0,2% WT) est négligeable et comparable à la quantité présente dans le diélectrique. Il est vrai que des particules de cuivre peuvent subsister après la première coupe, mais elles sont éliminées lors de la deuxième. Et comme il s'agit de composants de haute qualité, plusieurs coupes sont en fait toujours nécessaires.
La vitesse de coupe est aussi beaucoup plus élevée. Des tests effectués aux Pays-Bas montrent que les exigences de propreté les plus élevées du marché sont atteintes avec le nouveau fil, sans devoir faire de concessions au niveau du processus en termes de stabilité et de productivité.
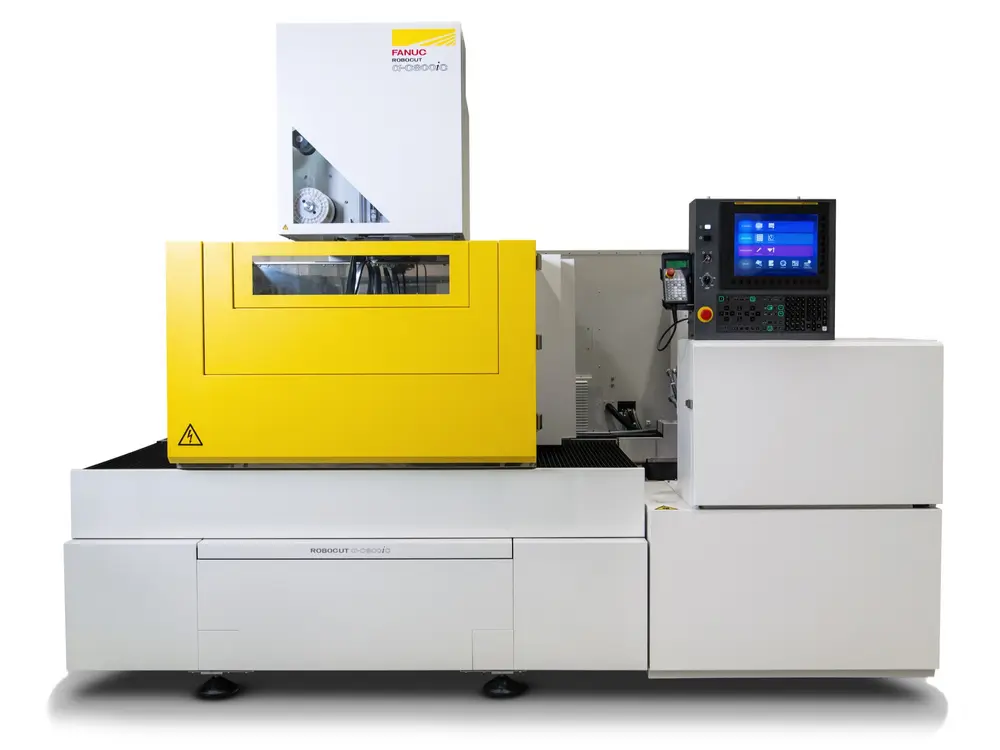
Lors de l'EMO de Hanovre, le fabricant japonais Fanuc a présenté officiellement le Robocut α-C800iC, complétant ainsi la série α-CIC. La nouvelle machine a une plage de travail de 1250 x 975 x 500 mm et a été développée pour l'usinage de pièces de turbines dans l'industrie aéronautique, entre autres. La série α-CIC est la gamme supérieure d'électroérosion à fil de Fanuc. L'une de ses caractéristiques est la capacité de compenser l'erreur d'angle de broche sur l'ensemble de la plage XY de la machine. La commande des machines d'électroérosion à fil a également été rendue plus intuitive. L'α-C800iC sera disponible sur le marché à partir du printemps 2024. La machine finale peut différer du prototype présenté à l'EMO de Hanovre
La durabilité devient-elle un thème?
Les fabricants de machines d'électroérosion à fil intègrent également diverses caractéristiques d'économie d'énergie dans leurs nouveaux modèles. La durabilité devient progressivement un thème.
Une autre contribution à la durabilité est la réutilisation du fil qui a déjà été utilisé pour l'électroérosion. Certains fabricants, comme les fabricants d'outils en carbure, ont mis en place un programme de retour. Ils collectent le fil usagé auprès de leurs clients - qui reçoivent une compensation pour cela - et le retraitent comme matière première dans la production de fil neuf. Ils s'orientent ainsi vers une économie circulaire. Le niveau de qualité du fil est conforme aux normes ISO.
Un fabricant suisse a lancé un programme en Italie, en Suisse et en Autriche pour récupérer les très vieilles machines et les matières premières qu'elles contiennent. Il s'agit en moyenne de 400 grammes de cuivre, 170 grammes d'acier au carbone et 200 kilos de composants électroniques. Les entreprises qui retournent leur vieille machine reçoivent un certificat indiquant la quantité de déchets et d'émissions de CO2 qu'elles ont économisée.
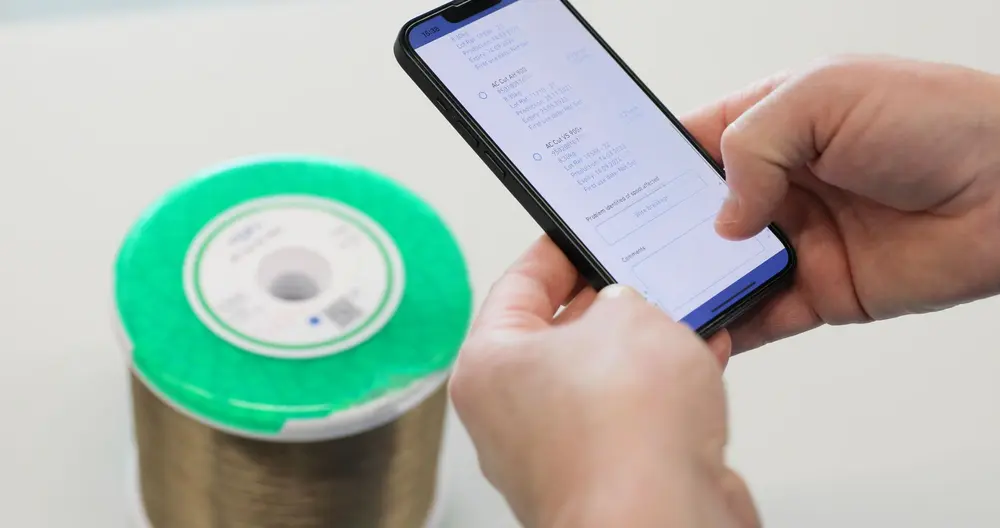
GF Machining Solutions a lancé cette année une application pour ses machines d'électroérosion à fil. En scannant le tag NFC Smart Wire avec son téléphone portable, l'utilisateur obtient des informations sur la longueur du fil sur la bobine et accède aux données des 50 dernières bobines de fil utilisées. L'application vérifie également que le fil utilisé correspond bien au programme en cours sur la machine